Military PCB Manufacturer
Military PCB Manufacturer. Aviation PCB and IPC Class III PCB production. We offer High quality PCB with zero defects. We offer the Military PCB and Aviation PCB from 2 layer to 50 layers. Rigid pcb, Flex PCBs, Rigid-Flex PCBs.
Military PCBs, or printed circuit boards, are meticulously engineered components designed to withstand the rigorous demands of military applications. These specialized PCBs are crafted with precision and care to meet stringent reliability, durability, and performance standards required by military specifications (MIL-SPEC). Unlike their commercial counterparts, military PCBs are built to endure extreme environmental conditions, including temperature fluctuations, humidity, shock, and vibration encountered in battlefield settings.
Constructed using high-reliability materials and advanced manufacturing techniques, military PCBs undergo rigorous testing and quality assurance measures to ensure optimal performance in critical military systems. From communication systems and radar equipment to avionics and missile guidance systems, military PCBs play a vital role in the operation and functionality of various defense electronics.
With a commitment to excellence and unwavering attention to detail, military PCBs exemplify the pinnacle of engineering prowess, providing the backbone for mission-critical military technologies that safeguard national security and defense capabilities.
What is a Military PCB?
A Military PCB (Printed Circuit Board) refers to a circuit board specifically designed and manufactured for use in military applications. These applications often require high reliability, durability, and performance in harsh environments, including extreme temperatures, vibrations, and electromagnetic interference.
Military PCBs typically undergo stringent testing and adhere to strict standards to ensure they meet the requirements of military specifications (MIL-SPEC). These specifications outline various parameters such as materials, construction techniques, environmental tolerances, and performance characteristics that military-grade PCBs must meet.
Key features of military PCBs may include:
- High-reliability materials: Military PCBs often use high-quality materials that can withstand harsh environmental conditions and provide long-term reliability.
- Rigorous testing: These PCBs undergo extensive testing to ensure they meet stringent military standards for reliability and performance.
- Environmental resistance:Military PCBs are designed to withstand extreme temperatures, humidity, shock, and vibration encountered in military operations.
- EMI/EMC protection: Military PCBs are often designed with features to minimize electromagnetic interference (EMI) and ensure electromagnetic compatibility (EMC) to maintain proper functioning in the presence of other electronic equipment.
- Longevity: Military PCBs are expected to have long operational lifetimes, often far exceeding those of commercial-grade PCBs.
Overall, the design and manufacturing of military PCBs prioritize durability, reliability, and performance to meet the demanding requirements of military applications.
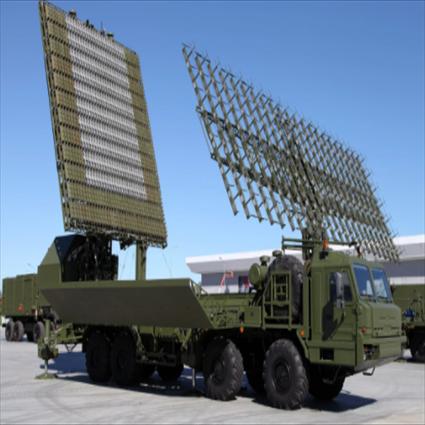
Military PCB
What are Military PCB Design Guidelines?
Military PCB design guidelines outline best practices and specifications for designing printed circuit boards (PCBs) intended for military applications. These guidelines ensure that the resulting PCBs meet the stringent requirements for reliability, durability, and performance in harsh environments typically encountered in military operations. Here are some common military PCB design guidelines:
- Compliance with MIL-STD-275: This standard specifies the requirements for printed wiring and printed wiring boards used in military electronic equipment. Adhering to this standard ensures that the PCB design meets military specifications.
- Component Selection: Choose components that meet military-grade specifications and are rated for operation in the intended environmental conditions, including temperature, humidity, shock, and vibration.
- High-reliability Materials: Select materials with proven reliability in harsh environments, such as high-temperature laminates, ruggedized substrates, and lead-free solder.
- EMI/EMC Considerations: Design the PCB layout to minimize electromagnetic interference (EMI) and ensure electromagnetic compatibility (EMC) with other electronic systems. This may involve proper grounding, shielding, and signal routing techniques.
