BT resin substrate manufacturing
BT resin substrate manufacturing. BT led pcb, BT bga substrates Vendor, we offer high quality BT PCB substrates from 2 layer to 22 layers. smallest gap and microtrace PCB substrates. BT resin substrate is a high-performance material used in electronics manufacturing, consisting of bismaleimide triazine (BT) resin. Renowned for its excellent thermal performance and mechanical strength, this substrate is widely utilized in the fabrication of printed circuit boards (PCBs). Withstanding extreme temperatures and harsh environmental conditions, BT resin substrate exhibits outstanding heat resistance, chemical resistance, and electrical insulation properties. Its high thermal conductivity and superior dimensional stability make it a preferred choice for high-power electronic devices, automotive, aerospace, and other industries. In PCB manufacturing, BT resin substrate serves as the core material for multi-layer boards, providing a reliable foundation for intricate circuit designs. Overall, the characteristics of BT resin substrate make it an indispensable component in modern electronics manufacturing, contributing significantly to the performance and reliability of products.
What is a BT Resin Substrate?
A BT resin substrate refers to a type of material used in electronics manufacturing, particularly in the fabrication of printed circuit boards (PCBs). “BT” stands for “bismaleimide triazine,” which is a type of resin known for its excellent thermal and mechanical properties, making it ideal for high-performance applications.
BT resin substrates are characterized by their ability to withstand high temperatures, making them suitable for use in environments where heat dissipation is critical, such as in high-power electronic devices or in automotive and aerospace industries. These substrates offer good dimensional stability, low moisture absorption, and excellent electrical insulation properties.
One of the key advantages of BT resin substrates is their reliability in harsh operating conditions, as they can maintain their structural integrity and electrical performance even when exposed to extreme temperatures and environmental stresses.
In PCB manufacturing, BT resin substrates are often used as the core material for multilayer boards, providing a stable and reliable foundation for mounting electronic components and creating complex circuit designs.
Overall, BT resin substrates play a vital role in enabling the development of high-performance electronic devices that demand durability, thermal stability, and excellent electrical properties.
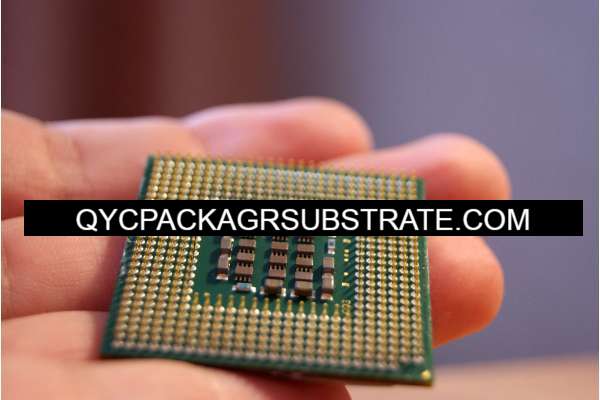
BT resin substrate manufacturing
What are the BT Resin Substrate Design Guidelines?
Design guidelines for BT resin substrates typically focus on optimizing the performance, reliability, and manufacturability of printed circuit boards (PCBs) using these materials. Here are some common BT resin substrate design guidelines:
- Thermal Management:BT resin substrates are known for their excellent thermal conductivity. Designers should ensure proper heat dissipation by incorporating thermal vias, heat sinks, and thermal pads into the PCB layout to prevent overheating of components.
- Signal Integrity:Maintain signal integrity by carefully routing high-speed traces, minimizing signal reflections, and controlling impedance throughout the PCB design. Consider factors such as trace length, spacing, and termination to reduce signal degradation.
- Layer Stackup:Design the layer stackup considering factors such as signal integrity, impedance matching, and thermal management. Optimize the layer configuration to meet the specific requirements of the application while balancing cost and manufacturability.
- Component Placement:Place components strategically to minimize signal interference, reduce parasitic capacitance, and facilitate efficient routing. Group components based on their function and connectivity to optimize signal paths and minimize signal distortion.
- Power Distribution: Design an efficient power distribution network to ensure stable voltage regulation and minimize voltage drops across the PCB. Use power planes and carefully route power traces to minimize impedance and noise.
- Manufacturing Considerations:Consider manufacturing constraints such as minimum trace width and spacing, minimum drill size, and aspect ratio limitations when designing the PCB layout. Ensure compliance with fabrication and assembly processes to facilitate smooth production.
- Reliability: Design for reliability by avoiding sharp corners, minimizing stress concentrations, and adhering to industry standards for mechanical and thermal stress relief. Perform thorough simulations and testing to validate the design’s reliability under various operating conditions.
