(MIS)Molded Interconnect Substrate
(MIS)Molded Interconnect Substrate manufacturer, we use the BT materials, ABF materials, r use other high speed and high frequency materials to produce such packaging substrates from 2 layer to 22 layers. Microtrace and small gap.
Molded Interconnect Substrates (MIS) represent a revolutionary advancement in electronic packaging and circuit integration. By seamlessly combining the functions of a printed circuit board (PCB) with a plastic injection-molded structure, MIS offers a host of benefits. Its unique design allows for the direct integration of electronic circuits into a molded plastic substrate, eliminating the need for separate wiring and soldering. This integration results in smaller form factors, reduced weight, and enhanced design flexibility compared to traditional PCBs. MIS finds applications across various industries, including consumer electronics, automotive, medical devices, and wearable technology, where space constraints and aesthetic considerations are paramount. With its ability to simplify assembly processes, reduce costs, and improve overall product performance, MIS represents a significant leap forward in electronic packaging technology.
What is a MIS (Molded Interconnect Substrate)?
A Molded Interconnect Substrate (MIS) is a specialized technology used in electronic packaging and circuit integration. It combines the functionalities of both a printed circuit board (PCB) and a plastic injection-molded component. MIS allows for the integration of electronic circuits directly into a molded plastic structure, enabling smaller form factors, reduced weight, and enhanced design flexibility compared to traditional PCBs.
In MIS, conductive traces are directly formed on the surface of the molded substrate, typically using processes like laser ablation, plating, or conductive ink deposition. This eliminates the need for separate wiring and soldering, reducing assembly time and cost. Additionally, components such as resistors, capacitors, and even integrated circuits (ICs) can be embedded within the substrate, further enhancing miniaturization and simplifying assembly.
MIS finds applications in various industries, including consumer electronics, automotive, medical devices, and wearable technology. Its benefits in terms of size, weight, and design freedom make it particularly suitable for products where space constraints and aesthetics are critical considerations. However, the design and manufacturing of MIS can be more complex than traditional PCBs, requiring specialized expertise and equipment.
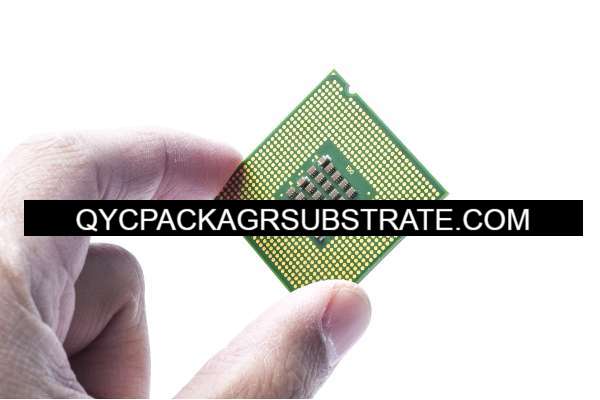
(MIS)Molded Interconnect Substrate
What are the MIS Design Guidelines?
The design guidelines for Molded Interconnect Substrates (MIS) typically include the following aspects:
- Substrate Material Selection: Choose a substrate material suitable for the molding process, typically high-temperature-resistant plastics such as polyimide (PI) or polyamide (PA).
- Conductive Path Design: Design conductive paths considering signal transmission, power dissipation, and circuit layout to ensure good electrical performance and signal integrity.
- Dimensions and Layout: Optimize dimensions and layout to meet the product’s space constraints and design requirements, considering component placement, orientation, and connectivity.
- Component Embedding and Wiring: Determine components that need embedding into the substrate, design appropriate embedding methods, and wiring plans to ensure smooth connectivity and circuit paths.
- Packaging and Protection: Select suitable packaging materials and methods to protect the circuit from environmental factors such as humidity, temperature, and mechanical stress.
- Manufacturability: Consider the manufacturability of the design, including the feasibility of the molding process, process tolerances, and cost-effectiveness.
- Testing and Validation:Plan testing and validation processes to ensure the design meets specification requirements, and perform necessary revisions and optimizations.
These guidelines help engineers and designers formulate appropriate design strategies for MIS projects, ensuring the performance, reliability, and production efficiency of the final product.
What is the MIS Fabrication Process?
The fabrication process for Molded Interconnect Substrates (MIS) typically involves several key steps:
- Substrate Preparation: The process begins with preparing the substrate material, which is usually a thermoplastic polymer such as polyimide (PI) or polyamide (PA). The substrate may be in the form of sheets or pre-molded structures depending on the specific requirements of the design.
- Surface Preparation: The surface of the substrate is prepared for circuit patterning. This may involve cleaning, surface treatment, and application of adhesion promoters to ensure proper adhesion of the conductive traces.
- Circuit Patterning: Conductive traces are patterned onto the substrate surface using techniques such as laser ablation, screen printing, or photolithography. This step defines the electrical pathways and interconnections of the circuit.
