Ajinomoto GL102R8HF package substrate Manufacturer
Ajinomoto GL102R8HF package substrate Manufacturer.High speed and high frequency material packaging substrate Manufacturer. Advanced packaging substrate production process and technology
Ajinomoto GL102R8HF package substrate is a high-performance foundation for semiconductor packaging, designed to meet the demanding requirements of modern electronic devices. Crafted with precision and expertise by Ajinomoto Fine-Techno Co., Inc., this substrate boasts exceptional electrical conductivity, thermal management capabilities, and mechanical robustness.
Featuring a carefully engineered layer configuration, the GL102R8HF substrate facilitates efficient signal routing and minimizes electromagnetic interference, ensuring optimal signal integrity and reliability. Its advanced material composition enables effective heat dissipation, crucial for maintaining the optimal operating temperature of semiconductor chips.
Engineered for manufacturability, the substrate design aligns with industry standards and processes, ensuring seamless integration into electronic device assembly lines. Rigorous reliability testing guarantees the substrate’s durability under various environmental conditions, promising long-term performance and stability.
In summary, Ajinomoto GL102R8HF package substrate represents a pinnacle of innovation and quality in semiconductor packaging, empowering electronic devices with superior functionality and longevity.
What is Ajinomoto GL102R8HF package substrate?
The Ajinomoto GL102R8HF is a type of package substrate commonly used in electronic devices, particularly in semiconductor packaging. Package substrates serve as the foundation for mounting and connecting semiconductor chips, facilitating the flow of electrical signals within the device.
Specifically, the GL102R8HF package substrate is likely manufactured by Ajinomoto Fine-Techno Co., Inc., a subsidiary of Ajinomoto Group specialized in the production of electronic materials, including package substrates. The “GL102R8HF” designation likely refers to specific dimensions, materials, and electrical properties of the substrate, although precise details may vary depending on the manufacturer’s specifications and the requirements of the electronic device being produced. These substrates are typically designed to provide high electrical conductivity, thermal management, and mechanical support for semiconductor chips.
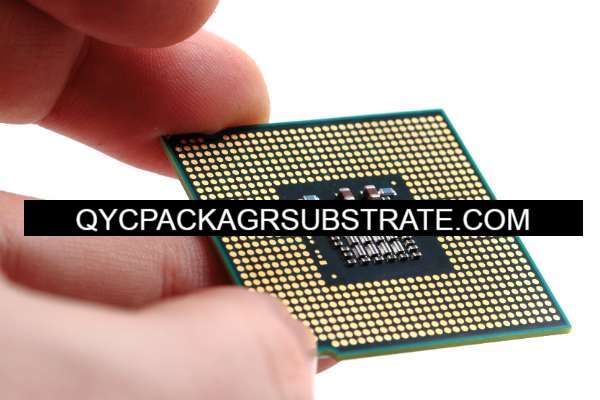
Ajinomoto GL102R8HF package substrate Manufacturer
What are the Ajinomoto GL102R8HF package substrate design guidelines?
Ajinomoto GL102R8HF is a specific type of package substrate used in electronic devices, particularly in semiconductor applications.
- Material Selection: Choose materials that offer excellent thermal conductivity, electrical insulation, and reliability. Common materials include FR-4, BT resin, polyimide, and ceramic substrates.
- Layer Stack-up: Design an optimal layer stack-up considering signal integrity, power delivery, and thermal management. This includes determining the number of signal layers, power/ground planes, and their respective placements.
- Routing Guidelines: Follow best practices for routing traces, vias, and pads to minimize signal distortion, crosstalk, and impedance mismatch. Use controlled impedance routing for high-speed signals.
- Via Design: Optimize via design for signal integrity and thermal performance. Use blind or buried vias for dense designs and thermal vias for heat dissipation.
- Thermal Management: Incorporate thermal vias, thermal pads, or heat spreaders to efficiently dissipate heat generated by components. Ensure adequate thermal relief for vias connected to thermal pads.
- Package Size and Shape: Design the package size and shape to accommodate the components and meet the requirements for mechanical stability, manufacturability, and assembly.
- Solder Mask and Silkscreen: Apply solder mask and silkscreen according to design requirements, ensuring proper solder mask relief for solder joints and clear labeling of components.
- Manufacturability: Design for manufacturability by considering fabrication processes such as drilling, plating, and solder mask application. Ensure that the design is compatible with the capabilities of the chosen manufacturing process.
- Reliability Considerations: Account for reliability factors such as thermal cycling, moisture absorption, and mechanical stress during design. Implement design features to enhance the substrate’s reliability and longevity.
- Compliance and Standards: Ensure compliance with industry standards and regulations relevant to package substrate design, such as IPC standards for PCB design.
