Advanced Semiconductor Glass Substrates
Advanced Semiconductor Glass Substrates Manufacturer, Glass material from the substrate,The finished substrate has a flatter surface, Lower coefficient of expansion and contraction, Higher precision substrate manufacturer.
Advanced Semiconductor Glass Substrates are specialized materials crucial for the manufacturing of cutting-edge semiconductor devices. These substrates offer a unique combination of properties tailored to meet the demanding requirements of modern semiconductor applications. With excellent thermal conductivity, electrical insulation, and chemical stability, they provide an ideal foundation for the fabrication of integrated circuits (ICs), light-emitting diodes (LEDs), photovoltaic cells, and more. Their uniformity, flatness, and transparency (in certain cases) further enhance their suitability for high-precision lithographic processes and optoelectronic applications. Manufactured through advanced techniques such as glass melting, thin film deposition, and surface modification, these substrates undergo rigorous quality control measures to ensure consistent performance and reliability. As semiconductor technology continues to advance, the role of advanced semiconductor glass substrates becomes increasingly significant, enabling the development of innovative and high-performance semiconductor devices that drive progress in various industries.
What is an Advanced Semiconductor Glass Substrate?
An Advanced Semiconductor Glass Substrate refers to a specialized type of substrate material used in the manufacturing of semiconductor devices. These substrates are typically made from glass, which offers several advantages over traditional silicon substrates in certain applications.
Some key characteristics and features of advanced semiconductor glass substrates include:
- Thermal Properties: Glass substrates often have better thermal conductivity compared to silicon, allowing for more efficient heat dissipation in semiconductor devices.
- Electrical Properties: Glass substrates can have tailored electrical properties, such as low dielectric constant and high insulation resistance, which are advantageous for specific semiconductor applications.
- Uniformity and Smoothness: Glass substrates can be manufactured with high levels of flatness, smoothness, and uniformity, which are crucial for lithographic processes in semiconductor fabrication.
- Transparency: Some glass substrates are transparent in certain wavelength ranges, which is useful for optoelectronic applications such as photonic devices and displays.
- Chemical Stability: Advanced glass substrates can exhibit high chemical stability, resisting reactions with harsh chemicals used in semiconductor processing.
- Compatibility:Glass substrates can be compatible with various deposition techniques such as sputtering, evaporation, and chemical vapor deposition (CVD), enabling the deposition of various semiconductor materials and thin films.
- Customization: Glass substrates can be engineered with specific properties tailored to the requirements of particular semiconductor devices and applications.
These advanced glass substrates are used in a range of semiconductor technologies including integrated circuits (ICs), light-emitting diodes (LEDs), photovoltaic cells, MEMS (Micro-Electro-Mechanical Systems), and more. They play a crucial role in enabling the development of high-performance and innovative semiconductor devices.
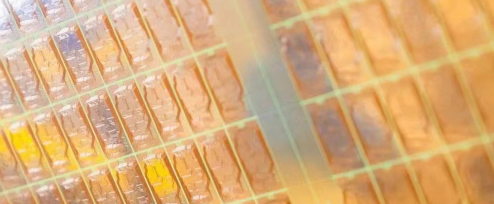
Advanced Semiconductor Glass Substrates
What are the Advanced Semiconductor Glass Substrates Design Guidelines?
Design guidelines for advanced semiconductor glass substrates can vary depending on the specific application and the requirements of the semiconductor device being manufactured. However, here are some general design considerations and guidelines that are often followed:
- Thermal Management: Ensure that the glass substrate has adequate thermal conductivity and heat dissipation properties to prevent overheating of the semiconductor device. This may involve optimizing the thickness and composition of the glass substrate.
- Electrical Properties: Tailor the electrical properties of the glass substrate to meet the requirements of the semiconductor device. This includes considerations such as dielectric constant, insulation resistance, and electrical breakdown voltage.
- Flatness and Uniformity: Design the glass substrate with high levels of flatness and surface uniformity to facilitate lithographic processes and ensure uniform deposition of semiconductor materials.
- Chemical Compatibility: Choose a glass substrate material that is chemically stable and compatible with the semiconductor fabrication processes used, including cleaning, etching, and deposition steps.
- Transparency: If transparency is required for optoelectronic applications, select a glass substrate material that offers high transparency in the relevant wavelength ranges.
