Radio Frequency Cavity PCB Manufacturer
Radio Frequency Cavity PCB Manufacturer. we can produce the best samllest bump pitch with 100um, the best smallest trace are 9um. and the smallest gap are 9um. most of the design are 15um to 30um trace and spacing.
Radio Frequency (RF) cavity PCBs are specialized printed circuit boards engineered for high-frequency electronic applications. These PCBs feature a unique cavity structure, meticulously designed to isolate critical RF components and optimize signal integrity. Utilizing advanced materials like Rogers, Taconic, Arlon, or Isola laminates, RF cavity PCBs offer low dielectric loss and consistent electrical properties across a wide frequency spectrum. Their design considerations include precise cavity dimensions, strategic component placement, controlled impedance routing, and effective grounding techniques to minimize signal loss and electromagnetic interference. RF cavity PCBs find extensive use in various high-frequency systems, including radio transmitters, receivers, amplifiers, antennas, radar systems, and wireless communication devices. With their superior performance characteristics and meticulous manufacturing processes involving CNC milling, laser drilling, and specialized copper deposition techniques, RF cavity PCBs deliver reliability, efficiency, and exceptional RF performance for demanding applications in modern electronics.
What is a Radio Frequency Cavity PCB?
A Radio Frequency (RF) cavity PCB (Printed Circuit Board) is a specialized type of PCB designed for applications involving radio frequency signals. RF cavity PCBs are typically used in high-frequency electronic devices such as radio transmitters, receivers, amplifiers, and antennas.
The term “cavity” in RF cavity PCB refers to a specific design feature on the PCB where a portion of the board is hollowed out or contains a cavity. This cavity serves several purposes:
- Resonance: The cavity can be designed to resonate at specific frequencies, which is useful in applications where precise frequency control is required, such as in RF filters and oscillators.
- Isolation: By isolating certain components or signals within the cavity, RF interference and crosstalk can be minimized, improving the overall performance of the RF circuit.
- Impedance Matching:The cavity can be used to create controlled impedance pathways for RF signals, ensuring efficient signal transmission and minimizing signal loss.
RF cavity PCBs require careful design and manufacturing techniques to achieve the desired performance characteristics at high frequencies. They may incorporate specialized materials and fabrication processes to minimize signal loss, maintain impedance consistency, and ensure reliable operation in RF environments.
Overall, RF cavity PCBs play a crucial role in the design and implementation of high-frequency electronic systems, enabling the efficient transmission, reception, and processing of RF signals.
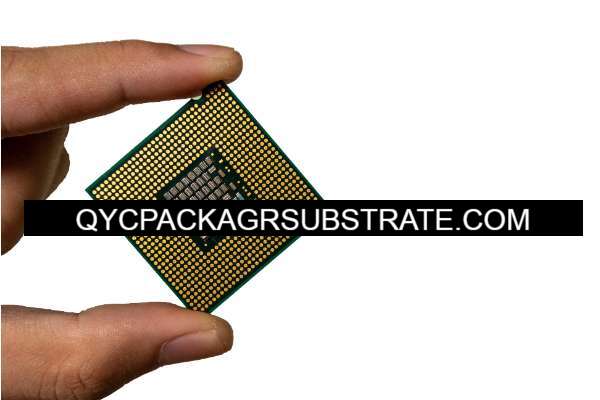
Radio Frequency Cavity PCB Manufacturer
What are the PCB Design Guidelines for Radio Frequency Cavity PCBs?
Designing RF cavity PCBs requires careful consideration of various factors to ensure optimal performance at high frequencies. Here are some important guidelines:
- Cavity Design: The cavity dimensions and shape should be carefully designed to achieve the desired resonant frequency or other performance characteristics. The cavity should be properly shielded to prevent interference from external sources.
- Material Selection: Choose PCB materials with low dielectric loss and consistent electrical properties across a range of frequencies. Common materials for RF cavity PCBs include high-frequency laminates like Rogers, Taconic, or Arlon.