- Environmental Resistance: Ensure that the PCB design can withstand extreme temperatures, humidity, shock, and vibration encountered in military applications. This may include conformal coating, ruggedized construction, and thermal management techniques.
- Signal Integrity: Pay attention to signal integrity issues such as impedance control, signal routing, and minimizing signal reflections to maintain reliable communication and performance.
- Reliability Testing: Perform rigorous testing and validation of the PCB design to ensure it meets military reliability standards. This may include environmental testing, reliability testing, and qualification testing according to military specifications.
- Long-term Availability:Consider the availability of components and materials for long-term support and maintenance of the military system throughout its operational lifespan.
- Documentation and Traceability: Maintain detailed documentation of the PCB design, including schematics, layout files, bill of materials (BOM), and manufacturing processes. Ensure traceability of components and materials for quality control and reliability assurance.
- Security Considerations: Implement security features and practices to protect the integrity and confidentiality of military electronic systems, including secure design methodologies and protection against tampering and cyber threats.
By following these military PCB design guidelines, designers can create PCBs that meet the demanding requirements of military applications in terms of reliability, durability, and performance.
What is the Military PCB Fabrication Process?
The military PCB fabrication process involves several steps to manufacture printed circuit boards (PCBs) that meet the stringent requirements for reliability, durability, and performance in military applications. Here’s an overview of the typical military PCB fabrication process:
- Design: The process begins with the design phase, where the PCB layout is created based on the specific requirements of the military application. Design considerations include component placement, signal routing, impedance control, and compliance with military standards and specifications (e.g., MIL-STD-275).
- Material Selection: High-reliability materials are selected for the PCB based on the environmental conditions and performance requirements of the military application. These materials may include ruggedized substrates, high-temperature laminates, and lead-free solder.
- Manufacturing Preparation:Once the design is finalized, manufacturing preparation begins. This involves preparing the manufacturing documentation, including Gerber files, drill files, and assembly drawings, as well as generating the bill of materials (BOM) for sourcing components.
- Material Preparation:The selected materials are prepared for the fabrication process. This may involve cutting the substrate panels to size, applying surface finishes (e.g., HASL, ENIG, or immersion silver), and preparing solder masks and silkscreens.
- Printed Circuit Board Production: The fabrication process starts with the production of the bare PCB. This typically involves several steps:
– Layer Stackup: If the PCB is multilayer, the individual layers are stacked together and laminated under heat and pressure.
– Drilling: Precision holes are drilled in the substrate panels to create vias and through-holes for component mounting and interconnection.
– Copper Plating: Copper is plated onto the substrate panels to create the circuit traces and plated through-holes.
– Etching: Excess copper is etched away using chemical processes, leaving behind the desired circuit traces.
– Surface Finishing: Surface finishes are applied to protect the copper traces and provide solderability.
- Component Assembly: Once the bare PCBs are fabricated, electronic components are assembled onto the boards using automated pick-and-place machines. This process may involve surface-mount technology (SMT) and through-hole components, depending on the design requirements.
- Soldering: The components are soldered onto the PCB using solder reflow ovens or wave soldering machines. This creates reliable electrical connections between the components and the circuit traces.
- Inspection and Testing: The assembled PCBs undergo rigorous inspection and testing to ensure they meet quality and reliability standards. This may include visual inspection, automated optical inspection (AOI), electrical testing, and functional testing.
- Quality Assurance: Quality assurance processes are implemented throughout the fabrication process to identify and address any issues that may affect the performance or reliability of the PCBs.
- Packaging and Shipping: Once the PCBs pass inspection and testing, they are packaged according to military specifications and prepared for shipping to the customer or assembly into military electronic systems.
Throughout the military PCB fabrication process, adherence to strict quality control standards and compliance with military specifications are critical to ensuring the reliability, durability, and performance of the finished PCBs in military applications.
How do you manufacture a Military PCB?
Manufacturing a military PCB involves several steps to ensure that the final product meets the stringent requirements for reliability, durability, and performance in military applications. Here’s a detailed overview of the process:
- Design Phase:
– Requirements Analysis: Understand the specific requirements of the military application, including environmental conditions, performance specifications, and compliance with military standards (e.g., MIL-STD-275).
– Schematic Design: Create a schematic diagram of the circuit layout, specifying the components and their interconnections.
