Rigid-flex packaging substrate manufacturer. the Package Substrate will be made with Showa Denko and Ajinomoto High speed materials.or other types high speed materials and high frequency materials.
Rigid-flex packaging substrate is a tech-savvy method frequently employed in electronic gadgets, especially within the realm of printed circuit boards (PCBs). It ingeniously melds together both rigid and flexible materials, creating a singular packaging entity that allows for heightened adaptability and more efficient spatial utilization in the design of electronic devices.
Traditional PCBs typically lean towards a rigid composition, often fashioned from materials like glass fiber-reinforced epoxy resin. However, the innovative approach of rigid-flex packaging seamlessly incorporates both rigid and flexible segments onto a unified board. The rigid elements supply a sturdy foundation for components, while the flexible portions facilitate the board’s ability to contort or fold, accommodating unconventional and spatially constrained configurations.
This technology proves particularly beneficial in scenarios where space is a premium, as seen in portable electronic contraptions such as smartphones, wearables, and medical devices. Rigid-flex PCBs mitigate the necessity for connectors and cables, as the flexible components adeptly substitute traditional wire harnesses, resulting in saved space and a potential uptick in reliability.
The selection of materials for rigid-flex packaging substrates is a meticulous process, ensuring resilience against the mechanical stresses associated with bending and folding. Common materials in use include flexible polyimide films and rigid counterparts like FR-4.
In essence, rigid-flex packaging substrates play a pivotal role in the downsizing and fortification of electronic devices, establishing themselves as a pivotal technology in the contemporary landscape of electronic design.
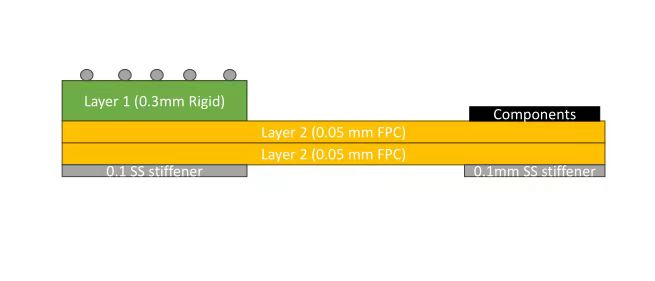
What Innovations Do Rigid-Flex Packaging Substrate Manufacturers Bring?
In the realm of rigid-flex packaging substrates, manufacturers are on a continual quest for groundbreaking advancements to elevate performance, adaptability, and dependability. Here are some noteworthy innovations in this space:
Material Marvels: Manufacturers are proactively delving into the realm of cutting-edge materials, ones that demonstrate enhanced mechanical strength, thermal resilience, and flexibility. This investigative journey involves seamlessly incorporating state-of-the-art high-performance polymers and composite materials, intricately designed to endure the demanding conditions of bending, folding, and a diverse array of environmental challenges.
Refined Miniaturization Tactics:Amidst the rising demand for electronic devices that are both smaller and lighter, manufacturers are leveraging sophisticated miniaturization techniques. This nuanced process entails meticulous refinements to the design and arrangement of rigid-flex PCBs, with a primary emphasis on achieving greater component density while steadfastly maintaining optimal performance.
Tech-Infused Flexibility: The integration of embedded technologies within rigid-flex substrates is a key focus, allowing for added functionalities and features. Think embedded sensors, antennas, or even microprocessors seamlessly incorporated within the flexible segments, contributing to a sleek and integrated design.
Creative Circuitry Designs: Exploring innovative circuit designs is a pursuit to maximize the advantages of flexible sections. This might involve inventive routing techniques, three-dimensional circuit structures, and distinctive interconnection methods, all aimed at optimizing signal integrity and minimizing electromagnetic interference.
Automation Excellence: The use of robotic arms and advanced machinery in the assembly process is a game-changer. This not only boosts precision and consistency but also ensures that manufacturing rigid-flex packaging substrates attains new levels of efficiency, quality, and reliability.
