Semiconductor Glass Substrates Manufacturer
Semiconductor Glass Substrates Manufacturer. we can produce the best samllest bump pitch with 100um, the best smallest trace are 9um. and the smallest gap are 9um. most of the design are 15um to 30um trace and spacing.
Mixed dielectric Rogers PCBs combine different dielectric materials within the PCB substrate, offering enhanced performance and versatility. By integrating multiple dielectric constants, these PCBs can efficiently control signal propagation and impedance matching, crucial for high-frequency applications. The Rogers substrate, renowned for its low loss tangent and stable dielectric properties, forms the foundation of these PCBs. This allows for improved signal integrity and reduced signal distortion, resulting in higher data transmission rates and better overall system performance. The incorporation of various dielectric materials enables precise impedance control, facilitating the design of complex RF and microwave circuits with minimal signal loss. Mixed dielectric Rogers PCBs find applications in telecommunications, aerospace, radar systems, and high-speed data transmission, where stringent signal integrity requirements are paramount. With their ability to accommodate diverse dielectric needs within a single substrate, these PCBs offer engineers flexibility and efficiency in designing advanced electronic systems.
What is a Semiconductor Glass Substrate (SGS)?
A Semiconductor Glass Substrate (SGS) is a specialized material used in the production of semiconductor devices, such as integrated circuits (ICs), microprocessors, and memory chips. It serves as the foundation upon which semiconductor components are built. The substrate is typically made from a high-purity glass material, such as borosilicate or fused silica, that has been engineered to possess specific properties suitable for semiconductor fabrication processes.
The primary function of the SGS is to provide a stable and flat surface onto which semiconductor layers can be deposited and patterned using photolithography and other microfabrication techniques. The flatness and smoothness of the substrate are crucial for ensuring the precise alignment and uniformity of the various layers that make up the semiconductor device.
One of the key advantages of using a glass substrate is its excellent thermal and dimensional stability. Glass has a low coefficient of thermal expansion, meaning it expands and contracts minimally with changes in temperature. This property helps to maintain the integrity of the semiconductor device, particularly during the high-temperature processing steps involved in fabrication.
Additionally, glass substrates offer good electrical insulation properties, which can help to minimize unwanted electrical interference between different components within the semiconductor device. This is particularly important for reducing signal noise and enhancing the overall performance of the device.
SGSs are manufactured using advanced manufacturing techniques, such as precision grinding, polishing, and chemical etching, to achieve the required surface characteristics and dimensional accuracy. The substrates are typically produced in large, flat sheets, which are then cut into smaller pieces known as wafers. These wafers serve as the starting material for the fabrication of individual semiconductor devices.
In summary, Semiconductor Glass Substrates play a critical role in the production of semiconductor devices by providing a stable, flat, and electrically insulating foundation for the deposition and patterning of semiconductor layers. Their unique combination of thermal and dimensional stability, along with excellent electrical properties, makes them an ideal choice for various semiconductor applications.
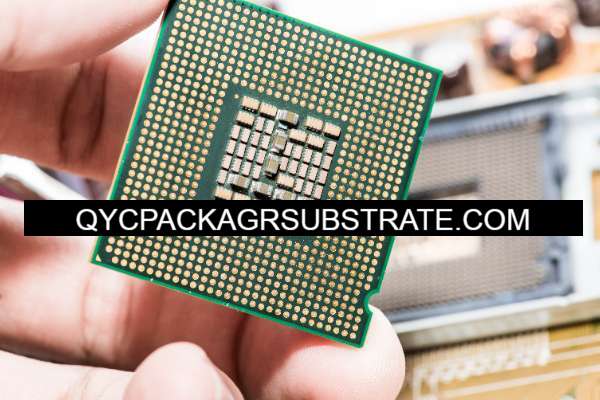
Semiconductor Glass Substrates Manufacturer
What are the Semiconductor Glass Substrate (SGS) Design Guidelines?
