Showa Denko MCL-E-795G Package Substrate Manufacturer
Professional Showa Denko MCL-E-795G Package Substrate Manufacturer, we mainly produce ultra-small bump pitch FC BGA/Flip Chip substrate, ultra-small trace and spacing BGA substrate and HDI microwave PCBs.
The Showa Denko MCL-E-795G package substrate is an advanced packaging solution renowned for its high performance. Utilizing cutting-edge materials and manufacturing techniques, this substrate exhibits excellent thermal and electrical properties, making it suitable for high-density integrated circuit packaging. Engineered with a multi-layered structure, it ensures robust signal transmission and power management. The MCL-E-795G substrate boasts exceptional reliability, capable of operating stably in various demanding environmental conditions. Additionally, it offers outstanding durability and longevity, laying a solid foundation for the reliability and performance of electronic products. Whether in telecommunications, automotive, industrial control, or consumer electronics, the MCL-E-795G stands as a dependable choice to meet the evolving technological demands.
What is the Showa Denko MCL-E-795G package substrate?
The Showa Denko MCL-E-795G package substrate is a high-performance substrate used in semiconductor packaging. It serves as a crucial component in the assembly of integrated circuits (ICs) and electronic devices. This substrate is designed with advanced materials and manufacturing processes to meet the demands of modern electronic applications.
The MCL-E-795G substrate offers several key features and benefits. Firstly, it provides excellent thermal conductivity, which is essential for efficient heat dissipation in semiconductor devices, ensuring their reliability and longevity. Additionally, it offers superior electrical properties, such as low signal loss and high-speed signal transmission capabilities, contributing to the overall performance of the electronic system.
Furthermore, the substrate exhibits exceptional dimensional stability and mechanical strength, maintaining its structural integrity even under harsh operating conditions. This reliability is crucial for ensuring the long-term functionality of electronic devices in various applications.
Moreover, the MCL-E-795G substrate is highly customizable, allowing manufacturers to tailor its specifications to meet specific requirements for different semiconductor packaging applications. This flexibility enables the development of innovative electronic products with optimized performance and cost-efficiency.
Overall, the Showa Denko MCL-E-795G package substrate represents a cutting-edge solution for semiconductor packaging, offering a combination of thermal, electrical, mechanical, and customization capabilities to meet the evolving needs of the electronics industry. Its advanced features contribute to the development of high-performance and reliable electronic devices across various sectors, including consumer electronics, automotive, telecommunications, and industrial applications.
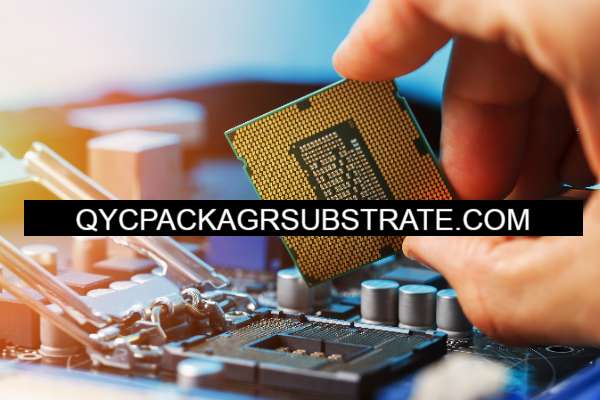
Showa Denko MCL-E-795G Package Substrate Manufacturer
What are the Showa Denko MCL-E-795G package substrate Design Guidelines?
Design guidelines for the Showa Denko MCL-E-795G package substrate typically include recommendations and specifications for various aspects of the substrate’s design and implementation. These guidelines aim to ensure optimal performance, reliability, and manufacturability of electronic devices utilizing the substrate. While specific guidelines may vary depending on the application and requirements, common aspects typically covered in the design guidelines may include:
- Material Specifications:Detailed specifications regarding the materials used in the substrate, including the composition, thickness, and properties of the substrate layers. This may include information on the dielectric material, conductive layers, and any other components integrated into the substrate.
- Thermal Management:Guidelines for managing thermal issues, including recommendations for thermal vias, thermal pads, and thermal dissipation strategies to ensure efficient heat transfer away from critical components.
- Electrical Design:Recommendations for optimizing electrical performance, such as signal routing, power distribution, and impedance control. This may include guidelines for signal integrity, power integrity, and minimizing electromagnetic interference (EMI).
- Package Layout:Guidelines for the layout and arrangement of components on the substrate, including considerations for component placement, routing channels, and spacing requirements to ensure proper functionality and manufacturability.
- Mechanical Considerations:Recommendations for mechanical design aspects, such as board thickness, mounting hole locations, and mechanical stress relief features to prevent substrate warpage or mechanical failures during assembly and operation.