Thermal Mastery: Acknowledging the escalating performance demands of electronic devices, manufacturers are concocting inventive thermal solutions. Flexible heat sinks and thermal vias are part of the arsenal, efficiently dissipating heat and safeguarding the reliability of components.
Ink Advances: Progress in printing technologies for flexible electronics is opening new doors. With the current capabilities, manufacturers have the ability to craft intricate circuit patterns with elevated precision, potentially laying the groundwork for production processes that are not only more cost-effective but also scalable for rigid-flex substrates.
Eco-Conscious Choices: In consideration of environmental sustainability, manufacturers are actively investigating materials and processes that minimize environmental impact. The objective is to craft substrates that not only deliver high performance but also adhere to environmental responsibility, ensuring ease of recyclability.
Quality Assurance Evolution: Enhanced testing methodologies and quality assurance techniques take center stage. Manufacturers are keen on early detection and rectification of defects in the production process, ensuring the reliability and longevity of rigid-flex packaging substrates.
These innovations collectively showcase the dynamic landscape in which rigid-flex packaging substrate manufacturers operate. Their focus is on delivering solutions that embody not just compactness and reliability, but also a keen understanding of the diverse and ever-evolving needs of modern electronic devices.
What Are the Different Types of Rigid-Flex Packaging Substrates?
Diverse types of rigid-flex packaging substrates cater to specific design intricacies and application requisites. They include:
Single-Layer Rigid-Flex: Marked by a lone rigid layer paired with a flexible counterpart, this variant suits applications demanding flexibility in a singular direction.
Double-Layer Rigid-Flex: Introducing dual rigid layers interconnected by flexible counterparts, this configuration offers heightened flexibility in both directions, serving more intricate design needs.
Multilayer Rigid-Flex: Encompassing multiple interconnected rigid and flexible layers, this type unleashes elevated design flexibility, often applied in cutting-edge electronic devices with complex circuitry.
Conductive-Filled Gaps Rigid-Flex: By infusing conductive materials into flexible areas, this substrate creates additional pathways for electrical signals. It proves valuable for optimizing signal integrity and mitigating electromagnetic interference.
Bonded Rigid-Flex: Employing adhesives to unite rigid and flexible layers, this configuration is esteemed for its reliability and robust construction.
Coverlay Rigid-Flex: Introducing a coverlay to shield the flexible part of the PCB, this type enhances durability and reliability, making it apt for applications involving repetitive bending.
Capacitive Rigid-Flex: With integrated capacitive touch-sensitive features, this substrate finds common application in devices requiring responsive touch interfaces.
The selection among these rigid-flex packaging substrate types hinges on the distinctive needs of the electronic device, considering factors like size constraints, flexibility prerequisites, and the complexity of the circuitry. Manufacturers collaborate closely with designers to discern the most suitable type based on the intended application.
What is the Relationship Between Rigid-Flex Packaging Substrate and IC Packaging?
The dynamic interplay between rigid-flex packaging substrates and IC (Integrated Circuit) packaging forms the backbone of modern electronic device design. These two elements dance in tandem, each wielding its influence to shape the functionality and resilience of the end product.
Synergetic Integration:
Rigid-flex packaging substrates act as the architectural canvas, providing a robust foundation for mounting and interconnecting electronic components, including the vital ICs.
ICs, the essential brains of electronic devices, find their place on the rigid sections of the rigid-flex PCB, delivering the computational power needed.
Crafting Miniaturization Mastery:
Rigid-flex packaging substrates take the lead in the art of miniaturization, enabling the creation of more compact and space-efficient electronic designs.
IC packaging techniques play a pivotal role, encapsulating semiconductor devices with precision to seamlessly integrate into the confined spaces offered by the flexible substrate.
Flexibility Ballet and Signal Integrity Symphony:
The flexible domains of rigid-flex substrates gracefully accommodate the need for bending and folding in devices with unconventional shapes.
IC packaging strategies and rigid section design must harmonize to ensure impeccable signal integrity, efficient thermal management, and resilience against mechanical stresses.