Remember that specific design guidelines may vary depending on the application, manufacturing process, and specific requirements of the electronic device. It’s essential to consult with substrate manufacturers, design engineers, and other experts to ensure the optimal design of the package substrate for your application.
What is the Ajinomoto GL102R8HF package substrate fabrication process?
The specific fabrication process for the Ajinomoto GL102R8HF package substrate might be proprietary information and not publicly available. However, I can provide a general overview of the typical fabrication process for package substrates used in electronic devices:
- Substrate Material Selection: Choose the appropriate substrate material based on the application requirements. Common materials include FR-4, BT resin, polyimide, and ceramic substrates.
- Layer Formation: Begin by preparing the substrate material in the form of thin layers or sheets. These layers may undergo treatments such as cleaning, surface activation, and coating with adhesion-promoting materials.
- Lamination: Stack the prepared layers together, typically with layers of copper foil in between. Apply heat and pressure to laminate the layers into a single structure, forming the core substrate.
- Drilling: Use precision drilling equipment to create holes (vias) in the substrate for interconnecting different layers. Advanced techniques such as laser drilling may be employed for high-density designs.
- Through-hole Plating: Plate the walls of the drilled vias with a conductive material (typically copper) to establish electrical connections between layers.
- Copper Pattern Formation: Apply a layer of copper foil or a thin copper coating to the surfaces of the substrate. Use photolithography and etching processes to define the copper patterns for traces, pads, and other features according to the circuit design.
- Surface Finishing: Apply surface finishes to protect exposed copper surfaces from oxidation and facilitate soldering. Common surface finishes include HASL (Hot Air Solder Leveling), ENIG (Electroless Nickel Immersion Gold), OSP (Organic Solderability Preservatives), and immersion tin.
- Solder Mask Application: Apply solder mask over the substrate surface, leaving openings (exposed areas) for solder pads and vias. Solder mask provides insulation and protection for the copper traces and prevents solder bridges during assembly.
- Silkscreen Printing: Print component labels, reference indicators, and other identifying information onto the substrate using silkscreen printing. This helps during assembly and inspection processes.
- Final Inspection: Perform visual inspection, electrical testing, and other quality control measures to ensure that the fabricated substrate meets the required specifications and standards.
It’s important to note that the fabrication process may vary depending on factors such as the type of substrate material, design complexity, and manufacturing capabilities of the facility. Advanced processes, such as sequential build-up (SBU) technology and embedded passive components, may also be employed for specific applications. For detailed information on the fabrication process of a specific substrate like Ajinomoto GL102R8HF, it’s best to consult with the manufacturer or obtain proprietary documentation.
How do you manufacture an Ajinomoto GL102R8HF package substrate?
Manufacturing an Ajinomoto GL102R8HF package substrate likely involves a series of proprietary processes specific to Ajinomoto’s production facilities. While the exact details of their manufacturing process are not publicly available, I can provide a generalized overview of the typical steps involved in manufacturing package substrates, which might be similar to the processes used for GL102R8HF:
- Substrate Preparation: The process begins with preparing the substrate material. This may involve cutting the substrate material into appropriate sizes and shapes, cleaning to remove any contaminants, and surface treatment to promote adhesion.
- Layer Stacking: Multiple layers of substrate material and copper foils are laminated together to form a composite structure. The number and arrangement of layers depend on the design requirements of the substrate.
- Drilling: Precision drilling machines are used to create holes (vias) in the substrate. These vias will later be used for interconnecting different layers of the substrate.
- Copper Plating: The walls of the drilled vias and the surfaces of the substrate are plated with a conductive material, usually copper, to establish electrical connections between layers and to form the copper traces.
- Copper Pattern Formation:Photolithography and etching processes are used to define the copper patterns on the substrate. A photoresist layer is applied, exposed through a photomask with the desired pattern, developed to remove the unexposed areas, and then etched to remove the exposed copper, leaving behind the desired copper traces and pads.
- Surface Finishing: Various surface finishes are applied to protect the exposed copper surfaces, improve solderability, and prevent oxidation. Common surface finishes include HASL, ENIG, OSP, and immersion tin.
- Solder Mask Application: A solder mask layer is applied over the substrate surface, leaving openings (exposed areas) for solder pads, vias, and component mounting locations. The solder mask provides insulation and protection for the copper traces and prevents solder bridges during assembly.
- Silkscreen Printing: Component labels, reference indicators, and other identifying information are printed onto the substrate surface using silkscreen printing. This aids in component placement and assembly.
- Final Inspection and Testing: The manufactured substrates undergo rigorous inspection and testing processes to ensure that they meet the required specifications and quality standards. This includes visual inspection, electrical testing, and possibly other specialized tests.
- Packaging and Shipping: Once the substrates pass inspection, they are packaged appropriately and shipped to customers or downstream assembly facilities for further integration into electronic devices.
