ISOLA 370HR PCB Manufacturer
ISOLA 370HR PCB Manufacturer. we can produce the best samllest bump pitch with 100um, the best smallest trace are 9um. and the smallest gap are 9um. most of the design are 15um to 30um trace and spacing.
ISOLA 370HR PCBs are renowned for their exceptional performance and reliability in demanding electronic applications. Constructed with ISOLA’s high-performance laminate material, these PCBs offer a unique combination of properties that make them ideal for critical industries such as telecommunications, aerospace, and medical devices.
With high thermal conductivity and low dielectric constant, ISOLA 370HR PCBs ensure efficient heat dissipation and minimal signal loss, making them suitable for high-speed and high-frequency circuitry. The material’s dimensional stability and mechanical strength guarantee long-term durability and robustness in harsh operating environments.
Designers appreciate the versatility of ISOLA 370HR PCBs, which allow for intricate circuit layouts, controlled impedance, and precise signal integrity. Whether it’s transmitting sensitive data or powering complex electronic systems, ISOLA 370HR PCBs deliver consistent performance, meeting the stringent requirements of modern electronic applications.
In summary, ISOLA 370HR PCBs represent the pinnacle of PCB technology, offering unmatched performance, reliability, and versatility for critical electronic systems.
What is ISOLA 370HR PCB?
ISOLA 370HR is a type of high-performance laminate material used in printed circuit boards (PCBs). PCBs are the foundation of electronic devices, providing a platform for electrical components to be connected and integrated.
ISOLA 370HR is known for its excellent electrical properties, such as high thermal conductivity and low dielectric constant, which make it suitable for high-frequency and high-speed applications. It’s also renowned for its mechanical strength and dimensional stability, crucial factors in ensuring the reliability and durability of electronic devices.
PCBs made with ISOLA 370HR are often used in industries where reliability and performance are critical, such as telecommunications, aerospace, and medical equipment manufacturing.
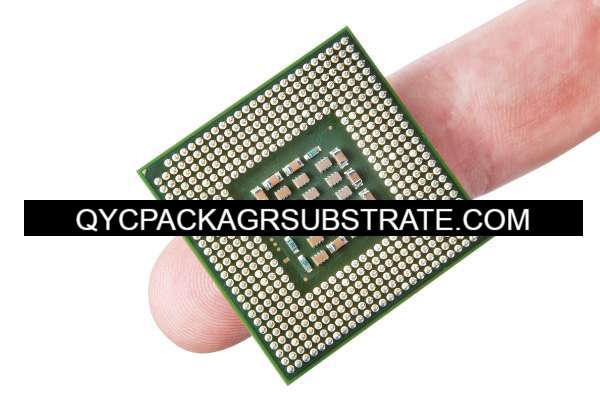
ISOLA 370HR PCB Manufacturer
What are the ISOLA 370HR PCB Design Guidelines?
Design guidelines for ISOLA 370HR PCBs typically cover several aspects to ensure optimal performance and reliability. While specific guidelines may vary depending on the application and manufacturer, here are some general recommendations:
- Material Selection: Choose ISOLA 370HR laminate material with appropriate thickness and copper weight based on the electrical and mechanical requirements of the PCB design.
- Layer Stackup: Design a suitable layer stackup considering signal integrity, impedance control, and thermal management requirements. Follow the manufacturer’s recommendations for layer arrangement and material thickness.
- Routing and Trace Width: Follow recommended trace width and spacing guidelines to maintain controlled impedance and signal integrity. Use wider traces for higher current-carrying signals and narrower traces for high-speed signals.
- Impedance Control: Ensure impedance matching for high-speed signal traces by controlling trace geometry, layer thickness, and dielectric constant. Use impedance calculators or simulation tools to verify impedance values.
- Ground and Power Planes: Implement solid ground and power planes to minimize electromagnetic interference (EMI) and provide stable power distribution. Ensure proper decoupling capacitor placement for noise suppression.
- Thermal Management: Incorporate thermal vias and heat sinks as needed to dissipate heat generated by active components and ensure reliable operation. Place components strategically to facilitate heat dissipation and avoid thermal hotspots.
- Component Placement: Optimize component placement to minimize signal path lengths, reduce crosstalk, and facilitate ease of assembly and testing. Follow best practices for signal integrity, such as separating high-speed and low-speed signals.
- Signal Integrity Analysis: Perform signal integrity analysis, including impedance matching, crosstalk analysis, and signal propagation delay, using simulation tools to verify the design’s performance before fabrication.
- 9. Manufacturability Considerations:Design the PCB layout with manufacturability in mind, considering factors such as panelization, solder mask alignment, and minimum feature sizes compatible with the fabrication process.