- Manufacturability:Guidelines to facilitate efficient and reliable manufacturing processes, including recommendations for panelization, solder mask design, fiducial markers, and other features to support automated assembly and inspection processes.
- Reliability Requirements:Specifications for reliability testing and qualification requirements to ensure that the substrate meets industry standards and reliability targets for expected operating conditions and product lifetime.
- Environmental Considerations:Guidelines for environmental compliance and sustainability, including recommendations for material selection, compliance with regulatory requirements, and considerations for end-of-life disposal or recycling.
- Documentation and Communication:Recommendations for documenting the substrate design, including providing detailed design files, specifications, and communication with manufacturing partners to facilitate collaboration and ensure accurate implementation of the design.
By adhering to these design guidelines, engineers and designers can optimize the performance, reliability, and manufacturability of electronic devices utilizing the Showa Denko MCL-E-795G package substrate, ultimately contributing to the success of their products in the marketplace.
What is the Showa Denko MCL-E-795G package substrate Fabrication Process?
The fabrication process of the Showa Denko MCL-E-795G package substrate involves several steps to produce a high-performance substrate suitable for semiconductor packaging. While specific details may vary based on manufacturing facilities and technologies, a general overview of the fabrication process typically includes the following key steps:
- Substrate Preparation:The fabrication process begins with the preparation of the substrate base material. This often involves selecting high-quality materials, such as glass fiber-reinforced epoxy resin or other advanced composite materials, and cutting them into appropriately sized panels or sheets.
- Surface Treatment:Surface treatment processes are employed to enhance the adhesion properties of the substrate material and promote uniform coating deposition in subsequent steps. This may involve processes such as cleaning, surface roughening, or applying adhesion promoters.
- Layer Formation:The substrate is built up through the deposition and patterning of multiple layers of materials. This typically includes the deposition of dielectric layers, conductive layers (such as copper), and possibly additional functional layers, depending on the specific requirements of the substrate design.
- Lamination:The individual layers are laminated together using heat and pressure to form a cohesive substrate structure. This process ensures proper adhesion between the layers and eliminates voids or air pockets that could compromise the substrate’s integrity.
- Drilling and Via Formation:Holes are drilled or punched through the substrate to create vias, which provide electrical connections between different layers of the substrate. These vias may be filled with conductive materials or plated with metal to ensure reliable electrical conductivity.
- Plating:Conductive traces and features on the substrate are typically formed through electroplating processes. This involves depositing metal layers, such as copper, onto the substrate surface and into the vias to create the desired circuit patterns and interconnections.
- Etching and Patterning:Photolithography and etching processes are used to define the circuit patterns and features on the substrate surface. Photomasks are used to selectively expose areas of the substrate to chemical etchants, which remove unwanted material and define the final circuit layout.
- Surface Finish:Surface finish processes are applied to the substrate to protect the copper traces, improve solderability, and enhance the substrate’s performance. Common surface finishes include immersion tin, immersion silver, electroless nickel immersion gold (ENIG), and organic solderability preservatives (OSP).
- Final Inspection and Testing:The fabricated substrates undergo rigorous inspection and testing to ensure they meet quality standards and specifications. This may include visual inspection, electrical testing, dimensional measurements, and reliability testing to verify performance under various conditions.
- Packaging and Shipping:Once fabricated and tested, the substrates are packaged according to customer requirements and shipped to semiconductor manufacturers for assembly into electronic devices.
Overall, the fabrication process of the Showa Denko MCL-E-795G package substrate involves a series of precise and controlled steps to create a high-quality substrate that meets the demanding requirements of semiconductor packaging applications. Advanced manufacturing technologies and quality control measures are employed throughout the process to ensure the reliability and performance of the final product.
How do you manufacture a Showa Denko MCL-E-795G package substrate?
Manufacturing a Showa Denko MCL-E-795G package substrate involves a series of intricate steps designed to produce a high-quality substrate suitable for semiconductor packaging. While specific details of the process may vary based on the manufacturer’s facilities and technologies, here’s a general overview of the manufacturing process:
- Substrate Material Selection:High-quality base materials are selected, typically including glass fiber-reinforced epoxy resin or other advanced composite materials. These materials are chosen for their excellent thermal and mechanical properties.
- Preparation of Substrate Sheets:The selected substrate materials are cut into appropriately sized panels or sheets, which will serve as the foundation for the substrate.
- Surface Treatment:Surface treatment processes are employed to enhance the adhesion properties of the substrate material. This may involve cleaning, surface roughening, or applying adhesion promoters to ensure uniform coating deposition in subsequent steps.
