Minimum spacing PCB manufacturing
Minimum spacing PCB manufacturing, Suitable for small pitch LED PCB, HDI PCB, BGA package substrates. we offer Minimum spacing PCB and Minimum spacing BGA substrates from 2 layer to 22 layers. the best smallest spacing are 9um.
A Minimum Spacing PCB is a type of printed circuit board designed for electronic devices, characterized by minimal spacing between circuit components to ensure stability and reliability. This design considers the mutual influence and interference between circuit components, reducing electromagnetic interference and signal crosstalk through precise layout and spacing control.
In a Minimum Spacing PCB, engineers must determine the optimal layout and spacing based on the properties of the circuit components and functional requirements. They need to consider factors such as signal transmission speed, current flow paths, and the electrical characteristics between components. Through careful design, signal distortion and circuit noise can be minimized, enhancing circuit performance and stability.
This type of PCB is common in high-performance electronic devices such as computers, communication equipment, and medical instruments. They require highly precise manufacturing processes and rigorous testing and validation to ensure their performance and reliability. In summary, Minimum Spacing PCBs are an essential part of the modern electronics engineering field, providing reliable circuit solutions for various applications.
What is a Minimum Spacing PCB?
A Minimum Spacing PCB refers to a printed circuit board (PCB) design in which components and conductive traces are placed with the smallest possible distance between them while maintaining the integrity and reliability of the circuit.
The “spacing” in PCB design refers to the minimum distance between conductive traces, components, and other features on the board. This distance is crucial to prevent electrical interference, crosstalk, short circuits, and other issues that can arise in electronic circuits.
Designers strive to minimize the spacing between components and traces to make the most efficient use of space on the board and to achieve compact, high-density designs. However, they must also adhere to industry standards and best practices to ensure the reliability and functionality of the PCB.
Achieving a minimum spacing PCB requires careful consideration of factors such as signal integrity, thermal management, manufacturability, and assembly processes. Advanced design tools and techniques, along with close collaboration between electrical engineers and PCB manufacturers, are essential to create successful minimum spacing PCB layouts.
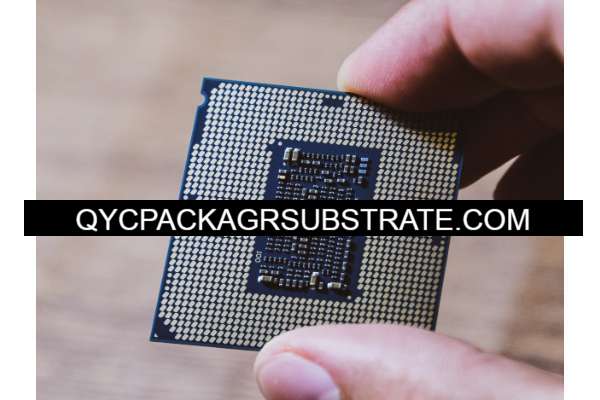
Minimum spacing PCB manufacturing
What are the Minimum Spacing PCB Design Guidelines?
Minimum spacing PCB design guidelines outline the recommended rules and considerations for placing components, traces, and other features on a printed circuit board (PCB) while maintaining the required minimum distances to ensure electrical performance, reliability, and manufacturability. Here are some common guidelines:
- Clearance between traces: Ensure an adequate clearance between traces to prevent electrical shorts. The minimum clearance depends on factors such as the voltage levels, signal integrity requirements, and manufacturing capabilities.
- Clearance between traces and pads: Maintain sufficient clearance between traces and component pads to prevent solder bridging during assembly. This also helps to avoid unintentional electrical connections.
- Clearance between traces and board edges: Provide a minimum distance between traces and the board edges to prevent manufacturing defects and ensure mechanical integrity.
- Clearance between components: Leave enough space between components to facilitate assembly, inspection, and maintenance. This also helps to prevent thermal interference between components.
- Clearance between components and heatsinks: If using heatsinks or heat sinks, ensure adequate clearance between components and heatsinks to allow for proper airflow and heat dissipation.
- Clearance for high-voltage components: Increase clearance around components carrying high voltages to minimize the risk of electrical breakdown and arcing.
