Aviation Substrate Manufacturer
What is Aviation Substrate (AS)?
Aviation Substrate Manufacturer and BGA package substrate Supplier. We use advanced Msap and Sap technology to produce the High multilayer interconnection bga substrates from 4 to 22 layers.
Aviation Substrate (AS) refers to a comprehensive framework of technologies and systems designed specifically for aviation applications. It encompasses various components such as hardware, software, communication protocols, and interfaces tailored to meet the demanding requirements of the aviation industry.
At its core, AS provides a solid foundation for the development and operation of aviation-related systems, including aircraft avionics, ground control stations, navigation systems, communication networks, and unmanned aerial vehicles (UAVs). AS is engineered to ensure safety, reliability, and efficiency in aviation operations, adhering to stringent standards and regulations set forth by aviation authorities worldwide.
AS facilitates the integration of cutting-edge technologies such as artificial intelligence, machine learning, advanced sensors, and data analytics into aviation systems, enabling enhanced capabilities such as autonomous flight, predictive maintenance, airspace management, and mission planning. By leveraging AS, aviation stakeholders can streamline operations, improve situational awareness, optimize resource utilization, and ultimately enhance the overall safety and performance of aviation systems.
Furthermore, AS is designed with scalability and interoperability in mind, allowing seamless integration with existing aviation infrastructure and future technologies. This flexibility enables continuous innovation and adaptation to evolving operational requirements and technological advancements in the dynamic field of aviation.
In summary, Aviation Substrate (AS) serves as a robust technological foundation that underpins the development, deployment, and operation of aviation systems, offering a comprehensive suite of capabilities to meet the evolving needs of the aviation industry.
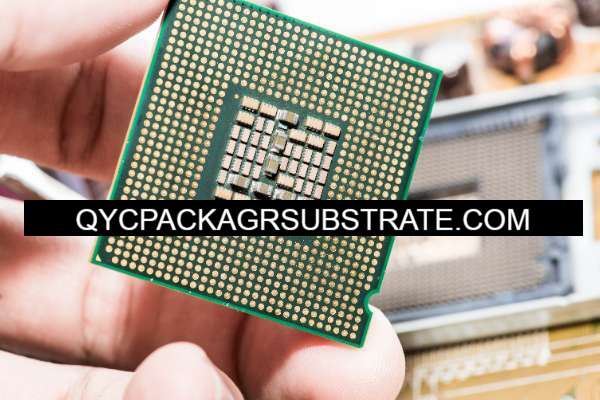
Aviation Substrate Manufacturer
What are the Aviation Substrate (AS) Design Guidelines?
The Aviation Substrate (AS) Design Guidelines outline a set of principles, standards, and best practices for the development, implementation, and integration of aviation-related technologies and systems. These guidelines serve as a framework to ensure consistency, reliability, safety, and efficiency across various aspects of aviation operations. Here’s an expanded explanation:
- Safety-Centric Design: AS design prioritizes safety above all else. This includes rigorous risk assessment, fault tolerance, redundancy, and fail-safe mechanisms to mitigate potential hazards and ensure safe operation in all conditions.
- Regulatory Compliance: AS adheres to relevant aviation regulations and standards established by civil aviation authorities such as the Federal Aviation Administration (FAA) in the United States, the European Union Aviation Safety Agency (EASA), and others. Compliance with these regulations is essential to ensure airworthiness and legal compliance.
- Modularity and Scalability: AS promotes a modular design approach, allowing components and subsystems to be developed and integrated independently. This modularity enhances flexibility, facilitates upgrades, and enables scalability to accommodate evolving operational requirements and technological advancements.
- Interoperability: AS emphasizes interoperability between different aviation systems and components, enabling seamless communication, data exchange, and integration across diverse platforms and networks. Standardized interfaces, protocols, and data formats facilitate interoperability and compatibility among interconnected systems.
- Cybersecurity: AS incorporates robust cybersecurity measures to safeguard aviation systems against cyber threats, including unauthorized access, data breaches, malware, and cyberattacks. Security features such as encryption, authentication, access control, and intrusion detection are integral components of AS design to protect critical aviation assets and data.
- Data Integrity and Reliability: AS ensures the integrity, accuracy, and reliability of data collected, processed, and transmitted within aviation systems. This includes data validation, error detection and correction, redundancy, data integrity checks, and synchronization mechanisms to maintain data consistency and reliability.
