Multi cavity substrates manufacturing
Multi Cavity Substrates Manufacturing. Open multiple cavity on the PCB or BGA substrates. Professional Cavity Substrates supplier. we offer Cavity PCBs from 3 layer to 30 layers.
Multi cavity substrates (MCS) are specialized substrates utilized in electronic manufacturing, particularly in high-frequency applications such as wireless communication and radar systems. These substrates feature multiple cavities or compartments designed to accommodate integrated circuits (ICs), passive components, and other electronic devices.
MCS offer several advantages, including efficient use of space, improved signal integrity, and reduced electromagnetic interference (EMI). By physically isolating components within individual cavities, MCS minimize crosstalk and interference, enhancing overall system performance.
Manufactured using advanced fabrication techniques, MCS are typically constructed from materials like ceramic, which offer excellent electrical properties, thermal conductivity, and mechanical stability. The design and layout of MCS can be customized to meet specific application requirements, allowing for optimized performance and reliability in complex electronic systems.
In summary, Multi cavity substrates provide a versatile platform for integrating multiple electronic components, enabling the development of high-performance devices in various fields of electronics.
What are Multi cavity substrates (MCS)?
Multi cavity substrates manufacturing. the Package Substrate will be made with Showa Denko and Ajinomoto High speed materials.or other types high speed materials and high frequency materials.
Multi cavity substrates (MCS) are specialized substrates used in electronics manufacturing, particularly in the field of microwave and RF (radio frequency) applications. These substrates are designed to accommodate multiple integrated circuits (ICs) or other components within individual cavities or compartments on the same substrate.
The primary purpose of multi-cavity substrates is to enable the integration of various components or circuits while maintaining isolation between them. This isolation is crucial in applications where interference between components can degrade performance or cause malfunctions. By physically separating components into individual cavities, MCS helps to minimize interference and improve overall system performance.
Multi-cavity substrates are commonly used in the development of high-frequency circuits, such as those found in wireless communication systems, radar systems, and microwave devices. They provide a compact and efficient means of integrating multiple components while maintaining signal integrity and minimizing losses.
The design and fabrication of multi-cavity substrates involve precise machining and layering techniques to create the necessary cavities and isolation structures. Different materials may be used depending on the specific requirements of the application, such as ceramic substrates for high-frequency applications or specialized polymers for cost-effective solutions.
Overall, multi-cavity substrates play a critical role in the development of advanced electronic systems by providing a platform for integrating multiple components with minimal interference, thereby enhancing performance and reliability.
What are the MCS Design Guidelines?
Designing multi-cavity substrates (MCS) involves several guidelines to ensure optimal performance and functionality. Here are some MCS design guidelines:
- Cavity Size and Shape: Cavities should be designed to accommodate the size and shape of the components they will contain. Proper sizing prevents overcrowding and ensures adequate spacing for components.
- Isolation: Each cavity should be properly isolated from adjacent cavities to prevent interference between components. This can be achieved through the use of isolation walls or layers within the substrate.
- Dielectric Properties: The dielectric properties of the substrate material should be carefully considered to minimize signal loss and interference. Low-loss dielectric materials are often preferred for high-frequency applications.
- Material Selection: Choose substrate materials suitable for the specific application requirements, considering factors such as dielectric constant, thermal conductivity, and mechanical strength.
- Grounding and Shielding: Proper grounding and shielding techniques should be implemented to minimize electromagnetic interference (EMI) and ensure signal integrity.
- Heat Dissipation: Ensure effective heat dissipation from components within the cavities to prevent overheating and maintain performance reliability.
- Routing and Interconnects: Plan the routing of interconnects between components to minimize signal distortion and loss. Use impedance-controlled traces for high-frequency signals.
- Manufacturability: Consider the manufacturability of the design, including factors such as fabrication techniques, cost, and scalability.
- Testing and Validation: Develop testing procedures to validate the performance of the MCS design, including electrical testing for signal integrity and functional testing under operating conditions.
- Feedback and Iteration: Gather feedback from testing and real-world usage to identify areas for improvement and iterate on the design as needed.
By adhering to these MCS design guidelines, engineers can develop substrates that meet the requirements of high-frequency applications while ensuring optimal performance, reliability, and manufacturability.
What is the MCS Fabrication Process?
The fabrication process for multi-cavity substrates (MCS) involves several steps to create the necessary cavities, interconnects, and other features required for integrating components. Here is an overview of the typical MCS fabrication process:
- Substrate Selection: Choose a suitable substrate material based on the specific application requirements, such as high-frequency performance, thermal conductivity, and mechanical strength. Common substrate materials include ceramics, glass, and specialized polymers.