– PCB Layout Design: Use PCB design software to lay out the components on the PCB, considering factors such as component placement, signal routing, impedance control, and EMI/EMC considerations.
– Design Review: Conduct a design review to ensure compliance with military specifications and address any potential issues.
- Material Selection:
– High-Reliability Materials: Choose materials that can withstand harsh environmental conditions and provide long-term reliability, such as high-temperature laminates, ruggedized substrates, and lead-free solder.
– Surface Finishes: Select appropriate surface finishes (e.g., HASL, ENIG, or immersion silver) to protect the copper traces and provide solderability.
- Manufacturing Preparation:
– Generate Manufacturing Files: Prepare the manufacturing documentation, including Gerber files, drill files, assembly drawings, and the bill of materials (BOM).
– Procurement: Source high-quality components and materials from trusted suppliers, ensuring compliance with military specifications.
– Tooling Preparation: Set up the manufacturing equipment, including CNC machines for drilling and routing, as well as pick-and-place machines for component assembly.
- Printed Circuit Board Production:
– Layer Stackup: If the PCB is multilayer, stack the individual layers together and laminate them under heat and pressure.
– Drilling and Plating: Drill precision holes in the substrate panels to create vias and through-holes for component mounting and interconnection. Plate copper onto the substrate panels to create the circuit traces and plated through-holes.
– Etching: Remove excess copper using chemical processes, leaving behind the desired circuit traces.
– Surface Finishing: Apply surface finishes to protect the copper traces and provide solderability.
- Component Assembly:
– Pick-and-Place: Use automated pick-and-place machines to accurately place surface-mount and through-hole components onto the PCB.
– Soldering: Solder the components onto the PCB using solder reflow ovens or wave soldering machines, ensuring reliable electrical connections.
- Inspection and Testing:
– Visual Inspection: Inspect the assembled PCBs visually for any defects or irregularities.
– Automated Optical Inspection (AOI): Use AOI systems to detect defects such as missing components, misalignment, or soldering issues.
– Electrical Testing: Test the electrical connectivity and functionality of the PCB using automated testers or functional testers.
– Environmental Testing: Subject the PCBs to environmental stress testing, including temperature cycling, humidity testing, shock, and vibration testing, to ensure they can withstand harsh conditions.
- Quality Assurance:
– Implement quality control processes throughout the manufacturing process to identify and address any issues that may affect the performance or reliability of the PCBs.
– Maintain detailed records of manufacturing processes, inspections, and test results for traceability and quality assurance purposes.
- Packaging and Shipping:
– Package the finished PCBs according to military specifications, ensuring proper protection during shipping and handling.
– Ship the PCBs to the customer or assembly facility, adhering to any specific packaging and shipping requirements.
Throughout the manufacturing process, adherence to strict quality control standards, compliance with military specifications, and continuous improvement efforts are essential to ensure the reliability, durability, and performance of the military PCBs in demanding military applications.
How much should a Military PCB cost?
The cost of a military PCB can vary significantly depending on various factors such as complexity, size, materials used, quantity ordered, and the specific requirements of the military application. Military-grade PCBs typically have higher reliability and performance standards compared to commercial-grade PCBs, which can affect the overall cost. Here are some factors that can influence the cost of a military PCB:
- Design Complexity: The complexity of the PCB design, including the number of layers, components, and routing requirements, can impact manufacturing costs. More complex designs may require additional fabrication steps and materials, leading to higher costs.
- Materials and Specifications: Military PCBs often require high-reliability materials and compliance with stringent military specifications (e.g., MIL-STD-275). The use of ruggedized substrates, high-temperature laminates, and specialty surface finishes can increase material costs.
- Manufacturing Process: The manufacturing process for military PCBs may involve additional steps such as environmental testing, reliability testing, and quality assurance measures, which can add to the overall cost.
- Volume: The quantity of PCBs ordered can affect the unit cost. Larger volume orders typically benefit from economies of scale, resulting in lower per-unit costs compared to smaller orders.
- Testing and Certification: Military PCBs may require testing and certification to ensure compliance with military standards and specifications. The cost of testing and certification services can contribute to the overall cost of the PCBs.
