Military Substrate Manufacturer
Military Substrate Manufacturer and package substrate Manufacturer. We use advanced Msap and Sap technology to make the High multilayer interconnection substrates from 4 to 22 layers, or other IPC Class III HDI Military PCBs from 4 layer to 108 layers.
Military substrates form the bedrock of modern defense and security systems, serving as the foundation upon which critical military technologies are built. These substrates encompass a diverse array of components, materials, and systems engineered to withstand the rigors of military operations. From advanced electronic circuitry to robust structural materials, military substrates are designed to excel in demanding environments, providing essential functionality, durability, and reliability. They play a pivotal role in aerospace, land, and maritime applications, supporting everything from communication networks and surveillance systems to armored vehicles and weapon platforms. Manufactured with precision and adherence to strict standards, military substrates are at the forefront of technological innovation, continuously evolving to meet the dynamic challenges of modern warfare. As the cornerstone of defense infrastructure, military substrates ensure the readiness, effectiveness, and security of armed forces around the world.
What is a Military Substrate?
“Military substrate” is not a standard term in military terminology. However, it’s possible that the term could be used in a specific context or by certain organizations to refer to a foundational or underlying element within military operations or systems.
Without more context, it’s challenging to provide a precise definition. However, in general, a “substrate” often refers to a base or foundation upon which something is built or supported. In a military context, this could refer to various elements such as:
- Infrastructure: The physical and organizational structures that support military operations, including bases, facilities, and logistical networks.
- Technology: The underlying technological systems and platforms used in military operations, including communications networks, weapons systems, and surveillance equipment.
- Doctrine:The fundamental principles and strategies that guide military planning and operations, serving as the conceptual framework upon which military forces are organized and employed.
- Personnel:The human resources that form the backbone of military organizations, including soldiers, officers, and support staff.
Without additional context, it’s difficult to provide a more specific interpretation of “military substrate.” If you have a particular context or use case in mind, providing more details could help in giving a more tailored explanation.
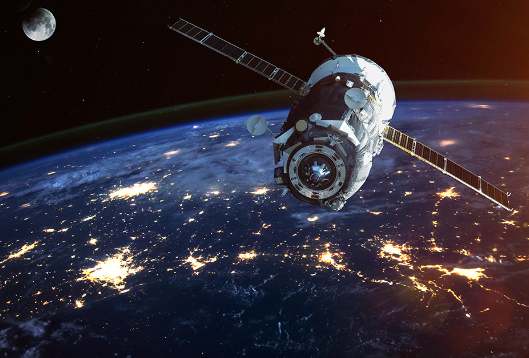
Military Substrate
What are Military Substrate Design Guidelines?
“Military substrate design guidelines” could refer to a set of principles or standards used in the development and construction of various components, systems, or infrastructure within the military domain. These guidelines may cover a wide range of areas, including technology, infrastructure, equipment, and operational procedures. Here are some possible examples of what these guidelines might entail:
- Security and Resilience: Designing military substrates with robust security measures to protect against physical and cyber threats. This could involve encryption protocols, secure access controls, and physical hardening of critical infrastructure.
- Interoperability: Ensuring that military substrates are compatible and interoperable with existing systems and platforms, as well as with those of allied forces. This could involve adherence to standardized communication protocols, data formats, and interface specifications.
- Scalability and Flexibility: Designing military substrates to be scalable and adaptable to changing operational requirements. This might involve modular designs that allow for easy expansion or modification as needed.
- Redundancy and Reliability: Building redundancy and failover mechanisms into military substrates to ensure continued functionality in the event of equipment failure or disruption. This could include backup power systems, redundant communication links, and redundant data storage.
- Environmental Considerations: Taking into account environmental factors such as terrain, climate, and electromagnetic interference when designing military substrates. This might involve selecting materials and technologies that can withstand harsh conditions and minimizing environmental impact.
- Mission Assurance: Ensuring that military substrates are designed to support mission-critical objectives with minimal risk of failure. This could involve rigorous testing and validation procedures to verify performance under various scenarios and conditions.
- Cost-Effectiveness:Designing military substrates to achieve a balance between performance and cost, maximizing operational effectiveness while minimizing acquisition and lifecycle costs.
These are just a few examples of the kinds of considerations that might be covered by military substrate design guidelines. Depending on the specific context and requirements of a given project or system, additional guidelines and criteria may apply.
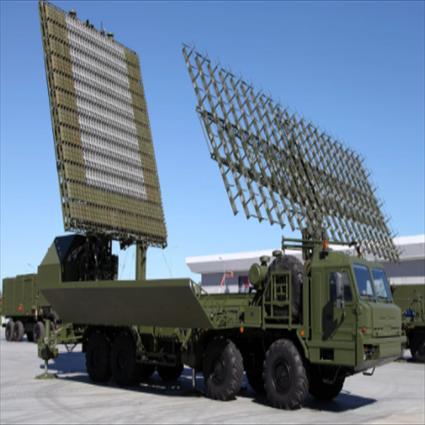
Military Substrate
What is the Military Substrate Fabrication Process?
