Metal Core PCB Manufacturer
Metal Core PCB Manufacturer. Heavy copper PCB, Super thick copper core( Copper core thickness from 0.1mm to 7.2mm) PCBs, or Embedded Super thick copper core PCB production.
Metal Core PCBs, or Metal Core Printed Circuit Boards, are specialized circuit boards designed for applications requiring efficient heat dissipation. Unlike traditional PCBs, Metal Core PCBs feature a metal core, typically made of aluminum or copper, which provides superior thermal conductivity. This allows Metal Core PCBs to effectively dissipate heat generated by high-power components, making them ideal for use in applications such as high-power LED lighting, automotive electronics, power supplies, and amplifiers.
The construction of Metal Core PCBs typically includes a layer of dielectric material sandwiched between the metal core and the copper traces. This dielectric layer provides electrical insulation while facilitating heat transfer from the components to the metal core. Metal Core PCBs offer several advantages over standard PCBs, including improved thermal management, higher power handling capability, better mechanical stability, and enhanced reliability.
Overall, Metal Core PCBs are essential components in electronics manufacturing, enabling the development of high-performance systems that demand efficient heat dissipation and reliable operation.
What is a Metal Core PCB?
A Metal Core PCB (Printed Circuit Board) is a type of circuit board that uses a metal core as its base material instead of the typical fiberglass epoxy substrate found in conventional PCBs. The metal core provides several advantages, particularly in terms of thermal management.
The typical construction of a Metal Core PCB includes a layer of thermally conductive material, such as aluminum or copper, as the core layer. This metal core helps dissipate heat generated by components more efficiently than traditional PCBs, making Metal Core PCBs suitable for applications where thermal management is crucial, such as high-power LED lighting, automotive lighting, power supplies, and amplifiers.
The construction of a Metal Core PCB typically involves three layers:
- Metal Core: This layer is usually made of aluminum or copper, providing thermal conductivity to dissipate heat generated by components on the board.
- Dielectric Layer: Above the metal core, there’s a dielectric layer that electrically insulates the circuit from the metal core.
- Copper Traces and Pads: The conductive traces and component pads are typically etched onto the dielectric layer. Components are soldered onto these pads.
Metal Core PCBs offer benefits such as improved heat dissipation, higher power handling capability, and better mechanical stability compared to standard PCBs. However, they can be more expensive to manufacture due to the use of specialized materials and processes.
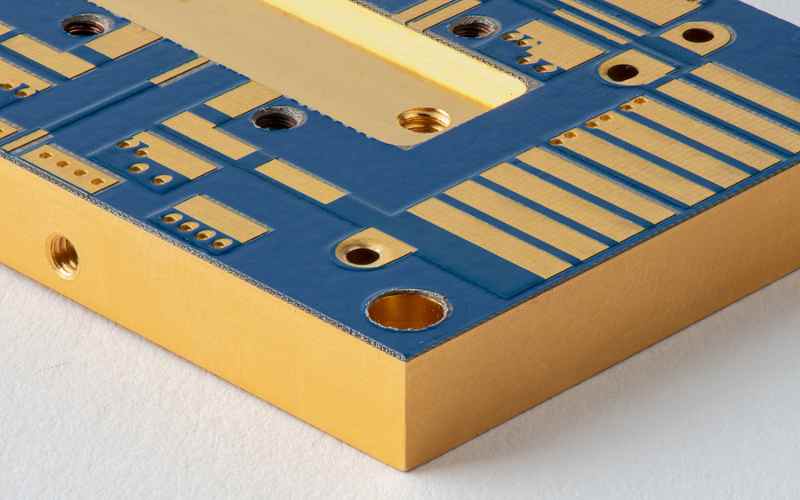
Metal Core PCB(7.2mm thickness copper PCBs)
What are the Metal Core PCB Design Guidelines?
