TU862HF Materials PCB Manufacturer
TU862HF Materials PCB Manufacturer,TU862HF Materials PCB is a specialized laminate for high-frequency circuits, known for its excellent electrical performance and stability. Its substrate is made of polytetrafluoroethylene (PTFE), offering low dielectric constant and low loss factor, ideal for applications requiring precise signal transmission. The copper foil conductive layer ensures reliable electrical connections and signal transmission. TU862HF PCB is widely used in communications, radar, aerospace, and other fields, providing reliable performance and signal integrity for high-frequency electronic devices.
What is TU862HF Materials PCB?
TU862HF is a type of material used in printed circuit boards (PCBs). It’s a high-frequency laminate designed for applications where signal integrity and high-frequency performance are critical, such as in RF (radio frequency) and microwave circuits.
This material typically consists of a high-performance substrate, such as PTFE (polytetrafluoroethylene), combined with a conductive layer of copper. PTFE is known for its low dielectric constant, low loss tangent, and stable electrical properties over a wide range of frequencies, making it ideal for high-frequency applications.
TU862HF PCBs offer excellent electrical performance, with low insertion loss and minimal signal distortion, making them suitable for use in telecommunications, aerospace, defense, and other industries where high-frequency signals are prevalent. Additionally, they often exhibit good thermal stability and mechanical strength, ensuring reliability in demanding environments.
When designing PCBs using TU862HF material, engineers must consider its unique electrical characteristics and tailor the layout and design to optimize performance. Proper impedance matching, signal routing, and grounding techniques are essential for maximizing the benefits of this high-frequency material.
Overall, TU862HF PCBs provide designers with a reliable solution for high-frequency applications where signal integrity and performance are paramount.
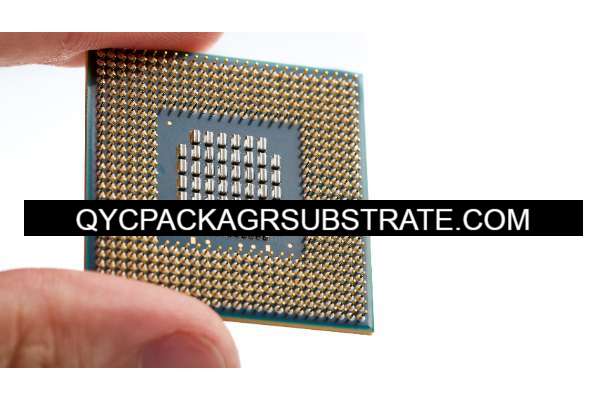
TU862HF Materials PCB Manufacturer
What are the TU862HF Materials PCB Design Guidelines?
Designing PCBs using TU862HF material requires careful consideration of its unique electrical characteristics to ensure optimal performance. Here are some general design guidelines for TU862HF materials:
- Impedance Matching: Maintain consistent impedance throughout the transmission lines to minimize signal reflections and ensure signal integrity. Use controlled impedance traces with appropriate widths and spacing according to the dielectric constant and thickness of TU862HF.
- Signal Routing: Route high-frequency traces with short, direct paths to minimize signal loss and interference. Avoid sharp bends and corners, as these can cause impedance mismatches and signal distortion. Use smooth, gradual curves instead.
- Grounding:Implement a solid ground plane beneath signal layers to provide a low-impedance return path for signals and reduce electromagnetic interference (EMI). Ensure good via stitching to connect all ground planes and minimize ground loops.
- Component Placement: Place high-frequency components close together to minimize trace lengths and reduce parasitic capacitance and inductance. Position components to minimize crosstalk and interference between adjacent traces.
- Via Design: Use high-quality plated-through vias (PTH) with low impedance to connect signal layers and ground planes. Minimize the number of vias in high-frequency signal paths to reduce parasitic effects.
- Decoupling Capacitors: Place decoupling capacitors strategically near high-frequency components to filter out noise and provide stable power distribution. Use low-inductance capacitors with short traces to minimize impedance.
- Thermal Management: Consider thermal management strategies to dissipate heat generated by high-power components. Ensure adequate spacing between heat-generating components and other sensitive circuitry to prevent thermal interference.
- Electromagnetic Compatibility (EMC): Design PCBs to meet EMC requirements by minimizing emissions and susceptibility to external interference. Use shielding techniques, such as grounded enclosures or shielding layers, where necessary.
- Simulation and Testing: Perform electromagnetic simulation and signal integrity analysis using specialized software tools to validate the design and ensure compliance with performance specifications. Conduct thorough testing of prototypes to verify electrical performance.
