Mini LED Substrate manufacturing
Mini LED Substrate Manufacturing, Minimum trace and minimum spacing, We offer the Mini LED PCB from 2 layer to 14 layers, the best samllest pads to pads spacing are 30um, most are 40um to 60um. we offer this small gap led pcb with fast shipping time. Mini LED substrates serve as the fundamental building blocks for advanced display technologies, offering unparalleled performance and versatility. These substrates, typically crafted from materials like silicon, glass, or ceramic, provide the essential foundation for mounting and connecting Mini LED chips. With their miniature size and high pixel density, Mini LED substrates enable displays to achieve stunning image quality, exceptional brightness, and energy efficiency.
Manufactured through precise processes, Mini LED substrates undergo meticulous thin film deposition, patterning, and chip mounting procedures to ensure optimal performance and reliability. Their compatibility with existing display manufacturing processes facilitates seamless integration into various applications, ranging from televisions and monitors to digital signage and automotive displays.
As the demand for high-resolution, immersive visual experiences continues to grow, Mini LED substrates are poised to play a pivotal role in driving innovation in display technology. With advancements in materials science and manufacturing techniques, Mini LED substrates promise to unlock new possibilities for next-generation displays, delivering captivating visuals and enhancing user experiences across diverse industries.
What is a Mini LED Substrate?
Mini LED Substrate manufacturing.High speed and high frequency material packaging substrate manufacturing. Advanced packaging substrate production process and technology
A Mini LED substrate refers to the base material used for manufacturing Mini LED displays. Mini LEDs are a type of LED technology that features smaller LED chips compared to traditional LEDs, typically measuring less than 0.2 mm in size. These smaller LED chips allow for higher pixel density and improved image quality.
The substrate is a crucial component in Mini LED displays as it provides a foundation for mounting the Mini LED chips, connecting them electrically, and ensuring proper heat dissipation. It is usually made of materials such as silicon, glass, or ceramic, depending on the specific requirements of the display.
The design and quality of the Mini LED substrate play a significant role in determining the overall performance and durability of the display. High-quality substrates help to achieve better heat dissipation, electrical conductivity, and mechanical stability, which are essential for ensuring long-term reliability and optimal performance of Mini LED displays.
What are the Mini LED Substrate Design Guidelines?
Mini LED substrate design guidelines typically encompass several key considerations to ensure optimal performance and reliability of Mini LED displays. Some common design guidelines may include:
- Thermal Management: Efficient heat dissipation is crucial for Mini LED displays to maintain optimal performance and longevity. The substrate design should facilitate effective thermal management, such as incorporating thermal vias or heat sinks to dissipate heat generated by the LEDs.
- Electrical Connectivity: The substrate should provide reliable electrical connections between the Mini LED chips and the driving electronics. This involves ensuring proper routing of electrical traces and vias to minimize signal loss and electromagnetic interference.
- Mechanical Stability: The substrate should be structurally robust to withstand mechanical stresses and vibrations encountered during handling, transportation, and operation. Adequate reinforcement and support structures may be incorporated into the design to enhance mechanical stability.
- Alignment and Positioning: Precise alignment and positioning of Mini LED chips on the substrate are essential for achieving uniform illumination and image quality. Design considerations should include mechanisms for accurate placement and alignment of the LEDs during manufacturing processes.
- Manufacturability: The substrate design should be compatible with established manufacturing processes and equipment. Design features that facilitate automated assembly, such as standardized footprints and component placement guidelines, can improve manufacturability and yield.
- Material Selection: Choosing appropriate substrate materials is crucial for meeting performance requirements and cost considerations. Factors such as thermal conductivity, electrical insulation, and mechanical strength should be taken into account when selecting substrate materials.
- Optical Considerations: The substrate design should minimize light attenuation and optimize light extraction efficiency to maximize the brightness and uniformity of the Mini LED display. This may involve surface treatments or coatings to enhance optical properties.
- Reliability and Durability: The substrate design should undergo rigorous testing and validation to ensure reliability and durability under various operating conditions, including temperature fluctuations, humidity, and mechanical stress.
