Probe Card Substrate Manufacturer
Probe Card Substrate Manufacturer,A Probe Card Substrate is a critical component in semiconductor testing, designed to interface with semiconductor devices during electrical testing. It features an array of fine-pitch electrical contacts that align with the device’s test points, allowing for precise measurement of electrical characteristics. Made from high-quality materials to ensure durability and accuracy, the probe card substrate supports reliable signal transmission and minimal signal loss. It often incorporates advanced technologies to handle high frequencies and complex test requirements. Used extensively in wafer testing and device validation, the probe card substrate is essential for ensuring the performance and quality of semiconductor products before they are packaged and deployed.
What is a Probe Card Substrate?
A probe card substrate is a crucial component in the semiconductor testing process, used to interface between the test equipment and the semiconductor device under test (DUT). It acts as a bridge that allows electrical signals to be transmitted between the test system and the semiconductor chip.
Typically, a probe card consists of several key parts: the probe card substrate itself, which provides the structural support and electrical pathways; the probe tips, which make contact with the DUT; and the connectors and circuits that link the probe card to the testing equipment. The substrate is made from materials that offer good electrical insulation and thermal stability, ensuring accurate test results and reliable performance.
The design of the probe card substrate is critical as it must handle high-frequency signals and maintain signal integrity. It often involves advanced materials and manufacturing techniques to achieve the necessary performance. High-frequency and high-density interconnections are common in these substrates to accommodate the complex demands of modern semiconductor testing.
In summary, the probe card substrate is an integral element of the testing infrastructure in semiconductor manufacturing. Its role in ensuring precise and reliable electrical connections between the test equipment and the DUT is essential for validating the performance and quality of semiconductor devices.
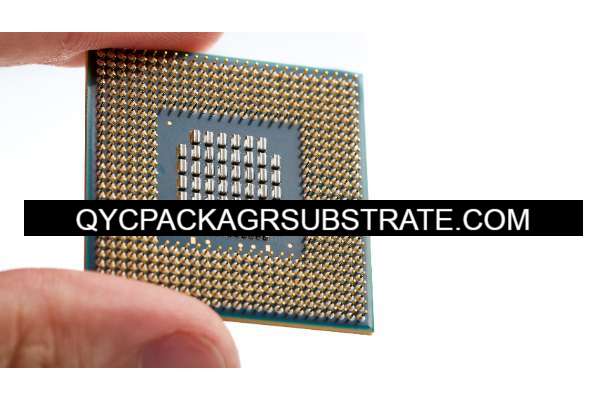
Probe Card Substrate Manufacturer
What are the Probe Card Substrate Design Guidelines?
Designing a probe card substrate involves several guidelines to ensure reliability, signal integrity, and overall performance. Here are key design guidelines for probe card substrates:
- Material Selection: Choose high-quality materials with excellent electrical insulation, thermal stability, and mechanical strength. Common materials include FR4, Rogers, or advanced ceramics, depending on the application’s frequency and temperature requirements.
- Thermal Management: Ensure effective heat dissipation to prevent thermal-induced errors. Include heat sinks or thermal vias to manage heat generated during testing.
- Signal Integrity: Design the substrate to minimize signal loss and interference. Use high-frequency laminates and ensure proper impedance matching to maintain signal integrity, especially for high-speed applications.
- Trace Design: Keep traces short and direct to reduce inductance and resistance. Use wider traces and thicker copper layers to handle higher currents and reduce resistance.
- Grounding and Shielding: Implement robust grounding techniques to minimize noise and crosstalk. Include ground planes and shielding to protect sensitive signals.
- Via and Hole Design: Minimize the use of vias and ensure they are properly plated and insulated. Use high-quality via fill and plating processes to maintain signal integrity and reliability.
- Mechanical Stability: Ensure the substrate has adequate mechanical support to handle the stresses of probing and alignment. Design for stability during operation and testing.
- Alignment and Mounting: Design precise alignment features for accurate probe placement and ensure proper mounting and support mechanisms.
- Testing and Validation: Include test points and validation procedures in the design to verify performance and reliability before deployment.
- Manufacturability: Consider manufacturability aspects, including ease of fabrication, cost, and the capabilities of available production technologies.
By adhering to these guidelines, designers can create probe card substrates that perform reliably and effectively in semiconductor testing applications.