By following these design guidelines and leveraging the unique characteristics of TU862HF material, engineers can develop high-performance PCBs optimized for high-frequency applications with excellent signal integrity and reliability.
What is the TU862HF Materials PCB Fabrication Process?
The fabrication process for PCBs using TU862HF material is similar to that of traditional PCBs, with some considerations specific to the characteristics of TU862HF. Here’s a general outline of the fabrication process:
- Material Preparation: Obtain TU862HF laminate sheets with the desired thickness and copper foil pre-bonded to one or both sides. Ensure that the laminate material is stored and handled according to manufacturer guidelines to prevent damage or contamination.
- Preparation of Design Files: Create or obtain the PCB design files, including the layout, traces, pads, and drill information, using PCB design software. Ensure that the design complies with the electrical and mechanical requirements of the intended application and the manufacturing capabilities of the fabrication facility.
- Preparation of Substrate: Cut the TU862HF laminate sheets to the required size based on the PCB design. Clean the substrate surfaces thoroughly to remove any contaminants that could affect adhesion or solderability.
- Copper Etching: Use chemical etching or mechanical milling techniques to remove excess copper from the laminate surface, leaving behind the desired traces and patterns according to the PCB design. Ensure precise control of etching parameters to achieve the desired trace widths and clearances.
- Drilling: Drill holes for through-hole components and vias using precision drilling equipment. Ensure accurate alignment of the drill holes with the PCB layout to maintain electrical connectivity and mechanical stability.
- Plating:Plate the drilled holes with copper to create plated-through vias, ensuring electrical continuity between different layers of the PCB. Follow industry-standard plating processes, such as electroless or electrolytic plating, to deposit a thin layer of copper inside the holes.
- Layer Lamination: If the PCB design includes multiple layers, laminate the individual layers together using heat and pressure to create a single, multi-layered PCB stack. Ensure proper alignment of the layers to maintain signal integrity and electrical connectivity.
- Final Etching and Surface Finishing: Perform a final etching step to remove any excess copper and define the outer edges of the PCB. Apply surface finish options such as HASL (Hot Air Solder Leveling), ENIG (Electroless Nickel Immersion Gold), or OSP (Organic Solderability Preservatives) to improve solderability and protect the copper traces from oxidation.
- Inspection and Testing: Inspect the finished PCBs for defects, such as shorts, opens, or dimensional inaccuracies, using visual inspection, automated optical inspection (AOI), or electrical testing techniques. Ensure that the fabricated PCBs meet the quality standards and specifications outlined in the design requirements.
- Final Packaging: Package the finished PCBs according to customer requirements, including protective packaging materials and labeling for identification and traceability during assembly and integration into electronic systems.
Throughout the fabrication process, it’s essential to adhere to industry standards and best practices to ensure the quality, reliability, and performance of the TU862HF PCBs for their intended applications. Collaboration with experienced PCB manufacturers familiar with high-frequency materials and processes can also help optimize the fabrication process and achieve desired results.
How do you manufacture a TU862HF Materials PCB?
Manufacturing a PCB using TU862HF material involves several steps, including material preparation, layer fabrication, drilling, plating, etching, and finishing. Here’s a detailed overview of the manufacturing process:
- Material Selection: Choose TU862HF laminate material with the desired thickness and copper foil configuration based on the PCB design requirements and high-frequency performance needs.
- Preparation of Design Files: Create or obtain the PCB design files, including the layout, traces, pads, and drill information, using PCB design software. Ensure that the design meets the electrical and mechanical specifications of the intended application and the capabilities of the fabrication facility.
- Laminate Preparation: Cut the TU862HF laminate sheets to the required size based on the PCB design. Clean the laminate surfaces thoroughly to remove any contaminants that could affect adhesion or solderability.
- Copper Cladding Preparation: If the laminate sheets do not already have copper foil bonded to them, laminate copper foil onto one or both sides of the substrate using heat and pressure. Ensure uniform adhesion and thickness of the copper foil across the laminate surface.
- Photoresist Application: Apply a layer of photoresist material onto the copper-clad laminate surface using a roller or spray-coating method. Ensure uniform coverage and thickness of the photoresist layer.
- Exposure and Development: Expose the photoresist layer to UV light through a photomask containing the PCB pattern. Develop the exposed photoresist to remove the unexposed areas, revealing the underlying copper traces and pads.