By adhering to these design guidelines, manufacturers can develop Mini LED substrates that meet the performance, reliability, and quality requirements of Mini LED displays, enabling the realization of high-resolution, high-brightness displays for various applications.
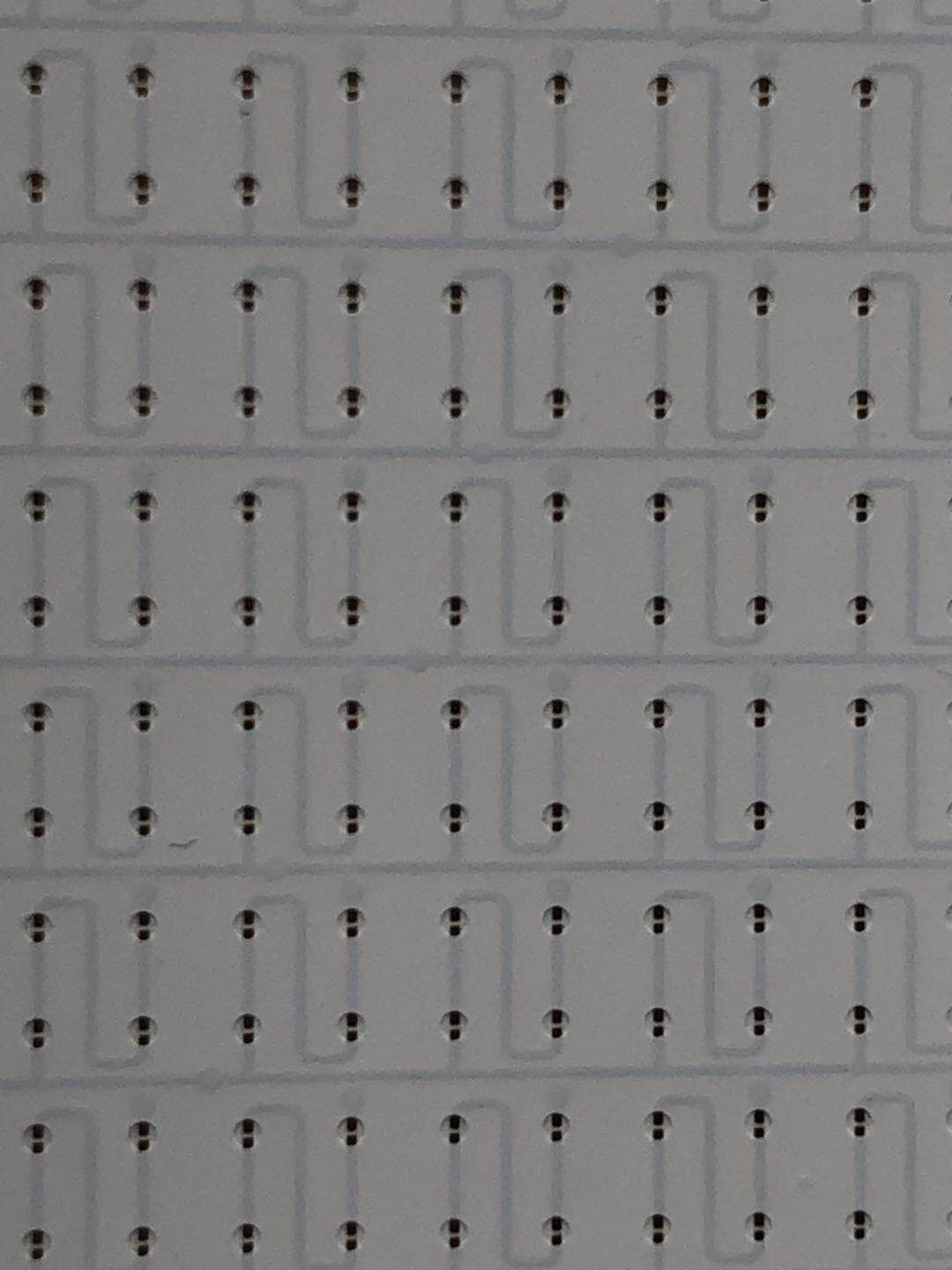
Mini LED Substrate
What is the Mini LED Substrate Fabrication Process?