The term “military substrate fabrication process” likely refers to the manufacturing process involved in producing various components, systems, or infrastructure used within the military domain. This process can vary widely depending on the specific item being fabricated, but here’s a general overview of the steps involved:
- Design and Planning: The process typically begins with the design phase, where engineers and designers create detailed plans and specifications for the military substrate. This may involve computer-aided design (CAD) software, simulations, and analysis to ensure that the final product meets the required performance and operational requirements.
- Material Selection: Once the design is finalized, the appropriate materials are selected based on factors such as strength, durability, weight, and cost. In the case of electronic components, specialized materials may be chosen for their electrical properties.
- Fabrication: The actual fabrication process begins, which can vary significantly depending on the type of substrate being produced. This could involve machining, casting, molding, forging, welding, or additive manufacturing techniques such as 3D printing. For electronic components, processes such as photolithography, deposition, etching, and assembly are commonly used.
- Quality Control: Throughout the fabrication process, quality control measures are implemented to ensure that the finished product meets the required standards and specifications. This may involve inspections, testing, and validation procedures to identify and correct any defects or deviations from the design.
- Assembly and Integration: Once the individual components or subsystems are fabricated, they are assembled and integrated into the final military substrate. This may involve additional testing and calibration to ensure that all components function together as intended.
- Testing and Evaluation: The completed military substrate undergoes rigorous testing and evaluation to verify its performance under various conditions and scenarios. This could include environmental testing, electromagnetic compatibility testing, stress testing, and functional testing to ensure that it meets or exceeds the required standards.
- Deployment and Maintenance: Once the military substrate has been successfully tested and evaluated, it is deployed for use in military operations. Ongoing maintenance and support may be required to ensure continued reliability and effectiveness throughout its lifecycle.
Overall, the military substrate fabrication process is a complex and highly specialized endeavor that requires expertise in engineering, materials science, manufacturing, and quality assurance. It plays a critical role in providing the military with the equipment, systems, and infrastructure needed to fulfill its missions effectively and efficiently.
How do you manufacture a Military Substrate?
Manufacturing a military substrate involves a series of steps tailored to produce components, systems, or infrastructure essential for military operations. Below is a generalized overview of the manufacturing process:
- Design and Specification: The process typically begins with defining the requirements and specifications of the military substrate. Engineers and designers work to develop detailed plans and designs, often utilizing computer-aided design (CAD) software. These designs must consider factors like functionality, durability, size, weight, and compatibility with existing systems.
- Material Selection: After the design phase, appropriate materials are selected based on the substrate’s requirements. Materials may include metals, polymers, composites, electronic components, and specialized materials for specific applications. The selection process considers factors like strength, conductivity, heat resistance, and environmental durability.
- Fabrication Techniques:
– Mechanical Components: Mechanical components may be fabricated using processes such as machining (milling, turning), casting, forging, stamping, or additive manufacturing (3D printing).
– Electronics: Electronic components are manufactured using techniques like semiconductor fabrication (cleanroom processes including photolithography, etching, deposition), assembly (soldering, wire bonding), and testing (electrical testing, functional testing).
– Structural Components: Structural components may be fabricated using techniques like welding, bonding, or composite layup.
- Assembly and Integration: Components produced in the fabrication phase are assembled into larger systems or structures. This involves careful alignment, connection, and integration to ensure proper functioning. Assembly may also include attaching electrical components, wiring, and sensors, as well as integrating software systems where applicable.
- Quality Control: Throughout the manufacturing process, rigorous quality control measures are implemented. This includes inspections, testing, and validation to ensure that components meet specifications and standards. Quality control checks may involve dimensional inspections, material testing, electrical testing, and functional testing.
- Testing and Validation: Once assembled, the military substrate undergoes comprehensive testing and validation. This includes functional testing to ensure that all components operate as intended, as well as environmental testing to assess performance under various conditions (e.g., temperature, humidity, vibration, shock). Testing may also involve simulations and modeling to predict behavior in real-world scenarios.
- Packaging and Deployment: After successful testing and validation, the military substrate is packaged for deployment. This may involve protective packaging to ensure safe transport and handling. Deployment procedures vary depending on the specific substrate and its intended use, whether it’s integrated into larger systems, installed at military installations, or deployed in the field.
- Lifecycle Support: Throughout the substrate’s lifecycle, ongoing maintenance, repair, and upgrades may be necessary to ensure continued reliability and effectiveness. This includes monitoring performance, conducting periodic inspections, and implementing upgrades or modifications as needed.
