Rogers Cavity PCB manufacturing. High frequency Cavity PCBs and High Speed cavity PCBs Vendor. we use the Rogers series materials to produce the cavity PCBs. open one cavity on a unit boards. or open multi-cavity on the rogers PCBs. we have this cavity boards production technology.
A Cross blind/buried vias PCB is a high-density, high-performance printed circuit board (PCB) design solution commonly used in complex electronic devices. This design employs blind and buried via technologies to maximize connections between different layers of the PCB while minimizing space occupation. Blind vias refer to holes visible only on one side, while buried vias are holes completely embedded within the PCB. By employing cross-layer routing, blind and buried vias can traverse between different layers, enabling more intricate circuit connections and enhancing the PCB’s performance and reliability. This design not only reduces the size of the PCB but also lowers signal transmission delay and improves signal integrity. Consequently, Cross blind/buried vias PCB has become the preferred design solution for many high-end electronic products such as smartphones, tablets, and high-performance computers.
What is a Rogers Cavity PCB?
We are a professional Rogers Cavity PCB manufacturing supplier, we mainly produce ultra-small bump pitch substrate, ultra-small trace and spacing packaging substrate and PCBs.
A Rogers Cavity PCB refers to a type of printed circuit board (PCB) that utilizes materials manufactured by Rogers Corporation, a company known for producing high-performance specialty materials for various industries, including electronics. Rogers PCBs are designed to offer exceptional electrical performance, especially in applications requiring high-frequency signals, such as in microwave and RF (radio frequency) circuits.
The term “cavity” in Rogers Cavity PCB refers to the construction technique where the PCB incorporates cavities or voids within the substrate layers. These cavities are typically filled with air or other dielectric materials to achieve specific electrical properties, such as controlled impedance and reduced signal loss.
Rogers Corporation offers a range of high-frequency laminate materials that are commonly used in the fabrication of Rogers Cavity PCBs. These materials often have low dielectric constants, low loss tangents, and excellent thermal stability, making them suitable for demanding applications where signal integrity is crucial.
Rogers Cavity PCBs are commonly used in telecommunications, aerospace, defense, medical devices, and other industries where high-frequency and high-speed circuitry is required. They are often found in applications such as antennas, radar systems, satellite communications, and wireless networking equipment.
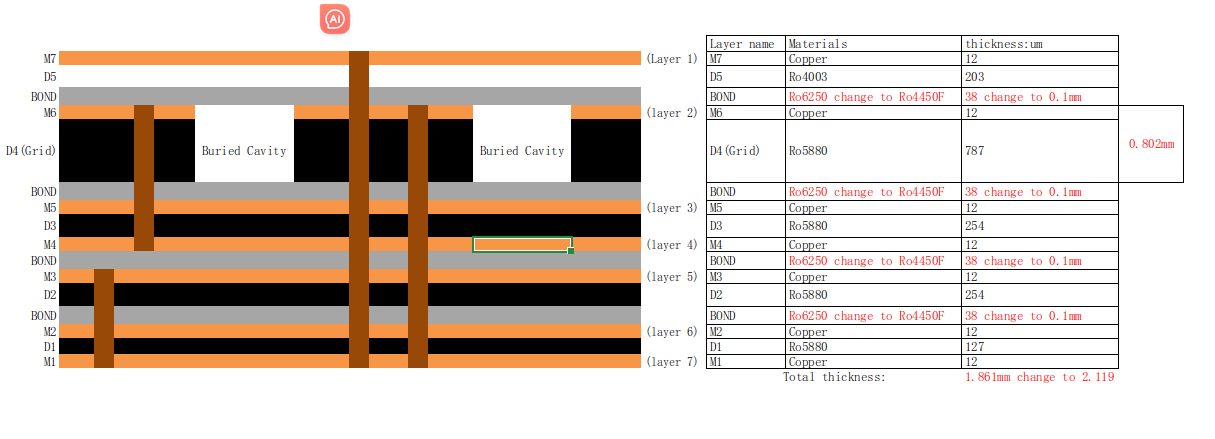
Rogers Cavity PCB
What are the Rogers Cavity PCB Design Guidelines?