- Trace width and spacing: Choose appropriate trace widths and spacing to meet the current-carrying capacity requirements and impedance control of the circuit. Consider factors such as signal integrity, power distribution, and thermal management.
- Minimum hole sizes: Define the minimum hole sizes for vias and through-holes based on the PCB fabrication process and component mounting requirements.
- Minimum annular ring sizes: Specify the minimum annular ring sizes (the ring of copper around a drilled hole) to ensure reliable electrical connections and mechanical strength.
- Compliance with standards: Adhere to industry standards and specifications such as IPC-2221 for PCB design to ensure compatibility with manufacturing processes and reliability standards.
- Design for manufacturability (DFM): Consider manufacturability factors such as solder mask expansion, panelization requirements, and assembly constraints when determining minimum spacing guidelines.
- Thermal considerations: Ensure adequate spacing and thermal relief for components that generate heat to prevent overheating and thermal stress on the PCB.
These guidelines may vary depending on the specific requirements of the PCB design, the manufacturing process, and the intended application. It’s essential to consult with PCB design experts and manufacturers to optimize the layout while adhering to minimum spacing guidelines.
What is the Minimum Spacing PCB Fabrication Process?
The minimum spacing PCB fabrication process involves several steps to create a printed circuit board (PCB) design with the smallest possible distances between components, traces, and other features while ensuring electrical performance, reliability, and manufacturability. Here’s an overview of the typical process:
- Design Preparation: The process begins with the preparation of the PCB design using computer-aided design (CAD) software. Designers define the layout of components, traces, vias, and other features according to the specifications and requirements of the circuit.
- Design Rule Check (DRC): Before fabrication, the design undergoes a design rule check (DRC) to ensure that it complies with minimum spacing guidelines, as well as other design rules such as trace width, clearance, and hole sizes. Any violations are identified and corrected at this stage.
- Panelization: For mass production, multiple PCB designs are often arranged on a larger panel to optimize fabrication efficiency. Panelization involves arranging the individual PCB designs within the panel while maintaining proper spacing between them.
- Photolithography: The PCB fabrication process typically starts with a substrate material, such as fiberglass-reinforced epoxy laminate, coated with a layer of copper foil. Photolithography is used to transfer the PCB design onto the copper layer. A photoresist material is applied to the copper surface, exposed to ultraviolet (UV) light through a mask containing the PCB pattern, and then developed to remove the unexposed photoresist, leaving behind the patterned photoresist mask.
- Etching: The exposed copper areas not protected by the photoresist mask are etched away using chemical etchants, leaving behind the desired copper traces and features defined by the PCB design. The etching process precisely controls the depth and dimensions of the copper features.
- Drilling: Holes are drilled at specified locations on the PCB for component mounting and interconnection through vias. The drill sizes and positions are determined by the PCB design, including the minimum spacing requirements for component pads and vias.
- Plating: After drilling, the inner walls of the holes are plated with a thin layer of conductive material, typically copper, to create electrical connections between the different layers of the PCB.
- Surface Finishing: Surface finishing processes are applied to the exposed copper surfaces to improve solderability, protect against oxidation, and enhance the reliability of the PCB. Common surface finishes include HASL (Hot Air Solder Leveling), ENIG (Electroless Nickel Immersion Gold), and OSP (Organic Solderability Preservatives).
- Solder Mask Application: A solder mask layer is applied over the entire surface of the PCB, leaving openings only where solder pads and vias are located. The solder mask protects the copper traces from environmental damage and prevents solder bridging during assembly.
- Silkscreen Printing: Information such as component labels, reference designators, and polarity markings are printed onto the PCB surface using a silkscreen printing process. This information assists in component placement, assembly, and troubleshooting.
- Final Inspection and Testing: The fabricated PCBs undergo inspection and testing to ensure they meet the quality standards and specifications defined by the design requirements and industry standards. This may include visual inspection, electrical testing, and functionality testing.
By carefully controlling each step of the PCB fabrication process and adhering to minimum spacing guidelines, manufacturers can produce high-quality PCBs with dense component layouts and optimized performance for various electronic applications.