- Human Factors and User Experience: AS considers human factors and user experience in design to optimize usability, ergonomics, and human-machine interaction. Intuitive user interfaces, clear feedback mechanisms, ergonomic design principles, and comprehensive training programs enhance operator performance, situational awareness, and decision-making capabilities.
- Resilience and Continuity of Operations: AS incorporates resilience and continuity measures to maintain operational functionality in the face of disruptions, failures, or adverse conditions. Redundant systems, backup power sources, disaster recovery plans, and contingency procedures ensure uninterrupted operation and mission continuity.
- Lifecycle Management and Maintenance:AS encompasses lifecycle management practices to support the development, deployment, operation, and maintenance of aviation systems throughout their lifecycle. This includes configuration management, version control, maintenance scheduling, performance monitoring, and proactive maintenance strategies to optimize system reliability, availability, and maintainability.
- Ethical Considerations: AS design takes into account ethical considerations such as privacy, accountability, transparency, and societal impacts. Ethical guidelines ensure responsible use of aviation technologies, respect for individual rights, and ethical decision-making in the development and deployment of aviation systems.
In summary, the Aviation Substrate (AS) Design Guidelines provide a comprehensive framework for the design, development, and integration of aviation technologies and systems, emphasizing safety, regulatory compliance, modularity, interoperability, cybersecurity, data integrity, human factors, resilience, lifecycle management, and ethical considerations to ensure the reliability, efficiency, and safety of aviation operations.
What is the Aviation Substrate (AS) Fabrication Process?
The Aviation Substrate (AS) fabrication process involves several stages, each aimed at creating components and systems that adhere to the stringent requirements of the aviation industry. While the specifics may vary depending on the nature of the component or system being fabricated, the following steps provide a general overview of the AS fabrication process:
- Requirements Analysis: The process begins with a thorough analysis of the requirements for the aviation component or system. This involves understanding the functional, performance, safety, regulatory, and environmental requirements that the AS must meet.
- Design and Engineering: Based on the requirements analysis, engineers develop detailed designs for the AS components or systems. This includes selecting appropriate materials, determining manufacturing processes, and creating digital models and blueprints.
- Prototyping: Prototyping is often conducted to validate the design and functionality of AS components or systems. Prototypes may be created using rapid prototyping techniques such as 3D printing or traditional machining processes, depending on the complexity and scale of the component or system.
- Manufacturing: Once the design is finalized and validated, the manufacturing process begins. This typically involves machining, molding, casting, welding, or additive manufacturing techniques to fabricate the individual components of the AS. Precision manufacturing processes are employed to ensure tight tolerances and high-quality standards.
- Assembly: After the individual components are fabricated, they are assembled into larger subsystems or complete systems according to the design specifications. Assembly may involve mechanical fastening, welding, adhesive bonding, or other joining techniques to integrate the components into a cohesive unit.
- Integration and Testing: Once assembled, the AS undergoes rigorous integration and testing to verify its functionality, performance, and compliance with safety and regulatory requirements. This includes functional testing, stress testing, environmental testing (e.g., temperature, vibration, humidity), and, in some cases, certification testing by regulatory authorities.
- Quality Assurance and Inspection:Throughout the fabrication process, quality assurance procedures are implemented to ensure that the AS components and systems meet the highest standards of quality and reliability. Inspection techniques such as dimensional inspection, non-destructive testing, and material analysis may be employed to identify and rectify any defects or inconsistencies.
- Documentation and Certification: Documentation is generated throughout the fabrication process to record specifications, procedures, test results, and other relevant information. Once the AS components or systems have successfully passed all tests and inspections, they may undergo certification by aviation authorities to validate their airworthiness and regulatory compliance.
- Packaging and Delivery: Finally, the fabricated AS components or systems are packaged and prepared for delivery to the end-users, whether they are aircraft manufacturers, operators, or maintenance facilities. Packaging may include protective measures to ensure the integrity of the components during transit and storage.
Overall, the Aviation Substrate (AS) fabrication process is a highly structured and controlled process that prioritizes quality, safety, and reliability to meet the demanding requirements of the aviation industry. Collaboration among engineers, manufacturers, quality assurance personnel, and regulatory authorities is essential to ensure the successful fabrication and deployment of AS components and systems.
