Microtrace RF PCB Manufacturer
Microtrace RF PCB and Package substrate Manufacturer. We use advanced Msap and Sap technology to produce the High multilayer interconnection substrates from 4 to 20layers.
Military Circuit Boards (MCBs) are specialized electronic components engineered to meet the rigorous demands of military applications. Designed to operate in harsh environments characterized by extreme temperatures, high levels of vibration, and exposure to moisture and contaminants, MCBs offer unparalleled reliability, durability, and performance. Constructed using high-quality materials and adhering to stringent military standards and specifications, these circuit boards undergo rigorous testing and qualification processes to ensure they can withstand the rigors of military use without failure. MCBs are integral components in a wide range of military equipment and systems, including communication systems, radar systems, weapon systems, avionics, and unmanned vehicles. With their ruggedized construction, advanced thermal management, and resistance to environmental factors, MCBs play a critical role in enhancing the effectiveness, safety, and mission readiness of military forces around the world.
What is a Military Circuit Board (MCB)?
A Military Circuit Board (MCB) is a type of circuit board designed and manufactured to meet the stringent requirements of military applications. These circuit boards are specifically engineered to withstand harsh environments, extreme temperatures, high levels of vibration, and other challenging conditions commonly encountered in military operations.
MCBs are built to adhere to strict military standards (such as MIL-STD-810 for environmental engineering considerations and MIL-PRF-55110 for printed wiring boards) to ensure reliability, durability, and performance in mission-critical systems. They are often used in military-grade electronic equipment, including communication systems, radar systems, weapon systems, and avionics.
The design and manufacturing processes for MCBs typically involve using high-quality materials, advanced fabrication techniques, and rigorous testing procedures to ensure they can withstand the rigors of military use without failure. Additionally, MCBs may incorporate features such as enhanced thermal management, conformal coatings for protection against moisture and contaminants, and ruggedized construction to enhance their resilience in demanding operational environments.
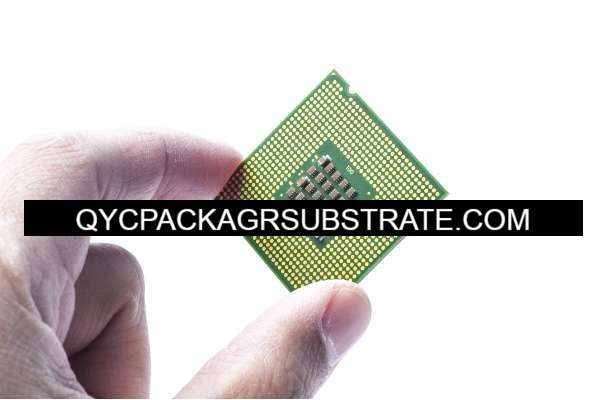
Microtrace RF PCB Manufacturer
What are the Military Circuit Board (MCB) Design Guidelines?
Military Circuit Board (MCB) design guidelines encompass a range of considerations to ensure the reliability, performance, and durability of circuit boards in military applications. Some key guidelines and best practices include:
- Compliance with Military Standards: MCBs should adhere to relevant military standards such as MIL-PRF-55110 for printed wiring boards and MIL-STD-810 for environmental engineering considerations.
- Component Selection: Use of high-quality components that meet military specifications and standards, including ruggedized or military-grade electronic components.
- Environmental Considerations: Design for operation in harsh environments, considering factors such as temperature extremes, humidity, vibration, shock, and exposure to contaminants like dust and moisture.
- Ruggedization: Incorporation of features to enhance durability, such as reinforcement of board materials, shock-absorbing mechanisms, and conformal coatings to protect against moisture, dust, and chemicals.
- Thermal Management: Implementation of effective thermal management techniques to ensure proper heat dissipation and prevent overheating, which can degrade performance and reliability.
- Signal Integrity: Careful routing of signal traces to minimize electromagnetic interference (EMI), crosstalk, and signal degradation, particularly important in high-frequency and sensitive military applications.
- Power Supply Design: Robust power supply design to provide stable and reliable power to all components, with considerations for backup power and protection against power fluctuations and surges.