- Component Placement: Place components strategically to minimize signal paths and reduce parasitic capacitance and inductance. Components sensitive to RF interference should be isolated within the cavity to prevent coupling with other signals.
- Grounding: Implement a solid ground plane on the PCB to provide low impedance return paths for RF signals and to reduce ground loops. Ensure that the ground plane is continuous and free from cuts or splits.
- Impedance Matching: Use controlled impedance traces and matching networks to ensure proper impedance matching between components and transmission lines. This helps minimize signal reflections and improves signal integrity.
- Signal Routing: Route RF traces with care to minimize signal loss and interference. Use wide traces for high-frequency signals and maintain consistent trace widths to control impedance. Avoid sharp bends and corners, as they can introduce impedance mismatches and signal degradation.
- Via Placement: Place vias strategically to minimize signal distortion and impedance changes. Use through-hole vias or backdrilling techniques to maintain signal integrity and minimize signal reflections.
- Shielding: Incorporate shielding techniques such as grounded metal enclosures or copper shielding layers to isolate sensitive RF components and prevent external interference.
- EMC Considerations: Design the PCB with electromagnetic compatibility (EMC) in mind to ensure compliance with regulatory standards and minimize electromagnetic interference (EMI) emissions.
- Simulation and Testing: Use RF simulation tools to verify the performance of the design before fabrication. Perform thorough testing, including impedance measurements, S-parameter analysis, and RF testing, to validate the design and ensure it meets the required specifications.
By following these guidelines, designers can create RF cavity PCBs that meet the stringent requirements of high-frequency applications, ensuring optimal performance and reliability.
What is the Radio Frequency Cavity PCB Fabrication Process?
The fabrication process for Radio Frequency (RF) cavity PCBs involves several specialized steps to ensure the precise creation of the cavity and the proper integration of RF components. Here’s an overview of the typical RF cavity PCB fabrication process:
- Design Preparation: The process begins with the design of the RF cavity PCB using specialized PCB design software. Design considerations include cavity dimensions, component placement, signal routing, and grounding techniques optimized for high-frequency performance.
- Material Selection: Choose high-frequency PCB materials such as Rogers, Taconic, or Arlon laminates with specific dielectric constants and low loss tangent characteristics suitable for RF applications. The choice of material depends on the desired operating frequency, performance requirements, and budget.
- Panelization: Arrange multiple PCB designs into a panel layout to optimize material usage and manufacturing efficiency. Panelization involves positioning individual PCBs within a larger panel, leaving space for routing, fiducial markers, and tooling holes.
- Cavity Creation: Use specialized machining techniques such as CNC milling or laser drilling to create the cavity within the PCB. The cavity dimensions and shape are precisely machined according to the design specifications, typically using computer-controlled equipment for accuracy.
- Copper Deposition: Deposit copper onto the PCB surface using a process such as electroplating or chemical deposition. Copper deposition forms the conductive traces, pads, and ground planes necessary for routing RF signals and connecting components.
- Etching: Use chemical etching or plasma etching to remove excess copper from the PCB surface, leaving behind the desired trace patterns and circuitry. Etching is typically controlled by applying a patterned resist layer to protect the copper where traces are required.
- Drilling and Via Formation: Drill holes for component mounting and via formation. Vias are conductive pathways that connect different layers of the PCB, allowing signals to pass between them. For RF cavity PCBs, special attention is given to via placement and impedance control to minimize signal distortion.
- Surface Finish: Apply a surface finish to protect the copper traces and ensure reliable solderability. Common surface finishes for RF PCBs include immersion gold, ENIG (Electroless Nickel Immersion Gold), and HASL (Hot Air Solder Leveling).
- Component Assembly: Place and solder RF components onto the PCB using surface mount technology (SMT) or through-hole technology (THT), depending on the design requirements. Careful attention is paid to component placement to minimize signal distortion and interference.
