Ceramic Packages for MEMS Sensors manufacturing
Ceramic Packages for MEMS Sensors, Ceramic Packages substrates Manufacturing, Ceramic PCBs Vendor, Ceramic packages for MEMS sensors are essential components designed to safeguard the delicate inner workings of MEMS devices. Crafted from specialized ceramic materials like alumina or aluminum nitride, these packages provide a protective barrier against environmental hazards such as moisture, dust, and temperature fluctuations. Their high thermal conductivity ensures efficient heat dissipation, while robust mechanical strength shields the sensors from physical shocks and vibrations. With meticulous design considerations, including hermetic sealing and precise dimensions, ceramic packages maintain the integrity of MEMS sensors, ensuring reliable performance in diverse applications. From automotive systems to medical devices and beyond, ceramic packages play a pivotal role in safeguarding the functionality and longevity of MEMS sensors, making them indispensable in modern technology landscapes.
What is a Ceramic Package for MEMS Sensors?
A ceramic package for MEMS (Microelectromechanical Systems) sensors refers to the enclosure or housing made of ceramic material that is used to protect and support the MEMS sensor. MEMS sensors are microscopic devices that integrate mechanical and electrical components on a single chip. These sensors are used in various applications such as automotive, consumer electronics, medical devices, industrial monitoring, and more.
The ceramic package serves several purposes for MEMS sensors:
- Protection: It provides a protective barrier against external environmental factors such as moisture, dust, temperature variations, and mechanical shocks, which could potentially damage the delicate MEMS components.
- Hermetic Seal: Many ceramic packages are designed to provide a hermetic seal, which prevents moisture and other contaminants from entering the package and affecting the performance and reliability of the MEMS sensor.
- Thermal Management: Ceramic materials often have good thermal conductivity properties, which can help in dissipating heat generated by the MEMS sensor during operation. This aids in maintaining the sensor’s temperature within the optimal range for accurate measurements.
- Mechanical Stability: Ceramic packages offer mechanical stability and rigidity, which is crucial for maintaining the structural integrity of the MEMS sensor, especially in applications where the sensor may be subjected to mechanical stress or vibration.
- Electrical Insulation: Ceramic materials are typically electrically insulating, which helps in preventing electrical interference or short circuits that could occur if the MEMS sensor comes into contact with conductive materials.
Overall, ceramic packages play a vital role in ensuring the reliability, durability, and performance of MEMS sensors in a wide range of applications.
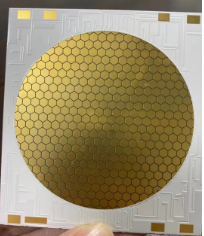
Ceramic PCB
What are the Ceramic Package Design Guidelines for MEMS Sensors?
Ceramic package design guidelines for MEMS sensors typically focus on ensuring reliability, performance, and manufacturability. Here are some key considerations:
- Material Selection: Choose ceramic materials with suitable properties such as thermal conductivity, mechanical strength, and hermeticity. Common materials include alumina (Al2O3) and aluminum nitride (AlN).
- Package Size and Shape: Design the package size and shape to accommodate the MEMS sensor while providing adequate space for wire bonding, sealing, and external connections. Consider the overall dimensions to fit the intended application requirements.
- Hermetic Sealing: Ensure the package design allows for hermetic sealing to protect the MEMS sensor from moisture and contaminants. This may involve using metal lids or ceramic-to-metal seals to achieve a reliable barrier.
- Thermal Management: Incorporate features for effective thermal management to dissipate heat generated by the MEMS sensor during operation. This could include thermal vias, heat sinks, or integrated thermal pads.
- Electrical Connectivity: Design the package to facilitate electrical connections to the MEMS sensor and external circuitry. This may involve providing bond pads, vias, or leads for wire bonding or soldering.
- Mechanical Stability: Ensure the package provides sufficient mechanical stability to protect the MEMS sensor from mechanical shocks and vibrations encountered during handling and operation.
- Package Assembly: Consider manufacturability during package assembly, including compatibility with assembly processes such as die attachment, wire bonding, sealing, and testing.
- Environmental Considerations: Assess the package design’s resistance to environmental factors such as temperature variations, humidity, and mechanical stress to ensure long-term reliability in different operating conditions.
- Cost Optimization: Balance performance requirements with cost considerations by optimizing the package design for efficient material usage and manufacturing processes without compromising functionality or reliability.
- Testing and Quality Assurance: Incorporate features that facilitate testing and quality assurance processes to ensure consistent performance and reliability of the MEMS sensor in mass production.
By adhering to these ceramic package design guidelines, manufacturers can develop robust and reliable packages for MEMS sensors suitable for various applications.