- EMI/EMC Compliance: Design for electromagnetic compatibility (EMC) to minimize electromagnetic emissions and susceptibility, ensuring that the MCB does not interfere with other equipment and is not susceptible to external electromagnetic interference.
- Testing and Qualification: Rigorous testing and qualification procedures to verify performance, reliability, and compliance with military standards, including environmental testing, vibration testing, thermal cycling, and functional testing.
- Documentation and Traceability: Comprehensive documentation of the design, fabrication, testing, and qualification processes, including material specifications, fabrication drawings, test reports, and traceability of components used.
By following these guidelines, MCB designers and manufacturers can ensure that circuit boards meet the stringent requirements of military applications, providing reliable and durable performance in demanding operational environments.
What is the Military Circuit Board (MCB) Fabrication Process?
The fabrication process for Military Circuit Boards (MCBs) involves several steps to produce high-quality circuit boards that meet the stringent requirements of military applications. Here’s an overview of the typical fabrication process:
- Design Preparation: The process begins with the preparation of the circuit board design. This involves creating a detailed layout of the circuitry, including component placement, routing of traces, and consideration of factors such as signal integrity, thermal management, and mechanical constraints.
- Material Selection: High-quality materials are selected for the substrate (often epoxy-based fiberglass), copper foil for conductive layers, solder mask, and surface finish. These materials must meet military specifications and standards for performance and reliability.
- Photoresist Application: A layer of photoresist material is applied to the substrate. Photoresist is a light-sensitive material that will be used to define the pattern of conductive traces and pads on the circuit board.
- Exposure and Development: The circuit board design, typically in the form of a photomask, is used to selectively expose the photoresist to UV light. The exposed areas become soluble, allowing them to be removed in the development process, leaving behind the pattern of conductive traces and pads.
- Etching: The exposed copper areas on the circuit board are then etched away using an etchant solution, leaving behind the desired pattern of conductive traces and pads on the substrate.
- Drilling: Holes are drilled in the circuit board for through-hole components and vias, which are used to establish connections between different layers of the board.
- Plating: A thin layer of metal, typically copper, is plated onto the walls of the drilled holes to establish electrical connections between layers and provide mechanical support for components.
- Surface Finishing: The surface of the circuit board is coated with a finish to protect the copper traces from oxidation and facilitate soldering. Common surface finishes for MCBs include gold immersion, tin-lead solder, and electroless nickel immersion gold (ENIG).
- Solder Mask Application: A solder mask layer is applied over the circuitry, leaving openings for component pads and vias. The solder mask protects the circuitry from solder bridges and environmental contaminants.
- Silkscreen Printing: Component designators, polarity marks, and other identifying information are printed onto the circuit board using a silkscreen printing process.
- Testing and Inspection: The fabricated circuit boards undergo rigorous testing and inspection to ensure they meet quality standards and specifications. This may include electrical testing, dimensional inspection, and visual inspection of the circuitry.
- Final Assembly: Once the circuit boards pass inspection, they are ready for final assembly, where components such as integrated circuits, resistors, capacitors, and connectors are soldered onto the board to complete the electronic assembly.
By following these steps and adhering to military standards and specifications throughout the fabrication process, manufacturers can produce Military Circuit Boards that meet the stringent requirements of military applications in terms of reliability, durability, and performance.
How do you manufacture a Military Circuit Board (MCB)?
Manufacturing a Military Circuit Board (MCB) involves a series of steps to produce high-quality circuit boards that meet the rigorous standards and requirements of military applications. Here’s an overview of the manufacturing process:
- Design Preparation: The manufacturing process begins with the preparation of the circuit board design. This involves creating a detailed layout of the circuitry using specialized electronic design automation (EDA) software, considering factors such as component placement, routing of traces, signal integrity, thermal management, and mechanical constraints. The design must comply with military specifications and standards.
- Material Selection: High-quality materials are selected for the substrate, conductive layers, solder mask, and surface finish. These materials must meet military standards for performance, reliability, and durability. Common materials include epoxy-based fiberglass for the substrate, copper foil for conductive layers, and solder mask materials with thermal and chemical resistance.