The fabrication process for Mini LED substrates involves several steps to create a base material capable of supporting and connecting the Mini LED chips while providing efficient thermal management and electrical connectivity. Here’s a general overview of the fabrication process:
- Substrate Preparation: The process begins with the preparation of the substrate material, which could be silicon, glass, or ceramic. The substrate is typically manufactured as a thin, flat sheet or wafer with precise dimensions and surface properties.
- Surface Preparation: The substrate surface is cleaned and prepared to ensure proper adhesion of subsequent layers and components. This may involve cleaning treatments, surface etching, or deposition of adhesion-promoting layers.
- Thin Film Deposition: Thin films of various materials are deposited onto the substrate surface using techniques such as physical vapor deposition (PVD), chemical vapor deposition (CVD), or sputtering. These thin films may include conductive layers for electrical connectivity, insulating layers for isolation, and reflective layers for optical enhancement.
- Pattern Definition: Photolithography or other patterning techniques are used to define the layout of Mini LED chip placement and electrical interconnects on the substrate surface. A photoresist layer is applied to the substrate, exposed to UV light through a mask, and developed to transfer the desired pattern onto the substrate.
- Mini LED Chip Mounting: Mini LED chips are placed onto the substrate according to the predefined pattern using pick-and-place or automated assembly equipment. The chips are bonded to the substrate surface using adhesive materials or soldering techniques.
- Wire Bonding or Flip-Chip Bonding: Electrical connections between the Mini LED chips and the substrate are established through wire bonding or flip-chip bonding techniques. Wire bonding involves attaching fine wires from the LED chip pads to corresponding pads on the substrate, while flip-chip bonding involves directly connecting the LED chip pads to the substrate pads without wires.
- Encapsulation and Packaging: The Mini LED chips and electrical connections are encapsulated and protected using transparent encapsulation materials to provide mechanical support and environmental protection. The encapsulated substrate may undergo additional processing steps such as curing, sealing, or coating.
- Testing and Quality Control: The fabricated Mini LED substrates undergo rigorous testing and quality control procedures to ensure proper functionality, electrical performance, and reliability. This may include electrical testing, optical inspection, thermal cycling, and reliability testing under various environmental conditions.