- Testing and Quality Assurance: Perform thorough testing and inspection of the fabricated RF cavity PCBs to ensure they meet the required specifications for performance and reliability. Testing may include electrical testing, impedance measurements, and RF testing using specialized equipment.
- Final Inspection and Packaging: Conduct a final inspection of the fabricated PCBs to verify quality and consistency. Once approved, package the PCBs for shipping or further assembly into electronic devices.
Throughout the fabrication process, strict quality control measures are implemented to ensure the integrity and reliability of the RF cavity PCBs, especially considering the critical nature of their applications in high-frequency electronic systems.
How do you manufacture a Radio Frequency Cavity PCB?
Manufacturing a Radio Frequency (RF) cavity PCB involves several specialized steps tailored to create the cavity structure and ensure high-frequency performance. Here’s a detailed overview of the manufacturing process:
- Design Preparation: Begin by designing the RF cavity PCB using dedicated PCB design software. Incorporate the cavity structure, component placement, signal routing, and grounding techniques optimized for RF performance.
- Material Selection: Choose high-frequency PCB materials with specific dielectric constants and low loss tangent characteristics suitable for RF applications. Materials like Rogers, Taconic, or Arlon laminates are commonly used. The choice depends on the desired operating frequency and performance requirements.
- Panelization: Arrange multiple PCB designs into a panel layout to optimize material usage and manufacturing efficiency. Panelization involves positioning individual PCBs within a larger panel, leaving space for routing, fiducial markers, and tooling holes.
- Cavity Creation: Utilize specialized machining techniques such as CNC milling or laser drilling to create the cavity within the PCB. The cavity dimensions and shape are precisely machined according to the design specifications, typically using computer-controlled equipment for accuracy.
- Copper Deposition: Deposit copper onto the PCB surface using processes like electroplating or chemical deposition. Copper deposition forms the conductive traces, pads, and ground planes necessary for routing RF signals and connecting components.
- Etching: Employ chemical etching or plasma etching to remove excess copper from the PCB surface, leaving behind the desired trace patterns and circuitry. Etching is controlled by applying a patterned resist layer to protect the copper where traces are required.
- Drilling and Via Formation: Drill holes for component mounting and via formation. Vias are conductive pathways that connect different layers of the PCB, allowing signals to pass between them. Special attention is given to via placement and impedance control to minimize signal distortion.
- Surface Finish: Apply a surface finish to protect the copper traces and ensure reliable solderability. Common surface finishes for RF PCBs include immersion gold, ENIG (Electroless Nickel Immersion Gold), and HASL (Hot Air Solder Leveling).
- Component Assembly: Place and solder RF components onto the PCB using surface mount technology (SMT) or through-hole technology (THT), depending on the design requirements. Component placement is critical to minimize signal distortion and interference.
- Testing and Quality Assurance: Conduct thorough testing and inspection of the manufactured RF cavity PCBs to ensure they meet the required specifications for performance and reliability. Testing may include electrical testing, impedance measurements, and RF testing using specialized equipment.
- Final Inspection and Packaging: Perform a final inspection of the manufactured PCBs to verify quality and consistency. Once approved, package the PCBs for shipping or further assembly into electronic devices.
Throughout the manufacturing process, stringent quality control measures are implemented to ensure the integrity and reliability of the RF cavity PCBs, given their critical applications in high-frequency electronic systems.
How much should a Radio Frequency Cavity PCB cost?
The cost of a Radio Frequency (RF) cavity PCB can vary significantly depending on several factors, including the following:
- Material:The choice of PCB material greatly influences the cost. High-frequency laminates such as Rogers, Taconic, or Arlon tend to be more expensive than standard FR-4 materials due to their superior RF performance characteristics.
- Complexity: The complexity of the PCB design, including the number of layers, intricacy of the cavity structure, density of components, and routing requirements, can impact the manufacturing cost. More complex designs typically require additional manufacturing steps and may involve higher labor costs.