Throughout the manufacturing process, strict quality control measures are implemented to ensure the reliability, consistency, and performance of the package substrates. Additionally, specialized equipment and expertise are required to carry out each step effectively and efficiently.
How much should an Ajinomoto GL102R8HF package substrate cost?
The cost of an Ajinomoto GL102R8HF package substrate can vary significantly depending on various factors such as:
- Quantity: Typically, the larger the order quantity, the lower the cost per unit. Bulk orders often receive discounts compared to smaller quantities.
- Specifications: The specific design requirements and features of the substrate can affect its cost. For example, substrates with higher layer counts, finer trace widths, or specialized materials may be more expensive to manufacture.
- Technology: Advanced manufacturing technologies and processes, such as laser drilling or embedded passive components, can increase the cost of the substrate.
- Quality Standards: Substrates manufactured to meet higher quality standards or specific certifications may command a higher price.
- Supplier: Different suppliers may offer different pricing structures based on their overhead costs, manufacturing capabilities, and market positioning.
- Market Conditions: Supply and demand dynamics, as well as market competition, can influence the pricing of package substrates.
Without specific quotes from Ajinomoto or their distributors, it’s challenging to provide an exact cost for the GL102R8HF package substrate. However, it’s recommended to directly contact Ajinomoto or their authorized distributors to inquire about pricing based on your specific requirements and order quantity. They can provide you with accurate pricing information and potentially offer volume discounts or negotiate pricing based on your needs.
What is the base material of Ajinomoto GL102R8HF package substrate?
The base material of Ajinomoto GL102R8HF package substrate is not publicly disclosed, as it likely contains proprietary information. Ajinomoto, like many companies in the electronics industry, may use a variety of base materials for their package substrates, depending on factors such as performance requirements, manufacturing processes, and customer preferences.
However, common base materials used in package substrates for electronic devices include:
- FR-4 (Flame Retardant-4): FR-4 is a widely used substrate material made from woven fiberglass cloth impregnated with epoxy resin. It offers good mechanical strength, dimensional stability, and electrical insulation properties.
- BT (Bismaleimide-Triazine): BT resin is known for its high-temperature resistance and low dielectric constant, making it suitable for high-frequency and high-speed applications.
- Polyimide: Polyimide substrates, also known as “kapton” substrates, are flexible and offer excellent thermal stability and chemical resistance. They are commonly used in flexible and rigid-flex PCBs.
- Ceramic: Ceramic substrates provide superior thermal conductivity and mechanical properties compared to organic substrates. They are often used in high-power applications and in environments with extreme temperatures.
- Metal Core: Metal core substrates feature a layer of metal (typically aluminum or copper) sandwiched between layers of dielectric material. They offer efficient heat dissipation and are commonly used in LED lighting and power electronics.
It’s important to note that the choice of base material depends on the specific requirements of the application, such as thermal performance, electrical properties, and cost considerations. For detailed information about the base material used in Ajinomoto GL102R8HF package substrate, you would need to consult directly with Ajinomoto or refer to their proprietary documentation.
Which company manufactures Ajinomoto GL102R8HF package substrate?
The Ajinomoto GL102R8HF package substrate is manufactured by Ajinomoto Co., Inc., a Japanese company renowned in the fields of chemistry and biotechnology. As a globally recognized leader in food and seasoning industries, Ajinomoto also holds extensive business interests in electronic materials.
Our company is also capable of producing similar package substrates. While we may not match the scale and resources of Ajinomoto, we possess advanced technology and rich experience to meet customer demands. As part of our operations, we have the ability to manufacture high-quality package substrates while maintaining competitive prices.
Our manufacturing process includes the following steps:
- Substrate Material Preparation: We select substrate materials such as FR-4, BT resin, polyimide, etc., based on customer requirements and ensure their quality through necessary preprocessing.
- Layer Stacking and Lamination: Multiple layers of substrate material with copper foil are stacked and laminated under heat and pressure to form the core structure of the substrate.
- Drilling and Plating: Precise drilling creates holes (vias) on the substrate, followed by electroplating to establish inter-layer electrical connections.
- Copper Pattern Formation: Copper patterns are defined on the substrate using photolithography and etching processes to create desired copper traces and pads.
- Surface Treatment: Surface treatments are applied to exposed copper surfaces to enhance their corrosion resistance and solderability.
- Solder Mask and Labeling: Solder mask is applied to the substrate surface, and labeling is done using silk-screen printing.
- Final Inspection and Testing: Rigorous inspection and testing are conducted on the manufactured package substrates to ensure compliance with customer specifications and quality requirements.
Through our professional team and advanced equipment, we deliver high-quality, reliable package substrates tailored to meet customer needs in electronic product manufacturing. We are committed to collaborating with customers, providing customized solutions, and ensuring timely delivery along with excellent after-sales service.