- Integration into Display Modules: Once validated, the Mini LED substrates are integrated into display modules along with other components such as driver electronics, backlights, and protective layers to create Mini LED displays ready for use in various applications.
Throughout the fabrication process, strict adherence to design specifications, process parameters, and quality standards is essential to produce Mini LED substrates with high performance, reliability, and consistency.
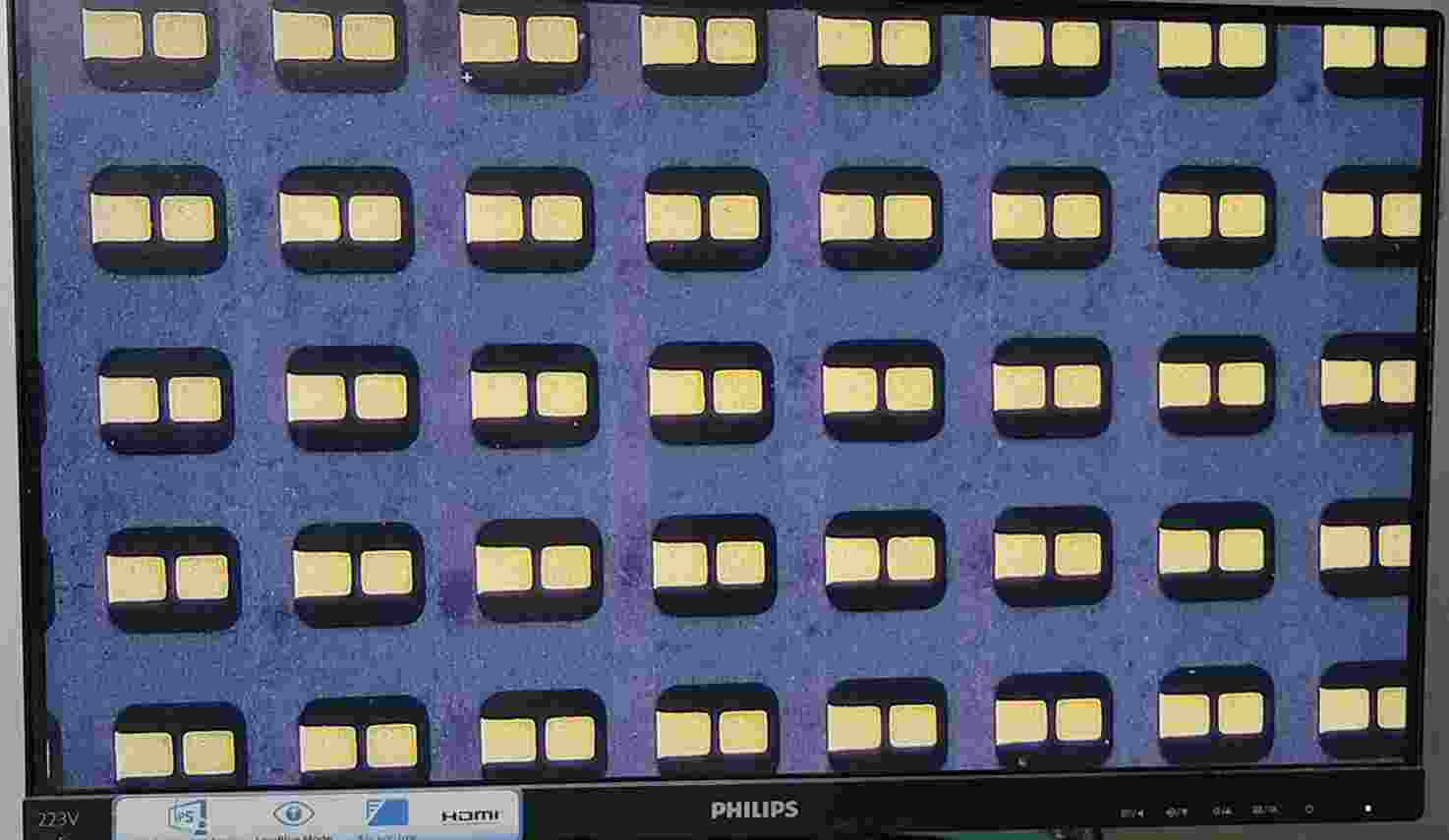
Small gap LED Substrate
How do you manufacture a Mini LED Substrate?
Manufacturing a Mini LED substrate involves several steps to create a base material capable of supporting Mini LED chips and providing necessary electrical connections, thermal management, and mechanical stability. Here’s a simplified overview of the manufacturing process:
- Substrate Selection: Choose a suitable substrate material such as silicon, glass, or ceramic. The substrate should have properties like thermal conductivity, mechanical strength, and electrical insulation appropriate for the application.
- Substrate Preparation: Prepare the substrate material by cutting it into the desired size and shape. Clean the substrate surface to remove contaminants and ensure proper adhesion of subsequent layers.
- Deposition of Thin Films:Deposit thin films onto the substrate surface using techniques like physical vapor deposition (PVD), chemical vapor deposition (CVD), or sputtering. These thin films may include conductive layers for electrical connectivity, insulating layers for isolation, and reflective layers for optical enhancement.
- Photolithography and Patterning: Use photolithography or similar techniques to define the layout of Mini LED chip placement and electrical interconnects on the substrate. Apply a photoresist layer, expose it to UV light through a mask, and develop the pattern onto the substrate surface.
- Mini LED Chip Mounting: Place Mini LED chips onto the substrate according to the predefined pattern using pick-and-place or automated assembly equipment. Bond the chips to the substrate surface using adhesive materials or soldering techniques.
- Wire Bonding or Flip-Chip Bonding: Establish electrical connections between the Mini LED chips and the substrate through wire bonding or flip-chip bonding techniques. Wire bonding involves attaching fine wires from the LED chip pads to corresponding pads on the substrate, while flip-chip bonding involves directly connecting the LED chip pads to the substrate pads without wires.