- Panelization: Individual circuit board designs are arranged into panels for efficient manufacturing. Panelization involves combining multiple circuit designs onto a single larger panel, optimizing material usage and production throughput.
- Photo Tooling: The circuit board design is used to create photomasks or photo tools that will be used in the fabrication process. Photomasks define the pattern of conductive traces, pads, and other features on the circuit board.
- Lamination: The substrate material (typically epoxy-based fiberglass) and copper foil layers are laminated together under heat and pressure to form a composite laminate. This process creates a solid foundation for the circuitry and establishes the conductive layers.
- Inner Layer Processing: The inner layers of the laminated substrate are processed to define the conductive traces and pads. This involves applying a layer of photoresist, exposing it to UV light through the photomasks, developing the pattern, and etching away the exposed copper to create the desired circuitry.
- Drilling: Precision holes are drilled in the circuit board for through-hole components and vias, which are used to establish connections between different layers of the board. CNC (computer numerical control) drilling machines are used for accurate hole placement.
- Plating: A thin layer of metal, typically copper, is plated onto the walls of the drilled holes to establish electrical connections between layers and provide mechanical support for components. This process is called electroplating or through-hole plating.
- Outer Layer Processing: The outer layers of the circuit board undergo a similar process to the inner layers, including applying photoresist, exposing it to UV light, developing the pattern, and etching away the exposed copper to define the outer layer circuitry.
- Surface Finishing: The surface of the circuit board is coated with a finish to protect the copper traces from oxidation and facilitate soldering. Common surface finishes for MCBs include gold immersion, tin-lead solder, and electroless nickel immersion gold (ENIG).
- Solder Mask Application: A solder mask layer is applied over the circuitry, leaving openings for component pads and vias. The solder mask protects the circuitry from solder bridges and environmental contaminants.
- Silkscreen Printing: Component designators, polarity marks, and other identifying information are printed onto the circuit board using a silkscreen printing process. This information helps with component placement and assembly.
- Testing and Inspection: The fabricated circuit boards undergo rigorous testing and inspection to ensure they meet quality standards and specifications. This may include electrical testing, dimensional inspection, and visual inspection of the circuitry.
- Final Assembly: Once the circuit boards pass inspection, they are ready for final assembly. Components such as integrated circuits, resistors, capacitors, connectors, and other electronic components are soldered onto the board to complete the electronic assembly.
- Quality Assurance and Documentation: Throughout the manufacturing process, quality assurance measures are implemented to ensure consistency and reliability. Comprehensive documentation is generated, including material specifications, fabrication drawings, test reports, and traceability information.
By following these steps and adhering to military standards and specifications throughout the manufacturing process, manufacturers can produce Military Circuit Boards that meet the stringent requirements of military applications in terms of reliability, durability, and performance.
How much should a Military Circuit Board (MCB) cost?
The cost of a Military Circuit Board (MCB) can vary widely depending on factors such as complexity, size, materials, manufacturing processes, quantity ordered, and any additional requirements or certifications needed for military applications.
Here are some key factors that can influence the cost of an MCB:
- Complexity of Design: The complexity of the circuit board design, including the number of layers, density of components, and sophistication of features, can significantly impact the cost. More complex designs may require specialized fabrication techniques and higher manufacturing tolerances, leading to increased costs.
- Materials and Specifications: The selection of high-quality materials that meet military specifications and standards can affect the cost of the circuit board. Military-grade materials and processes often come at a premium compared to standard commercial-grade alternatives.
- Manufacturing Processes: The manufacturing processes involved in producing the MCB, such as lamination, drilling, plating, etching, surface finishing, and testing, contribute to the overall cost. More advanced or specialized manufacturing processes may incur higher costs.
- Volume of Production: The quantity of MCBs ordered can impact the unit cost. Typically, larger production volumes allow for economies of scale, leading to lower per-unit costs. However, smaller production runs or prototypes may incur higher costs due to setup fees and lower production efficiency.