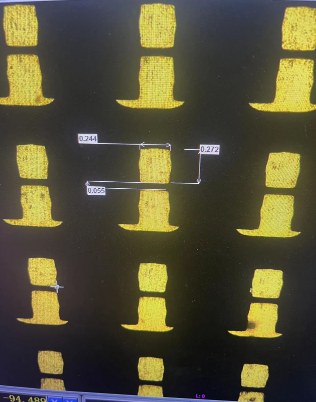
Minimum spacing PCB
How do you manufacture a Minimum Spacing PCB?
Manufacturing a minimum spacing PCB involves following a meticulous process to ensure that the layout meets tight spacing requirements while maintaining reliability and manufacturability. Here’s a step-by-step overview of how it’s typically done:
- Design Optimization: Start with a PCB design that is optimized for minimum spacing. This involves careful component placement, trace routing, and adherence to design rules and guidelines for spacing, clearance, and other parameters.
- Design Validation: Before manufacturing, perform a thorough design validation to ensure that the layout complies with minimum spacing requirements and other design rules. Use design rule checks (DRC) and design for manufacturability (DFM) analysis tools to identify and resolve any violations.
- Material Selection: Choose PCB materials that are suitable for achieving minimum spacing requirements. High-quality laminate materials with tight dimensional tolerances and excellent dielectric properties are essential for maintaining precision in the PCB fabrication process.
- Fabrication Setup: Set up the PCB fabrication process according to the requirements of the design. This includes selecting the appropriate manufacturing equipment, tooling, and processes to achieve tight tolerances and high precision.
- Photolithography: Use advanced photolithography techniques to transfer the PCB design onto the substrate material with high accuracy and resolution. Ensure precise alignment between layers and proper exposure and development of photoresist materials to define the circuit pattern.
- Etching: Employ precise etching processes to selectively remove copper from the substrate, leaving behind the desired traces and features. Control the etching parameters carefully to achieve the required trace widths and spacing while maintaining uniformity and accuracy across the PCB.
- Drilling and Plating: Use high-precision drilling equipment to create holes for vias and component mounting. Ensure that drill sizes and positions meet the minimum spacing requirements specified in the design. After drilling, apply plating processes to create conductive vias and ensure reliable electrical connections between layers.
- Surface Finishing:Apply surface finishes such as HASL, ENIG, or OSP to protect exposed copper surfaces, improve solderability, and enhance the reliability of the PCB. Choose surface finishes that are compatible with minimum spacing requirements and provide the necessary protection against environmental factors.
- Solder Mask Application: Apply solder mask materials over the entire surface of the PCB, leaving openings only for solder pads and vias. Ensure precise registration and coverage of solder mask layers to protect copper traces and prevent solder bridging during assembly.
- Silkscreen Printing: Print component labels, reference designators, and other markings onto the PCB surface using silkscreen printing techniques. Ensure clear and accurate printing to assist with component placement, assembly, and troubleshooting.
- Quality Control and Testing: Perform rigorous quality control and testing throughout the manufacturing process to verify compliance with minimum spacing requirements and other specifications. Conduct visual inspection, electrical testing, and functionality testing to ensure the integrity and reliability of the finished PCBs.
By carefully managing each step of the manufacturing process and utilizing advanced techniques and equipment, manufacturers can produce high-quality minimum spacing PCBs that meet the demanding requirements of modern electronic devices. Collaboration between PCB designers and manufacturers is essential to ensure successful fabrication of minimum spacing PCBs that achieve optimal performance and reliability.
How much should a Minimum Spacing PCB cost?
The cost of manufacturing a minimum spacing PCB can vary widely depending on several factors, including the complexity of the design, the quantity of PCBs ordered, the chosen materials and finishes, the manufacturing processes involved, and the capabilities of the PCB manufacturer. Here are some key factors that can influence the cost:
- Design Complexity: PCBs with dense component layouts, fine-pitch components, and intricate routing may require more advanced manufacturing processes and incur higher costs.
- Material Selection: The choice of PCB substrate material, copper thickness, and surface finish can impact the cost. High-performance materials with tight dimensional tolerances may be more expensive than standard options.
- Manufacturing Processes: Certain manufacturing processes, such as advanced photolithography, precision drilling, and tight-tolerance etching, may require specialized equipment and expertise, leading to higher manufacturing costs.