Designing a Rogers Cavity PCB involves adhering to specific guidelines to ensure optimal performance, especially in high-frequency applications. Here are some common design guidelines for Rogers Cavity PCBs:
- Material Selection: Choose appropriate Rogers high-frequency laminate material based on the required electrical properties, such as dielectric constant (εr), loss tangent (tan δ), and thermal stability.
- Layer Stackup: Design the layer stackup carefully to achieve the desired impedance and minimize signal losses. Consider incorporating cavity structures within the PCB layers if necessary.
- Cavity Design: If using cavities, ensure proper dimensions and placements to maintain structural integrity and electrical performance. The cavity dimensions should be optimized to minimize electromagnetic interference (EMI) and ensure consistent impedance.
- Transmission Line Routing: Implement controlled impedance transmission lines to maintain signal integrity. Use appropriate trace widths, spacing, and layer configuration to achieve the desired impedance matching.
- Grounding: Ensure a solid ground plane and proper grounding techniques to minimize ground loops and reduce electromagnetic interference (EMI). A continuous ground plane beneath signal traces helps to improve signal integrity.
- Component Placement: Optimize component placement to minimize signal path lengths and reduce parasitic capacitance and inductance. Place high-speed components closer to each other and minimize vias in high-frequency signal paths.
- Via Design: Use high-frequency optimized vias and minimize the number of vias in high-frequency signal paths to reduce discontinuities and impedance mismatches.
- Thermal Management: Consider thermal management techniques, such as thermal vias or heatsinks, especially in applications where heat dissipation is a concern due to high-power components or high ambient temperatures.
- Signal Integrity Analysis: Perform signal integrity analysis, such as impedance simulation and crosstalk analysis, using specialized software tools to validate the design and ensure compliance with performance requirements.
- Manufacturability: Consider manufacturability aspects during the design phase, such as ensuring compatibility with standard PCB fabrication processes and techniques.
By following these guidelines, designers can create Rogers Cavity PCBs that meet the stringent requirements of high-frequency applications while ensuring optimal performance and reliability.
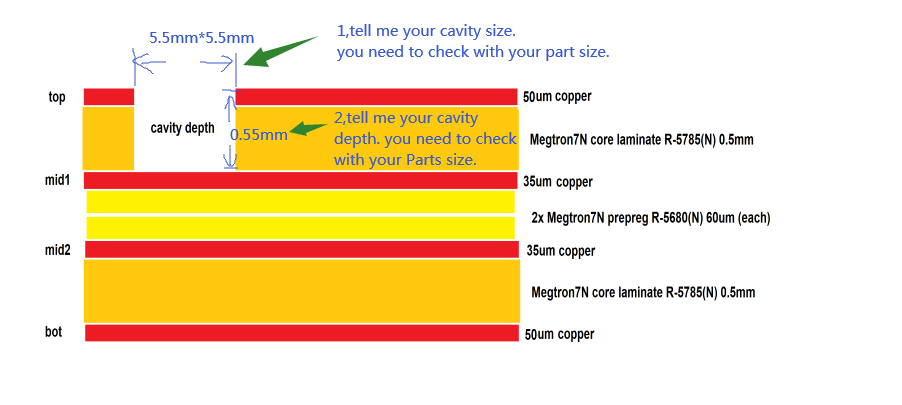
High speed Cavity PCB
What is the Rogers Cavity PCB Fabrication Process?
The fabrication process for Rogers Cavity PCBs involves several steps, similar to the fabrication process for standard printed circuit boards (PCBs), but with some specific considerations due to the use of high-frequency materials and cavity structures. Here’s an overview of the Rogers Cavity PCB fabrication process:
- Design: The process begins with the PCB design phase, where the circuit schematic and layout are created using PCB design software. Design considerations should include material selection, layer stackup design, cavity placement and dimensions, transmission line routing, grounding, and thermal management.
- Material Selection: Choose the appropriate Rogers high-frequency laminate material based on the required electrical properties for the specific application.
- Preparation: Prepare the substrate materials by cutting them to the required size according to the PCB design specifications.
- Layer Stackup: Assemble the layers according to the designed stackup, including the placement of cavity structures if applicable. Bond the layers together using heat and pressure to form a solid substrate.
- Drilling: Drill holes for component mounting pads, vias, and interconnections using precision drilling equipment. Special attention should be paid to the accuracy of hole placement and size to ensure proper alignment and impedance control.