- Environmental Considerations: Take into account environmental factors such as temperature, humidity, and vibration when designing BT resin substrate-based PCBs for applications in harsh environments. Select materials and coatings that provide protection against environmental stressors.
By following these design guidelines, engineers can optimize the performance, reliability, and manufacturability of PCBs using BT resin substrates, ensuring their suitability for a wide range of applications across industries.
What is the BT Resin Substrate Fabrication Process?
The fabrication process for BT resin substrates involves several steps to create the printed circuit boards (PCBs) using bismaleimide triazine (BT) resin as the substrate material. Here’s an overview of the typical fabrication process:
- Substrate Preparation: The process begins with preparing the BT resin substrate material. This involves cutting the substrate material into the desired size and shape according to the PCB design specifications.
- Surface Preparation: The surface of the BT resin substrate is cleaned and treated to ensure proper adhesion of the copper layers and other materials that will be applied during the fabrication process.
- Copper Cladding:A thin layer of copper foil is bonded or laminated onto one or both sides of the BT resin substrate. This copper layer will serve as the conductive material for the circuit traces and component pads.
- Photoresist Application: A layer of photoresist material is applied to the surface of the copper-clad BT resin substrate. The photoresist acts as a protective mask for the areas of copper that will remain after etching.
- Exposure and Development: The PCB design pattern is transferred onto the photoresist layer using photolithography techniques. The substrate is exposed to UV light through a photomask, which selectively hardens the photoresist in areas where copper is to be preserved. The unexposed photoresist is then washed away, revealing the underlying copper traces pattern.
- Etching: The exposed copper areas not protected by the photoresist are chemically etched away, leaving behind the desired copper traces and pads on the BT resin substrate.
- Strip and Clean:The remaining photoresist is stripped off from the substrate, leaving clean copper traces and pads on the BT resin surface. The substrate is then cleaned to remove any residual chemicals or contaminants.
- Surface Finish: Surface finish processes such as solder mask application, copper plating, and surface coating may be applied to protect the copper traces and provide solderability for component attachment.
- Drilling:Holes for through-hole components and vias are drilled into the substrate using precision drilling equipment. These holes provide electrical connections between different layers of the PCB.
- Plating and Plating Resist Removal: The drilled holes are plated with copper to provide electrical conductivity and strengthen the connections. Any plating resist used during this process is then removed.
- Final Inspection and Testing: The finished BT resin substrate undergoes rigorous inspection and testing to ensure that it meets the required specifications for electrical performance, dimensional accuracy, and reliability.
- Component Assembly: Once the BT resin substrate is fabricated, electronic components are assembled onto the PCB using soldering techniques, completing the manufacturing process.
Overall, the fabrication process for BT resin substrates involves a series of precise steps to create high-quality PCBs suitable for a wide range of electronic applications.
How do you manufacture a BT Resin Substrate?
Manufacturing a BT resin substrate involves several steps to create a stable and reliable foundation for printed circuit boards (PCBs). Here’s a detailed overview of the manufacturing process:
- Material Preparation: The manufacturing process starts with preparing the BT resin material. BT resin, known for its high thermal stability and mechanical strength, is typically supplied in the form of sheets or panels.
- Panel Cutting: The BT resin panels are cut into the desired size and shape using precision cutting equipment. This step ensures that the substrates match the specifications required for the intended PCB design.
- Surface Treatment: The surfaces of the BT resin substrates are cleaned and treated to remove any contaminants and to improve adhesion for subsequent processing steps. Surface treatment may involve processes such as chemical cleaning and plasma treatment.
- Copper Cladding: Thin copper foils are laminated onto one or both sides of the BT resin substrate. This copper cladding provides the conductive pathways for the circuit traces and component connections on the PCB.
- Lamination: The BT resin substrate and copper foils are pressed together under heat and pressure in a lamination press. This process ensures proper bonding between the substrate and copper layers, creating a strong and durable laminate.
- Drilling: Precision holes are drilled into the BT resin substrate using computer-controlled drilling machines. These holes are used for through-hole component mounting and for creating vias to establish electrical connections between different layers of the PCB.
- Electroplating: The drilled holes are plated with copper to reinforce the electrical connections and ensure conductivity between the PCB layers. Electroplating is typically performed using an electrolytic deposition process.
- Etching: A layer of photoresist is applied to the copper-clad surface of the BT resin substrate. The PCB design pattern is then transferred onto the photoresist layer using photolithography techniques. The exposed copper areas are etched away using chemical etchants, leaving behind the desired copper traces and pads.
- Solder Mask Application: A solder mask layer is applied over the copper traces and pads to insulate them and protect them from environmental factors. The solder mask also defines the areas where solder will be applied during component assembly.