Designing a Metal Core PCB requires careful consideration of several factors to ensure optimal performance, thermal management, and reliability. Here are some key guidelines to follow:
- Thermal Management: The primary advantage of Metal Core PCBs is their ability to dissipate heat efficiently. Ensure that components generating significant heat, such as power LEDs or high-power transistors, are placed close to the metal core for effective heat transfer. Also, use thermal vias to connect the component’s thermal pads to the metal core to further enhance heat dissipation.
- Material Selection: Choose the appropriate metal core material based on the specific requirements of your application. Aluminum is lightweight and cost-effective, while copper offers higher thermal conductivity but can be more expensive. Consider factors such as thermal conductivity, mechanical strength, and cost when selecting the metal core material.
- Dielectric Layer Thickness: The dielectric layer between the metal core and the copper traces should be thick enough to provide sufficient electrical insulation. However, a thicker dielectric layer can reduce thermal conductivity and increase thermal resistance. Strike a balance between electrical insulation and thermal performance based on your application’s requirements.
- Copper Trace Layout: Optimize the layout of copper traces to minimize thermal resistance and ensure efficient heat transfer. Distribute high-power components evenly across the board to prevent localized hotspots. Use wider traces for high-current paths to reduce resistance and minimize voltage drops.
- Component Placement:Place components strategically to minimize thermal gradients and ensure uniform temperature distribution across the board. Avoid clustering high-power components together, as this can lead to localized heating and thermal issues.
- Thermal Relief for Through-Hole Components: Use thermal relief pads for through-hole components to minimize the thermal resistance between the component leads and the copper traces. This helps prevent solder joint failures due to thermal expansion mismatch.
- Keep Signal Traces Away from High-Heat Areas: Whenever possible, route signal traces away from high-power components and areas with significant thermal gradients to prevent signal interference and ensure signal integrity.
- Consider PCB Assembly Process: Keep in mind the assembly process when designing Metal Core PCBs. Consider factors such as soldering temperature and the compatibility of materials with the assembly process to prevent thermal stress and ensure reliability.
By following these guidelines, you can design Metal Core PCBs that effectively manage heat, maintain electrical performance, and ensure long-term reliability in high-power applications.
What is the Metal Core PCB Fabrication Process?
The fabrication process for Metal Core PCBs is similar to that of standard PCBs, with some modifications to accommodate the metal core material and specialized requirements for thermal management. Here’s an overview of the typical Metal Core PCB fabrication process:
- Preparation of Metal Core Material:The process starts with the preparation of the metal core material, which is usually aluminum or copper. The metal core is typically in the form of sheets or panels with a specific thickness, depending on the application requirements.
- Preparation of Dielectric Layer: A layer of dielectric material is applied to the metal core to electrically insulate the circuit traces from the metal substrate. The dielectric material is typically a thermally conductive adhesive or an epoxy-based prepreg.
- Circuit Pattern Imaging: Similar to standard PCB fabrication, the circuit pattern is created using a photoresist layer. A photo mask containing the circuit pattern is aligned and exposed to UV light, transferring the pattern onto the photoresist layer on top of the dielectric material.
- Etching: After exposure, the unexposed areas of the photoresist are removed, leaving behind the desired circuit pattern. The exposed metal is then etched away using chemical etchants, leaving behind the circuit traces on the metal core.
- Drilling: Holes are drilled into the Metal Core PCB for through-hole components or vias. These holes allow for component placement and interconnection between different layers of the PCB.
- Copper Plating and Surface Finishing: Copper plating may be applied to the circuit traces to enhance conductivity and prevent oxidation. Surface finishes such as HASL (Hot Air Solder Leveling), ENIG (Electroless Nickel Immersion Gold), or OSP (Organic Solderability Preservatives) are applied to protect the copper traces and facilitate soldering during assembly.
- Component Assembly: Components are then assembled onto the Metal Core PCB using surface mount technology (SMT) or through-hole technology (THT), depending on the design requirements and component types.
- Thermal Management Enhancement: Depending on the application, additional thermal management features may be incorporated, such as thermal vias or thermal pads, to improve heat dissipation and thermal performance.