- Copper Plating: Apply a thin layer of copper to the substrate surface using processes such as electroless copper plating or electroplating. This copper layer serves as the conductive trace pattern for the circuit.
- Circuit Patterning: Apply a layer of photoresist material to the copper surface and expose it to UV light through a photomask with the desired circuit pattern. Develop and etch away the unexposed photoresist to remove unwanted copper, leaving behind the desired circuit traces.
- Cavity Creation (if applicable): Mill or rout out the cavity structures within the substrate layers using CNC machining equipment. Ensure precise dimensions and alignment to maintain structural integrity and electrical performance.
- Surface Finish: Apply a surface finish to protect the exposed copper traces from oxidation and facilitate solderability. Common surface finishes include HASL (Hot Air Solder Leveling), ENIG (Electroless Nickel Immersion Gold), and OSP (Organic Solderability Preservative).
- Component Assembly: Mount and solder electronic components onto the PCB using surface mount technology (SMT) or through-hole technology (THT), depending on the design requirements.
- Testing and Inspection: Perform electrical testing and visual inspection to verify the functionality and quality of the assembled PCBs. This may include continuity testing, impedance measurements, and visual inspection for defects.
- Final Finishing: Trim excess material from the PCB edges, apply labeling or marking as needed, and package the finished PCBs for shipping or further assembly.
Throughout the fabrication process, strict quality control measures should be implemented to ensure the integrity and reliability of the Rogers Cavity PCBs, especially in high-frequency applications where signal integrity is critical.
How do you manufacture a Rogers Cavity PCB?
Manufacturing a Rogers Cavity PCB involves several steps to ensure the precise fabrication of the PCB with the desired electrical properties. Below is a generalized outline of the fabrication process:
- Design: The process begins with the PCB design, where engineers use specialized PCB design software to create the layout, including the layer stackup, transmission line routing, cavity design, and component placement. Design considerations must adhere to Rogers Cavity PCB design guidelines to meet performance requirements.
- Material Selection: Select the appropriate Rogers high-frequency laminate material based on the desired electrical properties and performance specifications. The choice of material depends on factors such as dielectric constant, loss tangent, thermal stability, and frequency requirements.
- Substrate Preparation: Prepare the substrate materials according to the PCB design. This involves cutting the laminate sheets to the required size and cleaning them to remove any contaminants that could affect adhesion or electrical properties.
- Layer Preparation: Prepare the individual layers of the PCB stackup by applying adhesive to bond the copper foil to the substrate materials. In the case of cavity designs, precision milling or routing may be performed to create the cavities within the substrate layers.
- Circuit Patterning: Use photolithography or direct imaging techniques to transfer the PCB design onto the copper layers. This involves applying a photoresist material, exposing it to UV light through a mask, developing the resist, and etching away the unwanted copper to form the circuit traces and pads.
- Cavity Formation: If the design includes cavities, precision milling or routing equipment is used to create the cavities within the substrate layers. Care must be taken to ensure accurate dimensions and proper placement of the cavities.
- Layer Lamination: Assemble the individual layers of the PCB stackup using heat and pressure to laminate them together. This process bonds the layers and ensures proper alignment of the circuitry and cavities.
- Drilling and Plating: Drill holes for vias and component mounting pads using CNC drilling equipment. Then, plate the holes with conductive material (e.g., copper) to establish electrical connections between layers.
- Surface Finishing: Apply surface finish to protect the exposed copper surfaces and provide solderability. Common surface finishes include HASL (hot air solder leveling), ENIG (electroless nickel immersion gold), and OSP (organic solderability preservative).
- Final Inspection: Inspect the fabricated PCB for any defects, such as shorts, open circuits, or dimensional inaccuracies. Use automated optical inspection (AOI) and other testing methods to ensure quality and reliability.
- Testing: Perform electrical testing to verify the performance characteristics of the PCB, including impedance matching, signal integrity, and functionality. This may involve using specialized testing equipment and techniques tailored to high-frequency applications.
- Final Assembly: Once the PCBs pass inspection and testing, they can be assembled with components according to the specific application requirements.
Throughout the entire manufacturing process, strict quality control measures are implemented to ensure consistency, reliability, and adherence to performance specifications. Collaboration between PCB designers, engineers, and manufacturing personnel is crucial to achieving successful fabrication of Rogers Cavity PCBs.