Simplified Connections, Complexity Reduction Waltz:
Rigid-flex substrates take the spotlight by simplifying device designs, minimizing the need for additional connectors and cables.
IC packaging, employing innovative techniques like system-in-package (SiP) or multi-chip modules, contributes to consolidating multiple functions into a unified package, elegantly streamlining interconnections.
Guardians of Reliability Across Environments:
Both rigid-flex substrates and IC packaging techniques are entrusted with navigating environmental challenges such as temperature variations, humidity, and mechanical strains.
Through advanced packaging technologies and thoughtfully selected substrate materials, they collaborate to ensure the reliability and durability of the entire electronic system in diverse environmental conditions.
In essence, the intricate choreography between rigid-flex packaging substrates and IC packaging is a harmonious symphony. Rigid-flex substrates set the stage for component integration, and IC packaging techniques bring finesse to encapsulation, working together to achieve peak performance, compact designs, and unwavering reliability in the ever-evolving landscape of electronic devices.
How Does the Structure of Rigid-Flex Packaging Substrate Differ from Traditional PCBs?
The architectural framework of rigid-flex packaging substrates diverges significantly from traditional PCBs, mainly owing to the infusion of flexible materials. Here are discernible disparities in their structural blueprints:
Material Melange:
Traditional PCBs: Predominantly fashioned from rigid materials like FR-4, providing a steadfast and unyielding groundwork.
Rigid-Flex Substrates: Fuse a marriage of rigid materials for stability and flexible counterparts such as polyimide or PTFE for adaptability, fashioning a distinctive amalgamation tailored for versatile applications.
Stratum Structure:
Traditional PCBs: Comprise stacked rigid layers linked by vias and traces.
Rigid-Flex Substrates: Showcase an ensemble of rigid and flexible layers within a singular board, granting a passport to 3D designs and the capability to gracefully bend or fold in designated zones.
Flexibility Ballet and Bending Balletics:
Traditional PCBs: Embrace rigidity, abstaining from the dance of flexibility and confined to standard contours.
Rigid-Flex Substrates: Choreographed to elegantly bend or fold in specified regions, delivering the nimbleness required for applications craving non-traditional silhouettes.
Compact Choreography:
Traditional PCBs: Tailored for conventional outlines, often necessitating additional connectors and cables for intricate choreography.
Rigid-Flex Substrates: Orchestrating more compact designs by weaving in flexible sections, curtailing the need for extra connectors and adapting seamlessly to avant-garde forms.
Applications Symphony:
Traditional PCBs: Find resonance in conventional electronic devices where stiffness is virtuous.
Rigid-Flex Substrates: Take center stage in applications desiring a harmonious blend of flexibility and rigidity, whether in the world of wearables, medical instruments, or aerospace marvels.
Circuitry Sonata:
Traditional PCBs: Perform within the confines of planar and rigid scores.
Rigid-Flex Substrates: Unleash a symphony of intricate circuit designs, particularly in the flexible movements, orchestrating advanced functionalities within confined stages.
Connectivity Waltz:
Traditional PCBs: Engage in a tango of connectors and cables for intricate interconnections.
Rigid-Flex Substrates: Lead a waltz that streamlines connectivity, eschewing excessive connectors and harmonizing components into an integrated ensemble.
Weight and Size Pas de Deux:
Traditional PCBs: Tend towards heftiness, less inclined towards nimble adaptations.
Rigid-Flex Substrates: Choreograph a lighter and more adaptable performance, perfectly attuned for applications with a penchant for weight sensitivity.
In essence, the structural tapestry of rigid-flex packaging substrates is a ballet of fusion, gracefully intertwining the strengths of rigid and flexible materials. This distinctive choreography allows for versatile and compact performances, three-dimensional compositions, and adaptability to avant-garde forms, distinguishing them as virtuosos in the realm of electronic design.
What are the Main Structures and Production Technologies of Rigid-Flex Packaging Substrates?
Rigid-flex packaging substrates encompass various structures and production technologies to cater to the diverse needs of electronic devices. Here are the main structures and production technologies associated with rigid-flex packaging substrates:
Structures:
Single-Layer Rigid-Flex:
Consists of a single rigid layer and a single flexible layer.
