ZBC2000 Materials PCB Manufacturer
ZBC2000 Materials PCB Manufacturer. we can produce the best samllest bump pitch with 100um, the best smallest trace are 9um. and the smallest gap are 9um. most of the design are 15um to 30um trace and spacing.
ZBC2000 Materials PCBs represent the pinnacle of modern circuit board technology, meticulously crafted to deliver unparalleled performance and reliability. Engineered using high-performance substrate materials such as FR-4, Rogers RO4003C, or DuPont Pyralux, these PCBs offer exceptional electrical, thermal, and mechanical properties. Designed for applications demanding precision and stability, ZBC2000 Materials PCBs excel in industries like telecommunications, aerospace, and medical devices. Their ability to support high-speed digital, RF/microwave, and mixed-signal designs makes them versatile solutions for a wide range of electronic systems. With their low loss, high signal integrity, and excellent thermal management capabilities, ZBC2000 Materials PCBs ensure optimal performance even in the most demanding environments. Whether it’s facilitating data transmission in telecommunications networks or powering critical medical equipment, ZBC2000 Materials PCBs stand as the cornerstone of cutting-edge electronic innovation.
What is a ZBC2000 Materials PCB?
The ZBC2000 Materials PCB is a specialized printed circuit board (PCB) designed for use in electronic devices, particularly in applications where high performance and reliability are crucial. This type of PCB is specifically engineered to meet the demands of modern electronic systems, offering advanced materials and construction techniques to achieve optimal performance.
One key feature of the ZBC2000 Materials PCB is its use of high-quality materials that provide exceptional electrical and thermal properties. These materials may include advanced substrates such as FR-4, polyimide, or even specialized materials like Rogers RO4003C for applications requiring high-frequency performance. The choice of material depends on the specific requirements of the application, such as signal integrity, thermal management, or mechanical stability.
In addition to superior materials, the ZBC2000 Materials PCB typically employs advanced manufacturing processes to ensure precision and reliability. This may involve techniques such as controlled impedance routing, fine-pitch component placement, and multilayer construction to accommodate complex circuit designs and high-density interconnects. These processes help to minimize signal loss, reduce electromagnetic interference (EMI), and enhance overall system performance.
Furthermore, the ZBC2000 Materials PCB may incorporate additional features to enhance its functionality and reliability. This could include surface finishes such as gold plating or immersion silver to improve solderability and corrosion resistance, as well as solder mask and silkscreen options for labeling and protection.
Overall, the ZBC2000 Materials PCB represents a cutting-edge solution for demanding electronic applications, offering a combination of high-performance materials, advanced manufacturing techniques, and additional features to meet the needs of modern electronic systems. Whether used in telecommunications, aerospace, medical devices, or other industries, these PCBs play a critical role in enabling the performance and reliability of electronic devices and systems.
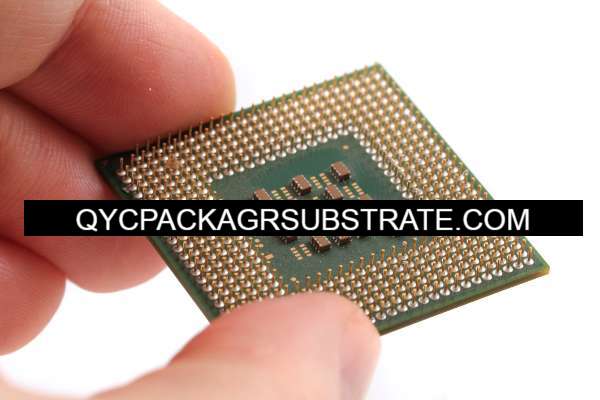
ZBC2000 Materials PCB Manufacturer
What are ZBC2000 Materials PCB Design Guidelines?
Designing PCBs with ZBC2000 materials requires careful consideration of various factors to ensure optimal performance and reliability. Here are some general design guidelines:
- Material Selection: Choose the appropriate substrate material based on the specific requirements of your application. Consider factors such as dielectric constant, thermal conductivity, and mechanical properties. ZBC2000 materials typically offer high-performance characteristics suitable for demanding applications.