- Layer Deposition:Multiple layers of materials are deposited onto the substrate sheets using various techniques such as vacuum deposition, chemical vapor deposition (CVD), or sputtering. These layers typically include dielectric materials and conductive materials such as copper.
- Lamination:The individual layers are laminated together using heat and pressure to form a cohesive substrate structure. This process ensures proper adhesion between the layers and eliminates voids or air pockets.
- Drilling and Via Formation:Holes are drilled or punched through the substrate to create vias, which provide electrical connections between different layers of the substrate. These vias may be filled with conductive materials or plated with metal to ensure reliable electrical conductivity.
- Pattern Transfer:Photolithography processes are used to define the circuit patterns and features on the substrate surface. Photomasks are employed to selectively expose areas of the substrate to chemical etchants, which remove unwanted material and define the final circuit layout.
- Conductor Plating:Conductive traces and features on the substrate are formed through electroplating processes. This involves depositing metal layers, such as copper, onto the substrate surface and into the vias to create the desired circuit patterns and interconnections.
- Surface Finish:Surface finish processes are applied to the substrate to protect the copper traces, improve solderability, and enhance the substrate’s performance. Common surface finishes include immersion tin, immersion silver, electroless nickel immersion gold (ENIG), and organic solderability preservatives (OSP).
- Quality Control:The fabricated substrates undergo rigorous inspection and testing to ensure they meet quality standards and specifications. This may include visual inspection, electrical testing, dimensional measurements, and reliability testing to verify performance under various conditions.
- Packaging and Shipping:Once fabricated and tested, the substrates are packaged according to customer requirements and shipped to semiconductor manufacturers for assembly into electronic devices.
Throughout the manufacturing process, advanced equipment, precise control mechanisms, and quality assurance measures are employed to ensure the reliability, performance, and consistency of the Showa Denko MCL-E-795G package substrates.
How much should a Showa Denko MCL-E-795G package substrate cost?
The cost of a Showa Denko MCL-E-795G package substrate can vary depending on several factors, including the specific requirements of the customer, the quantity ordered, and market conditions. Additionally, pricing may be influenced by factors such as customization options, substrate size, complexity of the design, and any additional services or features requested.
Since I don’t have access to real-time pricing information, I can’t provide an exact cost for the substrate. However, typically, high-performance package substrates like the MCL-E-795G are precision-engineered products manufactured with advanced materials and processes, which can contribute to their higher cost compared to standard substrates.
To obtain accurate pricing information for the Showa Denko MCL-E-795G package substrate, it’s best to directly contact Showa Denko or authorized distributors for a customized quote based on your specific requirements and order volume. They can provide you with pricing details, including any applicable discounts or bulk pricing options. Additionally, you may consider requesting quotes from multiple suppliers to compare prices and find the best deal for your needs.
What is the base material of the Showa Denko MCL-E-795G package substrate?
The base material of the Showa Denko MCL-E-795G package substrate is typically a high-performance composite material, often consisting of a glass fiber-reinforced epoxy resin (FR-4) or similar advanced composite. This material provides a sturdy foundation with excellent thermal and mechanical properties suitable for semiconductor packaging applications.
Glass fiber-reinforced epoxy resin is commonly chosen for package substrates due to its desirable characteristics, including high strength, dimensional stability, and good electrical insulation properties. Additionally, it offers relatively low cost compared to other high-performance substrate materials, making it a popular choice for a wide range of electronic applications.
The specific composition and formulation of the base material may vary depending on the requirements of the substrate design and the desired performance characteristics. Manufacturers like Showa Denko may also offer variations of their substrate products with different base materials tailored to specific applications or performance requirements.
Which companies manufacture Showa Denko MCL-E-795G package substrates?
Manufacturing of Showa Denko MCL-E-795G package substrates is typically undertaken by specialized semiconductor package substrate manufacturing companies. These companies possess advanced production equipment, technology, and professional teams to ensure the production of substrates that meet high standards.
Our company is one such manufacturer. As a professional semiconductor package substrate manufacturer, we have years of experience and expertise to meet customers’ demands for high-quality substrates, including Showa Denko MCL-E-795G package substrates.
We employ advanced manufacturing techniques and strict quality control standards to ensure that each substrate meets customer requirements. Our production equipment and lines are meticulously designed and optimized for efficient and precise manufacturing processes, ensuring product consistency and stability.
Furthermore, we prioritize communication and collaboration with customers to provide customized solutions tailored to their specific needs. Whether it’s material selection, process optimization, or product characteristics, we can adjust and optimize according to customer requirements to meet the needs of different industries and applications.