- Supplier and Location: The choice of PCB manufacturer or supplier can impact the cost, as prices may vary between different suppliers and regions. Additionally, factors such as lead times, quality standards, and support services may influence the overall value proposition.
- Customization and Add-Ons: Customization requirements or additional features such as conformal coating, special labeling, or serialization can increase the cost of the PCBs.
Given these variables, it’s challenging to provide a specific cost estimate for a military PCB without knowing the specific requirements of the project. However, military-grade PCBs typically command higher prices compared to commercial-grade PCBs due to the additional quality, reliability, and performance standards they must meet. It’s essential for organizations procuring military PCBs to carefully consider their requirements and work closely with PCB manufacturers or suppliers to obtain accurate cost estimates based on their specific needs.
What is Military PCB base material?
The base material for military PCBs, like any other PCB, serves as the substrate onto which the copper traces and electronic components are mounted. However, military-grade PCBs typically require materials that can withstand harsh environmental conditions and provide high reliability and durability. Here are some common base materials used in military PCBs:
- FR-4 (Flame Retardant 4): FR-4 is one of the most widely used base materials for PCBs in general, including military applications. It consists of a woven fiberglass cloth impregnated with an epoxy resin binder. FR-4 offers good mechanical strength, thermal stability, and electrical insulation properties, making it suitable for a wide range of military applications.
- High-Temperature Laminates: Military PCBs may require materials with enhanced thermal performance to withstand high operating temperatures encountered in military environments. High-temperature laminates, such as polyimide (e.g., Kapton) or PTFE (e.g., Teflon), are used to provide increased heat resistance and reliability.
- Ruggedized Substrates:Some military applications require PCBs to withstand extreme physical conditions, such as shock, vibration, and mechanical stress. Ruggedized substrates, including metal core PCBs (MCPCBs) or composite materials, are used to enhance the mechanical strength and durability of military PCBs.
- Ceramic Substrates: For high-frequency and RF/microwave applications common in military communications and radar systems, ceramic substrates are preferred due to their excellent electrical properties, low loss tangent, and high thermal conductivity. Alumina (Al2O3) and aluminum nitride (AlN) are commonly used ceramic materials for military PCBs.
- Metal Core PCBs (MCPCBs): MCPCBs feature a metal core (typically aluminum or copper) sandwiched between layers of insulating material. These PCBs offer excellent thermal conductivity, making them suitable for military applications requiring efficient heat dissipation, such as power electronics and LED lighting systems.
- Specialized Dielectric Materials: Some military PCBs may require specialized dielectric materials with specific electrical, thermal, or mechanical properties tailored to the application’s requirements. Examples include halogen-free materials, low-CTE (Coefficient of Thermal Expansion) materials, and materials with enhanced moisture resistance.
The choice of base material for a military PCB depends on factors such as the application requirements, environmental conditions, performance specifications, and compliance with military standards and specifications (e.g., MIL-STD-275). Military PCB manufacturers typically select materials that meet the stringent reliability, durability, and performance standards demanded by military applications.
Which company makes Military PCBs?
Many companies have rich experience and expertise in manufacturing military PCBs. Some of these companies include Advanced Circuits in North America, Yijie Circuit in China, Eltek in Israel, and Eurocircuits in Europe. These companies provide high reliability, durability, and high-performance PCB products for military applications by strictly adhering to military standards and specifications, as well as using high-quality materials and advanced manufacturing technologies.
At our company, we also have the capability to produce military PCBs. We have an experienced team familiar with the design, manufacturing, and testing processes of military PCBs. Our manufacturing facilities are equipped with advanced equipment and processes to meet the requirements of various military applications. We adhere to the principle of quality first, strictly implementing military standards and specifications to ensure that our PCB products meet the highest standards of reliability and durability.
Our advantages include:
- Professional Team: We have experienced engineers and technicians who can provide professional consulting and support to ensure smooth design and manufacturing processes.
- Advanced Equipment: Our manufacturing facilities are equipped with advanced equipment and processes to meet the manufacturing requirements of complex PCBs and ensure stable and reliable product quality.
- Strict Quality Control: We strictly implement a quality management system, including full-process control from raw material procurement to finished product inspection, to ensure that product quality meets military standard requirements.