By following these steps, manufacturers can produce military substrates that meet the stringent requirements of military applications, providing essential capabilities for defense and security operations.
How much should a Military Substrate cost?
Determining the cost of a military substrate is complex and depends on various factors such as the type of substrate, its complexity, size, materials used, technology involved, production volume, and the specific requirements of the military organization procuring it. Additionally, costs may vary based on the country of manufacture, labor rates, and regulatory requirements.
Here are some considerations that can influence the cost of a military substrate:
- Design Complexity: The complexity of the substrate’s design, including the number of components, the sophistication of technology involved, and the level of integration, can significantly impact its cost.
- Materials and Components: The cost of materials and components used in the substrate’s construction plays a significant role. Specialized materials, advanced electronics, and high-quality components can increase costs.
- Manufacturing Processes: The manufacturing processes involved, such as machining, casting, forging, electronics assembly, or additive manufacturing, can affect costs. Some processes may require specialized equipment and skilled labor, which can add to the overall cost.
- Testing and Validation:Rigorous testing and validation procedures are necessary to ensure the substrate meets military standards and specifications. Testing costs, including equipment, facilities, and personnel, contribute to the overall cost.
- Volume and Scale: Economies of scale can influence costs. Larger production volumes may lead to lower per-unit costs due to efficiencies in manufacturing, while smaller production runs may result in higher costs per unit.
- Regulatory Compliance: Compliance with military standards, regulations, and certifications can add costs. Meeting requirements for reliability, safety, environmental impact, and security may involve additional testing, documentation, and quality control measures.
- Research and Development: If the substrate involves new or innovative technologies, research and development costs may be significant and can impact the overall cost.
- Logistics and Support: Costs associated with logistics, transportation, installation, training, and ongoing support services should also be considered.
Given the wide range of factors involved, it’s challenging to provide a specific cost estimate for a military substrate without detailed specifications and requirements. Cost estimates are typically determined through a detailed analysis conducted during the procurement process, taking into account all relevant factors to arrive at an accurate cost assessment.
What is Military Substrate Base Material?
“Military substrate base material” typically refers to the foundational material used in the construction or fabrication of components, systems, or infrastructure for military purposes. The choice of base material depends on the specific application, performance requirements, environmental conditions, and manufacturing processes involved. Here are some common types of base materials used in military substrates:
- Metals: Metals such as steel, aluminum, titanium, and various alloys are commonly used as base materials in military substrates. Metals offer excellent strength, durability, and thermal conductivity, making them suitable for a wide range of applications, including structural components, armor, weapon systems, and vehicle chassis.
- Polymers: Polymers, including plastics, composites, and synthetic materials, are widely used in military substrates due to their lightweight, corrosion resistance, and versatility. Polymer-based materials are used in applications such as protective gear, equipment enclosures, vehicle components, and electronic housings.
- Ceramics: Ceramics are used in military substrates for their high hardness, wear resistance, and thermal stability. Ceramic materials such as alumina, silicon carbide, and boron carbide are utilized in armor systems, ballistic protection, and components requiring high-temperature resistance.
- Electronic Substrates: Electronic substrates, including printed circuit boards (PCBs), semiconductor materials, and conductive substrates, form the foundation for electronic components and systems used in military applications. These substrates provide the structural support and electrical connectivity required for various electronic devices, communication systems, sensors, and control systems.
- Textiles and Fabrics: Textiles and fabrics are used in military substrates for applications such as protective clothing, shelters, tents, and vehicle covers. Advanced textiles may incorporate materials like aramid fibers (e.g., Kevlar), ballistic nylon, and fire-resistant fabrics to provide protection against ballistic threats, extreme weather, and environmental hazards.
- Composite Materials: Composite materials, consisting of a combination of different materials such as fibers, resins, and fillers, are widely used in military substrates to achieve specific performance characteristics. Composite materials offer advantages such as high strength-to-weight ratio, corrosion resistance, and tailored mechanical properties. They are used in applications ranging from aircraft components and vehicle armor to body armor and weapon systems.
The selection of the appropriate base material for a military substrate depends on factors such as structural requirements, performance specifications, weight constraints, cost considerations, and environmental factors. Engineers and designers carefully evaluate these factors to choose the most suitable base material for each application within military systems and equipment.
Which company makes Military Substrates?
Many companies specialize in manufacturing military substrates. These companies include large enterprises in the aerospace and defense sectors, military contract manufacturers, as well as companies specializing in military technology and equipment development. Some well-known companies such as Lockheed Martin, Boeing, Northrop Grumman, and Raytheon Technologies have extensive experience and expertise in the military domain, covering production aspects such as aerospace, communication systems, military vehicles, and weapon systems. Additionally, there are many small and medium-sized enterprises focused on manufacturing military substrates for specific areas such as electronic devices, tactical equipment, defense systems, and more.
