RF Antenna substrate Manufacturer
We are a professional RF Antenna substrate Manufacturer, we mainly produce ultra-small bump pitch substrate, ultra-small trace and spacing packaging substrate and PCBs.
RF antenna substrates are vital components in wireless communication devices, supporting and constructing the radio frequency (RF) antenna system. They are specialized substrate materials, typically made of materials such as fiberglass epoxy laminate (FR-4), Rogers laminates, or polytetrafluoroethylene (PTFE). RF antenna substrates possess specific electrical properties, such as dielectric constant and loss factor, as well as mechanical properties, such as thickness and rigidity. These properties directly influence key parameters of the antenna, including impedance matching, radiation efficiency, and frequency response. When designing RF antenna substrates, various factors need to be considered, including operating frequency, power requirements, environmental conditions, and manufacturing costs. Through careful selection and design of RF antenna substrates, stable and efficient wireless communication systems can be realized to meet a variety of application needs.
What is RF Antenna substrate?
An RF (Radio Frequency) antenna substrate, typically implemented on a PCB (Printed Circuit Board), refers to the material layer upon which the RF antenna is constructed. It plays a crucial role in the performance of the RF antenna system. The substrate’s properties, such as dielectric constant, loss tangent, and thickness, significantly influence the antenna’s impedance matching, radiation efficiency, and overall performance.
Common substrate materials for RF antennas include FR-4 (a type of flame-retardant fiberglass epoxy laminate), Rogers laminates (such as RO3000 series), and Teflon-based materials (e.g., Teflon-based PTFE). Each material has its advantages and disadvantages in terms of electrical properties, cost, manufacturability, and suitability for specific applications.
Designing RF antennas on PCB substrates requires careful consideration of factors such as substrate material selection, substrate thickness, antenna geometry, and placement on the board to achieve optimal performance in terms of radiation pattern, gain, bandwidth, and impedance matching.
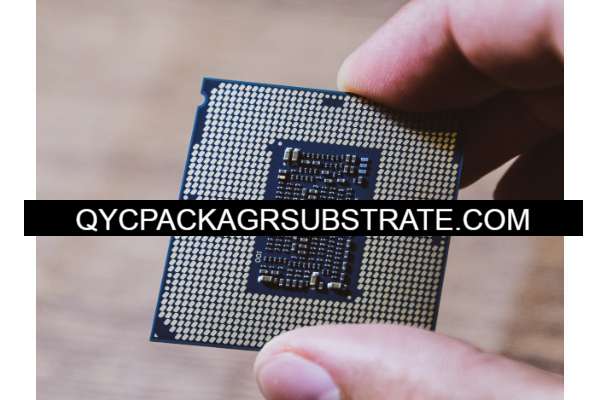
RF Antenna substrate Manufacturer
What are the RF Antenna substrate Design Guidelines?
Designing RF antenna substrates involves adhering to specific guidelines to ensure optimal performance. Here are some key design guidelines:
- Substrate Material Selection: Choose a substrate material with suitable electrical properties for RF applications. Factors to consider include dielectric constant (relative permittivity), loss tangent, thermal stability, and cost. Common materials include FR-4, Rogers laminates, and Teflon-based materials.
- Dielectric Constant (εr): The dielectric constant of the substrate affects the antenna’s impedance matching and radiation characteristics. Higher dielectric constants generally result in smaller antenna sizes but can also lead to higher losses.
- Substrate Thickness: The substrate thickness impacts the antenna’s impedance bandwidth and radiation efficiency. Thinner substrates generally offer broader bandwidth but may have mechanical limitations and higher losses. Thicker substrates provide mechanical robustness but may lead to narrower bandwidth.
- Substrate Homogeneity: Ensure the substrate material is homogeneous to avoid variations in dielectric properties, which can cause impedance mismatch and affect antenna performance.
- Copper Thickness and Surface Roughness: Maintain consistent copper thickness and surface roughness for the conductive traces on the substrate to minimize losses and ensure uniform current distribution.