- Documentation and Review: Document the PCB design thoroughly, including layer stackup, routing guidelines, and design constraints. Conduct design reviews with stakeholders to ensure compliance with specifications and standards.
These guidelines are intended to assist designers in creating ISOLA 370HR PCBs that meet the performance, reliability, and manufacturability requirements of their specific applications. It’s essential to consult the manufacturer’s datasheets and application notes for detailed recommendations and guidelines specific to the chosen laminate material.
What is the ISOLA 370HR PCB Fabrication Process?
The fabrication process for ISOLA 370HR PCBs follows standard procedures for manufacturing printed circuit boards, with specific considerations for the properties of the laminate material. Here’s a general overview of the fabrication process:
- Preparation of Design Files: The process begins with the preparation of design files, including the PCB layout, layer stackup, and manufacturing specifications. Design files are typically created using PCB design software and include Gerber files, drill files, and assembly drawings.
- Material Preparation: ISOLA 370HR laminate material is selected based on the required thickness and copper weight for the PCB design. The laminate sheets are then cleaned and prepared for the subsequent processes.
- Layer Stackup: The individual layers of the PCB, including copper foils and prepreg layers, are laminated together to create the desired layer stackup. This process may involve the use of heat and pressure to bond the layers securely.
- Drilling: Precision holes are drilled into the PCB stackup at locations specified by the design files. These holes accommodate through-hole components, vias, and mounting hardware. High-speed, precision drilling equipment is used for this process.
- Copper Plating: After drilling, the exposed copper surfaces inside the holes and on the outer layers are chemically cleaned and then plated with additional copper to reinforce the conductive pathways and facilitate soldering.
- Circuit Patterning: A photoresist layer is applied to the outer copper layers, followed by exposure to UV light through a photomask containing the circuit pattern. The exposed areas of the photoresist are chemically removed, leaving behind the desired copper traces.
- Etching: The PCB is submerged in an etchant solution that removes the unprotected copper, leaving only the desired circuit traces on the surface. The remaining photoresist is then stripped away, revealing the copper traces.
- Surface Finishing: Surface finishing processes such as hot air solder leveling (HASL), electroless nickel immersion gold (ENIG), or immersion tin may be applied to the exposed copper surfaces to improve solderability, corrosion resistance, and electrical performance.
- Solder Mask Application: A solder mask layer is applied over the exposed copper traces to insulate them from environmental factors and prevent unintended solder connections during assembly. Openings are created in the solder mask for component pads and vias.
- Silkscreen Printing: Component designators, logos, and other identifying information are printed onto the PCB surface using a silkscreen printing process. This helps to facilitate assembly and troubleshooting.
- Final Inspection and Testing: The completed PCBs undergo visual inspection, electrical testing, and dimensional verification to ensure they meet the specified quality standards and performance requirements.
- Routing and Panelization: Once individual PCBs pass inspection, they may be routed from the manufacturing panel and separated into individual boards, or they may remain part of a larger panel for assembly efficiency.
The fabrication process for ISOLA 370HR PCBs may vary slightly depending on the specific requirements of the design and the capabilities of the manufacturing facility. It’s essential to work closely with the PCB manufacturer to ensure that the fabrication process aligns with the intended design specifications and quality standards.
How do you manufacture an ISOLA 370HR PCB?
Manufacturing an ISOLA 370HR PCB involves several steps that are similar to the general PCB fabrication process but with specific considerations for the properties of the ISOLA 370HR laminate material. Here’s a detailed overview of how you would manufacture an ISOLA 370HR PCB:
- Preparation of Design Files: Begin by preparing the design files for the PCB layout using a PCB design software. These files typically include the PCB layout, layer stackup, drill files, and any other manufacturing specifications.
- Material Selection: Choose ISOLA 370HR laminate material with the appropriate thickness and copper weight based on the design requirements. ISOLA 370HR is known for its high thermal performance and electrical properties suitable for high-speed applications.
- Layer Stackup Design: Design the layer stackup considering factors such as signal integrity, impedance control, and thermal management. Follow the manufacturer’s recommendations for layer arrangement and material thickness to ensure optimal performance.
- Preparation of Laminate Material: Clean and prepare the ISOLA 370HR laminate material for lamination. This may involve cutting the laminate sheets to size and cleaning the surfaces to remove any contaminants.
- Lamination: The individual layers of the PCB, including copper foils and prepreg layers, are laminated together under heat and pressure to create the desired layer stackup. This process ensures strong bonding between the layers.
- Drilling: Precision holes are drilled into the laminated stackup at locations specified by the design files. These holes accommodate through-hole components, vias, and mounting hardware. High-precision drilling equipment is used for this process.
