Aluminum Nitride PCB manufacturing
Aluminum Nitride PCB Manufacturing, 96 AL2O3 Ceramic PCB, ALN Ceramic PCB, we offer products in the field: TEC Semiconductor thermoelectric refrigeration sheet, Sensor module package substrate, 3D ceramic packaging substrate, Lidar integrated substrate and other types Ceramic package substrates and PCBs.
Aluminum Nitride (AlN) PCBs are cutting-edge electronic substrates renowned for their exceptional thermal conductivity, electrical insulation properties, and mechanical robustness. These PCBs leverage aluminum nitride, a ceramic material, as their base, offering superior heat dissipation capabilities crucial for high-power applications. With their ability to efficiently transfer heat away from sensitive electronic components, AlN PCBs ensure optimal performance and reliability, even under demanding operating conditions.
Furthermore, AlN PCBs provide excellent electrical insulation, reducing the risk of short circuits and ensuring the integrity of signal transmission. Their mechanical strength and stability make them suitable for various electronic applications, including RF/microwave devices, power amplifiers, LED lighting, and high-frequency communication systems.
Manufactured with precision and expertise, Aluminum Nitride PCBs represent the pinnacle of modern electronic substrate technology. They empower engineers to design and develop innovative solutions that push the boundaries of electronic performance, making them indispensable in today’s technology-driven world.
What is an Aluminum Nitride PCB?
We are a professional Aluminum Nitride PCB manufacturing supplier, we mainly produce ultra-small bump pitch substrate, ultra-small trace and spacing packaging substrate and PCBs.
An Aluminum Nitride (AlN) PCB, also known as an AlN substrate or AlN-based printed circuit board, is a type of electronic substrate used in high-performance electronic applications.
Aluminum nitride is a ceramic material with excellent thermal conductivity, electrical insulation properties, and mechanical strength. These properties make it an ideal material for use in electronic substrates, especially in applications where high power densities and efficient heat dissipation are crucial.
AlN PCBs are used in a variety of applications, including high-power electronics, RF/microwave devices, power amplifiers, LED lighting, and high-frequency communication systems. They provide superior thermal management compared to traditional materials like FR-4 (a type of epoxy-based fiberglass) or ceramic substrates.
The manufacturing process for AlN PCBs typically involves depositing a thin layer of aluminum nitride onto a metal or ceramic base. This layer acts as the substrate for mounting electronic components, providing both electrical insulation and efficient heat transfer away from sensitive components.
Overall, Aluminum Nitride PCBs offer superior thermal performance, high electrical insulation, and mechanical stability, making them suitable for demanding electronic applications where reliability and performance are critical.
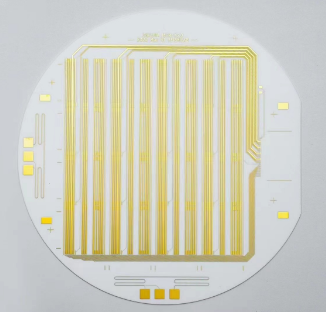
Aluminum Nitride PCB
What are the Aluminum Nitride PCB Design Guidelines?
Designing with Aluminum Nitride (AlN) PCBs requires attention to several key guidelines to ensure optimal performance and reliability. Here are some common design guidelines for Aluminum Nitride PCBs:
- Thermal Management: AlN PCBs are known for their excellent thermal conductivity. To leverage this property effectively, ensure that the design allows for efficient heat dissipation. Place high-power components strategically to minimize thermal gradients and hot spots. Use thermal vias to improve heat transfer from the components to the AlN substrate.
- Dielectric Layer Thickness: The dielectric layer thickness on AlN PCBs affects electrical performance. Typically, thinner dielectric layers offer better RF performance but may compromise mechanical strength. Balance the dielectric thickness based on the specific requirements of your application.
- Via Placement: Carefully plan the placement of vias to minimize signal distortion and impedance mismatches. Use via stitching or via fences for RF applications to maintain signal integrity and reduce electromagnetic interference (EMI).
- Component Placement: Place components with consideration for thermal management and signal integrity. Keep high-power components away from sensitive signal traces to avoid interference. Follow recommended component spacing guidelines to prevent overheating and ensure proper airflow.