How much should a Rogers Cavity PCB cost?
The cost of manufacturing a Rogers Cavity PCB can vary widely depending on several factors, including the complexity of the design, the size of the board, the quantity ordered, the choice of Rogers material, and the fabrication techniques involved. Here are some key factors that can influence the cost:
- Board Size and Complexity: Larger boards or those with intricate designs will generally cost more to manufacture due to increased material usage and more complex fabrication processes.
- Layer Count: The number of layers in the PCB affects the manufacturing cost. Rogers Cavity PCBs often have multiple layers to accommodate high-frequency circuitry and signal integrity requirements.
- Material Selection: Rogers Corporation offers various high-frequency laminate materials with different properties and costs. The choice of material will impact the overall cost of the PCB.
- Cavity Structure: If the PCB includes cavities, the fabrication process may be more complex and require specialized techniques, which can affect the cost.
- Features and Specifications: Additional features such as controlled impedance traces, blind/buried vias, surface finishes, and solder mask options can contribute to the overall cost.
- Quantity: Larger production runs typically result in lower per-unit costs due to economies of scale. Ordering in bulk can reduce the cost per board.
- Turnaround Time: Expedited fabrication services may incur additional charges compared to standard lead times.
- Supplier and Location: PCB fabrication costs can vary between different manufacturers and regions. Offshore fabrication may offer lower costs but could involve longer lead times and potential quality risks.
To obtain an accurate cost estimate for a specific Rogers Cavity PCB project, it’s recommended to consult with PCB manufacturers or suppliers. They can provide quotes based on the detailed specifications and requirements of the project. Additionally, obtaining multiple quotes from different suppliers can help in comparing costs and finding the most competitive offer.
What is the Rogers Cavity PCB base material?
The base material used in Rogers Cavity PCBs is typically a high-frequency laminate manufactured by Rogers Corporation. Rogers offers a range of specialty materials specifically designed for high-frequency applications, including RF/microwave circuits and other high-speed digital applications.
Some common examples of base materials used in Rogers Cavity PCBs include:
- Rogers RO4000 Series: This series includes high-frequency laminates with low dielectric constant (εr) and low loss tangent (tan δ), making them suitable for applications requiring high signal integrity and minimal loss. Examples include RO4350B, RO4003C, and RO4835.
- Rogers RO3000 Series: These laminates offer excellent electrical properties for high-frequency applications, with options for different dielectric constants and thicknesses. Examples include RO3003, RO3006, and RO3010.
- Rogers RO6000 Series: This series includes laminates with enhanced thermal performance, making them suitable for applications requiring high power handling capabilities combined with high-frequency performance.
- Rogers TMM Series: This series offers laminates with a combination of high-performance electrical properties and mechanical stability, making them suitable for both high-frequency and high-reliability applications.
These base materials are engineered to provide consistent electrical performance, thermal stability, and mechanical properties required for demanding applications in industries such as telecommunications, aerospace, defense, and medical devices. When designing Rogers Cavity PCBs, selecting the appropriate base material from these series is crucial to achieving the desired performance and reliability.
Which company makes Rogers Cavity PCBs?
Rogers Cavity PCBs are typically manufactured by specialized PCB manufacturing companies, which possess advanced technology and equipment, as well as experienced engineering teams capable of designing and producing high-performance Rogers cavity PCBs according to customer requirements. These companies often have extensive experience in handling complex designs and manufacturing processes while ensuring products meet the stringent requirements of high-frequency applications.
Our company is also capable of producing Rogers Cavity PCBs. As a professional PCB manufacturer, we have advanced production equipment and a skilled technical team capable of meeting customers’ demands for high-performance circuit boards. With our experienced engineering team, we can develop appropriate manufacturing solutions based on customers’ design requirements and specifications. We have established good partnerships with material suppliers such as Rogers Corporation, enabling us to obtain high-quality Rogers substrates to ensure product reliability and stability.
We employ advanced manufacturing processes and a rigorous quality control system to ensure the production of high-quality Rogers Cavity PCBs that meet customer requirements. We offer flexible customization services, providing Rogers Cavity PCBs in different specifications, layer counts, and characteristics according to customer needs, while ensuring timely delivery and competitive pricing.