- Layer Stackup: Design a layer stackup that meets the impedance requirements, signal integrity goals, and thermal management needs of the PCB. Utilize multiple layers effectively to minimize signal interference and achieve desired impedance control.
- Trace Routing: Follow best practices for trace routing to maintain signal integrity and minimize losses. Use controlled impedance routing for high-speed signals to ensure consistent signal quality throughout the PCB. Pay attention to signal integrity principles such as impedance matching, length matching, and signal return paths.
- Component Placement: Place components strategically to minimize signal path lengths, reduce crosstalk, and optimize thermal performance. Consider the placement of critical components such as high-speed ICs, connectors, and power distribution components to enhance electrical performance and ease of routing.
- Power Distribution: Design an efficient power distribution network (PDN) to ensure stable power delivery to all components on the PCB. Use appropriate power plane configurations, decoupling capacitors, and routing techniques to minimize voltage fluctuations and noise.
- Thermal Management: Implement effective thermal management strategies to dissipate heat generated by active components. Consider factors such as component placement, thermal vias, and heatsinks to optimize thermal performance and prevent overheating.
- Signal Integrity Analysis: Conduct thorough signal integrity analysis using simulation tools to verify the performance of high-speed signals, identify potential signal integrity issues, and optimize the design accordingly. Perform pre-layout and post-layout simulations to validate the design and ensure compliance with design requirements.
- Manufacturability: Design the PCB with manufacturability in mind to facilitate smooth production processes. Follow industry-standard design rules, consider fabrication and assembly constraints, and communicate effectively with PCB manufacturers to ensure successful fabrication and assembly.
By following these design guidelines, you can develop ZBC2000 Materials PCBs that meet the performance, reliability, and manufacturability requirements of your specific application.
What is the ZBC2000 Materials PCB Fabrication Process?
The fabrication process for ZBC2000 Materials PCBs involves several steps to transform the design into a physical circuit board ready for assembly. Here’s an overview of the typical fabrication process:
- Design Preparation: The fabrication process begins with the preparation of the PCB design files, typically in Gerber format, which contain detailed information about the PCB layout, including copper traces, solder mask, and silkscreen layers. These files are generated from the PCB design software used during the design phase.
- Material Preparation: The chosen substrate material, such as FR-4 or specialty materials like Rogers RO4003C, is prepared for the fabrication process. This may involve cutting the material to size and cleaning the surface to remove any contaminants that could affect adhesion.
- Layer Stackup: If the PCB design includes multiple layers, the layers are laminated together to create the layer stackup specified in the design. This process involves bonding the copper-clad substrate layers together using heat and pressure to form a single, multi-layered board.
- Copper Cladding: The outer layers of the PCB are coated with a thin layer of copper through a process called electroplating or electrodeposition. This copper layer forms the conductive traces and pads that make up the circuitry of the PCB.
- Photoresist Application: A layer of photoresist is applied to the surface of the copper-clad substrate. The photoresist serves as a mask for the subsequent etching process, allowing the desired circuit pattern to be transferred to the copper layer.
- Exposure and Development: The PCB design is transferred onto the photoresist layer using a process called photolithography. UV light is used to expose the photoresist through a photomask, which contains the circuit pattern. The exposed photoresist is then developed, removing the unexposed areas and leaving behind the pattern of the circuit traces and pads.
- Etching:The exposed copper areas not protected by the developed photoresist are etched away using chemical etchants. This process removes the unwanted copper, leaving behind the desired circuit pattern on the PCB substrate.
- Surface Finishing:After etching, the PCB undergoes surface finishing processes to improve solderability, corrosion resistance, and overall reliability. Common surface finishes include hot air leveling (HASL), electroless nickel immersion gold (ENIG), and immersion silver.
- Solder Mask Application: A layer of solder mask is applied over the entire surface of the PCB, covering the copper traces and pads while leaving the component mounting areas exposed. The solder mask protects the copper from oxidation and prevents solder bridges during assembly.