- Size and Shape:Determine the appropriate size and shape of the glass substrate based on the dimensions and layout of the semiconductor device being fabricated. Considerations such as wafer size and alignment marks should be taken into account.
- Surface Treatment: Consider surface treatments or coatings to enhance the properties of the glass substrate, such as anti-reflection coatings, passivation layers, or surface modifications for improved adhesion of semiconductor materials.
- Cost and Scalability: Evaluate the cost-effectiveness and scalability of the glass substrate manufacturing process to ensure that it can meet production requirements while remaining economically viable.
- Reliability and Durability: Design the glass substrate to withstand mechanical stress, thermal cycling, and other environmental factors encountered during device operation to ensure long-term reliability and durability.
- Integration Compatibility: Ensure that the glass substrate is compatible with the integration processes used to assemble and package the semiconductor device, including bonding techniques and encapsulation materials.
By following these design guidelines, manufacturers can optimize the performance, reliability, and manufacturability of semiconductor devices using advanced glass substrates.
What is the Advanced Semiconductor Glass Substrates Fabrication Process?
The fabrication process for advanced semiconductor glass substrates involves several steps to produce substrates with the desired properties and characteristics. Here’s a general overview of the fabrication process:
- Selection of Glass Material: The first step is to select a suitable glass material based on the desired properties of the semiconductor device being manufactured. Factors such as thermal conductivity, electrical properties, transparency, and chemical stability are considered during material selection.
- Glass Melting and Forming: The selected glass material is melted in a furnace at high temperatures. Once molten, the glass is formed into sheets or wafers using techniques such as floating, rolling, or drawing. This process helps achieve the desired thickness and flatness of the glass substrate.
- Surface Preparation: After forming, the glass substrates undergo surface preparation steps to clean and smooth the surface. This typically involves cleaning with solvents and/or acids to remove contaminants and improve surface quality.
- Lithography: In some cases, lithographic techniques may be employed to pattern the glass substrate surface. This involves applying a photoresist layer onto the substrate, exposing it to UV light through a mask, and developing the pattern by selectively removing the photoresist. Lithography is commonly used for creating alignment marks, surface texturing, or other features on the glass substrate.
- Thin Film Deposition: Semiconductor devices often require the deposition of thin films of various materials onto the glass substrate. Techniques such as physical vapor deposition (PVD), chemical vapor deposition (CVD), sputtering, or evaporation are used to deposit layers of semiconductor materials, metals, or dielectrics onto the substrate surface.
- Annealing and Thermal Treatment: After thin film deposition, the glass substrates may undergo annealing or thermal treatment processes to improve film adhesion, reduce stress, and enhance the overall stability of the substrate.
- Surface Modification: Surface treatments or coatings may be applied to the glass substrate to modify its properties for specific applications. For example, anti-reflective coatings, passivation layers, or hydrophobic coatings may be applied to enhance performance or durability.
- Quality Control and Testing: Throughout the fabrication process, quality control measures are implemented to ensure that the glass substrates meet the required specifications and standards. Various testing methods, including optical inspection, surface profilometry, and electrical testing, may be employed to assess substrate quality and performance.
- Packaging and Handling:Once fabrication is complete, the glass substrates are typically packaged and handled using cleanroom protocols to prevent contamination and damage before they are shipped to semiconductor device manufacturers for further processing.
By following these fabrication steps, manufacturers can produce advanced semiconductor glass substrates with tailored properties and characteristics to meet the demands of modern semiconductor devices and applications.
How do you manufacture Advanced Semiconductor Glass Substrate?
Manufacturing advanced semiconductor glass substrates involves a series of intricate processes to create substrates with precise properties and specifications. Here’s a step-by-step overview of the manufacturing process:
- Glass Material Selection: Choose a suitable glass material based on the requirements of the semiconductor device. Factors such as thermal conductivity, electrical properties, transparency, and chemical stability are considered during material selection.
- Glass Melting and Forming: The selected glass material is melted in a high-temperature furnace. Once molten, the glass is formed into sheets or wafers using techniques like floating, rolling, or drawing. This process ensures the desired thickness and flatness of the glass substrate.
- Surface Preparation: After forming, the glass substrates undergo surface preparation to clean and smooth the surface. This involves cleaning with solvents and acids to remove contaminants and improve surface quality.