- Etching: Use chemical etching or mechanical milling techniques to remove the exposed copper from the laminate surface, leaving behind the desired traces and patterns according to the PCB design. Control the etching parameters carefully to achieve precise trace widths and clearances.
- Drilling:Drill holes for through-hole components and vias using precision drilling equipment. Ensure accurate alignment of the drill holes with the PCB layout to maintain electrical connectivity and mechanical stability.
- Plating: Plate the drilled holes with copper to create plated-through vias, ensuring electrical continuity between different layers of the PCB. Follow industry-standard plating processes, such as electroless or electrolytic plating, to deposit a thin layer of copper inside the holes.
- Surface Finishing: Apply surface finish options such as HASL (Hot Air Solder Leveling), ENIG (Electroless Nickel Immersion Gold), or OSP (Organic Solderability Preservatives) to improve solderability and protect the copper traces from oxidation.
- Inspection and Testing: Inspect the finished PCBs for defects, such as shorts, opens, or dimensional inaccuracies, using visual inspection, automated optical inspection (AOI), or electrical testing techniques. Ensure that the fabricated PCBs meet the quality standards and specifications outlined in the design requirements.
- Final Packaging: Package the finished PCBs according to customer requirements, including protective packaging materials and labeling for identification and traceability during assembly and integration into electronic systems.
Throughout the manufacturing process, it’s crucial to maintain strict quality control measures and adhere to industry standards to ensure the reliability, performance, and functionality of the TU862HF PCBs for their intended applications. Collaboration with experienced PCB manufacturers familiar with high-frequency materials and processes can also help optimize the manufacturing process and achieve desired results.
How much should a TU862HF Materials PCB cost?
The cost of a TU862HF materials PCB can vary significantly depending on various factors such as the size, complexity, layer count, and quantities ordered, as well as additional features like surface finish and impedance control. However, as a high-frequency material with specialized properties, TU862HF typically commands a higher price compared to standard FR-4 or other PCB materials.
On average, the cost of a single TU862HF PCB prototype with standard specifications and moderate complexity can range from $50 to $200 USD. This price includes the cost of materials, fabrication, and any additional services such as solder mask, silkscreen, and electrical testing.
For larger production quantities, the cost per unit can decrease due to economies of scale, with prices ranging from $10 to $50 USD per PCB for volumes of a few hundred to several thousand units.
It’s important to note that prices can vary among PCB manufacturers based on their capabilities, expertise, location, and production volume. Additionally, custom requirements such as special tolerances, tight impedance control, or specific certifications may incur additional costs.
To get an accurate cost estimate for a TU862HF materials PCB, it’s recommended to contact multiple PCB manufacturers and provide detailed specifications and quantities for a customized quote. Additionally, consider factors such as lead time, quality assurance, and customer support when selecting a manufacturer to ensure the best value for your project.
What is TU862HF Materials PCB base material?
TU862HF is a type of high-frequency laminate used as the base material for PCBs. It typically consists of a substrate made from PTFE (polytetrafluoroethylene), also known by the brand name Teflon, combined with a layer of conductive material, such as copper foil bonded to one or both sides.
The PTFE substrate provides excellent electrical properties for high-frequency applications, including a low dielectric constant (εr), low dissipation factor (Df), and stable electrical performance over a wide range of frequencies. These properties make PTFE an ideal choice for applications where signal integrity and high-frequency performance are critical, such as in RF (radio frequency) and microwave circuits.
The copper foil bonded to the PTFE substrate serves as the conductive layer for routing electrical signals on the PCB. Copper is chosen for its high conductivity and excellent solderability, allowing for reliable electrical connections between components.
Overall, TU862HF PCBs leverage the unique properties of PTFE as the base material to provide exceptional electrical performance, making them suitable for demanding high-frequency applications in industries such as telecommunications, aerospace, defense, and radar systems.
Which company makes TU862HF Materials PCB?
TU862HF materials PCB are produced by multiple PCB material suppliers, including well-known high-frequency material suppliers such as Isola, Rogers Corporation, and Taconic. These companies have rich experience and technological strength in the field of high-frequency PCBs, capable of providing material solutions that meet various high-frequency application requirements.
For our company, we can also manufacture TU862HF materials PCB. As a professional PCB manufacturer, we have advanced production equipment, experienced engineering teams, and a strict quality control system. Our production processes and technologies meet the requirements of high-frequency PCB manufacturing, including precision processing of complex circuit boards, optimized signal transmission performance, and high-quality surface treatments.
We can provide the following services and advantages:
- Professional Team:We have an experienced engineering team capable of providing comprehensive support from design consultation to production optimization.