Semiconductor Glass Substrate (SGS) design guidelines are a set of recommendations and specifications used by semiconductor manufacturers to ensure the successful integration of glass substrates into semiconductor device fabrication processes. These guidelines cover various aspects of substrate design, including material selection, dimensional tolerances, surface quality, and compatibility with specific processing steps. Here are some common SGS design guidelines:
- Material Selection: Choose a high-purity glass material with suitable properties for semiconductor fabrication, such as low thermal expansion coefficient, high chemical resistance, and excellent optical transparency.
- Dimensional Tolerances: Specify tight dimensional tolerances for substrate thickness, flatness, and parallelism to ensure uniformity and accuracy in semiconductor device fabrication.
- Surface Quality: Ensure that the substrate surface is free from defects, such as scratches, pits, and contaminants, which can adversely affect device performance and yield.
- Thermal Stability: Select a glass material with low thermal expansion coefficient to minimize dimensional changes during high-temperature processing steps, such as thermal annealing and diffusion.
- Electrical Insulation: Verify that the glass substrate provides adequate electrical insulation to prevent leakage currents and minimize signal interference between semiconductor components.
- Compatibility with Processing Steps:Evaluate the compatibility of the glass substrate with various semiconductor fabrication processes, including deposition, etching, lithography, and bonding. Ensure that the substrate can withstand the chemical and thermal stresses associated with these processes without compromising its integrity.
- Wafer Handling: Design the substrate with features, such as flatness and edge profiles, that facilitate precise wafer handling and alignment during semiconductor device fabrication.
- Cleaning and Surface Treatment: Define procedures for cleaning and surface treatment of the glass substrate to remove contaminants and improve adhesion of thin-film layers deposited onto the substrate surface.
- Quality Control:Implement rigorous quality control measures to inspect and characterize the substrate material and ensure compliance with design specifications and industry standards.
- 10. Documentation:Maintain comprehensive documentation of SGS design specifications, manufacturing processes, and quality assurance procedures to facilitate traceability and reproducibility in semiconductor device fabrication.
By adhering to these Semiconductor Glass Substrate (SGS) design guidelines, semiconductor manufacturers can optimize the performance, reliability, and yield of semiconductor devices fabricated using glass substrates.
What is the Semiconductor Glass Substrate (SGS) Fabrication Process?
The fabrication process of Semiconductor Glass Substrates (SGS) involves several steps to produce high-quality glass substrates suitable for semiconductor device fabrication. Below is a general overview of the typical SGS fabrication process:
- Raw Material Selection: High-purity glass materials, such as borosilicate or fused silica, are chosen based on their specific properties, including low thermal expansion coefficient, high chemical resistance, and optical transparency.
- Glass Preparation:The selected glass material is melted in a furnace at high temperatures to form a homogeneous molten liquid. Various additives may be introduced to modify the properties of the glass, such as improving its thermal stability or enhancing its electrical insulation properties.
- Forming and Shaping: The molten glass is shaped into the desired form, typically large, flat sheets or ingots, using techniques such as rolling, drawing, or casting. The glass may undergo further processing, such as annealing, to relieve internal stresses and improve its dimensional stability.
- Cutting and Sizing: The formed glass sheets or ingots are cut into smaller pieces known as wafers, which serve as the substrates for semiconductor device fabrication. Precision cutting techniques, such as sawing or laser cutting, are used to achieve the desired dimensions and surface quality of the wafers.
- Grinding and Polishing: The surfaces of the glass wafers are ground and polished to achieve the required flatness, smoothness, and surface quality. Precision grinding and polishing techniques are employed to remove surface defects and achieve tight dimensional tolerances.
- Cleaning and Surface Treatment: The glass wafers undergo thorough cleaning and surface treatment processes to remove contaminants and improve the adhesion of subsequent thin-film layers deposited onto the substrate surface. Cleaning may involve chemical etching, ultrasonic cleaning, or plasma treatment to ensure the substrate is free from impurities.