- Customized Services: We can customize PCB products of various specifications and special requirements according to customer needs to meet the requirements of different application scenarios.
- Timely Delivery: We can provide timely delivery services according to customer requirements to ensure that projects are completed and delivered to customers on time.
In summary, our company has the capability to produce military PCBs and is committed to providing customers with high-quality, reliable, and high-performance products and services. We will continue to strive to improve our technical capabilities and service quality, working hand in hand with customers to create a better future.
What are the 7 qualities of good customer service?
Good customer service is essential for building strong relationships with customers and fostering loyalty. Here are seven qualities of good customer service:
- Responsiveness: Good customer service involves being prompt and responsive to customer inquiries, requests, and concerns. Responding quickly to customer needs demonstrates attentiveness and a commitment to addressing their issues in a timely manner.
- Empathy: Empathy is the ability to understand and relate to the feelings and experiences of customers. Good customer service representatives demonstrate empathy by listening actively, showing understanding, and acknowledging the customer’s perspective, even if they disagree.
- Clear Communication: Effective communication is crucial for providing good customer service. Customer service representatives should communicate clearly and concisely, using language that is easy for customers to understand. They should also be able to articulate solutions to problems and provide relevant information in a clear manner.
- Knowledgeability: Good customer service representatives have a strong understanding of the products or services they are supporting. They should be knowledgeable about product features, specifications, pricing, and policies, enabling them to answer customer questions accurately and provide helpful recommendations.
- Professionalism: Professionalism encompasses traits such as politeness, courtesy, and professionalism in demeanor and behavior. Good customer service representatives maintain a professional attitude at all times, remaining calm and composed, even in challenging situations.
- Problem-Solving Skills: Good customer service involves effectively addressing and resolving customer issues and concerns. Customer service representatives should possess strong problem-solving skills, being proactive in identifying solutions and taking appropriate action to resolve problems to the customer’s satisfaction.
- Follow-Up and Accountability: Good customer service doesn’t end with resolving an immediate issue. It involves following up with customers to ensure their needs have been met and their concerns have been addressed satisfactorily. Additionally, good customer service representatives take accountability for their actions and follow through on commitments made to customers.
By embodying these qualities, businesses can deliver exceptional customer service experiences that leave a positive impression on customers and contribute to long-term satisfaction and loyalty.
FAQs
What are Military PCBs?
Military PCBs are printed circuit boards specifically designed and manufactured for use in military applications. They are built to meet stringent requirements for reliability, durability, and performance in harsh environments encountered in military operations.
What are the Key Differences Between Military PCBs and Commercial PCBs?
Military PCBs are subject to higher reliability and performance standards compared to commercial PCBs. They often use high-reliability materials, undergo rigorous testing, and comply with military specifications (MIL-SPEC) to ensure they can withstand extreme temperatures, humidity, shock, and vibration.
What Standards Govern Military PCBs?
Military PCBs must comply with various military standards and specifications, including MIL-PRF-31032, MIL-PRF-55110, MIL-PRF-50884, and MIL-STD-275, among others. These standards outline requirements for materials, construction techniques, environmental tolerances, and performance characteristics.
What Environmental Conditions Can Military PCBs Withstand?
Military PCBs are designed to withstand a wide range of environmental conditions, including extreme temperatures (both high and low), humidity, shock, vibration, altitude, and exposure to harsh chemicals and solvents.
What Testing is Conducted on Military PCBs?
Military PCBs undergo various tests to ensure they meet reliability and performance standards. These tests may include environmental testing (temperature cycling, humidity testing, thermal shock), mechanical testing (vibration, shock), electrical testing (continuity, insulation resistance, impedance), and reliability testing (accelerated life testing, HALT/HASS).
What Applications Require Military PCBs?
Military PCBs are used in a wide range of military applications, including communication systems, radar systems, avionics, missile guidance systems, unmanned aerial vehicles (UAVs), defense electronics, and military vehicles (e.g., tanks, aircraft, ships).
How Can I Ensure the Quality of Military PCBs?
To ensure the quality of military PCBs, it’s essential to work with reputable PCB manufacturers who have experience and expertise in producing military-grade products. Look for manufacturers that comply with relevant military standards and specifications, provide thorough testing and quality control processes, and offer traceability and documentation for their products.