- Grounding and Shielding: Implement proper grounding techniques to minimize ground loops and noise. Use dedicated ground planes and shielding techniques to isolate sensitive signals from external interference sources.
- Trace Width and Spacing: Design trace widths and spacing according to the current carrying capacity and signal requirements. Ensure adequate clearance between traces to prevent signal crosstalk and maintain isolation between high-voltage and low-voltage circuits.
- Material Selection: Choose compatible materials for soldering and assembly processes. AlN PCBs often require specialized handling due to their ceramic nature. Ensure that the chosen materials are compatible with AlN substrates and assembly methods.
- Environmental Considerations: Consider the operating environment of the PCB, including temperature fluctuations, humidity, and exposure to corrosive substances. Select materials and coatings that can withstand these conditions for long-term reliability.
- Testing and Validation: Conduct thorough testing and validation of the AlN PCB design to ensure compliance with performance specifications and reliability requirements. Perform simulations and prototypes to verify thermal and electrical performance under various operating conditions.
By following these guidelines, designers can create Aluminum Nitride PCBs that meet the stringent requirements of high-performance electronic applications while ensuring reliability and longevity.
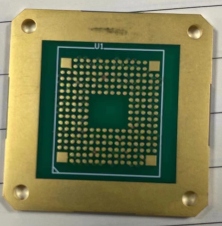
Ceramic Substrate
What is the Aluminum Nitride PCB Fabrication Process?
The fabrication process for Aluminum Nitride (AlN) PCBs involves several steps to produce the final substrate for electronic components. Here’s a general overview of the fabrication process:
- Substrate Preparation: The process begins with preparing the base material, typically a metal or ceramic substrate. Common substrate materials include aluminum, copper, or ceramic materials such as alumina (Al2O3). The substrate is cleaned and prepared to ensure proper adhesion of subsequent layers.
- Aluminum Nitride Deposition: A thin layer of aluminum nitride (AlN) is deposited onto the substrate surface. This can be achieved through various techniques such as physical vapor deposition (PVD), chemical vapor deposition (CVD), or sputtering. The AlN layer provides the electrical insulation and thermal properties required for the PCB.
- Dielectric Layer Deposition (Optional): Depending on the specific requirements of the PCB design, additional dielectric layers may be deposited on top of the AlN layer. These layers can provide further insulation and protection for the electronic components.
- Conductor Patterning: Next, conductive traces are patterned onto the substrate to create the desired circuit layout. This is typically done using photolithography, where a photoresist layer is applied to the substrate, exposed to UV light through a mask, and then developed to create the circuit pattern. The exposed areas are then etched away, leaving behind the conductive traces.
- Via Drilling and Plating: Vias are drilled through the substrate to create electrical connections between different layers of the PCB. After drilling, the vias are plated with conductive material (usually copper) to ensure good electrical conductivity between layers.
- Surface Finish: The surface of the PCB is coated with a surface finish to protect the conductive traces and provide solderability. Common surface finishes include immersion silver, immersion tin, ENIG (Electroless Nickel Immersion Gold), or OSP (Organic Solderability Preservatives).
- Final Inspection and Testing: Once the fabrication process is complete, the PCB undergoes inspection and testing to ensure it meets the required specifications and quality standards. This may include visual inspection, electrical testing, and dimensional measurements.
- Assembly: After fabrication, the AlN PCB is ready for component assembly. Electronic components such as integrated circuits, resistors, capacitors, and connectors are mounted onto the PCB using soldering techniques or other bonding methods.
Overall, the fabrication process for Aluminum Nitride PCBs combines precision manufacturing techniques with specialized materials to produce high-performance substrates for demanding electronic applications.
How do you manufacture an Aluminum Nitride PCB?
Manufacturing an Aluminum Nitride (AlN) PCB involves the following steps:
- Substrate Preparation: Select an appropriate substrate material, typically a metal or ceramic substrate such as aluminum, copper, or alumina (Al2O3). Clean and treat the substrate to ensure adhesion of subsequent layers.