- Quality Control and Inspection: Rigorous quality control measures are implemented to inspect and characterize the glass substrates at various stages of the fabrication process. Optical inspection, surface profilometry, and other characterization techniques are used to assess the dimensional accuracy, surface quality, and overall integrity of the substrates.
- Packaging and Storage: The finished glass substrates are packaged and stored in a controlled environment to prevent contamination and ensure their stability until they are ready for use in semiconductor device fabrication.
By following these steps, semiconductor manufacturers can produce high-quality Semiconductor Glass Substrates (SGS) that meet the stringent requirements of semiconductor fabrication processes, resulting in reliable and high-performance semiconductor devices.
How do you manufacture a Semiconductor Glass Substrate (SGS)?
Manufacturing Semiconductor Glass Substrates (SGS) involves several intricate steps to produce high-quality glass wafers suitable for semiconductor device fabrication. Here’s a detailed overview of the SGS manufacturing process:
- Raw Material Selection: High-purity glass materials are carefully chosen based on their properties, such as low thermal expansion coefficient, high chemical resistance, and optical transparency. Common materials include borosilicate glass and fused silica.
- Glass Melting: The selected glass materials are melted in a high-temperature furnace, typically operating at temperatures above 1000°C. This process ensures the formation of a homogeneous molten liquid.
- Forming and Shaping: The molten glass is shaped into large, flat sheets or ingots using techniques like rolling, drawing, or casting. The specific forming method depends on the desired dimensions and properties of the glass substrates.
- Annealing: The formed glass undergoes an annealing process to relieve internal stresses and improve its thermal stability. Annealing involves slowly cooling the glass at a controlled rate to prevent cracking or distortion.
- Cutting and Sizing: The annealed glass is cut into smaller pieces known as wafers. Precision cutting techniques, such as diamond sawing or laser cutting, are used to achieve the desired dimensions and surface quality of the wafers.
- Grinding and Polishing: The surfaces of the glass wafers are ground and polished to achieve the required flatness, smoothness, and surface quality. This step is crucial for ensuring uniformity and precision in semiconductor device fabrication.
- Cleaning and Surface Treatment: The glass wafers undergo thorough cleaning and surface treatment processes to remove contaminants and improve adhesion. Techniques such as chemical etching, ultrasonic cleaning, and plasma treatment are used to prepare the substrate surface for subsequent processing steps.
- Quality Control and Inspection: Rigorous quality control measures are implemented throughout the manufacturing process to inspect and characterize the glass substrates. Optical inspection, surface profilometry, and other characterization techniques are used to assess dimensional accuracy, surface quality, and overall integrity.
- Packaging and Storage: The finished glass wafers are carefully packaged and stored in a controlled environment to prevent contamination and ensure their stability. Proper storage conditions are essential to maintain the quality of the substrates until they are ready for use in semiconductor device fabrication.
By following these steps with precision and care, semiconductor manufacturers can produce high-quality Semiconductor Glass Substrates (SGS) that meet the demanding requirements of modern semiconductor fabrication processes, contributing to the production of reliable and high-performance semiconductor devices.
How much should a Semiconductor Glass Substrate (SGS) cost?
The cost of a Semiconductor Glass Substrate (SGS) can vary widely depending on several factors, including the size, thickness, quality, and specific requirements of the substrate. Here are some key factors that influence the cost of SGS:
- Material: The type and quality of glass used in the substrate significantly affect its cost. High-purity glass materials with superior properties, such as low thermal expansion coefficient and high chemical resistance, tend to be more expensive than standard glass materials.
- Size and Thickness: Larger and thicker glass substrates generally cost more due to the increased material and manufacturing costs associated with producing larger sizes and thicker layers of glass. Additionally, larger substrates may require specialized handling and processing equipment, further adding to the cost.
- Surface Quality: The level of surface quality required for the substrate, including flatness, smoothness, and absence of defects, can impact its cost. Substrates with tighter dimensional tolerances and higher surface quality specifications may require additional processing steps and quality control measures, leading to higher costs.