- Silkscreen Printing: Information such as component labels, reference designators, and logos are printed onto the PCB surface using a silkscreen printing process. This information helps during assembly and troubleshooting of the PCB.
- Final Inspection: The completed PCB undergoes thorough inspection to ensure that it meets the design specifications and quality standards. This may include visual inspection, electrical testing, and dimensional measurements to verify accuracy and functionality.
Once the fabrication process is complete, the finished ZBC2000 Materials PCBs are ready for assembly, where electronic components are mounted onto the board to create the final electronic system.
How do you manufacture a ZBC2000 Materials PCB?
Manufacturing a ZBC2000 Materials PCB involves a series of steps, from material selection to final inspection. Here’s a detailed overview of the manufacturing process:
- Material Selection:Choose the appropriate high-performance substrate material for the ZBC2000 Materials PCB based on the specific requirements of the application. This may include materials such as FR-4, polyimide, or specialized materials like Rogers RO4003C for high-frequency applications.
- Preparation of Substrate Material: Prepare the chosen substrate material by cutting it to the required size and cleaning the surface to remove any contaminants. This ensures proper adhesion of copper and other layers during the fabrication process.
- Layer Stackup Design: Determine the layer stackup configuration based on the PCB design requirements, including the number of layers, copper thickness, and dielectric properties. The layer stackup defines the arrangement of copper layers, prepreg layers, and core materials in the PCB.
- Copper Cladding: Apply a thin layer of copper to the outer surfaces of the substrate material through a process called electroplating or electrodeposition. This copper layer serves as the conductive material for the circuit traces and pads.
- Photoresist Application: Apply a layer of photoresist to the surface of the copper-clad substrate. The photoresist acts as a mask for the subsequent etching process, allowing the desired circuit pattern to be transferred onto the copper layer.
- Exposure and Development: Expose the photoresist layer to UV light through a photomask containing the circuit pattern. The exposed photoresist is then developed, removing the unexposed areas and leaving behind the pattern of the circuit traces and pads on the copper layer.
- Etching: Etch away the exposed copper areas using chemical etchants, leaving behind the desired circuit pattern on the substrate material. This process removes the unwanted copper, defining the conductive pathways of the PCB.
- Surface Finishing: Apply a surface finish to the exposed copper traces and pads to improve solderability, corrosion resistance, and overall reliability. Common surface finishes include hot air leveling (HASL), electroless nickel immersion gold (ENIG), and immersion silver.
- Solder Mask Application: Apply a layer of solder mask over the entire surface of the PCB, covering the copper traces and pads while leaving the component mounting areas exposed. The solder mask protects the copper from oxidation and prevents solder bridges during assembly.
- Silkscreen Printing: Print component labels, reference designators, and other markings onto the PCB surface using a silkscreen printing process. This information aids in component placement and identification during assembly.
- Final Inspection: Conduct thorough inspection of the finished PCB to ensure that it meets the design specifications and quality standards. This may include visual inspection, electrical testing, and dimensional measurements to verify accuracy and functionality.
Once the ZBC2000 Materials PCB has passed final inspection, it is ready for assembly, where electronic components are mounted onto the board to create the final electronic system.
How much should a ZBC2000 Materials PCB cost?
The cost of a ZBC2000 Materials PCB can vary widely depending on several factors, including the size and complexity of the board, the number of layers, the choice of materials, surface finishes, and the quantity ordered. Here are some factors that can influence the cost:
- Board Size and Complexity: Larger and more complex PCBs require more materials and manufacturing processes, leading to higher costs.
- Number of Layers: Multi-layer PCBs are generally more expensive than single or double-layer boards due to the additional layers and manufacturing steps involved.
- Materials: ZBC2000 materials are typically high-performance and may be more expensive than standard FR-4 materials. Specialty materials like Rogers RO4003C can further increase the cost.
- Surface Finish: Different surface finishes, such as ENIG or immersion silver, have different costs associated with them. More advanced surface finishes tend to be more expensive.