- Plating: After patterning, the substrate may undergo a plating process to enhance the conductivity and durability of the conductive traces. This involves depositing a thin layer of metal, such as copper, onto the substrate surface.
- Component Embedding: Components such as resistors, capacitors, and integrated circuits (ICs) may be embedded directly into the substrate during the molding process. This integration reduces the need for separate components and simplifies assembly.
- Molding: The substrate with the patterned conductive traces and embedded components is then placed into a mold cavity. Molten thermoplastic material is injected into the mold, encapsulating the substrate and forming the final molded structure.
- Curing and Cooling: The molded substrate undergoes a curing process to solidify the thermoplastic material and bond it to the conductive traces. After curing, the substrate is cooled to room temperature.
- Post-Processing: After molding, additional processes such as laser trimming, surface finishing, and inspection may be performed to ensure the final MIS meets quality and performance requirements.
- Testing and Validation: The finished MIS undergoes rigorous testing and validation to verify its electrical performance, mechanical integrity, and reliability.
Overall, the fabrication process for MIS combines aspects of traditional printed circuit board (PCB) manufacturing with plastic injection molding techniques, enabling the integration of electronic circuits into complex three-dimensional structures with high precision and reliability.
How do you manufacture a MIS?
Manufacturing a Molded Interconnect Substrate (MIS) involves several steps, combining aspects of traditional printed circuit board (PCB) manufacturing with plastic injection molding techniques. Here’s an overview of the manufacturing process:
- Substrate Preparation: The process begins with preparing the substrate material, typically a thermoplastic polymer such as polyimide (PI) or polyamide (PA). The substrate material may come in the form of sheets or pre-molded structures.
- Surface Preparation: The surface of the substrate is prepared for circuit patterning. This involves cleaning and possibly treating the surface to ensure proper adhesion of the conductive traces.
- Circuit Patterning: Conductive traces are patterned onto the substrate surface using techniques such as laser ablation, screen printing, or photolithography. This step defines the electrical pathways and interconnections of the circuit.
- Plating: After patterning, the substrate may undergo a plating process to enhance the conductivity and durability of the conductive traces. A thin layer of metal, typically copper, is deposited onto the substrate surface.
- Component Embedding: Components such as resistors, capacitors, and integrated circuits (ICs) may be embedded directly into the substrate during the molding process. This integration reduces the need for separate components and simplifies assembly.
- Molding: The prepared substrate with the patterned conductive traces and embedded components is placed into a mold cavity. Molten thermoplastic material is injected into the mold, encapsulating the substrate and forming the final molded structure.
- Curing and Cooling: The molded substrate undergoes a curing process to solidify the thermoplastic material and bond it to the conductive traces. After curing, the substrate is cooled to room temperature.
- Post-Processing: Additional processes such as laser trimming, surface finishing, and inspection may be performed after molding to ensure the final MIS meets quality and performance requirements.
- Testing and Validation: The finished MIS undergoes rigorous testing and validation to verify its electrical performance, mechanical integrity, and reliability.
Throughout the manufacturing process, strict quality control measures are implemented to ensure the consistency and reliability of the final MIS products. Collaboration between engineers, designers, and manufacturing experts is essential to optimize the process and meet the specific requirements of each application.
How much should a MIS cost?
The cost of a Molded Interconnect Substrate (MIS) can vary widely depending on several factors:
- Materials: The cost of the substrate material, conductive traces, embedded components, and any additional materials used in the manufacturing process will impact the overall cost.
- Manufacturing Process: The complexity of the manufacturing process, including circuit patterning, plating, molding, and post-processing steps, will affect the cost. More intricate designs and tighter tolerances may require specialized equipment and labor, increasing production costs.
- Volume: The volume of MIS units being produced can significantly impact the cost per unit. Higher volumes typically result in economies of scale, with lower per-unit manufacturing costs due to optimized production processes and material purchasing power.
- Design Complexity: The complexity of the MIS design, including the number of layers, density of circuitry, and integration of embedded components, will influence manufacturing costs. More complex designs may require additional process steps and quality control measures.
- Quality and Certification Requirements: Meeting specific quality standards and certifications, such as ISO standards or industry-specific regulations, may add additional costs to the manufacturing process.
- Supplier and Location: The choice of supplier and manufacturing location can also affect the cost of MIS production. Labor costs, overhead expenses, and logistical factors can vary depending on the supplier’s location and capabilities.
Overall, it is challenging to provide a specific cost estimate for an MIS without knowing the specific requirements of the project, including the design complexity, materials, volume, and quality standards. It’s essential to work closely with manufacturers and suppliers to obtain accurate cost estimates tailored to the project’s needs.
What is MIS base material?
The base material used in Molded Interconnect Substrates (MIS) typically consists of thermoplastic polymers that are suitable for injection molding processes. Some common materials used as MIS base materials include:
- Polyimide (PI): PI is a high-performance thermoplastic known for its excellent thermal stability, chemical resistance, and mechanical strength. It is often used in applications requiring high temperature and harsh environment operation.