- Certifications and Compliance: Obtaining certifications and ensuring compliance with military standards and specifications can add costs to the manufacturing process. Compliance with standards such as MIL-PRF-55110 for printed wiring boards and MIL-STD-810 for environmental engineering considerations may require additional testing and documentation.
- Testing and Quality Assurance: Rigorous testing and quality assurance measures are essential for ensuring the reliability and performance of MCBs in military applications. The cost of testing, inspection, and quality control activities is factored into the overall cost of manufacturing.
- Supplier and Location: The choice of supplier and their location can influence costs due to factors such as labor rates, overhead expenses, and shipping costs. Suppliers with specialized expertise in manufacturing MCBs for military applications may command higher prices.
Given these factors, it’s challenging to provide a specific cost without knowing the details of the MCB’s requirements and specifications. However, MCBs for military applications typically represent a significant investment due to the stringent requirements for reliability, durability, and performance. It’s essential to work closely with experienced manufacturers and suppliers who understand the unique challenges and standards associated with producing MCBs for military use.
What is Military Circuit Board (MCB) base material?
The base material used for Military Circuit Boards (MCBs) typically consists of layers of fiberglass reinforced epoxy resin, commonly referred to as FR-4 (Flame Retardant 4). FR-4 is a widely used substrate material in the electronics industry due to its excellent electrical insulation properties, mechanical strength, and thermal stability.
FR-4 material is composed of a woven glass fabric impregnated with epoxy resin, which is then cured to form a rigid and durable substrate. The glass reinforcement provides mechanical strength and dimensional stability, while the epoxy resin provides electrical insulation and adhesion properties.
In addition to FR-4, other advanced substrate materials may be used for MCBs in certain applications, depending on specific requirements such as high-frequency performance, thermal management, or environmental resistance. Some examples of alternative substrate materials include:
- Polyimide (PI): PI-based substrates offer high-temperature stability, excellent mechanical properties, and resistance to chemicals and radiation, making them suitable for extreme environmental conditions.
- Rogers Corporation Materials: Rogers Corporation produces specialized substrate materials tailored for high-frequency applications, such as RO4000 series laminates, which offer low dielectric loss and stable electrical performance at microwave frequencies.
- Metal Core PCBs (MCPCBs): MCPCBs feature a metal core, typically aluminum or copper, sandwiched between layers of dielectric material. These boards offer superior thermal conductivity and heat dissipation, making them suitable for power electronics and high-power applications.
- Ceramic-based Substrates: Ceramics such as aluminum oxide (Al2O3) or aluminum nitride (AlN) can be used as substrates for MCBs requiring exceptional thermal conductivity and high-temperature performance.
The choice of base material for an MCB depends on factors such as the application requirements, operating environment, frequency of operation, thermal management needs, and budget constraints. Manufacturers select the most suitable substrate material based on these considerations to ensure that the MCB meets the performance, reliability, and durability requirements of military applications.
Which company makes Military Circuit Boards (MCBs)?
Many companies specialize in manufacturing Military Circuit Boards (MCBs), including large electronic manufacturers globally and companies specifically dedicated to defense industries. Some well-known companies include Northrop Grumman, Lockheed Martin, Raytheon in the United States, and similar companies in other countries. These companies have extensive experience and technology to meet the strict requirements of military applications, producing high-quality and highly reliable military circuit boards.
Our company is also capable of producing Military Circuit Boards (MCBs). We have advanced manufacturing equipment, a professional engineering team, and extensive experience to meet various requirements for military applications. We are committed to ensuring that our products comply with military standards and specifications, providing reliable, durable, and stable performance circuit boards to meet customer needs.
Our production process strictly adheres to military standards and quality management systems, from design to manufacturing to testing, with each step carefully planned and executed. We use high-quality materials and advanced manufacturing techniques to ensure product quality and reliability. Our experienced team can flexibly meet various requirements and promptly resolve issues to ensure on-time delivery of products.
Our military circuit boards are widely used in communication systems, radar systems, weapon systems, aerospace, and other fields, gaining recognition and trust from customers. We not only offer standardized products but also customize designs according to specific customer requirements to meet the needs of different application scenarios.