- Lithography (Optional): In some cases, lithographic techniques may be employed to pattern the glass substrate surface. This involves applying a photoresist layer onto the substrate, exposing it to UV light through a mask, and developing the pattern by selectively removing the photoresist.
- Thin Film Deposition: Semiconductor devices often require the deposition of thin films of various materials onto the glass substrate. Techniques such as physical vapor deposition (PVD), chemical vapor deposition (CVD), sputtering, or evaporation are used to deposit layers of semiconductor materials, metals, or dielectrics onto the substrate surface.
- Annealing and Thermal Treatment: After thin film deposition, the glass substrates may undergo annealing or thermal treatment processes to improve film adhesion, reduce stress, and enhance overall stability.
- Surface Modification: Surface treatments or coatings may be applied to the glass substrate to modify its properties for specific applications. For example, anti-reflective coatings, passivation layers, or hydrophobic coatings may be applied to enhance performance or durability.
- Quality Control and Testing: Throughout the manufacturing process, quality control measures are implemented to ensure that the glass substrates meet the required specifications and standards. Various testing methods, including optical inspection, surface profilometry, and electrical testing, may be employed to assess substrate quality and performance.
- Packaging and Handling: Once manufacturing is complete, the glass substrates are packaged and handled using cleanroom protocols to prevent contamination and damage before they are shipped to semiconductor device manufacturers for further processing.
By following these manufacturing steps, advanced semiconductor glass substrates with tailored properties and characteristics can be produced to meet the demands of modern semiconductor devices and applications.
How much should an Advanced Semiconductor Glass Substrate cost?
The cost of an advanced semiconductor glass substrate can vary significantly depending on various factors such as the size, thickness, material composition, surface finish, quality specifications, and supplier/vendor. Additionally, market demand, competition, and technological advancements can also influence the pricing.
Typically, advanced semiconductor glass substrates can range in price from a few hundred dollars to several thousand dollars per substrate, with larger and more specialized substrates often commanding higher prices. For example, substrates used in high-performance computing (HPC), advanced photovoltaics, or specialized optoelectronic applications may be more expensive due to their unique requirements and higher precision manufacturing processes.
Moreover, the cost structure may include not only the materials and manufacturing expenses but also research and development costs, quality control measures, packaging, and logistics. Additionally, factors such as economies of scale, bulk purchasing, and long-term partnerships with suppliers can also impact the final cost.
Ultimately, the cost of an advanced semiconductor glass substrate is determined by a combination of factors, and it’s essential for businesses to carefully evaluate their requirements and budget constraints when sourcing these substrates.
What is the base material used in Advanced Semiconductor Glass Substrates?
The base material used in advanced semiconductor glass substrates is typically glass. This glass can be engineered to possess specific properties tailored to the requirements of semiconductor devices and applications. The composition of the glass can vary depending on factors such as thermal conductivity, electrical properties, transparency, chemical stability, and mechanical strength.
Various types of glass compositions may be used, including borosilicate glass, soda-lime glass, quartz glass (fused silica), and specialty glasses with specific additives or dopants to enhance certain properties. For example, borosilicate glass is known for its excellent thermal shock resistance and low coefficient of thermal expansion, making it suitable for applications requiring thermal stability. Quartz glass, on the other hand, offers high transparency in the ultraviolet (UV) and visible spectrum, making it ideal for optoelectronic applications.
The choice of base glass material depends on the specific requirements of the semiconductor device being manufactured, as well as factors such as cost, availability, and compatibility with the fabrication processes used.
Which company manufactures Advanced Semiconductor Glass Substrates?
Manufacturers of Advanced Semiconductor Glass Substrates typically include several companies. Some well-known companies in this field include Asahi Glass Co., Ltd. (AGC) in Japan, Schott AG in Germany, Corning Incorporated in the United States, among others. These companies possess extensive experience and expertise in semiconductor materials and processes, enabling them to produce high-quality advanced semiconductor glass substrates for various applications.
Our company is also a leading manufacturer specializing in advanced semiconductor glass substrates. We have advanced production equipment, cutting-edge technologies, and an experienced engineering team capable of designing and manufacturing semiconductor glass substrates with excellent performance. By utilizing advanced glass materials and employing precise manufacturing processes, we ensure that our products meet high-quality standards.