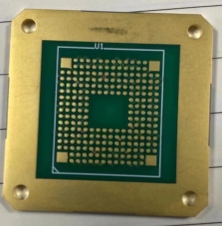
Ceramic Package Substrate
What is the Ceramic Package Fabrication Process for MEMS Sensors?
The fabrication process for ceramic packages used in MEMS sensors involves several steps to produce a housing that provides protection and support for the delicate MEMS components. Here’s an overview of the typical fabrication process:
- Material Preparation: The process begins with preparing the ceramic material for fabrication. Common ceramic materials used for MEMS sensor packages include alumina (Al2O3) and aluminum nitride (AlN). The ceramic material is typically supplied in the form of powder or pre-sintered sheets.
- Molding or Shaping: The ceramic material is molded or shaped into the desired form using techniques such as pressing, injection molding, or tape casting. This step helps in forming the basic structure of the ceramic package.
- Green Machining: In some cases, the green ceramic parts are machined or trimmed to achieve the desired dimensions and surface finish before sintering. Machining techniques such as milling, drilling, and grinding may be employed at this stage.
- Sintering: The green ceramic parts are subjected to high temperatures in a furnace in a process called sintering. Sintering involves heating the ceramic material to a temperature below its melting point, causing the particles to bond together and form a dense, solid structure. This step enhances the mechanical strength and density of the ceramic material.
- Surface Treatment: After sintering, the ceramic parts may undergo surface treatment processes such as polishing, lapping, or coating to improve surface smoothness, flatness, and hermeticity. Surface treatment helps in achieving the desired surface quality and functional properties of the ceramic package.
- Metallization: Metallization is performed to create electrical pathways on the ceramic surface for wire bonding or soldering connections. Metal layers are deposited onto the ceramic surface using techniques such as sputtering, evaporation, or screen printing. These metal layers serve as bond pads, vias, or leads for electrical connectivity.
- Assembly: After metallization, the ceramic packages are assembled with the MEMS sensor components. This may involve die attachment, wire bonding, or soldering to connect the MEMS sensor to the package. Additional components such as sealing lids or covers may also be integrated into the assembly to provide hermetic sealing.
- Quality Control and Testing: Throughout the fabrication process, quality control measures are implemented to ensure the dimensional accuracy, surface quality, and hermeticity of the ceramic packages. Testing procedures may include visual inspection, dimensional measurement, hermeticity testing, and electrical testing to verify the performance and reliability of the assembled MEMS sensor packages.
By following these fabrication steps, manufacturers can produce ceramic packages tailored to the specific requirements of MEMS sensors, ensuring robust protection and support for the sensitive MEMS components.
How do you manufacture a Ceramic Package for MEMS Sensors?
Manufacturing a ceramic package for MEMS (Microelectromechanical Systems) sensors involves several key steps. Here’s a general overview of the manufacturing process:
- Design: The manufacturing process begins with the design of the ceramic package. This involves determining the dimensions, shape, and features of the package to accommodate the MEMS sensor and meet the requirements of the application.
- Material Selection: Choose an appropriate ceramic material based on factors such as thermal conductivity, mechanical strength, hermeticity, and compatibility with MEMS fabrication processes. Common ceramic materials used for MEMS sensor packages include alumina (Al2O3) and aluminum nitride (AlN).
- Substrate Preparation: Prepare the ceramic material for processing. This may involve grinding, milling, or cutting the ceramic material into the desired shape and size.
- Forming: Form the ceramic material into the desired shape of the package using techniques such as pressing, injection molding, or tape casting. This step creates the green ceramic part, which is still porous and requires further processing.
- Green Machining: Optionally, perform machining operations on the green ceramic part to refine its dimensions and surface finish before sintering. Machining processes such as milling, drilling, and grinding may be used to achieve the desired shape and features.
- Sintering: Sinter the green ceramic part in a high-temperature furnace. During sintering, the ceramic material is heated to a temperature below its melting point, causing the particles to bond together and densify, forming a solid ceramic structure. This step enhances the mechanical strength and density of the ceramic package.
- Surface Treatment: After sintering, the ceramic package may undergo surface treatment processes to improve its surface finish, flatness, and hermeticity. Surface treatments such as polishing, lapping, or coating may be applied to achieve the desired surface properties.
- Metallization: Apply metal layers onto the ceramic surface to create electrical pathways for wire bonding or soldering connections. Metallization processes such as sputtering, evaporation, or screen printing are used to deposit metal layers onto the ceramic surface. These metal layers serve as bond pads, vias, or leads for electrical connectivity.