Suited for applications requiring flexibility in one direction.
Double-Layer Rigid-Flex:
Features two rigid layers interconnected by flexible layers.
Provides increased flexibility in both directions, accommodating more intricate designs.
Multilayer Rigid-Flex:
Incorporates multiple rigid layers interconnected by flexible layers.
Offers heightened design flexibility, often employed in complex electronic devices.
Conductive-Filled Gaps Rigid-Flex:
Integrates conductive materials into flexible areas, creating additional pathways for electrical signals.
Enhances signal integrity and reduces electromagnetic interference.
Bonded Rigid-Flex:
Joins rigid and flexible layers using adhesives.
Known for its reliability and robust construction.
Coverlay Rigid-Flex:
Adds a coverlay to protect the flexible part of the PCB.
Enhances durability and reliability, suitable for applications involving repeated bending.
Capacitive Rigid-Flex:
Integrates capacitive touch-sensitive features.
Commonly used in devices requiring touch interfaces.
Hybrid Rigid-Flex:
Combines different materials and technologies within a single rigid-flex PCB.
Allows for customized solutions tailored to specific application requirements.
Production Technologies:
Lamination:
Involves bonding together multiple layers of rigid and flexible materials.
Achieves a unified structure through heat and pressure.
Etching:
Used to selectively remove copper from the substrate, defining the conductive traces.
Enables precise circuit patterns on both rigid and flexible layers.
Drilling:
Involves creating holes or vias for interconnecting different layers.
Accommodates the passage of conductive materials between layers.
Additive Printing:
Utilizes additive manufacturing techniques, such as inkjet printing, for depositing conductive materials.
Allows for intricate and customized patterns.
Surface Finish:
Applies coatings to the exposed copper surfaces to enhance solderability and protect against oxidation.
Common surface finishes include HASL (Hot Air Solder Leveling) and ENIG (Electroless Nickel Immersion Gold).
Coverlay Application:
Involves applying a coverlay film over the flexible part of the PCB.
Protects against environmental factors and mechanical stress.
Adhesive Bonding:
Utilizes adhesives to bond rigid and flexible layers together.
Ensures the integrity of the overall structure.
Curing and Annealing:
Involves heat treatment processes to cure adhesives and enhance material properties.
Ensures the durability and stability of the rigid-flex substrate.
These structures and production technologies collectively enable the creation of versatile and reliable rigid-flex packaging substrates, addressing the intricate requirements of modern electronic devices. The choice of specific structures and production methods depends on the application’s demands and design considerations.
FAQs about Rigid-Flex Packaging Substrate
What characterizes a rigid-flex packaging substrate?
A dynamic player in the realm of printed circuit boards (PCBs), the rigid-flex packaging substrate seamlessly merges the robustness of rigid materials with the flexibility of its pliant counterparts. This ingenious design infusion begets heightened flexibility and adaptability within electronic devices.
What perks accompany the deployment of rigid-flex substrates?
Engaging rigid-flex substrates unfolds a trove of advantages—weight and space reduction, augmented reliability sans the clutter of connectors, and a penchant for conforming to avant-garde form factors. Designers revel in the newfound flexibility and streamlined interconnections these substrates bestow upon intricate electronic designs.
In which sectors do rigid-flex substrates assert their prominence?
The spotlight on rigid-flex substrates extends across diverse domains—wearable wonders, precision-driven medical instruments, aerospace marvels, and any electronic milieu where considerations of spatial economy, weight consciousness, and flexibility reign supreme.
How does the compositional symphony of rigid-flex substrates diverge from traditional PCBs?
The structural ballet of rigid-flex substrates unveils a harmonious blend, melding rigid and flexible layers into a singular board. This distinctive composition sets them apart from their traditional PCB counterparts, which often lack the graceful flex exhibited by specific regions in rigid-flex substrates.
What materials typically take the stage in the fabrication of rigid-flex substrates?