- Quantity: Larger production quantities often result in lower per-unit costs due to economies of scale. However, prototype or low-volume orders may have higher unit costs.
- Turnaround Time: Expedited manufacturing services typically come with higher costs compared to standard lead times.
- Additional Services: Additional services such as impedance control, blind/buried vias, and controlled depth drilling can add to the overall cost of the PCB.
As a rough estimate, the cost of a ZBC2000 Materials PCB can range from a few dollars for simple prototypes to several hundred dollars or more for complex, high-performance boards in larger quantities. It’s recommended to obtain quotes from multiple PCB manufacturers to get an accurate cost estimate based on your specific requirements and quantities. Additionally, keep in mind that prices may fluctuate over time due to changes in material costs, market demand, and other factors.
What is ZBC2000 Materials PCB base material?
ZBC2000 Materials PCBs utilize advanced base materials chosen for their exceptional performance characteristics in electronic applications. While there isn’t a single “ZBC2000” base material, the term generally refers to a category of high-performance substrate materials designed to meet the demanding requirements of modern electronic systems. These materials are carefully engineered to provide specific properties that enhance the performance, reliability, and durability of PCBs.
One common base material used in ZBC2000 Materials PCBs is FR-4 (Flame Retardant 4). FR-4 is a widely used substrate material known for its excellent electrical insulation properties, mechanical strength, and affordability. It consists of a woven fiberglass cloth impregnated with epoxy resin, making it suitable for a wide range of applications, from consumer electronics to aerospace and defense systems.
In addition to FR-4, ZBC2000 Materials PCBs may utilize specialized substrate materials tailored to specific performance requirements. For example, high-frequency applications may require materials with low dielectric loss and consistent electrical properties across a broad frequency range. Materials like Rogers RO4003C, DuPont Pyralux, or Arlon materials are commonly used for high-frequency PCBs due to their low-loss characteristics and stable electrical performance.
Other factors considered when selecting base materials for ZBC2000 Materials PCBs include thermal conductivity, coefficient of thermal expansion (CTE), moisture resistance, and environmental factors such as temperature and humidity extremes.
Ultimately, the choice of base material depends on the specific requirements of the application, including signal integrity, thermal management, mechanical stability, and reliability. By selecting the appropriate base material, designers can ensure that ZBC2000 Materials PCBs meet the performance and reliability standards demanded by today’s electronic systems.
Which company makes ZBC2000 Materials PCB?
Currently, there isn’t a single company specialized in producing “ZBC2000 Materials PCB”. In fact, “ZBC2000 Materials PCB” is a generic term used to describe printed circuit boards manufactured using high-performance substrate materials. These high-performance substrate materials can include FR-4, Rogers RO4003C, DuPont Pyralux, etc., to meet the high demands for performance and reliability in modern electronic systems.
Our company can produce ZBC2000 Materials PCBs because we have advanced equipment and technology, and we collaborate with multiple suppliers to acquire various high-performance substrate materials. Our manufacturing process complies with industry standards and can meet the manufacturing requirements for various complex circuit boards.
In our company, our manufacturing process includes the following steps:
- Design Validation and Preparation:We collaborate with clients to validate design specifications and prepare the necessary production files.
- Material Procurement and Preparation: We procure high-performance substrate materials from reliable suppliers to ensure quality and reliability.
- Production Process: We use advanced equipment and processes to produce ZBC2000 Materials PCBs according to client design requirements. This includes material pre-processing, lamination, copper foil processing, photolithography, etching, solder mask application, silk screen printing, and more.
- Surface Treatment: We offer various surface treatment options, including HASL, ENIG, immersion gold, etc., based on client requirements.
- Quality Control and Inspection: We strictly adhere to quality control standards, conducting rigorous inspections and testing at each manufacturing step to ensure the production of high-quality PCBs that meet client requirements.
- Delivery: We ensure on-time delivery of ZBC2000 Materials PCBs that meet client specifications, ensuring customer satisfaction and trust.