- Assembly: Assemble the ceramic package with the MEMS sensor components. This may involve die attachment, wire bonding, or soldering to connect the MEMS sensor to the package. Additional components such as sealing lids or covers may also be integrated into the assembly to provide hermetic sealing.
- Testing and Quality Control: Throughout the manufacturing process, conduct testing and quality control measures to ensure the dimensional accuracy, surface quality, hermeticity, and electrical performance of the ceramic packages. Testing procedures may include visual inspection, dimensional measurement, hermeticity testing, and electrical testing to verify the performance and reliability of the assembled MEMS sensor packages.
By following these manufacturing steps, ceramic packages tailored to the specific requirements of MEMS sensors can be produced, providing robust protection and support for the sensitive MEMS components.
How much should a Ceramic Package for MEMS Sensors cost?
The cost of a ceramic package for MEMS sensors can vary widely depending on several factors such as:
- Material: The type and quality of ceramic material used for the package can significantly impact its cost. High-purity ceramics or specialized materials may be more expensive than standard options.
- Size and Complexity: Larger or more complex packages typically require more material and labor, resulting in higher costs. Packages with intricate features, tight tolerances, or multiple layers may also incur additional manufacturing expenses.
- Volume: Economies of scale play a significant role in determining the cost of ceramic packages. Higher volume production runs generally result in lower per-unit costs due to efficiencies in material procurement, manufacturing processes, and overhead expenses.
- Manufacturing Process: The specific manufacturing techniques and processes employed, such as molding, sintering, machining, metallization, and assembly, can influence the overall cost. Some processes may require specialized equipment or skilled labor, adding to the cost.
- Additional Features: Additional features such as surface treatments, metallization, hermetic sealing, and testing can contribute to the cost of ceramic packages. Certain applications may require extra layers of protection or specific performance characteristics, which can increase costs.
- Supplier and Location: The choice of supplier and their location can impact the cost of ceramic packages. Different regions may have varying labor costs, overhead expenses, and material availability, affecting overall pricing.
- Quality and Certification: Packages manufactured to meet specific quality standards or certifications may entail higher costs due to additional testing, documentation, and compliance requirements.
Given these factors, it is challenging to provide a specific cost without detailed information about the package specifications, manufacturing requirements, and volume considerations. Generally, ceramic packages for MEMS sensors can range from a few dollars to tens or even hundreds of dollars per unit, depending on the factors mentioned above. Companies involved in the design and production of ceramic packages for MEMS sensors can provide accurate cost estimates based on individual project requirements.
What is Ceramic Package base material?
The base material for ceramic packages typically consists of specialized ceramic compounds that offer desirable properties for protecting and supporting the MEMS sensor components. Two common types of ceramic materials used as base materials for ceramic packages are:
- Alumina (Al2O3): Alumina ceramic, also known as aluminum oxide, is widely used in ceramic packages due to its excellent mechanical strength, thermal conductivity, and electrical insulation properties. It offers good resistance to temperature variations, chemical corrosion, and wear. Alumina ceramic packages are suitable for various applications where robustness and reliability are essential.
- Aluminum Nitride (AlN): Aluminum nitride is another ceramic material commonly used as a base material for ceramic packages, particularly in applications requiring high thermal conductivity. AlN exhibits exceptional thermal properties, including high thermal conductivity and thermal shock resistance, making it suitable for dissipating heat generated by the MEMS sensor during operation. It also provides good electrical insulation and dimensional stability.
These ceramic materials can be processed and shaped into the desired form for ceramic packages using techniques such as pressing, molding, or tape casting. They undergo sintering at high temperatures to form dense, solid structures suitable for housing MEMS sensors. Additionally, other ceramic compounds or composite materials may be utilized depending on specific application requirements, such as enhanced thermal performance, chemical resistance, or electrical properties.
Which company manufactures Ceramic Packages for MEMS Sensors?
Some companies specialize in manufacturing ceramic packages to provide protection and support for MEMS sensors. Some of these companies include Kyocera, Murata, NGK Insulators, TDK, and domestic enterprises such as Ruisheng Technology. These companies utilize advanced ceramic processing technologies and equipment to produce various specifications and types of ceramic packages to meet the needs of different application fields.
At our company, we also manufacture ceramic packages for MEMS sensors. As a professional ceramic manufacturer, we have advanced production equipment and a skilled technical team to provide high-quality ceramic packaging solutions. Our manufacturing process covers multiple steps from material preparation to shaping, sintering, surface treatment, metallization, assembly, and testing, ensuring that the products meet customer requirements and standards.
Our ceramic packaging products have the following features and advantages:
- High-quality materials: We use high-quality ceramic materials such as alumina (Al2O3) or aluminum nitride (AlN) to ensure that the products have good mechanical strength, thermal conductivity, and electrical insulation.