Rigid sections often don the cloak of materials like FR-4, while the flexible counterparts embrace the likes of polyimide or PTFE. The choice of materials choreographs itself in tune with the unique needs and aspirations of the application.
What challenges engage the manufacturing ballet of rigid-flex substrates?
The manufacturing saga of rigid-flex substrates encounters challenges akin to orchestrating a grand performance—ensuring robust bonding between rigid and flexible layers, maintaining the tempo of quality in flexible materials, and navigating the intricate dance of bending and folding during the manufacturing crescendo.
Are there distinct classifications adorning rigid-flex substrates?
Indeed, a spectrum of classifications graces the stage—single-layer, double-layer, multilayer, conductive-filled gaps, bonded, coverlay, capacitive, and hybrid rigid-flex substrates. Each classification pirouettes to its unique design notes, catering to the nuanced preferences of diverse applications.
What unfolds in the grand narrative of manufacturing rigid-flex substrates?
The manufacturing narrative orchestrates a grand tapestry, weaving together the layers through lamination, etching intricate circuit patterns, drilling passages for interconnections, and adorning with diverse surface finishes. Techniques like additive printing, coverlay application, adhesive bonding, and curing add layers of sophistication to this manufacturing opus.
What key considerations waltz in the selection of rigid-flex substrates for a specific application?
The selection waltz is guided by considerations of flexibility finesse, spatial constraints, weight aspirations, environmental nuances, and the choreography of circuit intricacies. Collaborative efforts between manufacturers and designers perform a duet, harmonizing to select the most fitting type for a given application.
How do rigid-flex substrates join the grand ballet of downsizing electronic devices?
Rigid-flex substrates gracefully join the ballet of downsizing by seamlessly incorporating flexible sections, alleviating the need for excessive connectors and cables. This dance of integration fosters the overall downsizing spectacle in the realm of electronic devices.
Conclusion
In conclusion, the realm of rigid-flex packaging substrates unfolds as a vibrant canvas where innovation and technological prowess converge. This fusion of rigidity and flexibility within a single board represents a paradigm shift in electronic design, catering to the intricate demands of contemporary devices that prioritize sleekness, adaptability, and unwavering dependability.
The dynamic interplay between rigid and flexible materials orchestrates a symphony of possibilities across diverse applications. From the graceful contours of wearable tech that seamlessly conforms to the human form to the intricate demands of medical instruments and the robust resilience required for aerospace systems, rigid-flex substrates stand as versatile enablers in the evolving landscape of electronic solutions.
Manufacturers, in their tireless pursuit of progress, continue to introduce pioneering advancements. The incorporation of high-performance polymers and composite materials emerges as a central narrative, fortifying these substrates to gracefully endure the bending, folding, and myriad environmental stresses encountered in real-world scenarios.
In response to the escalating desire for compact and lightweight electronic devices, an intricate dance of miniaturization techniques takes center stage. This involves meticulous design adjustments in rigid-flex PCBs, achieving heightened component density without compromising on performance—an artistry that traditional PCBs often struggle to emulate.
The narrative extends into the exploration of novel materials, boasting enhanced mechanical strength, thermal endurance, and flexibility. This exploration delves into the integration of cutting-edge polymers and composites, meticulously crafted to withstand the rigors of bending, folding, and the diverse array of challenges posed by different environments.
With a conscientious gaze towards environmental sustainability, manufacturers embark on a journey exploring materials and processes with reduced environmental impact. The aspiration goes beyond performance; it encompasses the creation of substrates that not only excel in functionality but also contribute to a greener and more ecologically responsible electronic landscape.
As we draw the curtain on this exploration of rigid-flex packaging substrates, the narrative unfolds as a testament to an industry pushing the boundaries of what’s possible. These substrates transcend their role as mere components; they emerge as catalysts for technological feats, facilitating the creation of devices seamlessly integrated into our daily lives. The journey continues, with each innovation propelling us further into a future where electronic devices are not just smart but also embody versatility, reliability, and a commitment to environmental stewardship.