- Ground Plane Design: Proper design of the ground plane beneath the antenna is crucial for achieving desired radiation characteristics, minimizing ground losses, and reducing electromagnetic interference (EMI). The ground plane should be large enough and provide good conductivity.
- Antenna Placement: Carefully select the location of the antenna on the PCB to minimize coupling with other components and to ensure adequate clearance from metallic or absorbing materials that could affect radiation patterns and efficiency.
- Signal Routing and Impedance Matching: Design transmission lines and matching networks to ensure proper impedance matching between the antenna and the RF circuitry. Use controlled impedance traces to minimize signal reflections and losses.
- EMI Considerations: Implement proper EMI shielding techniques and isolation measures to prevent interference from nearby components and external sources.
- Testing and Validation: Perform thorough testing and validation of the antenna design using simulation tools, prototyping, and measurement techniques to verify performance against design specifications and requirements.
By following these guidelines, designers can develop RF antenna substrates that meet the desired performance criteria for various wireless communication applications.
What is the RF Antenna substrate Fabrication Process?
The fabrication process for RF antenna substrates on PCBs involves several steps to create the necessary structure for mounting and integrating the antenna into an electronic device. Here’s a generalized overview of the process:
- Substrate Preparation: Select the appropriate substrate material based on the RF antenna design requirements. Common materials include FR-4, Rogers laminates, and Teflon-based materials. The substrate should have the desired dielectric constant, thickness, and mechanical properties.
- Copper Cladding: Apply a layer of copper foil to one or both sides of the substrate material. This copper layer will serve as the conductive material for creating the antenna elements and feed lines.
- Photoresist Application: Apply a layer of photoresist material onto the copper-clad substrate surface. The photoresist will act as a mask during the etching process to define the antenna’s geometry and traces.
- Artwork Generation: Create the artwork or design files specifying the desired antenna geometry, including radiating elements, feed lines, and any additional components such as matching networks or baluns. This artwork is typically generated using CAD (Computer-Aided Design) software.
- Exposure and Development: Transfer the artwork onto the photoresist layer using a process called photolithography. This involves exposing the photoresist to UV light through a photomask containing the antenna pattern and then developing the exposed photoresist to remove the unexposed areas, leaving behind the patterned photoresist.
- Etching: Etch away the unprotected copper areas using an etchant solution, leaving behind the desired antenna traces and structures on the substrate. The etching process selectively removes copper where the photoresist has been removed, defining the antenna geometry.
- Photoresist Stripping: Remove the remaining photoresist material from the substrate surface using a stripping solution or other appropriate methods, leaving behind the copper antenna traces and structures.
- Surface Finish: Apply a surface finish to the copper traces to improve solderability and protect against oxidation. Common surface finishes include ENIG (Electroless Nickel Immersion Gold), HASL (Hot Air Solder Leveling), and OSP (Organic Solderability Preservative).
- Assembly: If necessary, assemble additional components such as matching networks, connectors, or shielding onto the substrate to complete the RF antenna system.
- Testing and Quality Control: Perform testing and quality control checks to verify the functionality and performance of the fabricated RF antenna substrate, ensuring that it meets the design specifications and requirements.
By following these fabrication steps, manufacturers can produce RF antenna substrates suitable for integration into various electronic devices and wireless communication systems.
How do you manufacture an RF Antenna substrate?
Manufacturing an RF antenna substrate involves a series of processes to create the PCB (Printed Circuit Board) with the necessary antenna elements and structures. Here’s a detailed overview of the manufacturing process:
- Material Selection: Choose the appropriate substrate material based on the RF antenna design requirements. Common substrate materials include FR-4, Rogers laminates, and Teflon-based materials. Consider dielectric constant, loss tangent, thermal stability, and cost when selecting the material.
- Panelization: Arrange multiple antenna substrates on a larger panel for efficient manufacturing. Panelization helps optimize material usage and facilitates automated handling during subsequent manufacturing steps.