Our advanced semiconductor glass substrates can be used in diverse applications including integrated circuits, optoelectronic devices, photovoltaic cells, sensors, and more. We are committed to providing customized solutions to meet specific design requirements and performance specifications of our customers. Quality management and customer service are paramount in our company, ensuring that customers receive high-quality products and satisfactory service experiences.
Through continuous innovation and technological advancements, our company strives to maintain a competitive edge in the field of advanced semiconductor glass substrates, providing reliable solutions to drive the development and progress of the semiconductor industry.
What are the 7 qualities of good customer service?
Good customer service is essential for businesses to maintain customer satisfaction and loyalty. There are several qualities that contribute to providing excellent customer service. Here are seven key qualities:
- Responsiveness: Good customer service involves being responsive to customers’ needs and inquiries in a timely manner. This includes promptly answering phone calls, emails, and messages, as well as addressing customer concerns or issues as soon as possible.
- Empathy:Empathy is the ability to understand and share the feelings of customers. Good customer service representatives listen actively to customers, show empathy towards their concerns, and strive to find solutions that meet their needs.
- Clear Communication: Effective communication is crucial in providing good customer service. This involves conveying information clearly and concisely, using language that is easily understandable to customers, and ensuring that customers are kept informed throughout their interactions with the business.
- Professionalism: Good customer service requires professionalism in all interactions with customers. This includes being courteous, respectful, and maintaining a positive attitude, even in challenging situations. Professionalism also involves following company policies and procedures to ensure consistency in service delivery.
- Knowledgeability: Customer service representatives should have a good understanding of the products or services offered by the business. They should be knowledgeable about product features, pricing, policies, and procedures, and be able to provide accurate information and assistance to customers.
- Problem-Solving Skills: Good customer service involves being proactive in addressing customer problems and finding solutions to resolve them effectively. Customer service representatives should be resourceful, creative, and willing to go the extra mile to ensure customer satisfaction.
- Follow-Up: Following up with customers after their interactions with the business demonstrates a commitment to their satisfaction and shows that their feedback is valued. Good customer service includes following up to ensure that issues have been resolved satisfactorily and to gather feedback for improvement.
By embodying these qualities, businesses can deliver exceptional customer service experiences that foster customer loyalty and drive long-term success.
FAQs
What are advanced semiconductor glass substrates?
Advanced semiconductor glass substrates are specialized materials used in the manufacturing of semiconductor devices. They offer specific properties such as thermal conductivity, electrical insulation, and chemical stability, making them suitable for various semiconductor applications.
What are the advantages of using advanced semiconductor glass substrates?
Advanced semiconductor glass substrates offer advantages such as excellent thermal management, high electrical insulation, uniformity, transparency (in some cases), and compatibility with semiconductor fabrication processes.
What applications are advanced semiconductor glass substrates used in?
These substrates are used in a wide range of semiconductor applications including integrated circuits (ICs), light-emitting diodes (LEDs), photovoltaic cells, microelectromechanical systems (MEMS), sensors, and optoelectronic devices.
What types of glass are commonly used in advanced semiconductor glass substrates?
Common types of glass used include borosilicate glass, soda-lime glass, quartz glass (fused silica), and specialty glasses with tailored properties.
How are advanced semiconductor glass substrates manufactured?
The manufacturing process involves steps such as glass melting and forming, surface preparation, thin film deposition, annealing, surface modification, quality control, and packaging.
What factors should be considered when selecting advanced semiconductor glass substrates?
Factors to consider include thermal conductivity, electrical properties, transparency, chemical stability, surface quality, size, shape, and compatibility with fabrication processes.
What is the cost of advanced semiconductor glass substrates?
The cost varies depending on factors such as size, thickness, material composition, quality specifications, and supplier. Prices can range from hundreds to thousands of dollars per substrate.
Where can I purchase advanced semiconductor glass substrates?
Advanced semiconductor glass substrates can be purchased from specialized manufacturers, suppliers, or distributors that focus on semiconductor materials and components.
What are the future trends in advanced semiconductor glass substrates?
Future trends may include the development of novel glass compositions with enhanced properties, advancements in manufacturing processes for improved performance and cost-effectiveness, and the integration of glass substrates in emerging semiconductor technologies such as flexible electronics and wearable devices.