- Aluminum Nitride Deposition: Deposit a thin layer of aluminum nitride using techniques like physical vapor deposition (PVD), chemical vapor deposition (CVD), or sputtering onto the substrate surface. This layer provides electrical insulation and thermal properties.
- Patterning: Use photolithography to pattern conductive traces onto the aluminum nitride layer. This involves applying photoresist, exposure, development, and etching to create the desired circuit pattern.
- Via Drilling: Drill holes through the PCB using techniques like laser drilling or mechanical drilling to create vias. These vias establish electrical connections between different layers.
- Metallization: Plate metal, usually copper, onto the vias created through drilling to establish interlayer electrical connections.
- Surface Treatment: Coat the PCB surface with a surface treatment to protect the conductive traces and provide solderability. Common surface treatments include immersion silver, immersion tin, ENIG (Electroless Nickel Immersion Gold), or OSP (Organic Solderability Preservatives).
- Final Inspection and Testing: Inspect and test the finished PCB to ensure compliance with specifications and quality standards. This may include visual inspection, electrical testing, and dimensional measurements.
- Assembly: The finished AlN PCB is ready for component assembly. Electronic components such as integrated circuits, resistors, capacitors, and connectors are mounted onto the PCB using soldering techniques or other bonding methods.
These steps constitute the basic process for manufacturing Aluminum Nitride PCBs. They ensure that the PCB possesses the required electrical, thermal, and reliability properties suitable for various high-performance electronic applications.
How much should an Aluminum Nitride PCB cost?
The cost of an Aluminum Nitride (AlN) PCB can vary depending on several factors, including the size, complexity, quantity, and specific requirements of the PCB. Generally, AlN PCBs tend to be more expensive compared to traditional FR-4 PCBs due to the specialized materials and manufacturing processes involved.
Here are some factors that can influence the cost of an AlN PCB:
- Material Cost: Aluminum nitride is more expensive than traditional PCB substrates like FR-4. The cost of the raw material contributes significantly to the overall cost of the PCB.
- Manufacturing Processes: The fabrication processes involved in manufacturing AlN PCBs, such as deposition techniques, photolithography, and specialized surface treatments, can be more complex and costly compared to standard PCB manufacturing processes.
- Design Complexity: PCBs with intricate designs, tight tolerances, or multiple layers will generally cost more to manufacture due to the increased time and complexity involved in production.
- Quantities: Larger quantities of AlN PCBs typically lead to lower unit costs due to economies of scale. However, setting up production for small quantities may incur higher setup costs per unit.
- Additional Features: Specialized features such as impedance control, blind vias, buried vias, and controlled dielectric constant may add to the cost of the PCB.
- Lead Time: Expedited manufacturing or shorter lead times may come with additional costs due to the need to prioritize production resources.
To get an accurate cost estimate for an AlN PCB, it’s best to consult with PCB manufacturers or suppliers. They can provide quotes based on your specific requirements, including design specifications, quantity, lead time, and any additional features needed.
What is Aluminum Nitride PCB base material?
The base material of an Aluminum Nitride (AlN) PCB is, unsurprisingly, aluminum nitride. Aluminum nitride is a ceramic compound composed of aluminum and nitrogen atoms (AlN). It has excellent thermal conductivity, electrical insulation properties, and mechanical strength, making it an ideal substrate material for high-performance electronic applications.
Aluminum nitride PCBs typically consist of a thin layer of aluminum nitride deposited onto a metal or ceramic base substrate. This aluminum nitride layer serves as the foundation for mounting electronic components and provides the necessary electrical insulation and thermal management properties required for the PCB.
Overall, aluminum nitride is the key material that forms the base substrate of an Aluminum Nitride PCB, offering superior performance in terms of thermal conductivity and electrical insulation compared to traditional substrate materials like FR-4 (epoxy-based fiberglass) or ceramic substrates.
Which company makes Aluminum Nitride PCBs?
Currently, there are several companies producing Aluminum Nitride (AlN) PCBs, including some well-known manufacturers both domestically and internationally. Some major foreign manufacturers include Rogers Corporation, CeramTec, Kyocera, CoorsTek, among others. These companies possess advanced manufacturing technologies and extensive experience, enabling them to offer high-quality AlN PCB products.
