Mini led pcb manufacturing
What is Mini LED PCB?
Mini led pcb manufacturing and package substrate manufacturing. We use advanced Msap and Sap technology to produce smllest spacing mini LED and BGA substrates from 2 to 20 layers.
A Mini LED PCB (Printed Circuit Board) is a type of circuit board specifically designed to accommodate mini LEDs. Mini LEDs are smaller versions of traditional LEDs (Light Emitting Diodes) that offer improved brightness, contrast, and energy efficiency.
The Mini LED PCB typically features densely packed LED placements, allowing for high-resolution displays or lighting applications. These PCBs are engineered to efficiently manage power distribution, thermal dissipation, and signal routing for the mini LEDs, ensuring optimal performance and longevity.
Mini LED technology is often employed in various applications such as high-definition displays, backlighting for TVs, monitors, laptops, automotive lighting, and other illumination systems where precise control and high brightness are required. The Mini LED PCB plays a crucial role in integrating these mini LEDs into such applications effectively.
What is the function of Mini LED PCB?
The functions of Mini LED PCB include:
- Support: Mini LED PCB provides a platform for supporting and mounting mini LEDs, ensuring their correct positioning and secure connections.
- Power management: The circuit design on the PCB helps manage power distribution, ensuring that LEDs receive stable current and voltage to operate properly and provide consistent brightness.
- Signal routing: Wires and circuitry designs on the PCB are used to transmit control signals and data, allowing LEDs to be adjusted and controlled as needed.
- Thermal management: Since LED illumination generates heat, Mini LED PCBs often incorporate effective heat dissipation systems to maintain proper temperature during prolonged use, thus improving performance and longevity.
In summary, Mini LED PCBs play crucial roles in installation, power management, signal transmission, and thermal management, ensuring that mini LEDs operate effectively and deliver the desired optical performance.
What are the different types of Mini LED PCB?
There are several different types of Mini LED PCBs, each tailored to specific applications and requirements. Some common types include:
- Display PCBs: These PCBs are designed for use in high-resolution displays such as TVs, monitors, and digital signage. They typically feature densely packed mini LEDs arranged in a grid pattern to achieve high pixel density and image quality.
- Backlighting PCBs: Used in LCD panels for backlighting, these PCBs employ mini LEDs to provide uniform and adjustable illumination behind the display panel. They are commonly found in TVs, computer monitors, and automotive displays.
- Lighting PCBs: These PCBs are utilized in various lighting applications, such as architectural lighting, automotive lighting, and decorative lighting. They can be designed for surface-mounted or through-hole mini LEDs, depending on the specific lighting requirements.
- Specialized PCBs: Some Mini LED PCBs are designed for specific applications or industries, such as medical devices, aerospace, or industrial equipment. These PCBs may have unique features tailored to the needs of their intended use.
- Flexible PCBs: Flexible PCBs, also known as flex PCBs, are designed to be bent or twisted, making them suitable for applications where space constraints or unconventional form factors are present. They can be used in wearable devices, curved displays, and other innovative applications.
- Customized PCBs: In addition to standard types, Mini LED PCBs can be customized to meet specific requirements, including size, shape, layout, and performance characteristics. Customized PCBs are often used in specialized applications where off-the-shelf solutions may not suffice.
These are just a few examples of the different types of Mini LED PCBs available, and the choice of PCB type depends on factors such as the application, performance requirements, and design constraints.
What is the difference between Mini LED PCB and LED packaging?
The different types of Mini LED PCB include:
- Display PCB: Used in high-resolution display devices such as TVs, monitors, and digital signage. These PCBs feature tightly packed mini LEDs arranged in a grid pattern to achieve high pixel density and quality images.
- Backlighting PCB: Employed for backlighting LCD panels, these PCBs use mini LEDs to provide uniform and adjustable illumination from behind. They are commonly found in TVs, computer monitors, and automotive displays.
- Lighting PCB: Utilized for various lighting applications such as architectural, automotive, and decorative lighting. They can be designed for surface-mount or through-hole mini LEDs, depending on specific lighting requirements.
- Specialized PCB: Specifically designed for particular applications or industries like medical devices, aerospace, or industrial equipment. These PCBs may have specialized features tailored to their intended use.
- Flexible PCB: Also known as flex PCBs, these are designed to be bendable or twistable, suitable for applications with space constraints or unconventional shapes. They can be used in wearable devices, curved displays, and other innovative applications.
- Custom PCB: Apart from standard types, Mini LED PCBs can be customized to meet specific size, shape, layout, and performance requirements. Custom PCBs are often used in specialized applications requiring tailored solutions.
These are the different types of Mini LED PCBs, and the choice of PCB type depends on factors such as application, performance requirements, and design constraints.
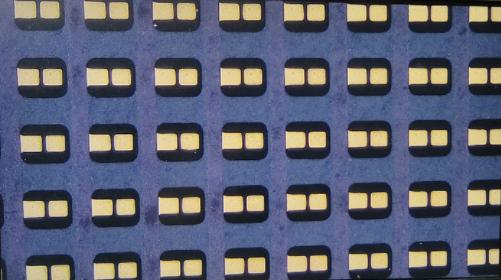
Mini LED PCB
What are the differences between Mini LED PCB and conventional PCBs?