In summary, our company, with its professional team, advanced manufacturing equipment, and strict quality control processes, can produce high-quality military circuit boards that comply with military standards and specifications, providing reliable solutions to customers.
What are the 7 qualities of good customer service?
Good customer service is essential for building strong relationships with customers and fostering loyalty. Here are seven qualities that contribute to excellent customer service:
- Responsive: A good customer service team is responsive and attentive to customer inquiries, concerns, and feedback. They acknowledge customer inquiries promptly and provide timely responses, whether through phone, email, chat, or in-person interactions.
- Empathetic: Empathy is crucial in customer service. Representatives should strive to understand the customer’s perspective, acknowledge their feelings, and demonstrate genuine concern for their needs and issues. Empathetic communication helps build trust and rapport with customers.
- Knowledgeable: Customers expect to receive accurate and helpful information from customer service representatives. A good customer service team is knowledgeable about products, services, policies, and procedures, enabling them to provide effective assistance and solutions to customer inquiries and issues.
- Patient: Dealing with customer inquiries and issues sometimes requires patience, especially when customers are frustrated or confused. Patient customer service representatives remain calm and composed, listen attentively to customer concerns, and work diligently to address their needs without rushing or becoming defensive.
- Resourceful:Good customer service involves problem-solving and finding solutions to customer issues efficiently. Resourceful representatives are proactive in seeking out information, leveraging available resources, and exploring alternative solutions to meet customer needs and resolve problems effectively.
- Professional: Professionalism is key in all customer interactions. Customer service representatives should maintain a courteous and respectful demeanor, use clear and polite language, and adhere to company policies and standards. Professionalism fosters a positive customer experience and reflects well on the company’s reputation.
- Follow-up: Following up with customers after resolving their inquiries or issues demonstrates care and commitment to customer satisfaction. Good customer service teams proactively follow up with customers to ensure that their needs were met, gather feedback on their experience, and address any additional concerns that may arise.
By embodying these qualities, organizations can deliver exceptional customer service experiences that leave a lasting positive impression on customers and contribute to long-term customer loyalty and satisfaction.
FAQs
What are Military Circuit Boards (MCBs)?
Military Circuit Boards (MCBs) are specialized circuit boards designed and manufactured to meet the stringent requirements of military applications. They are built to withstand harsh environments, extreme temperatures, high levels of vibration, and other challenging conditions encountered in military operations.
What makes MCBs different from standard circuit boards?
MCBs are built to higher standards of reliability, durability, and performance compared to standard circuit boards. They adhere to military specifications and standards, use high-quality materials, and undergo rigorous testing and qualification processes to ensure they can withstand the rigors of military use.
What are some common applications of MCBs?
MCBs are used in a wide range of military equipment and systems, including communication systems, radar systems, weapon systems, avionics, unmanned aerial vehicles (UAVs), ground vehicles, naval vessels, and more.
What are the key features of MCBs?
Key features of MCBs include ruggedized construction, enhanced thermal management, resistance to moisture, dust, and contaminants, high reliability, and compliance with military standards and specifications.
What are the main military standards and specifications for MCBs?
Common military standards and specifications for MCBs include MIL-PRF-55110 for printed wiring boards and MIL-STD-810 for environmental engineering considerations. These standards outline requirements for materials, fabrication processes, testing, and performance criteria.
How are MCBs manufactured?
The manufacturing process for MCBs involves several steps, including design preparation, material selection, panelization, photo tooling, lamination, inner and outer layer processing, drilling, plating, surface finishing, solder mask application, silkscreen printing, testing, and final assembly.
What are the benefits of using MCBs in military applications?
The benefits of using MCBs in military applications include increased reliability and durability, improved performance in harsh environments, longer service life, reduced risk of system failures, and enhanced mission effectiveness and safety.
Where can I find suppliers of MCBs?
Suppliers of MCBs can be found through online directories, trade shows, industry associations, and direct inquiries to manufacturers specializing in military electronics and circuit board fabrication.