How do you Manufacture Aviation Substrate (AS)?
Manufacturing Aviation Substrate (AS) involves a systematic process tailored to meet the stringent requirements of the aviation industry. Here’s a step-by-step guide to manufacturing AS:
- Material Selection: Choose materials that meet the performance, durability, and safety standards required for aviation applications. Common materials include lightweight metals like aluminum and titanium, composite materials such as carbon fiber reinforced polymers (CFRP), and high-strength alloys.
- Design and Engineering: Develop detailed designs and engineering specifications for AS components or systems. Utilize computer-aided design (CAD) software to create precise digital models and blueprints that account for structural integrity, aerodynamics, thermal properties, and other relevant factors.
- Manufacturing Planning: Plan the manufacturing process, considering factors such as production volume, lead times, equipment availability, and resource allocation. Develop a manufacturing schedule and identify any specialized tools or machinery required for the fabrication process.
- Fabrication Techniques: Employ advanced manufacturing techniques such as CNC machining, additive manufacturing (3D printing), precision casting, forging, or composite layup to fabricate AS components with tight tolerances and high-quality standards. Each technique may be selected based on the specific geometry, material properties, and production requirements of the component.
- Quality Control: Implement rigorous quality control measures throughout the manufacturing process to ensure that AS components meet the required standards for dimensional accuracy, material properties, surface finish, and structural integrity. Utilize inspection tools and techniques such as coordinate measuring machines (CMM), non-destructive testing (NDT), and visual inspection to verify quality at each stage of production.
- Assembly: Assemble fabricated components into larger subsystems or complete AS systems according to the design specifications. Utilize precision assembly techniques such as robotic automation, mechanical fastening, adhesive bonding, or welding to ensure proper alignment and structural integrity.
- Testing and Validation: Subject AS components and systems to comprehensive testing and validation procedures to verify functionality, performance, and compliance with safety and regulatory requirements. Testing may include functional testing, stress testing, environmental testing (e.g., temperature, vibration, humidity), and performance testing under simulated operating conditions.
- Certification and Compliance: Ensure that AS components and systems comply with applicable aviation regulations and standards, such as those set forth by the Federal Aviation Administration (FAA) in the United States or the European Union Aviation Safety Agency (EASA). Obtain necessary certifications and approvals to validate airworthiness and regulatory compliance.
- Documentation and Traceability: Maintain detailed documentation throughout the manufacturing process to record specifications, procedures, test results, and other relevant information. Establish traceability of materials and processes to facilitate quality assurance, troubleshooting, and regulatory compliance.
- Packaging and Delivery: Package AS components or systems securely for transportation and delivery to customers, aircraft manufacturers, operators, or maintenance facilities. Ensure that packaging provides adequate protection to prevent damage during transit and storage.
By following these steps, manufacturers can produce Aviation Substrate (AS) components and systems that meet the highest standards of quality, safety, and reliability required for aviation applications. Collaboration among engineers, manufacturers, quality assurance personnel, and regulatory authorities is essential to ensure successful manufacturing and deployment of AS.
How much should Aviation Substrate (AS) cost?
Determining the cost of Aviation Substrate (AS) can be complex and depends on various factors including the specific components or systems involved, their complexity, performance requirements, manufacturing techniques, materials used, regulatory compliance, and market dynamics. However, here are some considerations to help estimate the cost:
- Component Complexity: More complex AS components or systems typically involve higher manufacturing costs due to increased engineering effort, precision manufacturing techniques, and assembly processes.
- Materials: The choice of materials significantly impacts the cost of AS. Lightweight materials such as advanced composites and titanium alloys tend to be more expensive than conventional metals like aluminum, but they offer benefits such as reduced weight and increased strength.
- Manufacturing Techniques: Advanced manufacturing techniques such as CNC machining, additive manufacturing, and composite layup may require specialized equipment and expertise, impacting production costs.
- Regulatory Compliance: Ensuring compliance with aviation regulations and certification requirements can add costs associated with testing, validation, documentation, and certification processes.
- Economy of Scale:Production volume can affect unit costs, with larger production runs generally leading to lower per-unit costs due to economies of scale.
- Research and Development: If the AS involves innovative technologies or custom solutions, research and development costs may be significant and contribute to the overall cost.