- Copper Cladding: Apply a layer of copper foil to one or both sides of the substrate material. This copper layer will serve as the conductive material for creating the antenna elements, feed lines, and ground plane.
- Cleaning and Surface Preparation: Clean the substrate surface to remove any contaminants or residues that could affect adhesion or subsequent processing steps. Surface preparation may involve processes such as chemical cleaning or plasma treatment.
- Photoresist Application: Apply a layer of photoresist material onto the copper-clad substrate surface. The photoresist will act as a mask during the etching process to define the antenna’s geometry and traces.
- Artwork Generation: Create the artwork or design files specifying the desired antenna geometry, including radiating elements, feed lines, and any additional components such as matching networks or baluns. This artwork is typically generated using CAD (Computer-Aided Design) software.
- Exposure and Development: Transfer the artwork onto the photoresist layer using photolithography. Expose the photoresist to UV light through a photomask containing the antenna pattern, then develop the exposed photoresist to remove the unexposed areas, leaving behind the patterned photoresist.
- Etching: Etch away the unprotected copper areas using an etchant solution, leaving behind the desired antenna traces and structures on the substrate. The etching process selectively removes copper where the photoresist has been removed, defining the antenna geometry.
- Photoresist Stripping: Remove the remaining photoresist material from the substrate surface using a stripping solution or other appropriate methods, leaving behind the copper antenna traces and structures.
- Surface Finish: Apply a surface finish to the copper traces to improve solderability and protect against oxidation. Common surface finishes include ENIG (Electroless Nickel Immersion Gold), HASL (Hot Air Solder Leveling), and OSP (Organic Solderability Preservative).
- Drilling and Plating: Drill holes for component mounting and vias to establish electrical connections between different layers of the PCB. Plate the drilled holes with conductive material to ensure electrical continuity.
- Solder Mask Application: Apply a solder mask over the copper traces to protect them from oxidation and facilitate soldering during component assembly. The solder mask also provides electrical insulation between adjacent traces.
- Silkscreen Printing: Optionally, add component designators, logos, or other markings to the PCB surface using silkscreen printing.
- Final Inspection and Testing: Perform visual inspection, electrical testing, and quality control checks to verify the integrity and functionality of the manufactured RF antenna substrates. Ensure that they meet the design specifications and requirements.
- Separation: Separate individual antenna substrates from the manufacturing panel using singulation methods such as routing, milling, or mechanical punching.
By following these manufacturing steps, companies can produce RF antenna substrates tailored to specific applications, meeting performance, reliability, and cost requirements.
How much should an RF Antenna substrate cost?
The cost of an RF antenna substrate can vary widely depending on several factors, including the substrate material, size, complexity of the antenna design, manufacturing processes, and quantity ordered. Here are some factors that influence the cost:
- Substrate Material: Different substrate materials have different costs. FR-4, being a common and relatively inexpensive material, is often less costly compared to specialized materials like Rogers laminates or Teflon-based substrates, which tend to be more expensive due to their superior electrical properties.
- Size and Thickness: Larger and thicker substrates require more material and may involve additional manufacturing steps, leading to higher costs. Conversely, smaller and thinner substrates may be less expensive.
- Copper Thickness: The thickness of the copper layer on the substrate affects material cost and manufacturing complexity. Thicker copper layers typically cost more and may require additional processing steps such as higher-precision etching.
- Complexity of Antenna Design: Antennas with complex geometries, multiple layers, or intricate patterns may require more precise manufacturing processes and specialized equipment, contributing to higher costs.
- Manufacturing Volume: Economies of scale apply to PCB manufacturing. Larger production volumes typically result in lower per-unit costs due to efficiencies in material utilization, setup, and production processes.
- Manufacturing Technology: Advanced manufacturing technologies, such as high-precision photolithography, laser drilling, or automated assembly, may incur higher initial setup costs but can lead to improved quality and cost savings over the long term.