- Encapsulation and Packaging: Encapsulate the Mini LED chips and electrical connections using transparent encapsulation materials to provide mechanical support and environmental protection. Additional processing steps such as curing, sealing, or coating may be necessary.
- Testing and Quality Control: Conduct rigorous testing and quality control procedures to ensure proper functionality, electrical performance, and reliability of the fabricated Mini LED substrates. This may include electrical testing, optical inspection, thermal cycling, and reliability testing under various environmental conditions.
- Integration into Display Modules: Once validated, integrate the Mini LED substrates into display modules along with other components such as driver electronics, backlights, and protective layers to create Mini LED displays suitable for various applications.
Throughout the manufacturing process, strict adherence to design specifications, process parameters, and quality standards is crucial to produce Mini LED substrates with high performance, reliability, and consistency.
How much should a Mini LED Substrate cost?
The cost of a Mini LED substrate can vary significantly depending on various factors such as the substrate material, size, complexity of design, manufacturing processes, and vendor pricing. As of my last update in January 2022, specific pricing information for Mini LED substrates may not be readily available due to the proprietary nature of manufacturing processes and agreements between suppliers and customers.
However, I can provide some general insights:
- Material Cost: The choice of substrate material (e.g., silicon, glass, ceramic) significantly influences the cost. Silicon substrates are typically more expensive than glass or ceramic substrates.
- Manufacturing Complexity: The complexity of the substrate design and manufacturing processes can affect the cost. Substrates with intricate patterns, multiple layers, or advanced features may require more time and resources to manufacture, increasing the cost.
- Volume and Economy of Scale: Larger production volumes often lead to lower per-unit costs due to economies of scale. Manufacturers may offer discounts for bulk orders.
- Quality and Performance: Higher-quality substrates with superior performance characteristics may command a premium price compared to standard substrates.
- Supplier Pricing and Agreements: Prices can vary between different suppliers based on their manufacturing capabilities, overhead costs, profit margins, and competitive positioning. Additionally, pricing may be influenced by contractual agreements between suppliers and customers.
To obtain accurate pricing for Mini LED substrates, it’s advisable to directly contact manufacturers or suppliers specializing in LED substrate fabrication and inquire about pricing based on your specific requirements and order volume. Additionally, consulting industry experts or conducting market research may provide insights into typical pricing ranges for Mini LED substrates in the current market.
What is Mini LED Substrate base material?
The base material for Mini LED substrates can vary depending on the specific requirements of the application and the manufacturing processes involved. Some common materials used as the base substrate for Mini LED displays include:
- Silicon:Silicon substrates offer good thermal conductivity and mechanical stability, making them suitable for high-performance applications. They are often used in semiconductor manufacturing processes and can be processed into thin, flat wafers.
- Glass: Glass substrates provide excellent optical transparency, making them suitable for applications where optical performance is critical. They can be manufactured with precise dimensions and surface properties and are commonly used in display technologies.
- Ceramic: Ceramic substrates offer high thermal conductivity and mechanical strength, making them suitable for applications requiring efficient heat dissipation and robustness. They are often used in high-power LED applications and electronic packaging.
The choice of substrate material depends on factors such as thermal management requirements, mechanical stability, optical properties, and cost considerations. Each material has its advantages and limitations, and the selection is based on the specific needs of the Mini LED display design and manufacturing process.
Which company makes Mini LED Substrates? (Our Currently, many companies have rich experience and technological capabilities in manufacturing Mini LED Substrates. Some well-known companies include Samsung, LG, BOE, Infineon, Micron, and others. These companies have strong technical expertise and research and development capabilities in semiconductor manufacturing, display technology, and material science, enabling them to produce high-quality Mini LED Substrates.
As for our company, we also have the capability to manufacture Mini LED Substrates. We have advanced manufacturing equipment and a skilled technical team dedicated to the research and production of high-performance display devices and materials. Our engineering team has extensive experience and can customize various types of Mini LED Substrates according to customer requirements while ensuring compliance with quality standards and technical specifications.
We prioritize innovation and continuous improvement, striving to provide customers with excellent products and services. Our production processes strictly adhere to quality management systems to ensure the stability, reliability, and performance of our products. Meanwhile, we actively monitor the latest developments and technological trends in the industry, continuously optimizing our manufacturing processes to enhance product competitiveness.