- Advanced Equipment: We invest in advanced manufacturing equipment and technologies, including high-precision CNC machining equipment and automated production lines, to ensure production efficiency and product quality.
- Quality Assurance: We adopt strict quality control procedures, including inspections and testing at every manufacturing stage, to ensure that products meet customer requirements and international standards.
- Customization Services: We can customize TU862HF materials PCBs according to customer specifications and requirements, including different layer counts, thicknesses, surface treatments, and special process requirements.
- Timely Delivery: We can provide fast and reliable delivery services according to customer time requirements, ensuring that projects are completed on time.
In summary, as a professional PCB manufacturer, our company has the technical capabilities, production capacity, and service level required to manufacture TU862HF materials PCBs. We are committed to providing customers with high-quality, high-performance PCB products and working together for mutual development.
What are the 7 qualities of good customer service?
Good customer service is characterized by several key qualities that contribute to positive interactions and relationships between businesses and their customers. Here are seven qualities of good customer service:
- Responsiveness: Good customer service involves being prompt and proactive in addressing customer inquiries, concerns, and requests. Responding to customer inquiries in a timely manner demonstrates respect for their time and needs.
- Empathy:Empathy is the ability to understand and share the feelings of others. Good customer service representatives demonstrate empathy by actively listening to customers, acknowledging their concerns, and showing understanding and compassion.
- Clarity: Providing clear and concise communication is essential for good customer service. Clear communication helps customers understand products, services, policies, and solutions, reducing confusion and frustration.
- Professionalism: Professionalism encompasses various aspects of conduct, including politeness, respectfulness, and integrity. Good customer service representatives maintain professionalism in their interactions with customers, regardless of the circumstances.
- Problem-Solving Skills: Good customer service involves effectively addressing customer issues and resolving problems in a satisfactory manner. Strong problem-solving skills enable representatives to identify solutions, make decisions, and take appropriate actions to meet customer needs.
- Consistency: Consistency is key to building trust and credibility with customers. Providing consistent service experiences across different channels and interactions ensures reliability and predictability, leading to increased customer satisfaction and loyalty.
- Customer Focus: Good customer service is centered around the needs and preferences of the customer. Customer-focused organizations prioritize customer satisfaction and strive to exceed customer expectations by delivering personalized, relevant, and valuable experiences.
By embodying these qualities, businesses can create positive customer service experiences that foster trust, loyalty, and long-term relationships with their customers.
FAQs
What is TU862HF material?
TU862HF is a type of high-frequency laminate used in the fabrication of printed circuit boards (PCBs). It consists of a substrate made from PTFE (polytetrafluoroethylene), known for its excellent electrical properties, combined with a conductive layer of copper.
What are the key properties of TU862HF material?
TU862HF material offers low dielectric constant (εr), low dissipation factor (Df), and stable electrical performance over a wide range of frequencies. It is suitable for high-frequency applications where signal integrity and performance are critical.
What are the advantages of using TU862HF material for PCBs?
TU862HF material provides excellent electrical performance, including low insertion loss, minimal signal distortion, and high thermal stability. It is well-suited for applications such as RF (radio frequency) and microwave circuits, telecommunications, aerospace, and defense.
How does TU862HF material compare to other PCB materials?
Compared to standard PCB materials like FR-4, TU862HF offers superior high-frequency performance and signal integrity. It has lower loss tangent and better impedance control, making it ideal for applications requiring precise transmission of high-frequency signals.
Can TU862HF material PCBs be manufactured with standard processes?
Yes, TU862HF material PCBs can be fabricated using standard PCB manufacturing processes, including etching, drilling, plating, and surface finishing. However, special attention is needed to ensure proper handling and processing of the high-frequency laminate to maintain its electrical properties.
What design considerations are important for TU862HF material PCBs?
Designing TU862HF material PCBs requires attention to impedance matching, signal routing, grounding, and thermal management to optimize high-frequency performance and signal integrity. Proper layout and design techniques are essential to maximize the benefits of this specialized material.
Where can TU862HF material PCBs be used?
TU862HF material PCBs are used in various high-frequency applications, including telecommunications equipment, radar systems, aerospace and defense electronics, medical devices, and test and measurement instruments.
Is TU862HF material readily available from PCB manufacturers?
Yes, TU862HF material is available from several PCB material suppliers and manufacturers specializing in high-frequency laminates. Customers can specify TU862HF material when ordering PCBs for their specific application requirements.