In China, some specialized PCB manufacturers have also entered the field of aluminum nitride PCBs. They continuously enhance product quality and manufacturing capabilities by introducing advanced production equipment and technologies to meet market demands.
As a professional PCB manufacturer, our company is also capable of producing Aluminum Nitride PCBs. We have advanced production equipment and a skilled technical team, enabling us to customize high-quality, high-performance AlN PCBs for our customers. Our production processes strictly adhere to international standards, ensuring stable and reliable product quality. We can customize AlN PCBs of different sizes, thicknesses, and layer counts according to customer requirements, and provide various surface treatments and special process options. Whether the customer’s needs are for high-power electronics, RF/microwave devices, LED lighting, or other high-performance applications, we can provide AlN PCB solutions that meet their requirements.
We are committed to providing customers with high-quality products and professional services, establishing long-term and stable cooperative relationships with them. We will continue to pursue technological innovation and excellence in quality to meet the evolving needs of our customers, striving for successful collaboration with them.
Qualities of Good Customer Service:
Qualities of good customer service include:
- Responsiveness: Good customer service involves being prompt and timely in responding to customer inquiries, concerns, and requests. This includes acknowledging customer communications quickly and providing timely resolutions to their issues.
- Empathy: Empathy is crucial in understanding and acknowledging the customer’s perspective and emotions. Good customer service representatives listen actively, show genuine concern for the customer’s needs, and strive to address their concerns empathetically.
- Clear Communication: Effective communication is essential for providing good customer service. Customer service representatives should communicate clearly, using language that is easy to understand, and provide accurate information to help customers make informed decisions or resolve issues.
- Problem-Solving Skills: Good customer service involves the ability to identify and address customer problems effectively. Customer service representatives should possess strong problem-solving skills to analyze situations, identify root causes of issues, and propose appropriate solutions to resolve them.
- Product Knowledge: Customer service representatives should have in-depth knowledge about the products or services offered by the company. This enables them to answer customer questions accurately, provide product recommendations, and offer valuable assistance in product selection or troubleshooting.
- Professionalism: Good customer service requires professionalism in all interactions with customers. This includes maintaining a courteous and respectful demeanor, maintaining confidentiality, and adhering to company policies and procedures.
- Proactive Support: Anticipating customer needs and providing proactive support can enhance the customer experience. Good customer service representatives go above and beyond by offering assistance, suggestions, or additional information to help customers before they even ask.
- Follow-Up: Following up with customers after resolving an issue or completing a transaction shows care and commitment to their satisfaction. Good customer service includes checking in with customers to ensure that their needs were met and addressing any further concerns they may have.
- Adaptability: Customer service representatives should be adaptable and flexible in their approach to different customer situations. They should be able to tailor their communication style and problem-solving approach to meet the unique needs of each customer.
- Continuous Improvement: Finally, good customer service involves a commitment to continuous improvement. Companies should regularly gather feedback from customers, evaluate their service delivery processes, and implement changes or enhancements to improve the overall customer experience.
FAQs
What are the advantages of Aluminum Nitride PCBs?
Aluminum Nitride PCBs offer excellent thermal conductivity, electrical insulation, and reliability, making them ideal for applications requiring efficient heat dissipation.
Can Aluminum Nitride PCBs be used in high-power electronic devices?
Yes, Aluminum Nitride PCBs are suitable for high-power electronic devices due to their superior thermal management capabilities.
How do I choose between Aluminum Nitride and other PCB materials?
Consider factors such as thermal requirements, operating environment, cost, and specific application needs when choosing between Aluminum Nitride and other PCB materials.
What are the limitations of Aluminum Nitride PCBs?
Aluminum Nitride PCBs may be more expensive compared to traditional materials, and their use may require specialized fabrication processes and equipment.
Is Aluminum Nitride PCB manufacturing environmentally friendly?
Aluminum Nitride PCB manufacturing can be environmentally friendly if proper waste management and recycling practices are implemented during production processes.
Can Aluminum Nitride PCBs be used in consumer electronics?
Yes, Aluminum Nitride PCBs can be used in various consumer electronics, especially those requiring efficient heat dissipation, such as LED lighting systems and power electronics.