What is the Probe Card Substrate Fabrication Process?
The fabrication process for a probe card substrate involves several detailed steps to ensure high quality and precision. Here’s an overview of the typical fabrication process:
- Material Preparation: Select and prepare the substrate material, which may be FR4, Rogers laminate, or a ceramic material. This involves cutting the material to the desired size and thickness.
- Layer Deposition: Apply conductive layers (such as copper) onto the substrate. This is usually done through a process called lamination, where a thin layer of copper foil is bonded to the substrate material under heat and pressure.
- Photolithography:Coat the substrate with a photosensitive material (photoresist). Use photolithography to expose and develop the photoresist, creating a pattern for the conductive traces. The exposed areas are then etched away, leaving behind the desired circuit pattern.
- Etching: Perform chemical etching to remove the unwanted copper and reveal the conductive traces as per the design. This step requires precise control to ensure accurate trace dimensions and spacing.
- Via Formation: Drill or laser-cut vias into the substrate to create electrical connections between different layers. The vias are then plated with copper or another conductive material to establish electrical pathways.
- Layering and Bonding: If the design involves multiple layers, stack and bond them using adhesive layers. Each layer is aligned carefully, and the stack is laminated under heat and pressure.
- Electroplating: Apply additional layers of metal (often gold or nickel) to the pads and vias through electroplating. This enhances the conductivity and ensures a robust connection for probing.
- Inspection and Testing: Conduct thorough inspections and tests to verify the integrity of the conductive traces, vias, and overall substrate. This may involve optical inspection, electrical testing, and other quality control measures.
- Cutting and Shaping: Trim and shape the substrate to its final dimensions. This can include cutting out the probe card shape and any necessary mounting features.
- Assembly: Attach probe tips and connectors to the substrate. This step involves precise alignment and secure attachment to ensure proper contact with the semiconductor device.
- Final Testing: Perform final testing of the completed probe card to verify that all electrical connections are correct and that the probe card meets performance specifications.
- Packaging: Package the finished probe card substrate to protect it during shipping and handling.
This fabrication process ensures that the probe card substrate meets the stringent requirements for accuracy, reliability, and performance in semiconductor testing applications.
How Do You Manufacture a Probe Card Substrate?
Manufacturing a probe card substrate involves several detailed steps to ensure high precision and performance. Here’s a step-by-step overview of the process:
- Material Selection: Begin by selecting appropriate substrate materials, such as FR4, Rogers, or advanced ceramics, depending on the specific requirements for electrical performance and thermal management.
- Material Preparation: Cut the selected materials into the required sizes for the probe card substrate. Ensure the materials are clean and free from contaminants to maintain quality during subsequent processing.
- Layer Lamination: For multi-layer substrates, laminate the layers together. This involves applying adhesive and using a laminating press to bond the layers under heat and pressure. Ensure that the layers are aligned precisely to avoid misalignment.
- Patterning: Apply a photosensitive photoresist layer to the substrate. Use photolithography to expose the resist to UV light through a mask that defines the desired circuit patterns. Develop the resist to reveal the patterns for etching.
- Etching: Perform etching to remove excess copper from the exposed areas, creating the circuit patterns. This can be done using chemical etching or plasma etching methods. Ensure accurate and clean removal to avoid defects.
- 6. Via Drilling and Plating: Drill or laser-cut vias in the substrate where inter-layer connections are required. Plate the vias with copper to establish electrical connections between different substrate layers. Ensure proper filling and plating for reliable conductivity.
- Solder Mask Application: Apply a solder mask to protect areas that should not be soldered. This mask helps prevent solder bridging and short circuits, and it also protects the substrate from environmental damage.
- Surface Finishing: Apply surface finishes, such as gold or nickel plating, to areas where electrical contacts are needed. This enhances conductivity and improves the durability of the substrate.
- Assembly of Probe Tips: Attach the probe tips to the substrate. This step requires precise alignment to ensure accurate contact with the device under test (DUT). Use appropriate bonding or mounting techniques to secure the probe tips.
- Integration and Testing: Integrate the probe card substrate with the test system. Conduct rigorous testing to verify performance, including electrical testing, mechanical stability, and alignment checks. Ensure that the probe card functions correctly and meets all design specifications.
- Final Inspection and Quality Assurance: Perform a final inspection to check for any defects or issues. Conduct quality assurance checks to ensure the probe card substrate meets all required standards and specifications.