- Manufacturing Complexity: The complexity of the manufacturing process, including cutting, grinding, polishing, and surface treatment, can influence the cost of the substrate. More complex processes or specialized manufacturing techniques may require additional time, labor, and resources, increasing the overall cost.
- Volume and Scale: The volume and scale of production can also affect the cost of SGS. Bulk orders or larger production volumes may enable economies of scale, leading to lower unit costs. Conversely, smaller orders or custom requirements may incur higher costs due to setup and customization fees.
- Supplier and Market Dynamics: Market conditions, competition among suppliers, and fluctuations in raw material prices can impact the cost of SGS. Additionally, factors such as supplier reputation, lead times, and customer support services may influence pricing decisions.
Given these factors, the cost of Semiconductor Glass Substrates (SGS) can range from a few dollars to hundreds of dollars per unit, depending on the specific requirements and quality standards. It’s essential for semiconductor manufacturers to carefully consider their requirements and budget constraints when selecting SGS suppliers and negotiating pricing agreements.
What is Semiconductor Glass Substrate (SGS) base material?
The base material used for Semiconductor Glass Substrates (SGS) is typically high-purity glass, chosen for its specific properties that are suitable for semiconductor device fabrication processes. Common types of glass used as base materials for SGS include:
- Borosilicate Glass: Borosilicate glass is a type of glass containing boron trioxide as a major component. It is known for its low coefficient of thermal expansion, which means it expands and contracts minimally with changes in temperature. This property makes borosilicate glass suitable for applications requiring thermal stability, such as semiconductor fabrication.
- Fused Silica (Quartz): Fused silica, also known as quartz glass, is composed of silicon dioxide (SiO2) molecules arranged in a crystalline structure. It exhibits excellent optical transparency, high thermal stability, and low thermal expansion coefficient, making it ideal for use in high-temperature applications and semiconductor processing.
- Aluminosilicate Glass: Aluminosilicate glass is a type of glass containing both aluminum oxide (alumina) and silicon dioxide (silica). It offers a combination of thermal stability, chemical resistance, and mechanical strength, making it suitable for demanding semiconductor fabrication processes.
These base materials undergo specific manufacturing processes to produce glass substrates with precise dimensions, flatness, surface quality, and other characteristics required for semiconductor device fabrication. Depending on the specific application and performance requirements, semiconductor manufacturers may choose one of these types of glass or customize the composition to meet their needs.
Which company manufactures Semiconductor Glass Substrates (SGS)?
Currently, there are many companies specialized in the manufacturing of Semiconductor Glass Substrates (SGS). Some well-known companies include Corning, Schott, AGC, Hoya, among others. These companies possess advanced glass manufacturing technologies and facilities capable of producing high-quality glass substrates to meet the demands of the semiconductor industry.
In our company, we also have the capability to produce Semiconductor Glass Substrates. We have advanced glass processing equipment and technological expertise to manufacture high-quality SGS products that meet customer requirements. Here are some key advantages of our company’s SGS production capabilities:
- Advanced Manufacturing Facilities: We are equipped with advanced glass manufacturing equipment and process technologies to achieve precision processing and shaping of glass substrates, ensuring product dimensional accuracy and surface quality.
- Diverse Product Capabilities: Our company can customize SGS products in various sizes, thicknesses, and shapes according to customer requirements. Whether it’s standard specifications or custom designs, we can meet our customers’ needs.
- Strict Quality Control: We implement a rigorous quality control system to ensure that each batch of SGS products meets customer requirements and industry standards. From raw material procurement to finished product delivery, we closely monitor every step to ensure consistent product quality.
- Flexible Production Capacity: We have flexible production capacity to respond quickly to customer orders and requirements. Whether it’s small-batch production or large-scale orders, we can meet customer needs and ensure timely delivery.
In summary, our company has the professional capabilities and experience to produce Semiconductor Glass Substrates, providing customers with high-quality, reliable SGS products to support the development of the semiconductor industry.
What are the qualities of good customer service?