The difference between Mini LED PCB and LED packaging lies in their respective roles and components:
1. Mini LED PCB:
Function: Mini LED PCB (Printed Circuit Board) serves as a platform for mounting and connecting mini LEDs.
Components: The PCB includes circuitry for power distribution, signal routing, and possibly thermal management to ensure optimal performance of the mini LEDs.
Purpose: Mini LED PCBs are used to integrate and control mini LEDs in various applications such as displays, backlighting, and lighting systems.
2. LED Packaging:
Function: LED packaging involves encapsulating the LED chip (semiconductor material) to protect it from environmental factors and to provide electrical connections.
Components: LED packaging typically includes the LED chip, a phosphor coating (for white LEDs), and the package itself, which can be made of various materials such as plastic, ceramic, or epoxy.
Purpose: LED packaging is primarily focused on encapsulating the LED chip to ensure reliability, durability, and efficient light emission. It provides electrical connections for power supply and can influence factors such as light output, color rendering, and beam angle.
In summary, Mini LED PCB focuses on providing a platform for mounting and controlling mini LEDs within a system, while LED packaging involves encapsulating the LED chip to protect it and provide electrical connections for integration into various applications. Both play essential roles in the overall performance and functionality of LED-based systems.
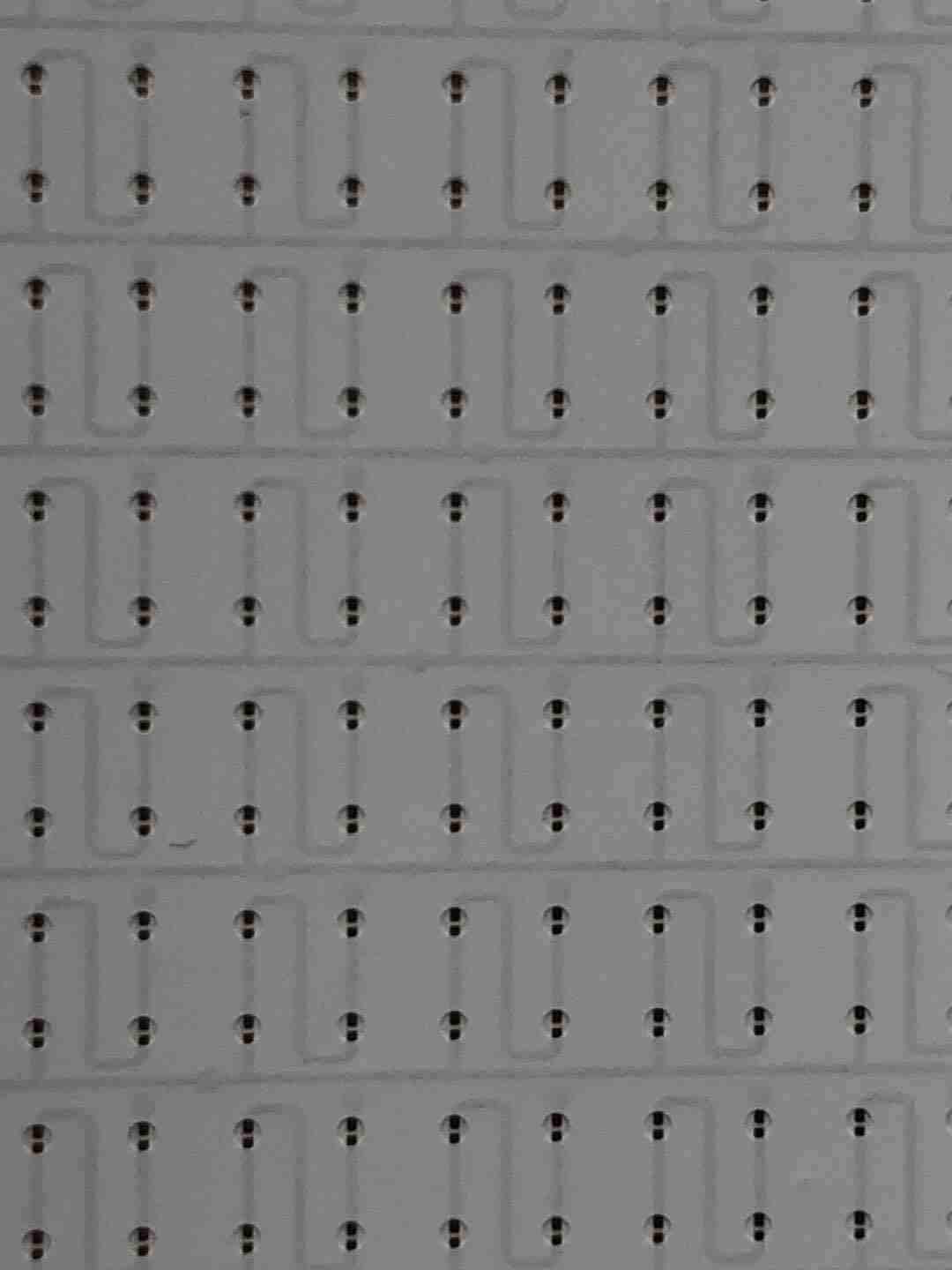
Mini LED PCB
What are the main structure and production technologies of Mini LED PCB?