- Precision machining:We have advanced machining equipment and skilled technicians to achieve precision machining of ceramic packaging, ensuring accurate dimensions and smooth surfaces.
- Diversified design:We can customize ceramic packages in various shapes, sizes, and functions according to customer requirements, meeting the needs of different MEMS sensor applications.
- Reliable quality control:We implement a strict quality control system, monitoring and inspecting every aspect of production from raw material procurement to manufacturing to ensure stable and reliable product quality.
- Flexible production capacity: We have flexible production capabilities to quickly produce and deliver according to customer orders, meeting their needs and time requirements.
In conclusion, our company can provide high-quality, reliable ceramic packaging products to effectively protect and support MEMS sensor applications. We are committed to providing customized solutions to meet specific customer needs and requirements.
What are the 7 qualities of good customer service?
Good customer service is characterized by several key qualities that contribute to positive customer experiences and satisfaction. Here are seven qualities of good customer service:
- Responsiveness: Good customer service involves being prompt and attentive to customer inquiries, requests, and concerns. Customers appreciate timely responses and solutions to their issues, whether it’s through phone calls, emails, live chat, or in-person interactions.
- Empathy: Empathy is the ability to understand and share the feelings of others. Good customer service representatives empathize with customers by listening actively, acknowledging their emotions, and demonstrating genuine concern for their needs and challenges.
- Professionalism: Professionalism entails maintaining a courteous, respectful, and helpful demeanor in all interactions with customers. This includes using proper language, addressing customers by name (if appropriate), and maintaining a positive attitude even in challenging situations.
- Knowledgeability: Good customer service requires having comprehensive knowledge about the products or services offered by the company. Customer service representatives should be well-trained and informed to provide accurate information, answer questions, and offer relevant assistance to customers.
- Problem-solving skills: Effective problem-solving skills are essential for resolving customer issues and concerns efficiently. Customer service representatives should be proactive in identifying and addressing customer problems, finding appropriate solutions, and following through to ensure customer satisfaction.
- Flexibility: Good customer service involves being flexible and adaptable to meet the diverse needs and preferences of customers. This may include accommodating special requests, providing personalized solutions, or adjusting policies and procedures when necessary to resolve customer issues.
- Consistency: Consistency is key to delivering a consistently high level of customer service across all interactions and touchpoints. Customers expect a consistent experience regardless of the channel they use to contact the company, whether it’s in-store, online, or over the phone.
By embodying these qualities, businesses can cultivate strong customer relationships, foster loyalty, and differentiate themselves from competitors in the marketplace.
FAQs (Frequently Asked Questions)
What is a ceramic package for MEMS sensors?
A ceramic package is an enclosure or housing made of ceramic material that is used to protect and support MEMS (Microelectromechanical Systems) sensors. It provides a protective barrier against environmental factors and helps maintain the structural integrity of the MEMS sensor.
What are the advantages of using ceramic packages for MEMS sensors?
Ceramic packages offer several advantages, including excellent thermal conductivity, mechanical strength, hermeticity, and electrical insulation. They provide robust protection against moisture, dust, temperature variations, and mechanical shocks, making them ideal for harsh operating environments.
What types of ceramic materials are used for MEMS sensor packages?
Common ceramic materials used for MEMS sensor packages include alumina (Al2O3) and aluminum nitride (AlN). These materials offer a combination of desirable properties such as high thermal conductivity, mechanical stability, and electrical insulation.
How are ceramic packages manufactured for MEMS sensors?
The manufacturing process for ceramic packages typically involves steps such as material preparation, molding or shaping, sintering, surface treatment, metallization, assembly, and testing. Advanced ceramic processing techniques and equipment are used to produce high-quality packages tailored to the specific requirements of MEMS sensors.
What considerations should be taken into account when designing ceramic packages for MEMS sensors?
Design considerations for ceramic packages include material selection, package size and shape, hermetic sealing, thermal management, electrical connectivity, mechanical stability, environmental resistance, cost optimization, and quality control.
What applications are ceramic packages for MEMS sensors commonly used in?
Ceramic packages for MEMS sensors find applications in various industries such as automotive, consumer electronics, medical devices, industrial monitoring, aerospace, and telecommunications. They are used in pressure sensors, accelerometers, gyroscopes, microphones, and other MEMS-based devices.
How can I choose the right ceramic package for my MEMS sensor application?
Choosing the right ceramic package involves considering factors such as the operating environment, performance requirements, size constraints, cost considerations, and compatibility with MEMS fabrication processes. Consulting with experienced ceramic packaging suppliers can help identify the most suitable solution for your specific application needs.