Professional High Frequency Substrate Manufacturer, we mainly produce ultra-small bump pitch package substrate, ultra-small trace and spacing packaging substrate and microtrace HDI PCBs.
HFPS, or High Frequency Package Substrate, is a specialized material designed for electronic packaging, specifically tailored for high-frequency applications like RF and microwave circuits. These substrates undergo meticulous engineering to deliver exceptional electrical performance, particularly in the GHz range and above.
Distinctive Attributes of HFPS:
Low Dielectric Constant (Dk): Materials with a low dielectric constant in High-Frequency Printed Circuit Boards (HFPCBs) play a crucial role in minimizing signal loss and maintaining signal integrity, particularly at higher frequencies.
Low Loss Tangent (Df): HFPS, with its low loss tangent, reduces signal attenuation, enabling high-fidelity transmission of signals.
Dimensional Stability: HFPS maintains consistent dimensions across diverse temperature and environmental conditions, guaranteeing reliability and steady performance.
Efficient Thermal Conductivity: HFPS prioritizes efficient heat dissipation, averting thermal challenges that could compromise performance or reliability.
High Reliability:HFPS materials are designed to meet stringent reliability standards, guaranteeing consistent performance even under challenging operational conditions.
High-frequency printed circuit boards (HFPS) typically rely on a range of materials, including advanced ceramics like alumina (Al2O3) and aluminum nitride (AlN), along with composite options such as polytetrafluoroethylene (PTFE)-based materials like polyimide and laminates from DuPont’s Rogers™ line.
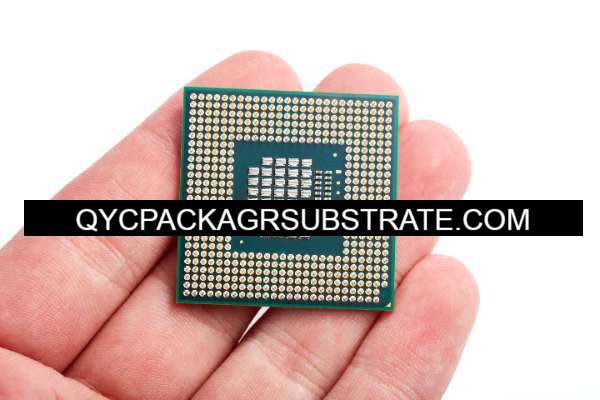
What are the Functions of High Frequency Package Substrates?
The High Frequency Package Substrate (HFPS) serves several crucial functions in electronic systems, particularly in high-frequency applications like RF and microwave circuits. Here’s an overview of its key roles:
Signal Integrity Preservation: HFPS materials are engineered to minimize signal loss and maintain signal integrity at high frequencies. By reducing distortion and attenuation, HFPS ensures that signals transmitted through the substrate remain clear and reliable.
Effective Thermal Management: HFPS substrates facilitate efficient heat dissipation, preventing thermal issues that could degrade electronic component performance. This function is vital for maintaining system reliability, especially in high-frequency environments where heat generation is common.
Mechanical Stability: HFPS provides a stable and durable platform for mounting electronic components. It ensures dimensional stability across varying temperatures and environmental conditions, offering reliable mechanical support for components.
Electrical Isolation: HFPS materials may offer electrical isolation between different components or circuit elements, minimizing interference and crosstalk in high-frequency circuits. This function helps maintain the integrity of signals and ensures optimal circuit performance.
Integration Support: HFPS substrates enable the seamless integration of various electronic components, such as RFICs, power amplifiers, antennas, and filters. This integration streamlines circuit design and manufacturing processes, enhancing overall system efficiency.
In summary, HFPS plays a crucial role in enhancing the efficiency, reliability, and performance of electronic systems operating at high frequencies. Its functions contribute to ensuring the seamless transmission of signals and the optimal operation of high-frequency circuits in modern communication and wireless technology applications.
What are the Different Types of High Frequency Package Substrate?
High-frequency package substrates (HFPS) comprise a range of specialized types, designed to fulfill the varied requirements of high-frequency electronic applications.
Ceramic substrates, such as alumina (Al2O3) and aluminum nitride (AlN), are highly valued for their outstanding thermal conductivity and mechanical stability. They are preferred in high-power RF applications due to their durability.
Polymer substrates filled with ceramics merge the benefits of both materials, providing high thermal conductivity and low dielectric loss alongside flexibility. They find application across a range of high-frequency electronic systems.
Substrates based on Polytetrafluoroethylene (PTFE), including polyimide and DuPont’s Rogers™ laminates, are renowned for their minimal dielectric loss, making them perfect for high-frequency RF and microwave applications, especially when flexibility is a key requirement.