- Quantity: Economies of scale apply in PCB manufacturing, meaning that larger production quantities generally result in lower per-unit costs. Ordering higher quantities can help reduce the cost per PCB, especially for custom or specialized designs.
- Surface Finish and Features: The choice of surface finish and additional features such as gold plating, impedance control, and special coatings can affect the overall cost of the PCB.
- Manufacturing Process: The specific manufacturing processes involved, such as CNC machining for cavity creation, specialized drilling techniques, and assembly methods, can contribute to the overall cost.
- Supplier and Location: The choice of PCB manufacturer and their location can influence pricing due to differences in labor costs, overhead expenses, and supply chain logistics.
Given these variables, it’s challenging to provide a precise cost estimate without specific details about the RF cavity PCB requirements. However, for a rough estimate, the cost of a basic RF cavity PCB with standard features and materials might range from a few dollars to several tens of dollars per square inch. More complex designs or those requiring premium materials and features could cost significantly more.
For accurate pricing, it’s advisable to consult with PCB manufacturers or suppliers and provide them with detailed specifications of the desired RF cavity PCB design. They can then provide customized quotes based on the specific requirements and production volumes.
What is the base material for Radio Frequency Cavity PCBs?
The base material for Radio Frequency (RF) cavity PCBs plays a critical role in determining the electrical properties and performance characteristics of the board at high frequencies. Commonly used base materials for RF cavity PCBs include:
- Rogers Corporation Materials: Rogers Corporation offers a range of high-performance laminates specifically designed for RF and microwave applications. Materials such as RO3000 series, RO4000 series, and RT/duroid series are popular choices for RF cavity PCBs due to their low dielectric loss, stable electrical properties over a wide frequency range, and excellent dimensional stability.
- Taconic Advanced Dielectric Materials: Taconic Advanced Dielectric Materials provides specialized laminates optimized for high-frequency applications. Materials like Taconic TLY series and TLC series offer low loss tangent, high thermal conductivity, and excellent mechanical properties suitable for RF cavity PCBs.
- Arlon Electronic Materials: Arlon Electronic Materials offers a variety of laminates tailored for RF and microwave circuits. Materials such as Arlon AD series and 85N series provide high-frequency performance, low insertion loss, and good thermal management properties required for RF cavity PCBs.
- Isola Group Materials: Isola Group manufactures laminates suitable for RF and microwave applications. Materials like Isola FR408HR and IS680 are engineered to deliver consistent electrical performance, thermal stability, and reliable signal integrity in RF cavity PCBs.
These base materials typically consist of woven glass or ceramic reinforcement impregnated with a resin system, such as epoxy or polyimide. They are engineered to have specific dielectric constants, low loss tangents, and controlled thicknesses to meet the stringent requirements of RF circuits operating at high frequencies.
When selecting the base material for an RF cavity PCB, designers consider factors such as operating frequency, signal integrity requirements, thermal management, mechanical stability, and cost. By choosing the appropriate base material, designers can ensure optimal performance and reliability of RF cavity PCBs in various high-frequency applications.
Which company manufactures Radio Frequency Cavity PCBs?
Some companies specialize in manufacturing Radio Frequency (RF) cavity PCBs, including Rogers Corporation, Taconic Advanced Dielectric Materials, Arlon Electronic Materials, and Isola Group. These companies offer various high-performance substrate materials suitable for RF and microwave applications, including materials used for manufacturing RF cavity PCBs.
We also manufacture RF cavity PCBs. We have advanced manufacturing equipment and technology to meet the high-performance requirements of our customers for RF PCBs. We use advanced materials such as Rogers, Taconic, Arlon, and Isola high-frequency substrate materials to ensure excellent RF characteristics of the PCB.
Our manufacturing process follows strict standards, carefully planned and controlled from design to production. Our engineering team has extensive experience and expertise to provide customized RF cavity PCB solutions to meet specific customer requirements.