Through our professional team, advanced equipment, and stringent quality management system, our company is capable of producing high-quality ZBC2000 Materials PCBs that meet the high requirements for performance, reliability, and delivery.
What are the 7 qualities of good customer service?
Good customer service is essential for building strong relationships with customers and fostering loyalty. Here are seven qualities of good customer service:
- Responsiveness:Good customer service involves promptly addressing customer inquiries, concerns, and requests. Responding to customers in a timely manner demonstrates respect for their time and shows that their needs are being taken seriously.
- Empathy:Empathy is the ability to understand and share the feelings of others. Good customer service representatives empathize with customers by acknowledging their emotions, listening actively, and showing genuine concern for their needs and experiences.
- Clear Communication: Effective communication is crucial in customer service interactions. Good customer service representatives communicate clearly and concisely, using language that is easy for customers to understand. They provide accurate information and avoid jargon or technical language that may confuse customers.
- Problem-Solving Skills: Good customer service involves effectively addressing customer problems and finding solutions to meet their needs. Customer service representatives should be skilled at identifying issues, analyzing root causes, and implementing appropriate solutions in a timely manner.
- Professionalism:Professionalism is key to building trust and credibility with customers. Good customer service representatives conduct themselves in a professional manner, maintaining a positive attitude, remaining calm under pressure, and adhering to company policies and procedures.
- Patience: Dealing with customer inquiries and concerns can sometimes be challenging, especially if customers are upset or frustrated. Good customer service representatives demonstrate patience and tolerance, remaining calm and composed even in difficult situations.
- Personalization: Tailoring the customer experience to meet individual needs and preferences is an important aspect of good customer service. Good customer service representatives personalize interactions by addressing customers by name, remembering past interactions, and offering relevant product recommendations or solutions.
By embodying these qualities, businesses can provide exceptional customer service experiences that leave a positive impression on customers and encourage repeat business and referrals.
FAQs
What are ZBC2000 Materials PCBs?
ZBC2000 Materials PCBs are printed circuit boards manufactured using high-performance substrate materials, such as FR-4, Rogers RO4003C, or DuPont Pyralux. These materials are chosen for their exceptional electrical, thermal, and mechanical properties, making them suitable for demanding electronic applications.
What are the advantages of ZBC2000 Materials PCBs?
ZBC2000 Materials PCBs offer several advantages, including high signal integrity, low loss, excellent thermal performance, and reliability. These properties make them ideal for applications requiring high-frequency operation, precision, and stability.
What industries commonly use ZBC2000 Materials PCBs?
ZBC2000 Materials PCBs are used in various industries, including telecommunications, aerospace, defense, medical devices, automotive, and industrial electronics. They are particularly well-suited for applications where high performance and reliability are critical.
What types of designs can be implemented on ZBC2000 Materials PCBs?
ZBC2000 Materials PCBs support a wide range of designs, including high-speed digital, RF/microwave, analog, and mixed-signal circuits. They can accommodate complex designs with tight tolerances, controlled impedance requirements, and fine-pitch components.
Are ZBC2000 Materials PCBs more expensive than standard PCBs?
The cost of ZBC2000 Materials PCBs can vary depending on factors such as board size, complexity, materials, and quantity ordered. While they may be more expensive than standard FR-4 PCBs, the enhanced performance and reliability they offer can justify the investment for certain applications.
Can ZBC2000 Materials PCBs be manufactured using standard PCB fabrication processes?
Yes, ZBC2000 Materials PCBs can be manufactured using standard PCB fabrication processes, albeit with some modifications to accommodate the specific properties of the chosen substrate materials. Manufacturers may need to adjust parameters such as etching chemistry, lamination conditions, and surface finish options to optimize the manufacturing process for ZBC2000 Materials PCBs.
Where can I find a reliable supplier for ZBC2000 Materials PCBs?
Reliable suppliers for ZBC2000 Materials PCBs can be found through various channels, including online directories, trade shows, industry forums, and referrals from other businesses. It’s important to research potential suppliers, review their capabilities and certifications, and request quotes to ensure they can meet your specific requirements.