- Quantity: Economies of scale typically apply, meaning that larger production runs tend to result in lower per-unit costs. Ordering higher quantities of minimum spacing PCBs can help reduce the overall cost per board.
- Lead Time: Expedited manufacturing services often come at a premium cost. Longer lead times may offer more cost-effective options, especially for standard PCB designs.
- Additional Services: Additional services such as design validation, DFM analysis, panelization, and testing may incur extra charges but can help ensure the quality and reliability of the final PCBs.
- Supplier Selection: Different PCB manufacturers may offer varying pricing structures and capabilities. It’s essential to obtain quotes from multiple suppliers and evaluate factors such as quality, reliability, and customer support in addition to cost.
- Shipping and Handling: Consider the cost of shipping and handling, especially for international orders, as this can add to the overall cost of the PCBs.
Given these factors, it’s challenging to provide a specific cost for manufacturing a minimum spacing PCB without more detailed information about the design requirements and production specifications. However, as a rough estimate, the cost of manufacturing a minimum spacing PCB can range from a few dollars to tens or even hundreds of dollars per board, depending on the complexity and volume of the order. It’s advisable to consult with PCB manufacturers to obtain accurate quotes based on the specific project requirements.
What is the Minimum Spacing PCB base material?
The base material for a minimum spacing PCB, like for any other PCB, is typically a laminate composed of a substrate material and a layer of conductive copper foil. The choice of base material is crucial as it directly affects the electrical performance, mechanical strength, and reliability of the PCB. Here are some common base materials used in minimum spacing PCBs:
- FR-4: FR-4 (Flame Retardant 4) is the most widely used substrate material for PCBs due to its excellent overall performance and cost-effectiveness. It is a fiberglass-reinforced epoxy laminate that provides good electrical insulation, mechanical strength, and dimensional stability. FR-4 is suitable for a wide range of applications, including those requiring minimum spacing designs.
- High-Speed Materials: For high-frequency and high-speed applications where signal integrity is critical, specialized laminate materials may be used. These materials, such as PTFE (Polytetrafluoroethylene) or RO4350B, offer low dielectric loss, tight dimensional tolerances, and controlled impedance characteristics, making them suitable for minimum spacing designs in high-speed PCBs.
- Polyimide: Polyimide-based laminates, such as Kapton, are known for their excellent thermal stability and flexibility. They are often used in applications where the PCB needs to withstand high temperatures or undergo bending or flexing. Polyimide materials can be suitable for minimum spacing designs in flexible or rigid-flex PCBs.
- Metal Core Materials: For applications requiring enhanced thermal management, metal core materials such as aluminum or copper-clad laminates may be used. These materials offer superior thermal conductivity compared to traditional FR-4, making them suitable for dissipating heat from high-power components in minimum spacing designs.
- Ceramic: Ceramic substrates, such as alumina (Al2O3) or aluminum nitride (AlN), are used in specialized applications requiring high thermal conductivity, excellent electrical insulation, and stability at extreme temperatures. Ceramic materials can be suitable for minimum spacing designs in high-power RF (radio frequency) or microwave PCBs.
- Flexible Substrates: Flexible substrates, such as polyimide or polyester films, are used in flexible PCBs or rigid-flex PCBs, where the PCB needs to bend or conform to a specific shape. These materials offer flexibility and lightweight properties while still providing electrical insulation and mechanical strength for minimum spacing designs.
The choice of base material depends on various factors, including the specific requirements of the application, the desired electrical performance, thermal considerations, and cost constraints. Designers should carefully select the appropriate base material based on these factors to ensure the successful fabrication and performance of minimum spacing PCBs.
Which company makes Minimum Spacing PCBs?
Many companies are capable of manufacturing Minimum Spacing PCBs, depending on their manufacturing capabilities, technological expertise, and equipment facilities. Well-known PCB manufacturers include international giants like Foxconn, Flex, and Lite-On, as well as smaller and medium-sized PCB firms worldwide. These companies typically possess advanced production lines, experienced technical teams, and stringent quality control systems to meet customers’ demands for Minimum Spacing PCBs.