- Substrate Preparation: Prepare the substrate surface by cleaning and treating it to ensure proper adhesion of subsequent layers and features.
- Layer Deposition: Deposit thin film layers onto the substrate using techniques such as sputtering, chemical vapor deposition (CVD), or physical vapor deposition (PVD). These layers may include conductive materials for interconnects, dielectric materials for insulation, and metalization for grounding and shielding.
- Pattern Definition: Define the desired patterns for cavities, interconnects, and other features using photolithography or other patterning techniques. Photomasks are used to transfer the pattern onto the substrate surface.
- Etching: Use wet or dry etching processes to selectively remove material from the substrate surface according to the defined patterns. This step creates the cavities and features necessary for component integration.
- Dielectric Layer Deposition: Deposit dielectric layers onto the substrate surface to insulate the cavities and provide isolation between components. These dielectric layers help minimize interference and signal loss.
- Conductor Deposition: Deposit additional layers of conductive materials onto the substrate surface to create interconnects, grounding planes, and shielding structures. These conductive layers may be patterned using photolithography and etching processes.
- Assembly and Integration: Mount components such as integrated circuits (ICs), passive components, and other devices into the cavities on the substrate surface. Use techniques such as flip-chip bonding, wire bonding, or soldering for component attachment.
- Testing and Quality Assurance: Perform electrical testing and quality assurance checks to verify the functionality and performance of the fabricated MCS. This may include continuity testing, impedance measurements, and functional testing under operating conditions.
- Packaging and Encapsulation: Optionally, encapsulate the MCS in a protective housing or package to provide mechanical stability, environmental protection, and enhanced reliability.
By following these steps, manufacturers can fabricate multi-cavity substrates suitable for high-frequency applications, such as RF and microwave systems, with optimized performance, reliability, and manufacturability.
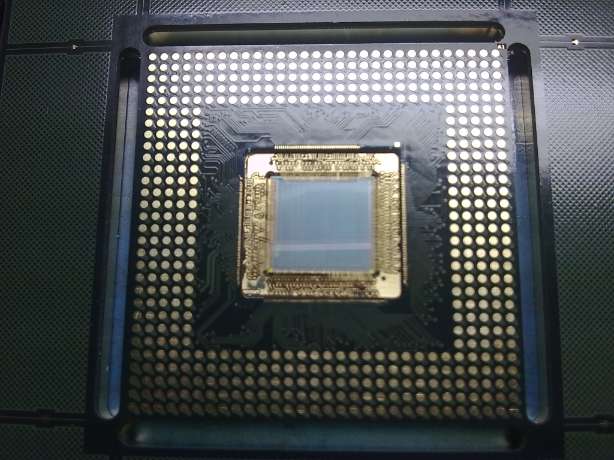
Multi cavity substrates
How do you manufacture MCS?
Manufacturing multi-cavity substrates (MCS) involves a series of intricate processes aimed at creating the necessary cavities and features to accommodate components while ensuring optimal performance and reliability. Here’s an overview of the typical manufacturing steps for MCS:
- Substrate Selection: Choose a suitable substrate material based on the specific requirements of the application. Common substrate materials include ceramics (e.g., alumina, aluminum nitride), glass, and specialized polymers. The choice depends on factors such as dielectric properties, thermal conductivity, mechanical strength, and cost.
- Substrate Preparation: Prepare the substrate surface by cleaning it thoroughly to remove any contaminants and ensure proper adhesion of subsequent layers. Surface treatment techniques may include chemical cleaning, plasma treatment, or mechanical polishing.
- Layer Deposition:
– Conductive Layers: Deposit thin film layers of conductive materials, such as copper or gold, onto the substrate surface using techniques like sputtering, evaporation, or electroplating. These layers will form the interconnects, grounding planes, and signal traces.
– Dielectric Layers: Deposit dielectric materials, such as silicon dioxide or polyimide, to insulate the conductive layers and provide electrical isolation between components. Dielectric layers are typically applied using methods like spin coating, chemical vapor deposition (CVD), or screen printing.
- Lithography and Etching:
– Photolithography: Apply a photoresist layer onto the substrate surface and use photomasks to define the desired patterns for cavities, interconnects, and other features.
– Etching: Use wet or dry etching processes to selectively remove material from the substrate surface based on the patterns defined by photolithography. This step creates the cavities and exposes the conductive traces and pads.
- Cavity Formation: Use precision machining techniques such as milling, drilling, or laser ablation to create the cavities within the substrate. The dimensions and shapes of the cavities should be designed to accommodate the components while ensuring proper alignment and spacing.
- Component Integration:
– Mount the components, such as integrated circuits (ICs), discrete devices, and passive components, into the cavities on the substrate surface. Techniques like flip-chip bonding, wire bonding, or soldering may be used for component attachment.