The main structure and production technologies of Mini LED PCB typically involve several key components and manufacturing processes:
- Substrate Material Selection: The substrate material forms the base of the PCB and provides mechanical support and electrical insulation. Common substrate materials include FR-4 (fiberglass reinforced epoxy laminate), metal core PCBs (MCPCBs), and flexible materials such as polyimide for flexible PCBs.
- Circuit Design: The circuit design involves the layout of conductive traces, pads, and vias on the PCB to establish electrical connections between components, such as mini LEDs, resistors, and drivers. Advanced design software is used to optimize signal integrity, power distribution, and thermal management.
- Mini LED Placement and Soldering: Mini LEDs are placed onto the PCB according to the desired layout and configuration. Surface-mount technology (SMT) is commonly used for mini LED placement, where solder paste is applied to the pads, and then the components are mounted using pick-and-place machines. Alternatively, through-hole technology (THT) can be used for certain applications where mini LEDs are mounted through holes in the PCB and soldered from the opposite side.
- Solder Mask Application: A solder mask layer is applied over the PCB to protect the circuitry and prevent solder bridging during soldering. The solder mask is typically a green or other colored resin applied to the PCB surface, leaving openings only where solder joints are required.
- Silkscreen Printing: Silkscreen printing is used to apply component labels, markings, and other identifiers onto the PCB surface for easy assembly and identification. This process helps technicians and assemblers identify component placement, polarity, and orientation.
- Surface Finish: Surface finish techniques such as HASL (hot air solder leveling), ENIG (electroless nickel immersion gold), or OSP (organic solderability preservatives) are applied to the exposed copper traces to protect them from oxidation and provide a suitable surface for soldering components.
- Testing and Inspection: After assembly, Mini LED PCBs undergo testing and inspection processes to ensure functionality and quality. This may include electrical testing, visual inspection, and thermal testing to verify proper operation and reliability.
Overall, the production of Mini LED PCBs involves a combination of precise design, component placement, soldering techniques, and quality control measures to ensure the reliability and performance of the final product.
FAQs
What is a Mini LED PCB?
A Mini LED PCB is a type of printed circuit board designed to accommodate mini LEDs. It provides a platform for mounting and connecting mini LEDs for various applications such as displays and lighting systems.
What are the main components of a Mini LED PCB?
The main components of a Mini LED PCB include the substrate material, conductive traces, pads, vias, mini LEDs, resistors, drivers, solder mask, and surface finish.
What are the common applications of Mini LED PCBs?
Mini LED PCBs are commonly used in high-resolution displays, backlighting for LCD panels, automotive lighting, architectural lighting, and various other lighting applications where precise control and high brightness are required.
What are the advantages of Mini LED technology?
Mini LED technology offers advantages such as improved brightness, contrast, energy efficiency, and finer pixel pitch compared to traditional LEDs. It also enables thinner and lighter display designs with better color accuracy and uniformity.
What production technologies are used for Mini LED PCBs?
Production technologies for Mini LED PCBs include substrate material selection, circuit design, mini LED placement and soldering (using surface-mount or through-hole technology), solder mask application, silkscreen printing, surface finish application, and testing/inspection processes.
How do Mini LED PCBs differ from traditional LED PCBs?
Mini LED PCBs are designed to accommodate smaller-sized LEDs known as mini LEDs, which offer improved performance compared to traditional LEDs. Mini LED PCBs often feature denser LED placement, finer pitch, and enhanced thermal management to support the unique characteristics of mini LEDs.
What factors should be considered when selecting a Mini LED PCB?
Factors to consider when selecting a Mini LED PCB include the application requirements (such as display resolution, brightness, and color accuracy), size and form factor constraints, thermal management capabilities, reliability, and cost.
What are the future trends in Mini LED technology and PCB manufacturing?
Future trends in Mini LED technology and PCB manufacturing may include further advancements in mini LED performance, increased integration of Mini LED arrays into flexible and curved displays, and improvements in manufacturing processes to enhance efficiency and reduce costs.
Conclusion
It seems like you’re looking for a conclusion. Concluding a document or discussion often involves summarizing the main points or findings. Here’s a generic conclusion:
In conclusion, the topic of Mini LED PCBs encompasses various aspects, including their structure, production technologies, applications, and benefits. These PCBs play a crucial role in integrating and controlling mini LEDs in a wide range of devices and systems, such as displays, backlighting, and lighting solutions. Understanding the different types, production processes, and quality control measures associated with Mini LED PCBs is essential for achieving optimal performance and reliability in LED-based applications. As technology continues to advance, Mini LED PCBs are expected to play an increasingly important role in driving innovation and enhancing the capabilities of various electronic products.