- Additional Features: Additional features such as surface finish, silkscreen printing, impedance control, and EMI shielding can add to the overall cost of the RF antenna substrate.
- Supplier and Location: The choice of PCB manufacturer and their location can impact costs due to differences in labor costs, overhead expenses, and supply chain logistics.
Given these factors, it’s challenging to provide a specific cost without knowing the exact requirements and specifications of the RF antenna substrate. However, as a rough estimate, the cost of a basic RF antenna substrate for low-volume production could range from a few dollars to several tens of dollars per unit. For high-volume production, the cost per unit may decrease significantly due to economies of scale.
What is RF Antenna substrate base material?
The base material for RF antenna substrates refers to the material upon which the RF antenna is constructed. This material forms the foundation for the antenna structure and influences its electrical and mechanical properties. Several types of materials are commonly used as base substrates for RF antennas:
- FR-4 (Flame Retardant-4): FR-4 is a widely used substrate material in PCB manufacturing due to its cost-effectiveness, availability, and good mechanical properties. It consists of a woven fiberglass epoxy laminate with flame-retardant properties. FR-4 substrates typically have a moderate dielectric constant (around 4.4) and are suitable for many RF applications, especially those operating at lower frequencies.
- Rogers Laminates:Rogers Corporation produces a range of high-performance laminates specifically designed for RF and microwave applications. These laminates, such as the RO3000 series, feature low dielectric loss, tight tolerance control, and excellent stability over frequency and temperature. Rogers laminates are often chosen for high-frequency RF antennas and circuits where superior electrical properties are required.
- Teflon-Based Materials: Teflon-based materials, such as polytetrafluoroethylene (PTFE), offer exceptional electrical properties, including low dielectric constant, low loss tangent, and high thermal stability. These materials are well-suited for high-frequency and high-power RF applications where low signal loss and impedance control are critical. Examples include materials like DuPont’s Teflon-based substrates, such as Teflon PTFE and Teflon PTFE/ceramic composites.
- Ceramic Substrates: Ceramic materials, such as alumina (Al2O3) or aluminum nitride (AlN), offer high thermal conductivity, excellent stability over temperature, and low dielectric loss. Ceramic substrates are commonly used in RF antennas and circuits for applications requiring high power handling and thermal dissipation, such as RF power amplifiers.
The choice of RF antenna substrate base material depends on various factors, including frequency of operation, power requirements, environmental conditions, cost constraints, and manufacturing considerations. Designers select the substrate material that best balances these factors to achieve the desired performance and reliability for the specific RF application.
Which company makes RF Antenna substrates?
Many companies produce RF antenna substrates, some of which include Rogers Corporation, DuPont, and specialized PCB manufacturing companies. These companies offer a variety of materials and processes to meet the needs of different RF applications. For example, Rogers Corporation manufactures high-performance RF laminates such as the RO3000 series, which exhibit excellent electrical performance and stability suitable for high-frequency RF applications. DuPont offers Teflon series materials, such as Teflon PTFE and Teflon PTFE/ceramic composites, known for their low loss, low dielectric constant, and high thermal stability, ideal for applications requiring low signal loss and impedance control.
Our company can also manufacture RF antenna substrates with the following advantages and capabilities:
- Professional Team: We have an experienced team of engineers proficient in RF antenna design and PCB manufacturing technology. They can provide customized RF antenna substrate solutions based on customer requirements.
- Advanced Processes: We employ advanced PCB manufacturing processes and equipment to ensure that the produced RF antenna substrates exhibit excellent electrical performance, reliability, and consistency.
- Diverse Material Selection: We offer a variety of substrate material options, including FR-4, Rogers laminates, Teflon, etc., to meet the requirements of different RF applications.
- Quality Control: We strictly adhere to quality management systems, ensuring that every aspect of production, from raw material procurement to manufacturing, undergoes rigorous quality control to meet customer requirements and standards.