- Surface Finish: Surface finish processes such as immersion tin, gold plating, or electroless nickel immersion gold (ENIG) may be applied to the exposed copper surfaces to improve solderability and corrosion resistance.
- Final Inspection and Testing: The finished BT resin substrates undergo thorough inspection and testing to ensure they meet the required specifications for dimensional accuracy, electrical performance, and reliability. This may include visual inspection, electrical testing, and thermal cycling tests.
- Component Assembly: Once the BT resin substrates pass inspection, electronic components are assembled onto the PCB using automated pick-and-place machines and soldering techniques. This completes the manufacturing process, producing fully functional printed circuit boards ready for use in electronic devices.
By following these steps, manufacturers can produce high-quality BT resin substrates that meet the stringent requirements of various electronic applications.
How much should a BT Resin Substrate cost?
The cost of a BT resin substrate can vary depending on several factors, including the size, thickness, complexity of the design, quantity ordered, and the supplier. Additionally, market conditions, material availability, and production processes can also influence the overall cost. However, to provide a general idea:
- Material Cost: BT resin is typically more expensive than standard FR-4 epoxy resin used in traditional PCB substrates due to its superior thermal and mechanical properties. The cost of the BT resin itself contributes to the substrate’s overall price.
- Manufacturing Cost: The manufacturing processes involved in producing BT resin substrates, such as lamination, drilling, electroplating, and etching, require specialized equipment and expertise. Labor costs, overhead expenses, and facility maintenance also impact manufacturing costs.
- Additional Processes: Surface finishing, solder mask application, and other finishing processes add to the substrate’s cost. These processes may vary depending on the specific requirements of the PCB design and the desired quality standards.
- Volume Discounts: Larger orders typically qualify for volume discounts, where the cost per unit decreases as the quantity ordered increases. Bulk purchasing can help reduce the overall cost of BT resin substrates, especially for mass production runs.
- Supplier and Location: The choice of supplier and their location can affect the substrate’s cost due to differences in overhead expenses, labor rates, shipping fees, and import/export tariffs.
To get an accurate cost estimate for BT resin substrates, it’s essential to contact PCB manufacturers or suppliers directly and provide detailed specifications of your requirements. They can offer quotations based on your specific needs and volume expectations. Additionally, it’s advisable to compare prices from multiple suppliers to ensure competitiveness and quality assurance.
What is BT Resin Substrate Base Material?
The base material of a BT resin substrate refers to the underlying material upon which the BT (bismaleimide triazine) resin is applied or laminated to create the substrate for printed circuit boards (PCBs). In other words, it is the foundational material that provides structural support and serves as the core of the PCB.
The base material for BT resin substrates is typically composed of a reinforcement material, such as woven or non-woven glass fabric, combined with a resin matrix. The resin matrix is impregnated with BT resin, which provides exceptional thermal stability, mechanical strength, and electrical properties required for high-performance electronic applications.
Common types of base materials used for BT resin substrates include:
- Glass Reinforced Epoxy (FR-4): FR-4 is a widely used base material for PCBs, consisting of woven glass fabric impregnated with an epoxy resin matrix. BT resin can be laminated onto FR-4 substrates to enhance their thermal performance and reliability.
- Polyimide (PI): Polyimide substrates offer excellent thermal stability and flexibility, making them suitable for applications requiring high-temperature resistance. BT resin can be applied to polyimide base materials to improve their mechanical properties and facilitate high-density interconnects.
- Metal Core: Some BT resin substrates utilize a metal core, such as aluminum or copper, to provide enhanced thermal conductivity and heat dissipation capabilities. The metal core is typically sandwiched between layers of BT resin and reinforcement materials to create a composite structure.
- Ceramic: Ceramic base materials offer superior thermal conductivity and electrical insulation properties, making them suitable for high-power and high-frequency applications. BT resin can be applied to ceramic substrates to improve their mechanical strength and reliability.
The choice of base material for BT resin substrates depends on factors such as the desired thermal performance, electrical properties, mechanical strength, and cost considerations. Each type of base material offers unique advantages and is selected based on the specific requirements of the PCB design and application.
Which company makes BT Resin Substrate?
BT resin substrates are produced by several companies, including Panasonic, Shengyi Technology, Isola, Rogers Corporation, and others. These companies have extensive experience and technological expertise in the electronics manufacturing industry, enabling them to produce high-quality BT resin substrates to meet various application needs.