- Copper Plating: After drilling, the exposed copper surfaces inside the holes and on the outer layers are chemically cleaned and then plated with additional copper to reinforce the conductive pathways and facilitate soldering.
- Circuit Patterning: Apply a photoresist layer to the outer copper layers, then expose it to UV light through a photomask containing the circuit pattern. The exposed areas of the photoresist are chemically removed, leaving behind the desired copper traces.
- Etching: Submerge the PCB in an etchant solution that removes the unprotected copper, leaving only the desired circuit traces on the surface. The remaining photoresist is then stripped away, revealing the copper traces.
- Surface Finishing: Apply surface finishes such as hot air solder leveling (HASL), electroless nickel immersion gold (ENIG), or immersion tin to the exposed copper surfaces to improve solderability, corrosion resistance, and electrical performance.
- Solder Mask Application: Apply a solder mask layer over the exposed copper traces to insulate them from environmental factors and prevent unintended solder connections during assembly. Openings are created in the solder mask for component pads and vias.
- Silkscreen Printing: Print component designators, logos, and other identifying information onto the PCB surface using a silkscreen printing process to facilitate assembly and troubleshooting.
- Final Inspection and Testing: Perform visual inspection, electrical testing, and dimensional verification to ensure that the completed PCBs meet the specified quality standards and performance requirements.
- Routing and Panelization: Once individual PCBs pass inspection, they may be routed from the manufacturing panel and separated into individual boards, or they may remain part of a larger panel for assembly efficiency.
Throughout the manufacturing process, it’s important to maintain strict quality control measures to ensure that the ISOLA 370HR PCBs meet the desired specifications and performance criteria. Collaboration with a reputable PCB manufacturer experienced in working with ISOLA materials can help ensure a successful manufacturing outcome.
How much should an ISOLA 370HR PCB cost?
The cost of an ISOLA 370HR PCB can vary widely depending on several factors, including:
- Board Size: Larger boards typically cost more due to the increased material and manufacturing time required.
- Layer Count: The number of layers in the PCB affects manufacturing complexity and cost. More layers generally result in higher costs.
- Material Thickness: Thicker laminate material may incur higher material costs.
- Copper Weight: Thicker copper layers or higher copper weights can increase material costs.
- Surface Finish: Different surface finishes, such as HASL, ENIG, or immersion tin, have varying costs.
- Trace Width and Spacing: Tighter tolerances for trace width and spacing may require more precise manufacturing processes, affecting costs.
- Hole Size and Density: Smaller holes or higher hole densities may increase drilling and plating costs.
- Complexity of Design: Complex PCB designs with fine pitch components, blind/buried vias, or controlled impedance requirements may require specialized manufacturing processes, which can increase costs.
- Quantity: Larger production quantities typically result in lower per-unit costs due to economies of scale.
- Turnaround Time: Expedited manufacturing services may incur additional fees.
To get an accurate cost estimate for an ISOLA 370HR PCB, it’s best to consult with PCB manufacturers or suppliers directly. They can provide quotes based on your specific design requirements and production volume. Additionally, online PCB cost calculators provided by some manufacturers can give you a rough estimate based on certain parameters like board size, layer count, and quantity.
What is ISOLA 370HR PCB base material?
ISOLA 370HR is a type of high-performance laminate material used as the base material for PCBs (Printed Circuit Boards). It is composed of a woven glass fabric substrate impregnated with epoxy resin, which provides mechanical strength, dimensional stability, and electrical insulation properties. The woven glass fabric serves as the reinforcement material, while the epoxy resin acts as the matrix that binds the fabric together and provides protection against environmental factors.
The key characteristics of ISOLA 370HR PCB base material include:
- High Thermal Performance: ISOLA 370HR exhibits excellent thermal conductivity properties, making it suitable for applications where heat dissipation is a concern.
- Low Dielectric Constant and Loss: The material has a low dielectric constant and low dissipation factor, which is beneficial for high-frequency and high-speed signal transmission with minimal signal loss.
- Dimensional Stability: ISOLA 370HR offers good dimensional stability, meaning it maintains its shape and size under various environmental conditions, ensuring reliable PCB performance over time.
- Mechanical Strength: The material provides sufficient mechanical strength to support components and withstand assembly and handling processes without deformation or damage.
- Chemical Resistance: ISOLA 370HR is resistant to common chemicals used in PCB manufacturing processes, protecting the integrity of the circuitry during fabrication.
Overall, ISOLA 370HR is a popular choice for PCB applications that demand high reliability, performance, and thermal management capabilities, such as telecommunications, aerospace, automotive, and industrial electronics.