- Flexible Production Capacity: We have flexible production capabilities to meet customer demands for different batch sizes and delivery schedules, providing customized services and support.
With our professional team, advanced processes, and strict quality control, our company can provide customers with high-quality, reliable RF antenna substrates to meet various RF application requirements.
What are the 7 qualities of good customer service?
Good customer service is characterized by several key qualities that contribute to a positive customer experience and foster long-term customer satisfaction. Here are seven qualities of good customer service:
- Responsiveness: Good customer service involves promptly addressing customer inquiries, concerns, and requests. Being responsive means acknowledging customers promptly, providing timely assistance, and ensuring that their needs are met in a timely manner.
- Empathy: Empathy is the ability to understand and empathize with the customer’s feelings, perspectives, and situations. Good customer service representatives demonstrate empathy by actively listening to customers, acknowledging their emotions, and showing genuine concern for their needs and concerns.
- Professionalism: Professionalism encompasses maintaining a courteous, respectful, and professional demeanor when interacting with customers. This includes using appropriate language, tone, and behavior, as well as demonstrating knowledge and competence in addressing customer issues.
- Efficiency: Good customer service involves efficiently resolving customer inquiries and issues without unnecessary delays or complications. This includes having streamlined processes, effective problem-solving skills, and access to relevant information and resources to address customer needs promptly.
- Reliability: Reliability is essential for building trust and confidence in customer service interactions. Good customer service means delivering on promises, following through on commitments, and ensuring consistency in the quality of service provided.
- Flexibility: Flexibility involves adapting to customers’ unique needs, preferences, and circumstances. Good customer service representatives are adaptable and resourceful, willing to accommodate customer requests and find creative solutions to meet their needs effectively.
- Proactivity: Proactivity involves anticipating customer needs, identifying potential issues or concerns, and taking proactive steps to address them before they escalate. Good customer service goes beyond reactive responses and strives to anticipate and preemptively resolve customer issues to enhance the overall customer experience.
By embodying these qualities, organizations can cultivate a culture of excellent customer service and build strong relationships with their customers, leading to increased loyalty, satisfaction, and advocacy.
FAQs
What is an RF antenna substrate?
An RF antenna substrate is the material upon which an RF antenna is constructed. It plays a crucial role in the performance of the antenna system by influencing factors such as impedance matching, radiation efficiency, and mechanical stability.
What are common materials used for RF antenna substrates?
Common materials include FR-4 (a type of fiberglass epoxy laminate), Rogers laminates (such as the RO3000 series), Teflon-based materials (e.g., Teflon PTFE), and ceramic substrates (e.g., alumina or aluminum nitride).
How does the choice of substrate material impact antenna performance?
The choice of substrate material affects the antenna’s electrical properties, such as dielectric constant and loss tangent, which in turn influence parameters like impedance matching, bandwidth, and radiation efficiency.
What factors should be considered when selecting an RF antenna substrate?
Factors to consider include dielectric constant, loss tangent, thermal stability, cost, mechanical properties, and suitability for the specific application and frequency range of the RF antenna.
What are some best practices for designing RF antenna substrates?
Best practices include optimizing substrate thickness, selecting appropriate ground plane configurations, implementing controlled impedance traces, and considering EMI shielding and isolation techniques.
How are RF antenna substrates manufactured?
The manufacturing process typically involves steps such as substrate preparation, copper cladding, photoresist application, artwork generation, etching, surface finish application, drilling, solder mask application, and final inspection.
What are some key considerations for ensuring high-quality RF antenna substrates?
Key considerations include material homogeneity, dimensional accuracy, surface finish quality, copper thickness consistency, adherence to design specifications, and thorough testing and validation.
Where can I find suppliers or manufacturers of RF antenna substrates?
Suppliers can be found through online directories, industry trade shows, and referrals. It’s essential to evaluate suppliers based on factors such as material quality, manufacturing capabilities, lead times, and customer support.