Liquid Crystal Polymer (LCP) substrates stand out for their exceptional high-frequency performance and minimal dielectric loss. Their remarkable dimensional stability and ability to accommodate high-density interconnects render them optimal for cutting-edge RF and microwave applications.
Flexible Substrates: Polyimide films and similar flexible substrates provide excellent flexibility, catering to bendable circuit needs. They’re deployed in wearable electronics and conformal antennas operating at high frequencies.
Substrates reinforced with glass fibers harness the strength and thermal conductivity of glass, making them well-suited for high-power RF applications that demand durability.
Each HFPS type brings distinct advantages, empowering designers to select the most fitting substrate for their high-frequency electronic system requirements.
What is the Relationship between High Frequency Package Substrate and IC Packaging?
The connection between High Frequency Package Substrate (HFPS) and Integrated Circuit (IC) packaging is fundamental in electronic systems, particularly those operating at high frequencies. Here’s how they intertwine:
Foundational Support: HFPS serves as the base for mounting and connecting ICs and electronic components. It provides the structure for IC mounting, ensuring stable connections and mechanical reliability.
Signal Integrity Preservation: HFPS is crucial for maintaining signal fidelity within the IC package. By minimizing signal distortion and loss, HFPS ensures clear and reliable signal transmission, vital in high-frequency circuits where signal accuracy is paramount.
Thermal Regulation: Effective heat management is essential for IC performance, especially in high-frequency applications prone to heat generation. HFPS facilitates heat dissipation from ICs, regulating temperature and preventing thermal issues that could degrade performance.
Electrical Optimization: The selection of HFPS material and design directly influences IC packaging’s electrical performance. HFPS with low dielectric loss and high thermal conductivity enhances electrical characteristics, ensuring efficient signal transmission and minimal signal loss.
Package Miniaturization: HFPS technologies enable the development of compact IC packages, allowing for increased component density and improved performance in high-frequency applications. Advanced HFPS materials and manufacturing techniques support the creation of smaller, lighter packages without sacrificing functionality.
Integration Support: HFPS facilitates the integration of multiple ICs and components within a single package, promoting system efficiency and reducing interconnect complexity. This integration streamlines design and enhances overall performance in high-frequency electronic systems.
In summary, the relationship between HFPS and IC packaging is synergistic, with HFPS providing foundational support, signal integrity preservation, thermal management, electrical optimization, package miniaturization, and integration support critical for high-performance, high-frequency electronic applications.
How Does High Frequency Package Substrate Differ from PCBs?
High Frequency Package Substrates (HFPS) and Printed Circuit Boards (PCBs) are pivotal components within electronic systems, yet they diverge in their design, functionality, and application:
Material Composition: HFPS are crafted from specialized materials like ceramics (e.g., alumina, aluminum nitride) or polymer composites, meticulously engineered for high-frequency performance with low dielectric loss and superior thermal conductivity. In contrast, PCBs typically employ fiberglass-reinforced epoxy laminates (FR-4) or similar materials optimized for general electronic applications.
Frequency Handling: HFPS are finely tuned to operate efficiently at high frequencies, typically ranging from several gigahertz (GHz) to tens of gigahertz or beyond. While PCBs can handle some high-frequency signals, they lack the specific optimization for high-frequency performance and are predominantly used in lower frequency applications.
Signal Preservation: HFPS are intricately designed to minimize signal loss, distortion, and electromagnetic interference, ensuring impeccable signal fidelity, particularly crucial in high-frequency circuits. PCBs, due to their construction and material properties, may exhibit more pronounced signal degradation, especially at higher frequencies.
Thermal Management: HFPS often integrate advanced features for efficient heat dissipation, essential for maintaining component reliability in high-power and high-frequency environments. In contrast, PCBs may not offer the same level of thermal management capability and may necessitate additional cooling measures.
Manufacturing Approach: HFPS are typically manufactured using specialized processes like thin-film deposition, laser drilling, and precision machining, tailored specifically for high-frequency performance. PCBs, on the other hand, are produced through standard PCB fabrication techniques such as etching and soldering, suitable for a diverse array of electronic applications.
Application Scope: HFPS are purposefully designed for high-frequency applications such as RF/microwave circuits, antennas, and high-speed data communication systems. Conversely, PCBs find utility across various electronic devices and industries, encompassing consumer electronics, industrial machinery, and automotive systems.
In essence, while both HFPS and PCBs are indispensable in electronic systems, HFPS excel in high-frequency performance, offering unparalleled signal integrity, thermal management, and reliability compared to PCBs primarily optimized for lower frequency applications.
What are the Main Structures and Production Technologies of High Frequency Package Substrate?