By following these steps, manufacturers can produce high-quality probe card substrates that are essential for accurate and reliable semiconductor testing.
How Much Should a Probe Card Substrate Cost?
The cost of a probe card substrate can vary widely depending on several factors, including its complexity, material requirements, and manufacturing specifications. Here are some key factors that influence the cost:
- Material: High-frequency materials, advanced ceramics, or other specialized materials can significantly increase costs compared to standard materials like FR4.
- Complexity and Layers: More complex probe card substrates with multiple layers, fine traces, or advanced features will generally be more expensive. Multi-layer substrates or those requiring high precision and intricate designs add to the cost.
- Quantity: The cost per unit often decreases with higher production volumes due to economies of scale. Custom or low-volume orders typically have higher per-unit costs.
- Size and Design: Larger substrates or those with unique design requirements can increase the cost. The complexity of the probe tips and their alignment also impacts the price.
- Fabrication Technology: The choice of fabrication techniques and technologies, such as advanced photolithography, etching, and plating, can affect costs. High-precision or advanced processes generally cost more.
- Testing and Quality Assurance: Comprehensive testing and quality assurance processes can add to the overall cost. Ensuring that the probe card substrate meets all performance and reliability standards may require additional resources.
- Lead Time: Shorter lead times or expedited production can increase costs. Standard production schedules are typically more cost-effective.
On average, probe card substrates can range from a few hundred to several thousand dollars per unit. Basic substrates might cost around $500 to $1,000, while more complex or high-performance designs could exceed $3,000 or more per unit. For precise quotes, it’s best to consult with manufacturers and provide detailed specifications for the probe card substrate.
What is Probe Card Substrate Base Material?
The base material of a probe card substrate is the foundational layer that provides structural support and electrical properties for the probe card. The choice of base material affects the performance, reliability, and cost of the probe card. Here are some common base materials used:
- FR4 (Fiberglass-Reinforced Epoxy): This is a widely used, cost-effective material for many probe card substrates. It offers good electrical insulation and mechanical strength but may not be suitable for high-frequency applications due to its relatively high dielectric loss.
- High-Frequency Laminates: Materials such as Rogers or Taconic laminates are used for applications requiring high-frequency performance. These materials have low dielectric loss and stable electrical properties, making them ideal for high-speed and high-frequency testing.
- Ceramic Substrates: Advanced ceramics like aluminum oxide (Al2O3) or beryllium oxide (BeO) provide excellent thermal conductivity and electrical insulation. They are used in high-power and high-precision applications due to their stability and performance under extreme conditions.
- Polyimide: This material is known for its high thermal stability and flexibility. Polyimide substrates are often used in flexible probe cards or those requiring high-temperature operation.
- Metal-Core Substrates: These substrates have a metal core, such as copper or aluminum, which provides enhanced thermal dissipation. They are used in high-power applications where managing heat is crucial.
- Glass-Polyimide Composites: These combine the mechanical stability of glass with the flexibility of polyimide, offering a balance of performance characteristics for certain probe card designs.
The choice of base material depends on factors such as the required electrical performance, thermal management needs, mechanical stability, and cost considerations. Each material has its advantages and is selected based on the specific requirements of the probe card application.
Which Company Makes Probe Card Substrates?
Several companies specialize in manufacturing probe card substrates, offering a range of materials and designs to meet various testing needs. Here are some notable companies in the probe card substrate market:
- KLA Corporation: KLA is a leading provider of semiconductor equipment and probe card technology, offering high-performance probe card substrates for various semiconductor testing applications.
- Advantest: Advantest provides a variety of probe card solutions, including high-frequency and high-density probe cards, widely used in integrated circuit (IC) testing.
- FormFactor:FormFactor is a globally recognized supplier of probe cards, offering a range of probe card substrates including those for high-frequency and high-power applications.
- MJC Electronics: MJC Electronics specializes in manufacturing high-quality probe card substrates used extensively in semiconductor testing and quality control.
- Technoprobe: Technoprobe offers various probe card solutions, from standard to custom probe card substrates, catering to different testing needs.
- MicroFriend:MicroFriend provides a range of probe card substrates primarily for the semiconductor testing field, known for their precision and reliability.