What are the qualities of good customer service?
Good customer service is characterized by several qualities that contribute to positive interactions and relationships between a company and its customers. Some key qualities include:
- Empathy: Good customer service representatives are empathetic and understanding towards customers’ needs, concerns, and emotions. They listen actively, acknowledge customers’ feelings, and strive to address their issues effectively.
- Responsiveness: Quick and timely responses to customer inquiries, requests, and complaints are essential for providing good customer service. Customers appreciate being attended to promptly and receiving timely updates on the status of their inquiries or issues.
- Clear Communication: Effective communication is crucial for ensuring that customers understand information, instructions, and solutions provided by the company. Customer service representatives should communicate clearly, using simple language and avoiding technical jargon when necessary.
- Product Knowledge: Good customer service requires a thorough understanding of the company’s products or services. Representatives should be knowledgeable about product features, benefits, and usage guidelines, enabling them to provide accurate information and assistance to customers.
- Problem-Solving Skills: Customer service representatives should possess strong problem-solving skills to effectively address customers’ issues and resolve conflicts. They should be proactive in finding solutions and taking ownership of problems until they are resolved satisfactorily.
- Professionalism: Maintaining professionalism in all interactions with customers is essential for building trust and credibility. Customer service representatives should remain calm, courteous, and respectful, even in challenging situations, and refrain from making personal or derogatory remarks.
- Flexibility: Good customer service involves being flexible and adaptable to meet customers’ varying needs and preferences. Representatives should be willing to accommodate reasonable requests, explore alternative solutions, and tailor their approach to suit each customer’s situation.
- Follow-Up and Feedback: Following up with customers after resolving their issues or completing transactions demonstrates attentiveness and care. Additionally, soliciting feedback from customers about their experiences allows companies to identify areas for improvement and enhance the quality of their service.
- Consistency: Consistency in delivering high-quality service across all customer touchpoints and interactions is essential for building a strong reputation and fostering customer loyalty. Customers should receive consistent treatment and assistance regardless of the channel or representative they engage with.
- Going Above and Beyond: Exceptional customer service often involves going the extra mile to exceed customers’ expectations and create memorable experiences. Whether it’s offering personalized recommendations, providing additional assistance, or offering special discounts or perks, going above and beyond can leave a lasting impression on customers.
Overall, good customer service is about building positive relationships with customers by demonstrating empathy, responsiveness, professionalism, and a commitment to meeting their needs and exceeding their expectations.
FAQs
What is Ajinomoto GL102R8HF package substrate?
Ajinomoto GL102R8HF is a type of package substrate used in electronic devices, particularly in semiconductor applications. It provides a foundation for mounting and interconnecting electronic components.
What are the key features of Ajinomoto GL102R8HF?
The specific features of Ajinomoto GL102R8HF may vary, but typical features include high thermal conductivity, excellent electrical insulation properties, and reliability in demanding operating environments.
What applications is Ajinomoto GL102R8HF suitable for?
Ajinomoto GL102R8HF package substrates are commonly used in various electronic devices such as smartphones, tablets, computers, automotive electronics, and industrial equipment.
What materials are used in the construction of Ajinomoto GL102R8HF?
The exact materials used in Ajinomoto GL102R8HF package substrate may be proprietary information. However, common materials in package substrates include FR-4, BT resin, polyimide, and ceramic substrates.
What are the advantages of using Ajinomoto GL102R8HF package substrate?
Ajinomoto GL102R8HF package substrate offers benefits such as efficient heat dissipation, reliable electrical connectivity, and compatibility with high-density electronic components.
What design guidelines should be followed when using Ajinomoto GL102R8HF?
While specific design guidelines for Ajinomoto GL102R8HF may be proprietary, general design principles such as thermal management, signal integrity, and manufacturability should be considered.
Where can I purchase Ajinomoto GL102R8HF package substrate?
Ajinomoto GL102R8HF package substrates are typically available through authorized distributors or directly from Ajinomoto Co., Inc. It’s recommended to contact the company or their distributors for purchasing information.
Are there any certifications or standards compliance associated with Ajinomoto GL102R8HF?
Ajinomoto GL102R8HF package substrate may comply with industry standards and certifications relevant to electronic components and materials. Customers can inquire about specific certifications from Ajinomoto or their distributors.
Can Ajinomoto GL102R8HF be customized for specific applications?
Ajinomoto may offer customization services for GL102R8HF package substrate to meet specific customer requirements such as size, thickness, material composition, and additional features.
What technical support or documentation is available for Ajinomoto GL102R8HF?
Ajinomoto may provide technical support, datasheets, application notes, and other documentation to assist customers in using GL102R8HF package substrate effectively and efficiently.