- Polyamide (PA): PA, also known as nylon, is a versatile thermoplastic with good mechanical properties and chemical resistance. It is commonly used in various industries for its durability and ease of processing.
- Liquid Crystal Polymer (LCP): LCP is a specialized thermoplastic known for its outstanding electrical properties, dimensional stability, and chemical resistance. It is often used in high-frequency and high-speed applications.
- Polycarbonate (PC): PC is a widely used thermoplastic known for its excellent impact resistance, optical clarity, and dimensional stability. It is commonly used in consumer electronics and automotive applications.
These base materials provide the structural foundation for the MIS and serve as the substrate onto which conductive traces are patterned. The choice of base material depends on factors such as thermal requirements, mechanical properties, chemical resistance, and cost considerations specific to the application requirements.
Which company makes MIS?
Several companies manufacture Molded Interconnect Substrates (MIS), including Mitsubishi Chemical and Panasonic from Japan, as well as MacDermid Alpha from the United States. These companies possess extensive experience and technical expertise in the electronics industry, offering various types of MIS products to meet diverse application requirements.
As for our company, we are also a professional electronic manufacturing enterprise with advanced production equipment and a skilled technical team capable of providing high-quality MIS solutions. We have rich experience in MIS manufacturing and prioritize product quality, innovation, and customer satisfaction.
Our production capabilities and strengths include:
- Technical Expertise: We have a professional research and development team and engineering team capable of designing and manufacturing customized MIS products to meet customer requirements.
- Production Equipment: Equipped with advanced production equipment and process technology, we can achieve high-efficiency, high-precision production to ensure product quality and stability.
- Quality Management: We strictly adhere to quality management systems, conducting full-process quality control and testing to ensure that products meet relevant standards and specifications.
- Customer Service: We value communication and cooperation with customers, providing professional technical support, customized services, and after-sales support to meet customer needs and expectations.
Through our efforts and continuous innovation, we can deliver high-quality, reliable MIS products to meet various application requirements in the electronics industry. We are willing to collaborate with customers to drive the development and innovation of electronic technology.
What are the 7 qualities of good customer service?
The seven qualities of good customer service are:
- Responsiveness: Being prompt and timely in addressing customer inquiries, concerns, and requests. Responding to customer needs quickly demonstrates attentiveness and care.
- Empathy: Understanding and empathizing with the customer’s situation, feelings, and perspective. Showing empathy helps build rapport and trust with customers, leading to better relationships.
- Clarity: Communicating clearly and effectively with customers, avoiding jargon or technical language that may confuse them. Providing clear information helps customers understand the solutions or options available to them.
- Professionalism: Maintaining professionalism in all interactions with customers, including being courteous, respectful, and maintaining a positive attitude even in challenging situations. Professionalism builds confidence and reassurance for customers.
- Flexibility: Being adaptable and flexible to accommodate customer needs and preferences. Being willing to explore different solutions or alternatives demonstrates a commitment to customer satisfaction.
- Problem-solving: Effectively addressing and resolving customer issues or complaints in a timely and satisfactory manner. Demonstrating problem-solving skills helps build trust and loyalty with customers.
- Consistency: Providing consistent and reliable customer service experiences across all touchpoints and interactions. Consistency builds trust and confidence in the brand and ensures a positive overall customer experience.
By embodying these qualities, businesses can deliver exceptional customer service that exceeds expectations and fosters long-term customer loyalty.
FAQs
What is a Molded Interconnect Substrate (MIS)?
A Molded Interconnect Substrate (MIS) is a specialized technology used in electronic packaging and circuit integration. It combines the functionalities of both a printed circuit board (PCB) and a plastic injection-molded component.
How does MIS differ from traditional PCBs?
MIS allows for the integration of electronic circuits directly into a molded plastic structure, eliminating the need for separate wiring and soldering. This results in smaller form factors, reduced weight, and enhanced design flexibility compared to traditional PCBs.
What are the advantages of using MIS?
Advantages of MIS include smaller form factors, reduced weight, enhanced design flexibility, simplified assembly, and potential cost savings due to fewer components and assembly steps.
What industries use MIS?
MIS finds applications in various industries, including consumer electronics, automotive, medical devices, wearable technology, and more. Its benefits in terms of size, weight, and design flexibility make it suitable for products where space constraints and aesthetics are critical considerations.
What are the key components of MIS?
The key components of MIS include the substrate material (typically a thermoplastic polymer), conductive traces, embedded components (such as resistors, capacitors, and integrated circuits), and any additional materials used in the manufacturing process.
What is the manufacturing process for MIS?
The manufacturing process for MIS involves substrate preparation, surface preparation, circuit patterning, plating, component embedding, molding, curing and cooling, post-processing, and testing and validation.
What are the design guidelines for MIS?
Design guidelines for MIS include substrate material selection, conductive path design, dimensions and layout optimization, component embedding and wiring, packaging and protection, manufacturability considerations, and testing and validation processes.