Good customer service encompasses several qualities that contribute to positive interactions and relationships with customers. Here are some key qualities:
- Responsive: Good customer service involves promptly addressing customer inquiries, concerns, and requests. Being responsive demonstrates attentiveness to customer needs and a commitment to providing timely assistance.
- Empathy: Empathy involves understanding and acknowledging the customer’s feelings, concerns, and perspectives. Empathetic customer service representatives listen actively, express understanding, and show compassion towards customers’ situations.
- Clear Communication: Effective communication is essential for providing good customer service. Customer service representatives should communicate clearly and concisely, using language that is easy for customers to understand. They should also actively listen to customers and provide accurate information and explanations.
- Problem-Solving Skills: Good customer service involves effectively resolving customer issues and problems. Customer service representatives should possess strong problem-solving skills, including the ability to analyze situations, identify solutions, and take appropriate action to resolve issues to the customer’s satisfaction.
- Professionalism: Professionalism involves conducting oneself with integrity, respect, and courtesy towards customers at all times. Customer service representatives should maintain a positive attitude, remain calm and composed, and treat customers with dignity and professionalism, regardless of the situation.
- Product Knowledge: Good customer service requires a deep understanding of the products or services being offered. Customer service representatives should be knowledgeable about their company’s offerings, including features, benefits, pricing, and policies, enabling them to provide accurate information and assistance to customers.
- Adaptability: Customer service representatives should be adaptable and flexible in their approach to meeting customer needs. They should be able to adjust their communication style, problem-solving strategies, and service delivery methods based on the unique preferences and requirements of each customer.
- Follow-Up: Following up with customers after resolving their issues or inquiries demonstrates commitment to customer satisfaction. Good customer service involves checking in with customers to ensure that their needs have been met, soliciting feedback, and addressing any additional concerns or questions they may have.
By embodying these qualities, businesses can cultivate strong customer relationships, foster loyalty, and differentiate themselves in the marketplace through exceptional customer service.
FAQs
What is a Semiconductor Glass Substrate (SGS)?
A Semiconductor Glass Substrate (SGS) is a specialized material used as the foundation for manufacturing semiconductor devices such as integrated circuits (ICs), microprocessors, and memory chips. It provides a stable and flat surface onto which semiconductor layers are deposited and patterned during fabrication.
What are the advantages of using Semiconductor Glass Substrates?
Semiconductor Glass Substrates offer advantages such as high thermal stability, excellent electrical insulation properties, precise dimensional control, and compatibility with semiconductor fabrication processes. They provide a reliable foundation for producing high-performance semiconductor devices.
What types of glass are commonly used for Semiconductor Glass Substrates?
Common types of glass used for Semiconductor Glass Substrates include borosilicate glass, fused silica (quartz), and aluminosilicate glass. These glasses are chosen for their specific properties such as low thermal expansion coefficient, high chemical resistance, and optical transparency.
How are Semiconductor Glass Substrates manufactured?
The manufacturing process of Semiconductor Glass Substrates involves steps such as glass melting, forming, cutting, grinding, polishing, cleaning, and surface treatment. These processes are carried out with precision to achieve the required dimensions, flatness, and surface quality of the substrates.
What are the applications of Semiconductor Glass Substrates?
Semiconductor Glass Substrates are used in various semiconductor applications, including microelectronics, optoelectronics, photovoltaics, and display technologies. They serve as the foundation for fabricating a wide range of semiconductor devices with different functionalities and performance requirements.
What factors should be considered when selecting Semiconductor Glass Substrates?
When selecting Semiconductor Glass Substrates, factors such as material properties, dimensional tolerances, surface quality, thermal stability, electrical insulation properties, and compatibility with fabrication processes should be considered to ensure optimal performance and reliability of the semiconductor devices.
Where can Semiconductor Glass Substrates be sourced from?
Semiconductor Glass Substrates can be sourced from specialized glass manufacturers, semiconductor equipment suppliers, and distributors. It’s essential to choose a reputable supplier with expertise in producing high-quality SGS products to meet specific application requirements.