Whether in telecommunications, aerospace, defense, or medical equipment fields, our company can provide reliable solutions to meet customers’ demands for high-performance Rogers Cavity PCBs. We are committed to delivering quality products and services to our customers, working together to achieve success and development.
What are the 7 qualities of good customer service?
Good customer service is characterized by several key qualities that contribute to positive interactions and relationships with customers. Here are seven qualities of good customer service:
- Empathy: Good customer service representatives demonstrate empathy by understanding and acknowledging customers’ concerns, feelings, and perspectives. They put themselves in the customer’s shoes and respond with compassion and understanding.
- Communication Skills: Effective communication is essential for good customer service. Representatives should be clear, concise, and courteous in their communication, whether it’s in person, over the phone, or via written channels. They should listen actively, ask relevant questions, and provide helpful information or solutions.
- Problem-Solving Abilities: Good customer service involves resolving issues and addressing problems promptly and effectively. Representatives should be skilled at identifying problems, analyzing situations, and offering appropriate solutions or alternatives to meet customers’ needs.
- Product Knowledge: A good understanding of the products or services offered is crucial for providing excellent customer service. Representatives should be knowledgeable about the features, benefits, and usage of the products or services they support. This enables them to answer questions accurately and offer valuable assistance to customers.
- Patience: Dealing with customer inquiries, complaints, and requests requires patience and resilience. Good customer service representatives remain calm and composed, even in challenging situations. They listen attentively, handle difficult customers tactfully, and persevere until issues are resolved satisfactorily.
- Responsiveness: Timely responsiveness is a key aspect of good customer service. Representatives should respond promptly to customer inquiries, whether it’s answering phone calls, replying to emails, or addressing messages on social media platforms. Quick response times demonstrate attentiveness and a commitment to customer satisfaction.
- Professionalism: Good customer service is delivered with professionalism and integrity. Representatives should conduct themselves professionally, adhering to company policies, ethical standards, and industry regulations. They should treat all customers with respect, courtesy, and fairness, regardless of the situation.
By embodying these qualities, businesses can cultivate strong customer relationships, foster customer loyalty, and enhance their reputation for delivering exceptional customer service.
FAQs (Frequently Asked Questions)
What is a Rogers Cavity PCB?
A Rogers Cavity PCB refers to a printed circuit board (PCB) that utilizes materials manufactured by Rogers Corporation, specifically designed for high-frequency applications. These PCBs often incorporate cavities or voids within the substrate layers to achieve controlled impedance and reduce signal loss.
What are the advantages of Rogers Cavity PCBs?
Rogers Cavity PCBs offer several advantages, including high electrical performance, low signal loss, excellent thermal stability, and suitability for high-frequency applications. They are widely used in industries such as telecommunications, aerospace, and defense where signal integrity is crucial.
How are Rogers Cavity PCBs different from standard PCBs?
Rogers Cavity PCBs differ from standard PCBs primarily in the materials used and the incorporation of cavities within the substrate layers. Rogers materials are specifically engineered for high-frequency applications, offering superior electrical properties compared to standard PCB materials.
What applications are Rogers Cavity PCBs used for?
Rogers Cavity PCBs are used in a variety of high-frequency applications, including antennas, radar systems, satellite communications, wireless networking equipment, and RF/microwave circuits. They are also found in medical devices, automotive electronics, and other industries requiring high-performance circuitry.
How do you design Rogers Cavity PCBs?
Designing Rogers Cavity PCBs involves careful consideration of factors such as material selection, layer stackup, cavity design, transmission line routing, grounding, and thermal management. Specialized design software and expertise in high-frequency PCB design are often required.
What are the cost considerations for Rogers Cavity PCBs?
The cost of Rogers Cavity PCBs depends on factors such as board size, complexity, material selection, quantity ordered, and manufacturing processes involved. Typically, Rogers Cavity PCBs may have higher manufacturing costs compared to standard PCBs due to the specialized materials and processes involved.
Where can I find a manufacturer for Rogers Cavity PCBs?
Several PCB manufacturers specialize in the fabrication of Rogers Cavity PCBs. It’s recommended to research and contact reputable manufacturers with experience in high-frequency PCB fabrication. Additionally, consulting with Rogers Corporation or their authorized distributors can provide recommendations for qualified manufacturers.