Our company also manufactures probe card substrates. We have the capability to produce a wide range of probe card substrates, including those for high-frequency, high-density, and high-power applications. Our probe card substrates feature the following:
- High Precision: We use advanced manufacturing processes and equipment to ensure high precision and stability in our probe card substrates, meeting stringent testing requirements.
- Quality Materials: We select high-quality base materials such as high-frequency dielectrics and ceramics to ensure excellent performance under high-frequency and high-power conditions.
- Flexible Design: We offer custom design services based on customer needs, including various layer counts, layouts, and probe configurations to suit different applications.
- Strict Quality Control:We implement rigorous quality control procedures to ensure that every probe card substrate undergoes comprehensive testing and inspection before shipment, guaranteeing performance and reliability.
- Excellent Service: We provide comprehensive technical support and after-sales service to ensure customers receive timely assistance and solutions throughout the usage of our products.
In summary, our company is dedicated to providing high-quality and reliable probe card substrates to meet the diverse needs of customers and offer professional solutions for semiconductor testing.
What are the 7 Qualities of Good Customer Service?
Good customer service is essential for building strong customer relationships and ensuring satisfaction. Here are seven key qualities of excellent customer service:
- Responsiveness: Good customer service means being prompt in addressing customer inquiries, issues, or concerns. Quick responses show customers that their time and needs are valued, helping to resolve problems efficiently and maintain satisfaction.
- Empathy: Empathetic service involves understanding and acknowledging the customer’s feelings and perspectives. Showing empathy helps build rapport, reassures customers, and demonstrates that the service provider genuinely cares about their experience and concerns.
- Knowledgeability: Service representatives should be well-informed about the products, services, and policies of the company. This expertise allows them to provide accurate information, solve problems effectively, and offer valuable advice to customers.
- Patience: Patience is crucial in customer service, especially when dealing with frustrated or confused customers. Taking the time to listen, explain, and address issues thoroughly without rushing or becoming frustrated helps build trust and ensures a positive experience.
- Communication Skills: Clear and effective communication is essential for good customer service. Representatives should be able to convey information clearly, listen actively, and adapt their communication style to the customer’s preferences and needs.
- Consistency: Consistency in service ensures that customers receive the same high level of care and attention every time they interact with the company. Maintaining consistent service standards helps build trust and reliability.
- Problem-Solving Ability: A good customer service representative should be able to quickly identify and address issues, offering practical solutions and alternatives. Effective problem-solving involves not only fixing the immediate issue but also anticipating and addressing potential future concerns.
By embodying these qualities, companies can deliver exceptional customer service that fosters customer loyalty, enhances satisfaction, and contributes to long-term success.
FAQs
What is a probe card substrate?
A probe card substrate is a component used in semiconductor testing to interface between the test equipment and the semiconductor device under test (DUT). It provides the structural and electrical connections necessary to accurately test the DUT.
What materials are commonly used for probe card substrates?
Common materials include FR4 (fiberglass-reinforced epoxy), high-frequency laminates (such as Rogers or Taconic), ceramics (like aluminum oxide or beryllium oxide), and polyimide. The choice of material depends on the performance requirements, such as frequency, thermal management, and mechanical stability.
What factors influence the cost of a probe card substrate?
The cost is influenced by factors such as the complexity of the design, material used, number of layers, size, production volume, and additional features like thermal management or high-frequency performance.
How is a probe card substrate manufactured?
The manufacturing process typically includes material preparation, layer lamination (for multi-layer designs), photolithography to define circuit patterns, etching to create traces, via drilling and plating, solder mask application, surface finishing, probe tip attachment, and final testing.
What are the key design considerations for probe card substrates?
Key design considerations include material selection, thermal management, signal integrity, trace design, grounding and shielding, via and hole design, mechanical stability, alignment, and manufacturability.
What is the role of probe card substrates in semiconductor testing?
Probe card substrates act as a critical interface between the semiconductor test equipment and the DUT. They ensure accurate electrical connections, facilitate signal transmission, and enable reliable testing of the semiconductor devices.
How do probe card substrates differ from other types of substrates, like PCB or IMS?
Probe card substrates are specifically designed for semiconductor testing and typically include high-density interconnections and advanced materials to handle high frequencies and precise alignments. In contrast, standard PCBs (Printed Circuit Boards) are used for general electronic circuit connections, and IMS (Insulated Metal Substrates) are used for thermal management in high-power applications.