Our production facilities are equipped with advanced processing equipment and quality control systems to ensure that each RF cavity PCB meets the requirements and standards of our customers. We also offer comprehensive testing and validation services to ensure the performance and reliability of our products.
Whether for small-batch production or large-scale production, we can provide customers with high-quality, reliable, and cost-effective RF cavity PCB products. We are committed to establishing long-term partnerships with customers and providing them with the best solutions to meet the evolving demands of the RF electronics market.
What are the 7 qualities of good customer service?
Good customer service is essential for building strong relationships with customers and ensuring their satisfaction. Here are seven qualities that characterize good customer service:
- Responsiveness: Good customer service involves being prompt and responsive to customer inquiries, requests, and concerns. Customers appreciate quick and efficient assistance, whether it’s answering questions, resolving issues, or providing support.
- Empathy: Empathy is the ability to understand and relate to the feelings and experiences of customers. Good customer service representatives show empathy by listening attentively to customer concerns, acknowledging their emotions, and demonstrating genuine concern for their well-being.
- Clarity: Effective communication is crucial in customer service. Good customer service involves conveying information clearly and concisely, avoiding jargon or technical language that may confuse customers. Clear communication helps ensure that customers understand the assistance or solutions provided.
- Professionalism: Good customer service is characterized by professionalism in interactions with customers. This includes maintaining a polite and respectful demeanor, adhering to company policies and procedures, and representing the company in a positive light at all times.
- Problem-solving skills: Customers often seek assistance to resolve issues or overcome challenges. Good customer service representatives possess strong problem-solving skills, enabling them to identify the root cause of problems, explore possible solutions, and take appropriate actions to address customer concerns effectively.
- Flexibility: Every customer is unique, and their needs and preferences may vary. Good customer service involves being flexible and adaptable to accommodate different customer requirements. This may involve customizing solutions, offering alternative options, or adjusting service delivery to meet individual customer needs.
- Follow-up: Following up with customers after resolving their issues or completing a transaction demonstrates commitment to their satisfaction. Good customer service includes proactive follow-up to ensure that customers are happy with the resolution and to address any additional questions or concerns they may have.
By embodying these qualities, businesses can deliver exceptional customer service experiences that foster loyalty, repeat business, and positive word-of-mouth referrals.
FAQs
What is a Radio Frequency (RF) cavity PCB?
A Radio Frequency (RF) cavity PCB is a specialized type of printed circuit board designed for high-frequency electronic applications. It typically features a cavity structure to isolate sensitive RF components and optimize signal integrity.
What are the advantages of RF cavity PCBs?
RF cavity PCBs offer several advantages, including improved signal isolation, reduced electromagnetic interference (EMI), enhanced impedance control, and better heat dissipation, making them suitable for high-frequency and high-power RF applications.
What materials are used for RF cavity PCBs?
Common materials for RF cavity PCBs include high-frequency laminates such as Rogers, Taconic, Arlon, and Isola, known for their low dielectric loss, stable electrical properties, and excellent RF performance characteristics.
What are the key design considerations for RF cavity PCBs?
Design considerations for RF cavity PCBs include cavity dimensions and shape, material selection, component placement, signal routing, grounding techniques, impedance matching, and shielding to optimize RF performance and minimize signal loss and interference.
What applications are RF cavity PCBs used for?
RF cavity PCBs are used in a wide range of high-frequency electronic devices and systems, including radio transmitters, receivers, amplifiers, antennas, radar systems, wireless communication devices, and RF test equipment.
How are RF cavity PCBs manufactured?
The manufacturing process for RF cavity PCBs involves specialized steps such as cavity creation using CNC milling or laser drilling, copper deposition, etching, drilling and via formation, surface finishing, component assembly, testing, and quality assurance to ensure high-performance RF characteristics.
What factors affect the cost of RF cavity PCBs?
The cost of RF cavity PCBs depends on factors such as material selection, complexity of the design, quantity ordered, surface finish, additional features, manufacturing processes, and supplier/vendor pricing.