Which company manufactures ISOLA 370HR PCBs?
ISOLA 370HR PCB base material is manufactured by ISOLA, a company based in the United States. ISOLA is a well-known supplier of printed circuit board materials, specializing in providing high-performance and reliable PCB material solutions. Their products are widely used in various industries, including telecommunications, aerospace, medical devices, and industrial controls.
As a professional PCB manufacturer, our company is also capable of producing ISOLA 370HR PCBs. We have advanced production equipment and a skilled technical team to meet customers’ demands for high-performance PCBs. Our manufacturing process strictly adheres to international standards and quality management systems, ensuring stable and reliable product quality.
Our advantages include:
- High-quality manufacturing processes:We employ advanced production techniques and stringent quality control measures to ensure that every PCB meets customers’ requirements and standards.
- Customized services: We can customize ISOLA 370HR PCBs with different specifications, layer counts, and characteristics to meet the needs of various application scenarios.
- Competitive pricing:We actively optimize production costs and offer competitive prices, providing customers with high cost-performance products and services.
- Timely delivery:We are able to deliver orders on time, ensuring that customers’ production plans proceed smoothly.
As your partner, we are committed to providing you with high-quality ISOLA 370HR PCBs and working together for mutual development. If you have any requirements or questions, please feel free to contact us, and we will be happy to serve you.
What are the 7 qualities of good customer service?
Good customer service is essential for building strong relationships with customers and ensuring their satisfaction. Seven qualities that characterize good customer service are:
- Responsiveness: Responding promptly to customer inquiries, concerns, and requests demonstrates that you value their time and are committed to addressing their needs efficiently.
- Empathy: Understanding and empathizing with customers’ perspectives and emotions fosters a sense of connection and trust. Showing empathy allows you to better understand their challenges and provide appropriate solutions.
- Clear Communication: Communicating clearly and effectively helps prevent misunderstandings and ensures that customers have a clear understanding of the information, products, or services being provided. Use language that is easy to understand and avoid jargon.
- Problem-solving Skills: Being able to identify and resolve customer issues and concerns effectively demonstrates competence and builds confidence in your ability to provide solutions. Take ownership of problems and work proactively to find resolutions.
- Professionalism: Maintaining a professional demeanor, even in challenging situations, instills confidence and trust in customers. This includes being courteous, respectful, and maintaining a positive attitude at all times.
- Consistency: Providing consistent experiences across all customer interactions, whether in-person, over the phone, or online, builds reliability and trust. Consistency in service delivery, policies, and communication helps establish a strong brand reputation.
- Going the Extra Mile: Going above and beyond customers’ expectations by offering personalized assistance, anticipating their needs, and providing additional support or resources demonstrates your commitment to customer satisfaction. This can include offering special discounts, follow-up calls, or providing educational materials.
By embodying these qualities, businesses can create positive experiences for their customers, build loyalty, and differentiate themselves from competitors.
FAQs
What is ISOLA 370HR PCB material?
ISOLA 370HR is a high-performance laminate material used as the base material for printed circuit boards (PCBs). It offers excellent thermal conductivity, low dielectric constant, and mechanical strength, making it suitable for high-speed and high-frequency applications.
What are the key features of ISOLA 370HR PCBs?
The key features of ISOLA 370HR PCBs include high thermal performance, low dielectric constant and loss, dimensional stability, mechanical strength, and chemical resistance.
What industries commonly use ISOLA 370HR PCBs?
ISOLA 370HR PCBs are used in various industries, including telecommunications, aerospace, automotive, medical devices, and industrial controls, where reliability, performance, and thermal management are critical.
What are the design guidelines for ISOLA 370HR PCBs?
Design guidelines for ISOLA 370HR PCBs include considerations such as material selection, layer stackup design, routing and trace width, impedance control, thermal management, component placement, manufacturability, and documentation.
How is ISOLA 370HR PCB material fabricated?
The fabrication process for ISOLA 370HR PCBs involves steps such as material preparation, layer stackup design, drilling, copper plating, circuit patterning, etching, surface finishing, solder mask application, silkscreen printing, final inspection, and routing/panelization.
What factors affect the cost of ISOLA 370HR PCBs?
The cost of ISOLA 370HR PCBs can vary depending on factors such as board size, layer count, material thickness, copper weight, surface finish, trace width and spacing, hole size and density, complexity of design, quantity, and turnaround time.
Where can I find a reliable manufacturer for ISOLA 370HR PCBs?
Reliable manufacturers of ISOLA 370HR PCBs can be found through online search engines, industry directories, trade shows, and referrals from colleagues or industry experts. It’s important to choose a manufacturer with experience, expertise, and a track record of delivering high-quality products.