- Market Demand and Competition: Market dynamics, including supply and demand, competition, and industry trends, can influence pricing. Unique or specialized AS solutions may command higher prices in the market.
- Lifecycle Costs: Consideration should be given to the lifecycle costs of AS, including maintenance, repair, and operational expenses over the lifespan of the component or system.
Given these factors, the cost of Aviation Substrate (AS) can vary widely. It’s essential for manufacturers and customers to conduct thorough cost analysis, considering all relevant factors, to determine a fair and competitive price for AS components and systems. Additionally, pricing should reflect the value proposition, performance benefits, and competitive advantages offered by the AS in comparison to alternative solutions.
What is Aviation Substrate (AS) Base Material?
The base material used in Aviation Substrate (AS) can vary depending on the specific application, performance requirements, and manufacturing considerations. However, some common base materials used in AS fabrication include:
- Aluminum Alloys: Aluminum and its alloys are widely used in aviation due to their lightweight properties, corrosion resistance, and ease of machining. They are commonly employed in structural components, airframes, and aerospace fasteners.
- Titanium Alloys:Titanium alloys offer high strength-to-weight ratio, excellent corrosion resistance, and heat resistance, making them suitable for critical components in aircraft engines, landing gear, and structural applications where strength and durability are paramount.
- Composite Materials: Composite materials, such as carbon fiber reinforced polymers (CFRP) and fiberglass, are increasingly used in aviation for their exceptional strength-to-weight ratio, stiffness, and fatigue resistance. They are utilized in components such as fuselage panels, wings, and rotor blades to reduce weight and improve fuel efficiency.
- Steel Alloys: Certain applications in aviation, particularly in landing gear and engine components, may require the use of steel alloys due to their high strength, toughness, and heat resistance properties.
- High-Performance Plastics: Engineering plastics such as polyetheretherketone (PEEK) and polyphenylene sulfide (PPS) are utilized in AS for their lightweight, chemical resistance, and thermal stability. They are often used in interior components, electrical insulation, and non-structural applications.
- Ceramic Matrix Composites (CMC): CMCs offer exceptional heat resistance and mechanical properties at high temperatures, making them suitable for use in aircraft engines, exhaust components, and thermal protection systems.
The selection of base material for AS depends on factors such as the specific application, operating environment, performance requirements, regulatory compliance, cost considerations, and manufacturing feasibility. Engineers and designers carefully evaluate these factors to choose the most appropriate material that meets the demanding requirements of the aviation industry while optimizing performance, reliability, and cost-effectiveness.
Which company manufactures Aviation Substrate (AS)?
Currently, many aerospace companies are manufacturing and developing Aviation Substrate (AS). These companies include well-known global enterprises as well as small companies specializing in the aerospace field. They are dedicated to researching, developing, and manufacturing various AS components and systems, including aircraft avionics systems, UAV platforms, aviation communication equipment, navigation systems, and more.
Our company is also capable of manufacturing Aviation Substrate (AS). As a company focused on the aerospace field, we possess advanced technology and equipment, as well as an experienced team of engineers and technicians. Our production line can meet various manufacturing requirements for AS components and systems, ensuring they adhere to strict quality standards and industry requirements.
Our manufacturing capabilities include but are not limited to the following aspects:
- Design and Engineering:We have a professional design team capable of designing AS components and systems according to customer requirements and specifications. We utilize advanced computer-aided design (CAD) software and simulation tools to ensure design schemes meet performance requirements and airworthiness standards.
- Manufacturing Technology: Our production line is equipped with advanced manufacturing equipment and processes capable of processing and forming various materials. We can utilize advanced technologies such as CNC machining, additive manufacturing, etc., to precisely manufacture AS components with complex geometries and precision parts.
- Quality Control: We strictly adhere to quality control procedures to ensure every production process meets quality standards and regulatory requirements. We utilize advanced inspection equipment and techniques to conduct comprehensive quality inspections and tests, ensuring the reliability of AS components.
- Certification and Compliance: Our production processes comply with relevant certifications and regulatory requirements in the aerospace industry. Our AS components and systems can undergo rigorous testing and certification processes to obtain necessary approvals, ensuring they meet aviation safety standards and regulatory requirements.
In summary, our company possesses the technological strength, production capacity, and quality assurance capabilities required to manufacture Aviation Substrate (AS). We are committed to providing customers with high-quality and reliable AS components and systems to meet their aerospace application needs.