– Ensure proper alignment and connection of the components to the conductive traces and pads within the cavities.
- Quality Control and Testing:
– Perform rigorous quality control checks throughout the manufacturing process to ensure consistency and reliability.
– Conduct electrical testing and functional verification to validate the performance of the fabricated MCS. This may include continuity testing, impedance measurements, and functional testing under simulated operating conditions.
- Packaging and Encapsulation: Optionally, encapsulate the MCS in protective housing or package to provide mechanical stability, environmental protection, and enhanced reliability. This step may involve sealing the substrate in epoxy resin or other encapsulation materials.
- Final Inspection and Packaging: Conduct a final inspection to ensure compliance with specifications and customer requirements. Package the finished MCS products according to industry standards for storage, shipping, and handling.
By following these manufacturing steps with precision and attention to detail, manufacturers can produce high-quality multi-cavity substrates tailored to the needs of various high-frequency electronic applications.
How much should an MCS cost?
The cost of manufacturing multi-cavity substrates (MCS) can vary significantly depending on several factors, including the complexity of the design, substrate material, manufacturing processes involved, component integration, quality requirements, and volume of production. Here are some key factors that influence the cost of MCS:
- Design Complexity: The complexity of the MCS design, including the number and size of cavities, intricacy of interconnects, and features required for component integration, directly impacts the manufacturing cost. More complex designs may require additional fabrication steps and resources, leading to higher costs.
- Substrate Material: The choice of substrate material plays a significant role in determining the cost of MCS. Materials like high-performance ceramics or specialized polymers with specific dielectric properties may be more expensive compared to standard substrate materials like FR-4.
- Manufacturing Processes: The fabrication processes involved in MCS production, such as layer deposition, lithography, etching, and component integration, contribute to the overall manufacturing cost. Advanced manufacturing techniques and equipment may increase production costs but can also improve efficiency and quality.
- Component Integration: The cost of integrating components into the MCS, including assembly techniques like flip-chip bonding, wire bonding, or soldering, can affect the overall manufacturing cost. More complex integration processes may require specialized equipment and skilled labor, leading to higher costs.
- Quality Requirements: Meeting stringent quality standards and reliability requirements may entail additional costs for quality control measures, testing, and inspection throughout the manufacturing process.
- Volume of Production: Economies of scale play a significant role in determining the cost of MCS. Higher volumes of production generally lead to lower per-unit manufacturing costs due to efficiencies in materials procurement, labor utilization, and equipment utilization.
- Supplier and Location: The choice of suppliers and manufacturing facilities can influence the cost of MCS. Factors such as labor costs, overhead expenses, and geographical location may impact production costs.
It’s challenging to provide a specific cost estimate for MCS without detailed information about the design requirements and production parameters. Typically, manufacturers will provide quotes based on the specific project specifications, including the design complexity, materials, and volume of production. Collaborating with a reputable manufacturer and providing clear project requirements can help determine the most cost-effective solution for producing MCS.
What is the MCS base material?
The choice of base material for multi-cavity substrates (MCS) depends on various factors such as the specific application requirements, desired electrical properties, thermal considerations, mechanical strength, and cost constraints. Several materials are commonly used as the base substrate for MCS fabrication. Some of the most frequently utilized materials include:
- Ceramics: Ceramics such as alumina (Al2O3) and aluminum nitride (AlN) are popular choices for high-frequency applications due to their excellent electrical insulation properties, high thermal conductivity, and mechanical stability. Alumina is often preferred for its relatively low cost, while aluminum nitride offers superior thermal conductivity.
- Glass: Glass substrates are used in certain MCS applications, particularly in microelectromechanical systems (MEMS) and bioelectronics. Glass offers excellent optical transparency, chemical resistance, and biocompatibility, making it suitable for specific applications where these properties are essential.
- Polyimide: Polyimide-based substrates are flexible and lightweight, making them suitable for applications requiring conformal and bendable substrates. Polyimide offers good thermal stability, chemical resistance, and low dielectric loss, making it suitable for flexible electronics and certain high-frequency applications.
- Rigid-Flex PCBs: In some cases, rigid-flex PCBs (Printed Circuit Boards) are used as the base material for MCS. These substrates combine rigid and flexible layers, allowing for the integration of components in both rigid and flexible regions. Rigid-flex PCBs offer advantages in terms of space-saving, weight reduction, and improved reliability.
- Specialized Polymers: Certain specialized polymers, such as liquid crystal polymers (LCPs), liquid crystal elastomers (LCEs), and other advanced engineering plastics, are used in MCS fabrication for specific applications requiring unique material properties such as low dielectric loss, high-temperature stability, or biocompatibility.