For our company, as a manufacturer of military substrates, we possess the following advantages and capabilities:
- Technical Expertise: We have a professional team of engineers and technicians with the skills and experience needed to design and manufacture various types of military substrates. We are familiar with the latest manufacturing technologies and processes and can customize solutions according to customer requirements.
- High Quality and Reliability:We are committed to providing high-quality, reliable, and durable products to meet the stringent requirements of military applications. We strictly adhere to international standards and quality management systems to ensure that our products meet customer specifications and standards.
- Innovation and Flexibility: We focus on innovation and flexibility, continuously improving and optimizing our production processes to enhance efficiency and performance. We can customize products according to customer needs and respond promptly to market changes and technological developments.
- Partnerships: We have established close partnerships with suppliers, partners, and customers to drive successful project implementation. We collaborate with leading companies in various industries to develop new technologies and solutions.
- Comprehensive Services: We provide comprehensive services including design, manufacturing, testing, delivery, and support to ensure that customers achieve satisfactory results. We maintain close communication with customers, address issues promptly, and provide technical support and training.
In summary, as a professional manufacturer of military substrates, we are committed to providing customers with high-quality, high-performance products and services to meet their military application needs and expectations. We will continue to strive for excellence and work together with customers to create a better future.
What are the 7 qualities of good customer service?
Good customer service is characterized by several key qualities that contribute to a positive experience for customers. Here are seven qualities of good customer service:
- Responsiveness: Good customer service involves being responsive to customer inquiries, concerns, and requests in a timely manner. This means promptly answering phone calls, responding to emails, and addressing customer needs as quickly as possible.
- Empathy: Empathy is the ability to understand and share the feelings of others. Good customer service representatives demonstrate empathy by listening actively to customers, acknowledging their concerns, and showing genuine concern for their well-being.
- Professionalism:Professionalism involves maintaining a courteous and respectful demeanor when interacting with customers. This includes using proper language, maintaining a positive attitude, and adhering to company policies and procedures.
- Knowledgeability: Good customer service representatives possess a thorough understanding of the products or services they are supporting. They are able to answer customer questions accurately, provide relevant information, and offer helpful recommendations or solutions.
- Efficiency: Efficiency is essential in delivering good customer service. This involves resolving customer issues quickly and effectively, minimizing wait times, and streamlining processes to ensure a smooth customer experience.
- Flexibility: Good customer service requires flexibility in adapting to the unique needs and preferences of each customer. This may involve offering customized solutions, accommodating special requests, or being willing to make exceptions within reason.
- Follow-up: Follow-up is an important aspect of good customer service. After addressing a customer’s issue or inquiry, it’s important to follow up to ensure that the resolution was satisfactory and to offer any additional assistance if needed. This demonstrates a commitment to customer satisfaction and helps build long-term relationships.
By embodying these qualities, businesses can deliver exceptional customer service that fosters loyalty, enhances reputation, and contributes to overall success.
FAQs
What are military substrates?
Military substrates refer to the foundational components, systems, or infrastructure used in military equipment, technology, and systems. They serve as the base or framework upon which various military applications are built.
What are the types of military substrates?
Military substrates encompass a wide range of materials, components, and systems, including structural materials, electronic components, communication systems, armor, sensors, and more.
What are the key features of military substrates?
Military substrates are characterized by qualities such as durability, reliability, performance under harsh conditions, compatibility with military standards, and often incorporate features for enhanced security and survivability.
How are military substrates manufactured?
The manufacturing process for military substrates involves various steps including design, material selection, fabrication, assembly, testing, and validation. Different manufacturing techniques and processes are used depending on the type and complexity of the substrate.
What are the applications of military substrates?
Military substrates are used in a wide range of applications across defense and security sectors, including aerospace, land vehicles, maritime vessels, communication systems, weapons systems, surveillance equipment, and protective gear.
What are the challenges in manufacturing military substrates?
Challenges in manufacturing military substrates include meeting stringent quality and performance standards, ensuring compatibility with existing systems, addressing security concerns, managing costs, and navigating regulatory requirements.
Who manufactures military substrates?
Military substrates are manufactured by a variety of companies, including large defense contractors, specialized manufacturers, and suppliers of military equipment and technology. These companies may produce substrates for specific applications or components within larger systems.
What are the future trends in military substrates?
Future trends in military substrates include advancements in materials science, integration of emerging technologies such as artificial intelligence and nanotechnology, development of lightweight and multifunctional materials, and increasing emphasis on sustainability and environmental resilience.