What are the 7 qualities of good customer service?
Good customer service is essential for building positive relationships with customers and ensuring their satisfaction. Here are seven qualities that contribute to providing excellent customer service:
- Responsiveness: Responding promptly to customer inquiries, concerns, and requests demonstrates attentiveness and a commitment to addressing their needs in a timely manner. Whether it’s through phone, email, chat, or in-person interactions, being responsive shows that you value the customer’s time and prioritize their concerns.
- Empathy: Empathy involves understanding and acknowledging the customer’s feelings, concerns, and perspectives. By putting yourself in the customer’s shoes and demonstrating genuine empathy, you can build rapport, establish trust, and create a more positive customer experience.
- Clear Communication: Effective communication is crucial for conveying information clearly and accurately to customers. This includes listening actively to understand their needs, providing clear explanations and instructions, and ensuring that communication channels are open and accessible for customers to reach out with questions or feedback.
- Professionalism:Maintaining a professional demeanor and attitude in all customer interactions is essential for establishing credibility and trust. This includes being courteous, respectful, and polite, even in challenging situations. Demonstrating professionalism instills confidence in customers and reflects positively on the company’s reputation.
- Problem-Solving Skills: Good customer service involves the ability to effectively address and resolve customer issues and complaints. This requires strong problem-solving skills, critical thinking, and resourcefulness to identify solutions and take appropriate action to resolve problems to the customer’s satisfaction.
- Flexibility: Being flexible and adaptable to meet the diverse needs and preferences of customers is important for delivering personalized service. This may involve accommodating special requests, customizing solutions, or adjusting policies and procedures when necessary to better serve the customer’s needs.
- Consistency: Consistency in service delivery helps build trust and reliability with customers. It involves providing a consistent level of quality and experience across all customer touchpoints, whether it’s in-store interactions, online transactions, or customer support channels. Consistency ensures that customers know what to expect and helps foster long-term loyalty.
By embodying these qualities, businesses can deliver exceptional customer service experiences that not only meet but exceed customer expectations, fostering customer satisfaction, loyalty, and advocacy.
FAQs (Frequently Asked Questions)
What is Aviation Substrate (AS)?
Aviation Substrate (AS) refers to a comprehensive framework of technologies and systems designed specifically for aviation applications. It encompasses various components such as hardware, software, communication protocols, and interfaces tailored to meet the demanding requirements of the aviation industry.
What are the key components of Aviation Substrate (AS)?
The key components of AS include aircraft avionics, ground control stations, navigation systems, communication networks, and unmanned aerial vehicles (UAVs). These components work together to ensure the safe and efficient operation of aviation systems.
What are the benefits of using Aviation Substrate (AS)?
Using AS offers several benefits, including enhanced safety, reliability, efficiency, and performance of aviation systems. AS facilitates the integration of cutting-edge technologies such as artificial intelligence, machine learning, and data analytics, enabling capabilities such as autonomous flight, predictive maintenance, and airspace management.
How is Aviation Substrate (AS) different from other aviation technologies?
AS differs from other aviation technologies in that it provides a comprehensive framework specifically tailored for aviation applications. While other technologies may focus on specific components or functionalities, AS encompasses a wide range of components and systems designed to meet the diverse needs of the aviation industry.
Is Aviation Substrate (AS) compliant with aviation regulations?
Yes, AS is designed to comply with relevant aviation regulations and standards established by civil aviation authorities such as the Federal Aviation Administration (FAA) in the United States, the European Union Aviation Safety Agency (EASA), and others. Compliance with these regulations is essential to ensure airworthiness and legal compliance.
How can Aviation Substrate (AS) improve aviation operations?
AS can improve aviation operations by enhancing safety, reliability, efficiency, and performance. By leveraging advanced technologies and standardized interfaces, AS enables capabilities such as autonomous flight, predictive maintenance, real-time data analytics, and optimized airspace management, leading to improved operational effectiveness and reduced costs.
Is Aviation Substrate (AS) customizable for specific aviation applications?
Yes, AS is highly customizable to meet the specific requirements and preferences of different aviation applications. Whether it’s for commercial aircraft, military drones, air traffic management systems, or other aviation platforms, AS can be tailored to accommodate various operational needs and performance criteria.