High Frequency Package Substrates (HFPS) are adaptable in their composition and manufacturing approaches, each tailored to specific needs. Here’s a breakdown of typical structures and production methods:
Structures:
a. Multilayer Design: HFPS commonly adopt a multilayered structure, alternating between conductive and insulating layers. This configuration enables efficient signal routing and power distribution while safeguarding signal integrity.
b. Embedded Passive Components: Certain HFPS incorporate passive components like resistors, capacitors, or inductors directly into the substrate layers. This integration enhances circuit performance by mitigating parasitic effects.
c. Microstrip or Stripline Configuration: HFPS may utilize microstrip or stripline configurations for high-frequency signal routing, embedding signal traces within dielectric layers to minimize signal loss and interference.
d. Heat Dissipation Features: To manage thermal concerns in high-power applications, HFPS may integrate features such as thermal vias, metal-filled vias, or heat spreaders to efficiently dissipate heat from active components.
Production Techniques:
a. Thin-Film Deposition: Techniques like sputtering or chemical vapor deposition (CVD) are employed to deposit thin layers of conductive and dielectric materials onto substrate surfaces with precise thickness control.
b. Laser Drilling: Laser drilling is used to create fine vias and microvias in HFPS substrates, enabling precise interconnection between layers while minimizing signal degradation.
c. Precision Machining: Computer Numerical Control (CNC) machining precisely mills substrate materials, forming intricate patterns, vias, and features as per design specifications.
d. Lamination and Pressing: HFPS fabrication often involves lamination processes where layers of substrate materials and conductive patterns are pressed together under controlled conditions, yielding a solid substrate.
e. Surface Treatment: Techniques such as plasma treatment or chemical etching may be applied to enhance adhesion, solderability, and surface properties of HFPS substrates.
f. Quality Control and Testing: Stringent testing procedures, including electrical testing, impedance measurements, and thermal analysis, ensure the reliability and performance of HFPS substrates before integration into electronic systems.
In summary, the production of HFPS combines advanced manufacturing technologies and meticulous fabrication processes to meet the specific demands of high-frequency electronic applications.
Frequently Asked Questions (FAQs)
What defines a High Frequency Package Substrate (HFPS)?
HFPS is a specialized substrate crucial for high-frequency electronic packaging. It serves as a stable platform for mounting and connecting high-frequency electronic components.
What are the standout features of HFPS?
HFPS boasts low dielectric loss, high thermal conductivity, and exceptional high-frequency performance. Its multilayer structure enables precise signal routing and impedance matching.
What advantages does HFPS offer over standard PCBs?
HFPS excels in signal integrity, minimizing signal loss, and managing heat compared to traditional PCBs. It’s tailored for high-frequency applications, ensuring superior performance.
How does HFPS differ from conventional PCBs?
HFPS is purpose-built for high-frequency scenarios, prioritizing low dielectric loss and minimal signal degradation at high frequencies. This sets it apart from standard PCBs, which may not meet high-frequency demands.
Which materials are typically used in HFPS?
HFPS can be crafted from ceramics like alumina or aluminum nitride, along with specialized polymer composites. These materials offer excellent electrical properties and thermal conductivity crucial for high-frequency performance.
What production methods are involved in manufacturing HFPS?
The production of HFPS entails advanced techniques such as thin-film deposition, laser drilling, precision machining, and lamination. These processes ensure accurate fabrication and high-quality substrates suitable for high-frequency applications.
What design considerations should I bear in mind when using HFPS?
Key design aspects include impedance matching, signal routing, thermal management, and minimizing parasitic effects. Consulting experienced engineers and following high-frequency design best practices is advised.
Conclusion
In summary, High Frequency Package Substrates (HFPS) represent critical components in high-frequency electronic systems, renowned for their superior performance and reliability. Their attributes, including low dielectric loss, high thermal conductivity, and precise signal routing capabilities, make them indispensable for applications requiring stringent signal integrity and efficient thermal management.
Utilizing advanced manufacturing techniques such as thin-film deposition, laser drilling, and precision machining, HFPS are meticulously engineered to meet the exacting demands of high-frequency circuits, RF/microwave devices, and high-speed data communication systems.
Compared to conventional PCBs, HFPS stand out due to their specialized design and materials tailored explicitly for high-frequency applications. Design considerations, such as impedance matching, optimized signal routing, and effective thermal dissipation, are pivotal in maximizing HFPS performance within electronic systems.
Furthermore, ensuring reliability through comprehensive testing and stringent quality control procedures during production is essential for the successful integration of HFPS across various applications.
Ultimately, HFPS play an integral role in advancing high-frequency electronics, offering unparalleled performance, reliability, and signal integrity. By understanding their characteristics, manufacturing processes, and application requirements, engineers and designers can effectively leverage HFPS to drive innovation and progress within the field.