- Testing and Inspection: Once assembly is complete, the Metal Core PCB undergoes testing and inspection to ensure that all components are correctly soldered, and the circuit functions as intended. This may include electrical testing, functional testing, and visual inspection.
- Final Finishing and Packaging: After testing, the Metal Core PCB is subjected to final finishing processes such as depanelization, where individual boards are separated from larger panels, and then packaged for shipment to the end-user or assembly facility.
By following these fabrication steps, manufacturers can produce Metal Core PCBs that meet the specific requirements for thermal management and reliability in high-power applications.
How do you manufacture a Metal Core PCB?
Manufacturing a Metal Core PCB involves several steps, from designing the circuit layout to assembling components onto the board. Here’s an overview of the manufacturing process:
- Design: The process begins with designing the Metal Core PCB layout using PCB design software. During this phase, considerations for thermal management, component placement, and routing of traces are crucial. Designers need to optimize the layout to ensure efficient heat dissipation and electrical performance.
- Material Selection: Choose the appropriate metal core material based on the application requirements. Aluminum and copper are commonly used due to their excellent thermal conductivity. Select the dielectric material based on its thermal performance and electrical insulation properties.
- Preparation of Metal Core: The metal core material is prepared by cutting it into the desired size and shape. The surface may be cleaned and treated to ensure proper adhesion of the dielectric layer.
- Application of Dielectric Layer: Apply the dielectric material onto the metal core using methods such as lamination or adhesive bonding. The dielectric layer provides electrical insulation between the metal core and the copper traces while facilitating heat transfer.
- Circuit Pattern Imaging: Transfer the circuit pattern onto the Metal Core PCB using a photoresist layer. This involves exposing the photoresist to UV light through a photo mask containing the desired circuit pattern.
- Etching: Etch away the exposed metal using chemical etchants, leaving behind the circuit traces on the metal core. The remaining photoresist is then removed, leaving clean copper traces.
- Drilling:Drill holes into the Metal Core PCB for through-hole components or vias. These holes allow for component placement and interconnection between different layers of the PCB.
- Copper Plating and Surface Finishing: Apply copper plating to the circuit traces to enhance conductivity and prevent oxidation. Apply surface finishes such as HASL, ENIG, or OSP to protect the copper traces and facilitate soldering during assembly.
- Component Assembly: Components are assembled onto the Metal Core PCB using surface mount technology (SMT) or through-hole technology (THT). Automated pick-and-place machines accurately position components onto the board, and solder paste is applied to the pads before reflow soldering.
- Thermal Management Enhancement: Depending on the application, additional thermal management features such as thermal vias or thermal pads may be incorporated to improve heat dissipation.
- Testing and Inspection:Conduct testing and inspection to ensure that all components are correctly soldered, and the circuit functions as intended. This may include electrical testing, functional testing, and visual inspection.
- Final Finishing and Packaging: After testing, the Metal Core PCB undergoes final finishing processes such as depanelization, where individual boards are separated from larger panels, and then packaged for shipment to the end-user or assembly facility.
By following these manufacturing steps, manufacturers can produce Metal Core PCBs that meet the specific requirements for thermal management and reliability in high-power applications.
How much should a Metal Core PCB cost?
The cost of Metal Core PCBs can vary widely depending on several factors, including the size and complexity of the board, the choice of materials, the number of layers, surface finish options, and the quantity ordered. Here are some general factors that can influence the cost of Metal Core PCBs:
- Size and Complexity: Larger and more complex Metal Core PCBs with dense component placement and intricate routing will typically cost more to manufacture due to increased material and labor requirements.
- Material Choice: The cost of the metal core material (e.g., aluminum or copper) and the dielectric material used can significantly impact the overall cost of the PCB. Copper-based Metal Core PCBs tend to be more expensive due to the higher cost of copper compared to aluminum.
- Number of Layers: Metal Core PCBs can be single-sided, double-sided, or multilayered. The number of layers affects fabrication complexity and material costs. Multilayer Metal Core PCBs are generally more expensive than single or double-sided boards.