The selection of the MCS base material depends on balancing the desired electrical, thermal, and mechanical properties with cost considerations and manufacturability. Each material has its advantages and limitations, and the choice depends on the specific requirements of the application and the performance characteristics needed for the MCS.
Which company manufactures Multi cavity substrates?
There are several companies that manufacture Multi cavity substrates (MCS), some of which include Murata Manufacturing Co., Ltd., Kyocera Corporation, and Rogers Corporation. These companies possess advanced technologies and facilities capable of producing high-quality MCS to meet various needs across different fields, including wireless communication, radar systems, medical devices, and more.
As a company dedicated to electronic manufacturing, we also have the capability to produce Multi cavity substrates. We have advanced production equipment and a skilled technical team capable of customizing MCS according to the requirements of our customers, including design, manufacturing, and assembly processes. Our production process is strictly managed according to quality management systems to ensure stable and reliable product quality.
Our Multi cavity substrates are made from high-quality materials such as ceramic substrates or high-performance polymers, offering excellent electrical characteristics, thermal conductivity, and mechanical strength suitable for various high-frequency applications. We can also customize MCS in different sizes, shapes, and configurations to meet specific application requirements.
In addition to producing high-quality Multi cavity substrates, we also provide excellent customer service. Our team works closely with customers to understand their needs and provide customized solutions. We prioritize communication and feedback with customers, continuously improving and optimizing our products to ensure customer satisfaction and foster long-term partnerships.
In summary, our company has the technology, equipment, and team necessary to produce Multi cavity substrates, and we are committed to providing high-quality customized products and excellent customer service to meet the needs of our customers and achieve mutual development.
Qualities of Good Customer Service
Good customer service is characterized by several key qualities that contribute to positive interactions and relationships between businesses and their customers. Here are some qualities of good customer service:
- Responsive: Good customer service is responsive to customer inquiries, concerns, and feedback in a timely manner. This includes promptly answering phone calls, emails, and messages, as well as addressing customer needs in real-time during face-to-face interactions.
- Empathetic: Empathy is essential in understanding and relating to customers’ feelings, concerns, and frustrations. Good customer service representatives demonstrate empathy by actively listening to customers, acknowledging their emotions, and showing genuine care and concern.
- Knowledgeable: Customer service representatives should possess a thorough understanding of the products or services offered by the business. They should be able to provide accurate information, answer questions, and offer relevant advice or recommendations to help customers make informed decisions.
- Professionalism: Professionalism entails maintaining a courteous and respectful demeanor when interacting with customers, regardless of the situation. This includes using appropriate language, tone, and body language, as well as following company policies and procedures.
- Problem-Solving Skills: Good customer service involves effectively addressing customer concerns and resolving issues in a satisfactory manner. Customer service representatives should be equipped with problem-solving skills to identify root causes, propose solutions, and follow through until the issue is resolved.
- Adaptability: Every customer interaction is unique, and good customer service requires adaptability to meet the diverse needs and preferences of customers. This may involve adjusting communication styles, accommodating special requests, or finding creative solutions to unexpected challenges.
- Consistency: Consistency is key to building trust and reliability with customers. Good customer service should be consistent across all channels and interactions, ensuring that customers receive the same level of service regardless of the platform or representative they engage with.
- Follow-Up: Following up with customers after their initial interaction demonstrates a commitment to their satisfaction and provides an opportunity to address any lingering concerns or feedback. Good customer service involves proactive follow-up to ensure that customers’ needs have been met and that they are satisfied with the resolution.
- Respect for Privacy: Customer service representatives should respect customers’ privacy and confidentiality by handling their personal information with care and only using it for its intended purpose. This includes complying with data protection regulations and safeguarding sensitive information from unauthorized access or disclosure.
- Continuous Improvement: Good customer service is a continuous process of learning and improvement. Businesses should actively solicit feedback from customers, analyze trends and patterns, and implement changes to enhance the customer experience over time.
By embodying these qualities, businesses can foster positive relationships with their customers, improve customer satisfaction and loyalty, and differentiate themselves in a competitive marketplace.
FAQs (Frequently Asked Questions)
What are the lead times for MCS production?
Lead times vary depending on project complexity and volume. Contact our sales team for specific lead time estimates.
Can you provide design assistance for MCS projects?
Yes, we offer design support to help optimize MCS layouts for performance and manufacturability.
What surface finishes do you offer for MCS?
We offer a range of surface finishes including HASL (Hot Air Solder Leveling), ENIG (Electroless Nickel Immersion Gold), and OSP (Organic Solderability Preservatives).
Do you offer expedited manufacturing services for urgent projects?
Yes, we provide expedited manufacturing options for projects with tight deadlines. Contact us for more information and availability.