As a professional manufacturer of Mini LED Substrates, we are committed to establishing long-term partnerships with customers to drive industry development and progress. We will provide satisfactory solutions to customers with excellent product quality, high-quality service, and flexible customization capabilities, achieving mutually beneficial development.
What are the 7 qualities of good customer service?
Good customer service is essential for building and maintaining positive relationships with customers. Here are seven qualities that characterize good customer service:
- Responsiveness: Good customer service involves promptly addressing customer inquiries, concerns, and requests. Responding to customers in a timely manner shows that their needs are valued and helps to foster trust and satisfaction.
- Empathy: Empathy is the ability to understand and share the feelings of others. Good customer service representatives demonstrate empathy by actively listening to customers, acknowledging their concerns, and showing genuine concern for their well-being.
- Clarity and Communication: Effective communication is crucial for providing good customer service. Customer service representatives should communicate clearly and concisely, avoiding jargon or technical language that may confuse customers. They should also ensure that customers understand the information provided and any next steps required.
- Problem-solving Skills: Good customer service involves effectively resolving customer issues and complaints. Customer service representatives should possess strong problem-solving skills, be resourceful in finding solutions, and be empowered to make decisions that benefit the customer.
- Professionalism: Professionalism encompasses various qualities such as courtesy, respectfulness, and integrity. Customer service representatives should conduct themselves professionally at all times, maintaining a positive attitude and treating customers with dignity and respect.
- Product Knowledge: Good customer service requires a thorough understanding of the products or services being offered. Customer service representatives should be knowledgeable about the features, benefits, and usage of the products or services and be able to provide accurate information to customers.
- Follow-up and Follow-through: Following up with customers after a service interaction demonstrates a commitment to their satisfaction. Good customer service involves ensuring that any promises made to customers are fulfilled, and following through on commitments in a timely manner.
By embodying these qualities, businesses can deliver exceptional customer service experiences that help to build loyalty, enhance brand reputation, and drive customer satisfaction and retention.
FAQs (Frequently Asked Questions)
What is a Mini LED substrate?
A Mini LED substrate is a base material used for manufacturing Mini LED displays. It provides a foundation for mounting Mini LED chips, connecting them electrically, and ensuring proper heat dissipation.
What are the advantages of Mini LED substrates?
Mini LED substrates offer several advantages, including higher pixel density, improved image quality, enhanced brightness, and better energy efficiency compared to traditional LED displays.
What materials are used to make Mini LED substrates?
Mini LED substrates can be made from materials such as silicon, glass, or ceramic, depending on the specific requirements of the display.
How are Mini LED substrates manufactured?
The manufacturing process for Mini LED substrates involves several steps, including substrate preparation, deposition of thin films, patterning, Mini LED chip mounting, wire bonding, encapsulation, testing, and quality control.
What factors should be considered when selecting Mini LED substrates?
Factors to consider when selecting Mini LED substrates include thermal conductivity, electrical conductivity, mechanical stability, material cost, manufacturability, and compatibility with display requirements.
What applications are Mini LED substrates used for?
Mini LED substrates are used in various applications, including high-resolution displays, televisions, monitors, digital signage, automotive displays, and augmented reality/virtual reality (AR/VR) devices.
What are the differences between Mini LED substrates and other display technologies?
Mini LED substrates offer advantages such as higher pixel density, improved image quality, and better energy efficiency compared to traditional LED displays. They also provide a more cost-effective alternative to technologies like OLED displays.
Are Mini LED substrates compatible with existing display manufacturing processes?
Yes, Mini LED substrates are compatible with existing display manufacturing processes, allowing for seamless integration into production lines and facilitating the development of next-generation displays.
What are the future trends in Mini LED substrate technology?
Future trends in Mini LED substrate technology include further improvements in pixel density, increased adoption in various applications, advancements in manufacturing processes, and integration with emerging display technologies.
Where can I purchase Mini LED substrates?
Mini LED substrates can be purchased from various suppliers specializing in display components and materials. It’s advisable to research different suppliers, compare product offerings, and inquire about pricing and customization options.