As for our company, we are also a professional electronic manufacturing enterprise with advanced production equipment and a skilled technical team, capable of producing high-quality BT resin substrates. Our manufacturing capabilities and strengths include:
- Advanced Production Equipment: We have advanced production equipment and technology, including automated production lines, precision drilling equipment, and efficient surface treatment and coating processes, ensuring the production of high-quality BT resin substrates that meet customer requirements.
- Rich Experience: We have many years of experience and professional knowledge in the electronic manufacturing field, with a deep understanding and accumulation of BT resin substrate production processes and quality control.
- Quality Control System: We strictly implement a quality management system, from raw material procurement to production process control and inspection, to ensure that each batch of products meets customer requirements and standards.
- Customized Service: We can customize BT resin substrates of various specifications, thicknesses, and special requirements according to customer needs, providing personalized solutions and support.
- Continuous Improvement: We continuously improve and optimize production processes and technologies to adapt to industry developments and changes in customer needs, providing customers with better products and services.
With our professional capabilities and strengths, our company can produce high-standard BT resin substrates, providing reliable support and solutions for customers’ electronic manufacturing projects. We are committed to establishing long-term cooperative relationships with customers, achieving win-win situations together.
What are the 7 qualities of good customer service?
Good customer service is characterized by several key qualities that help foster positive relationships with customers and enhance their overall experience. Here are seven qualities of good customer service:
- Responsive: Good customer service involves being responsive to customers’ needs and inquiries in a timely manner. Whether it’s answering questions, addressing concerns, or resolving issues, prompt responses demonstrate attentiveness and a commitment to customer satisfaction.
- Empathetic: Empathy is essential in understanding customers’ perspectives, feelings, and concerns. Good customer service representatives listen actively, demonstrate compassion, and strive to put themselves in the customer’s shoes to provide personalized support and solutions.
- Knowledgeable: Customers value interactions with representatives who are knowledgeable about the products or services being offered. Good customer service entails having a thorough understanding of the company’s offerings, policies, and procedures to provide accurate information and guidance to customers.
- Professionalism: Professionalism is key to delivering consistently high-quality customer service experiences. This includes maintaining a courteous demeanor, using proper language and tone, and adhering to established communication standards and etiquette.
- Problem-solving skills: Effective problem-solving skills are crucial for resolving customer issues and addressing challenges in a timely and satisfactory manner. Good customer service representatives are proactive in identifying solutions, offering alternatives, and taking ownership of problems until they are fully resolved.
- Flexibility: Good customer service involves being flexible and adaptable to accommodate customers’ varying needs and preferences. This may involve accommodating special requests, adjusting policies when appropriate, and finding creative solutions to meet customers’ requirements.
- Follow-up and follow-through: Following up with customers after interactions and ensuring that issues are fully resolved demonstrates commitment and accountability. Good customer service involves following through on promises, providing updates as needed, and seeking feedback to continuously improve the customer experience.
By embodying these qualities, organizations can cultivate strong customer relationships, build trust and loyalty, and differentiate themselves in the competitive marketplace.
FAQs
What is BT resin substrate?
BT resin substrate refers to a type of material used in electronics manufacturing, particularly in printed circuit boards (PCBs). It is made of bismaleimide triazine (BT) resin, known for its excellent thermal and mechanical properties.
What are the advantages of BT resin substrates?
BT resin substrates offer superior thermal stability, mechanical strength, and electrical properties compared to traditional substrates. They are ideal for high-performance electronic applications that require reliability and durability.
What are the applications of BT resin substrates?
BT resin substrates are used in various electronic devices and industries, including telecommunications, aerospace, automotive, medical devices, and consumer electronics. They are particularly suitable for applications where high temperatures and harsh environments are present.
How are BT resin substrates manufactured?
BT resin substrates are typically manufactured using a process that involves laminating BT resin onto a base material, such as fiberglass-reinforced epoxy (FR-4). The substrate is then processed through various steps, including drilling, copper cladding, etching, and surface finishing, to create the final PCB substrate.
What are the key considerations when designing with BT resin substrates?
When designing with BT resin substrates, factors such as thermal management, signal integrity, layer stackup, component placement, power distribution, and manufacturing constraints need to be taken into account to ensure optimal performance and reliability of the PCB.
Are BT resin substrates more expensive than traditional substrates?
BT resin substrates generally have a higher cost compared to traditional substrates like FR-4 due to the specialized materials and manufacturing processes involved. However, the superior performance and reliability offered by BT resin substrates often justify the investment for high-end electronic applications.
Where can I purchase BT resin substrates?
BT resin substrates can be purchased from various suppliers and manufacturers specializing in electronic materials and PCB fabrication. It’s essential to choose a reputable supplier that can provide high-quality substrates tailored to your specific requirements and application needs.