As a PCB manufacturer, our company also has the capability to produce Minimum Spacing PCBs, with the following strengths and capabilities:
- Advanced production equipment:We have state-of-the-art PCB manufacturing equipment and process technologies, including precision lithography machines, high-precision drilling equipment, and precise chemical etching machines, enabling us to achieve high accuracy and quality in PCB manufacturing.
- Professional technical team:Our company has an experienced technical team, including engineers, technicians, and quality control personnel, who can provide professional technical support and services to ensure that PCB designs meet customers’ requirements and standards.
- Strict quality control:We have established a strict quality management system, from raw material procurement to production manufacturing, process control, and final inspection, all under strict monitoring and control to ensure stable and reliable PCB quality.
- Customized services for customers:We can customize PCB designs according to customers’ needs and requirements, providing corresponding technical support and solutions to meet various application demands.
In summary, our company has the capability and experience to produce Minimum Spacing PCBs, and we are committed to providing customers with high-quality, reliable PCB products and services. We will continue to improve and enhance our manufacturing capabilities and technical expertise to meet customers’ growing demands and challenges.
What are the 7 qualities of good customer service?
Good customer service is characterized by several key qualities that contribute to a positive experience for customers. Here are seven qualities:
- Responsiveness: Good customer service involves promptly addressing customers’ inquiries, concerns, and requests. Being responsive shows customers that their needs are valued and that the company is committed to providing timely assistance.
- Empathy: Empathy is the ability to understand and share the feelings of others. Good customer service representatives demonstrate empathy by listening attentively to customers’ concerns, showing understanding of their perspectives, and expressing genuine concern for their well-being.
- Professionalism: Professionalism encompasses a range of behaviors, including courtesy, respectfulness, and competence. Good customer service representatives maintain a professional demeanor at all times, treating customers with respect and courtesy while demonstrating expertise in their field.
- Knowledgeability: Customers expect to receive accurate and helpful information from customer service representatives. Good customer service involves having a thorough understanding of the company’s products or services, policies, procedures, and industry standards, allowing representatives to effectively address customers’ questions and concerns.
- Adaptability: Every customer interaction is unique, and good customer service requires adaptability to respond effectively to diverse situations and customer preferences. Customer service representatives should be flexible and open-minded, willing to adjust their approach to meet the needs of each individual customer.
- Problem-solving skills: Good customer service involves effectively resolving customers’ issues and complaints in a timely and satisfactory manner. Customer service representatives should be skilled problem-solvers, capable of analyzing situations, identifying root causes of problems, and implementing appropriate solutions to achieve resolution.
- Follow-up and follow-through: Good customer service doesn’t end with the resolution of a customer’s immediate issue. It also involves following up with customers to ensure their satisfaction, addressing any additional concerns that may arise, and following through on any promises or commitments made during the interaction.
By embodying these qualities, companies can cultivate strong relationships with their customers, foster loyalty and trust, and differentiate themselves in the marketplace based on the quality of their customer service.
FAQs
What is a Minimum Spacing PCB?
A Minimum Spacing PCB refers to a printed circuit board design where components and traces are placed with the smallest possible distance between them while ensuring the integrity and reliability of the circuit.
Why is minimum spacing important in PCB design?
Minimum spacing is important in PCB design to prevent electrical interference, crosstalk, short circuits, and other issues that can arise when components and traces are too close together. It ensures the reliability and functionality of the circuit.
What factors determine minimum spacing requirements in PCB design?
Minimum spacing requirements in PCB design are determined by factors such as voltage levels, signal integrity requirements, manufacturing capabilities, thermal considerations, and industry standards.
How are minimum spacing guidelines established in PCB design?
Minimum spacing guidelines in PCB design are established based on industry standards, such as IPC-2221, and best practices. Designers consider factors such as trace width, clearance, component sizes, and manufacturing tolerances to determine appropriate spacing requirements.
What are the challenges of designing and manufacturing Minimum Spacing PCBs?
Challenges of designing and manufacturing Minimum Spacing PCBs include ensuring signal integrity, managing thermal issues, maintaining manufacturability, and meeting reliability standards while achieving compact and high-density designs.
What are some design techniques for achieving minimum spacing in PCBs?
Design techniques for achieving minimum spacing in PCBs include careful component placement, optimized routing, use of advanced design software, adherence to design rules, and collaboration with PCB manufacturers.