- Surface Finish: The choice of surface finish, such as HASL, ENIG, or OSP, can influence the cost of Metal Core PCBs. Some surface finishes may require additional processing steps, which can increase manufacturing costs.
- Quantity:Larger order quantities typically result in lower per-unit costs due to economies of scale. Manufacturers may offer volume discounts for bulk orders of Metal Core PCBs.
- Turnaround Time: Expedited or quick-turn fabrication services may come with additional costs compared to standard lead times.
- Additional Features: Specialized features such as impedance control, blind/buried vias, or gold plating can add to the overall cost of Metal Core PCBs.
As a rough estimate, Metal Core PCBs can range in cost from a few dollars for simple single-sided boards to several hundred dollars for complex multilayered boards with advanced features. It’s best to request quotes from multiple PCB manufacturers based on your specific design requirements to get an accurate cost estimate.
What is Metal Core PCB base material?
The base material of a Metal Core PCB is typically a thermally conductive metal substrate, which provides the foundation for the circuitry and components. The most commonly used metals for Metal Core PCB substrates are aluminum and copper. These metals offer excellent thermal conductivity properties, which is one of the primary reasons for using them in applications where efficient heat dissipation is essential.
- Aluminum: Aluminum is a popular choice for Metal Core PCBs due to its lightweight, cost-effectiveness, and good thermal conductivity. The aluminum substrate usually has a thickness ranging from 0.8mm to 3.2mm, although thicker substrates may be used for specialized applications. Aluminum-based Metal Core PCBs are commonly used in applications such as LED lighting, automotive electronics, and power supplies.
- Copper: Copper offers even higher thermal conductivity compared to aluminum, making it suitable for applications that require superior heat dissipation. Copper-based Metal Core PCBs are often used in high-power electronic devices, RF/microwave applications, and power amplifiers. Copper substrates typically have a thickness ranging from 0.5mm to 2.0mm.
In addition to aluminum and copper, other metals such as steel and alloy blends may also be used as base materials for Metal Core PCBs in certain specialized applications. However, aluminum and copper are the most widely used metals due to their favorable combination of thermal conductivity, cost-effectiveness, and availability.
Which company makes Metal Core PCBs?
There are many companies specialized in manufacturing Metal Core PCBs, some of the well-known manufacturers include Advanced Circuits, TTM Technologies, and Sanmina. These companies have advanced manufacturing equipment and rich experience, capable of meeting various application requirements and providing high-quality Metal Core PCB products.
As for our company, we are a dedicated electronics manufacturing company with advanced production lines and an experienced team. Our production capabilities cover a wide range of needs, from simple single-sided Metal Core PCBs to complex multilayered ones. We employ advanced processes and strict quality control standards to ensure that each production step meets the highest standards.
As a Metal Core PCB manufacturer, our strengths lie in:
- Professional Technical Team: We have a professional technical team with extensive experience in PCB design and manufacturing, capable of providing customized solutions to meet specific customer requirements.
- Advanced Manufacturing Equipment: We invest in advanced manufacturing equipment and technology, including high-precision CNC drilling machines, automated SMT production lines, and precision testing equipment, to ensure product quality and delivery times.
- Quality Assurance: We strictly adhere to international standards and industry specifications, implementing rigorous control and inspection at every stage, from raw material procurement to production, to ensure stable product quality and reliability.
- Customer Service: We value communication and cooperation with customers, providing timely and efficient technical support and after-sales service to ensure customer satisfaction and long-term cooperation.
In summary, our company has the technical strength, manufacturing capabilities, and quality assurance system required to produce Metal Core PCBs, meeting the needs of customers in lighting, power supply, automotive electronics, and other fields. We are willing to cooperate with customers to promote the development of the electronics manufacturing industry.
What are the qualities of good customer service?