In summary, our company possesses the technology, equipment, and experience necessary to manufacture Showa Denko MCL-E-795G package substrates and provide high-quality, customized products and services to support our customers’ projects reliably.
What are the qualities of good customer service?
Good customer service is characterized by several key qualities that contribute to positive interactions and relationships between businesses and their customers. Some of these qualities include:
- Responsiveness:Good customer service involves promptly addressing customer inquiries, concerns, and requests. Being responsive shows customers that their needs are valued and that the business is committed to assisting them in a timely manner.
- Empathy:Empathizing with customers’ situations and emotions is crucial for understanding their perspectives and providing personalized support. Showing empathy helps build trust and rapport with customers, even in challenging situations.
- Clear Communication: Effective communication is essential for conveying information clearly and accurately to customers. Good customer service representatives should be able to explain products, policies, and solutions in a way that is easy for customers to understand.
- Problem-Solving Skills:Resolving customer issues and problems efficiently and effectively is a hallmark of good customer service. This involves identifying root causes, exploring solutions, and taking proactive steps to address concerns to the customer’s satisfaction.
- Professionalism:Maintaining professionalism in all interactions with customers, including remaining calm, courteous, and respectful, regardless of the circumstances, is important for fostering a positive customer experience.
- Product Knowledge:Having a deep understanding of the company’s products or services allows customer service representatives to provide accurate information, make relevant recommendations, and address customer questions or concerns effectively.
- Follow-Up:Following up with customers after resolving an issue or completing a transaction demonstrates commitment to their satisfaction and helps ensure that their needs have been met.
- Adaptability:Being adaptable and flexible in responding to customers’ diverse needs and preferences is essential for providing personalized support and accommodating varying circumstances.
- Consistency:Providing consistent service across all customer touchpoints, whether in-person, over the phone, or online, helps build trust and confidence in the brand.
- Continuous Improvement:Striving for continuous improvement by soliciting customer feedback, analyzing trends, and implementing changes based on insights helps businesses enhance their customer service practices over time.
Overall, good customer service involves a combination of responsiveness, empathy, communication skills, problem-solving abilities, professionalism, product knowledge, follow-up, adaptability, consistency, and a commitment to continuous improvement. By prioritizing these qualities, businesses can build strong relationships with their customers and differentiate themselves in the marketplace.
FAQs
What is Showa Denko MCL-E-795G package substrate?
Showa Denko MCL-E-795G is a high-performance package substrate used in semiconductor packaging. It offers excellent thermal conductivity, electrical properties, and mechanical strength, making it suitable for various electronic applications.
What are the key features of Showa Denko MCL-E-795G package substrate?
Key features include high thermal conductivity for efficient heat dissipation, superior electrical properties for signal integrity, and excellent dimensional stability and mechanical strength.
What are the applications of Showa Denko MCL-E-795G package substrate?
Showa Denko MCL-E-795G substrates are used in a wide range of electronic devices, including consumer electronics, automotive electronics, telecommunications equipment, and industrial applications.
What are the benefits of using Showa Denko MCL-E-795G package substrate?
Benefits include improved reliability and longevity of electronic devices due to efficient heat dissipation, enhanced electrical performance, and structural integrity under harsh conditions.
How can I obtain Showa Denko MCL-E-795G package substrates?
Showa Denko MCL-E-795G substrates can be obtained directly from Showa Denko or through authorized distributors. Contacting the company or its distributors will provide information on pricing, availability, and ordering processes.
Can Showa Denko MCL-E-795G package substrates be customized?
Yes, Showa Denko MCL-E-795G substrates can be customized to meet specific requirements, such as substrate size, thickness, electrical properties, and surface finish, depending on the application needs.
What are the environmental considerations for Showa Denko MCL-E-795G package substrates?
Showa Denko MCL-E-795G substrates may adhere to environmental regulations and standards, and the company may provide information on material composition, compliance, and recyclability.
Are there any design guidelines available for Showa Denko MCL-E-795G package substrates?
Yes, design guidelines for Showa Denko MCL-E-795G substrates may be available to assist customers in optimizing substrate layout, thermal management, electrical design, and manufacturability.
How can I ensure the reliability of electronic devices using Showa Denko MCL-E-795G package substrates?
Following recommended design guidelines, conducting thorough testing, and adhering to best practices in substrate assembly and integration can help ensure the reliability of electronic devices using Showa Denko MCL-E-795G substrates.
Are there any warranty or support services available for Showa Denko MCL-E-795G package substrates?
Showa Denko or its authorized distributors may offer warranty coverage and support services to address any issues or concerns with the performance or quality of MCL-E-795G substrates.