Good customer service encompasses several qualities that contribute to a positive and satisfying experience for customers. Here are some key qualities:
- Responsiveness: Being responsive to customer inquiries, concerns, and requests in a timely manner shows that you value their time and are committed to addressing their needs promptly.
- Empathy: Showing empathy involves understanding and acknowledging the customer’s feelings and perspective. Empathetic responses demonstrate that you care about the customer’s experience and are willing to listen and empathize with their situation.
- Clear Communication: Effective communication is essential for providing good customer service. Communicate clearly and concisely, using language that is easy to understand, and actively listen to customers to ensure their needs are understood.
- Problem-Solving Skills: Good customer service representatives are adept at identifying and resolving customer issues and complaints efficiently and effectively. They can navigate challenges with patience and creativity to find satisfactory solutions for customers.
- Product Knowledge: Having a deep understanding of the products or services being offered allows customer service representatives to provide accurate information and guidance to customers. Product knowledge instills confidence in the customer and enhances trust in the company.
- Professionalism: Maintaining professionalism in interactions with customers involves being courteous, respectful, and maintaining a positive attitude, even in challenging situations. Professionalism builds trust and confidence in the company’s brand and reputation.
- Follow-Up: Following up with customers after resolving their issues or inquiries shows that you care about their experience and are committed to ensuring their satisfaction. Follow-up communication can include checking in to ensure the issue was resolved satisfactorily or seeking feedback on the customer’s experience.
- Adaptability: Good customer service requires the ability to adapt to different customer needs, preferences, and communication styles. Being flexible and adaptable allows customer service representatives to provide personalized assistance and support to each customer.
- Consistency: Consistency in the quality of customer service across all interactions and touchpoints helps build trust and loyalty with customers. Consistent service delivery ensures that customers know what to expect and can rely on a positive experience each time they engage with the company.
- Continuous Improvement: Good customer service is a continuous process of learning and improvement. Companies should actively seek feedback from customers, analyze customer service metrics, and implement changes and enhancements to continuously enhance the customer experience.
By embodying these qualities, companies can deliver exceptional customer service that fosters loyalty, satisfaction, and positive relationships with customers.
FAQs
What is a Metal Core PCB?
A Metal Core PCB, or Metal Core Printed Circuit Board, is a type of circuit board that uses a metal core as its base material instead of the typical fiberglass epoxy substrate found in conventional PCBs. The metal core provides several advantages, particularly in terms of thermal management.
What are the advantages of Metal Core PCBs?
Metal Core PCBs offer several advantages, including improved heat dissipation, higher power handling capability, better mechanical stability, and enhanced reliability compared to standard PCBs. They are commonly used in applications where thermal management is crucial, such as high-power LED lighting, automotive electronics, and power supplies.
Which metals are commonly used for the core of Metal Core PCBs?
The most commonly used metals for the core of Metal Core PCBs are aluminum and copper. These metals offer excellent thermal conductivity properties, which are essential for efficient heat dissipation in high-power applications.
How do Metal Core PCBs differ from standard PCBs?
The main difference between Metal Core PCBs and standard PCBs is the use of a metal core as the base material instead of fiberglass epoxy. This metal core provides enhanced thermal conductivity, allowing Metal Core PCBs to dissipate heat more efficiently than standard PCBs.
What factors should be considered when designing Metal Core PCBs?
When designing Metal Core PCBs, factors such as thermal management, material selection, copper trace layout, component placement, and surface finish options should be carefully considered to ensure optimal performance, reliability, and manufacturability.
Are Metal Core PCBs more expensive than standard PCBs?
Metal Core PCBs can be more expensive to manufacture than standard PCBs due to the use of specialized materials and processes. However, the cost can vary depending on factors such as size, complexity, material choice, and quantity ordered.
Can Metal Core PCBs be assembled using surface mount technology (SMT) or through-hole technology (THT)?
Yes, Metal Core PCBs can be assembled using both surface mount technology (SMT) and through-hole technology (THT), depending on the design requirements and component types. SMT is more commonly used for smaller, surface-mount components, while THT is used for larger through-hole components.