Ultra-thin hard PCB
Ultra-thin hard PCB Manufacturer, Not Flex PCB, we made the Hard PCB with Ultra-thin thcikness. the finished board thickness are from 3mil, 4mil, 5mil to 8mil. if your boards are 4 layer to 6 layers. we can finished the PCB thickness with 8mil to 10mil. We’ll make the board thinner, as you requested.
Ultra-thin hard PCBs represent the pinnacle of modern circuit board technology, embodying a delicate balance between minimal thickness and robust durability. These PCBs, often measuring fractions of a millimeter in thickness, are engineered to withstand the rigors of demanding applications where space constraints are paramount. Crafted from advanced materials such as polyimide or liquid crystal polymer, they offer exceptional thermal stability and mechanical strength while maintaining a slim profile.
The design of ultra-thin hard PCBs prioritizes efficiency and performance, with meticulous attention given to component placement, trace routing, and thermal management. Despite their diminutive size, these PCBs exhibit remarkable resilience, capable of supporting complex electronic systems found in smartphones, wearables, medical devices, and aerospace equipment.
Manufacturing ultra-thin hard PCBs requires precision and expertise, leveraging cutting-edge fabrication techniques to achieve the desired thickness without compromising integrity. While challenging to produce, the benefits of ultra-thin hard PCBs—such as space-saving design, reduced weight, and enhanced functionality—make them indispensable in today’s technology-driven world.
What is an Ultra-thin hard PCB?
We are a professional Ultra-thin hard PCB Manufacturer, we mainly produce ultra-small bump pitch substrate, ultra-small trace and spacing packaging substrate and PCBs.
An ultra-thin hard PCB (Printed Circuit Board) is a type of PCB that is exceptionally thin while still maintaining rigidity and durability. These PCBs are typically used in applications where space is limited or weight needs to be minimized, such as in mobile devices, wearables, medical devices, and aerospace applications.
The “ultra-thin” aspect refers to the thickness of the PCB, which is usually significantly thinner than standard PCBs. These PCBs can be as thin as a fraction of a millimeter, making them ideal for applications where thickness is a critical factor.
Despite their thinness, ultra-thin hard PCBs are designed to be robust and reliable, with materials and construction methods chosen to ensure they can withstand the rigors of their intended application environment.
Overall, ultra-thin hard PCBs offer a combination of compactness, light weight, and durability, making them suitable for a wide range of high-tech and space-constrained applications.
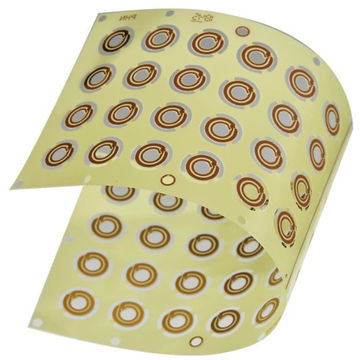
Ultra-thin hard PCB
What are the Ultra-thin hard PCB Design Guidelines?
Designing ultra-thin hard PCBs requires careful attention to several key guidelines to ensure the reliability, manufacturability, and performance of the board. Here are some general design guidelines for ultra-thin hard PCBs:
- Thickness Considerations: Ultra-thin PCBs are typically defined as having a thickness of less than 0.8mm, but they can be even thinner, depending on the application. Understand the minimum thickness requirements based on the mechanical constraints of your application.
- Material Selection: Choose materials that provide the necessary rigidity and durability while maintaining a thin profile. Common substrate materials for ultra-thin PCBs include FR-4, polyimide (PI), and liquid crystal polymer (LCP).
- Layer Count: Limit the number of layers to reduce thickness and cost. Use advanced routing techniques to maximize signal integrity and minimize electromagnetic interference (EMI) while keeping the layer count low.
- Component Placement: Optimize component placement to minimize the overall footprint of the PCB while ensuring proper clearance and spacing between components. Consider component height and size constraints to maintain a thin profile.
- Trace Width and Spacing:Use appropriate trace widths and spacing to accommodate the manufacturing process and ensure signal integrity. Thinner traces may be necessary to reduce overall thickness, but be mindful of current carrying capacity and impedance requirements.
- Vias and Plated Through-Holes (PTH): Minimize the use of vias and PTHs to reduce thickness and manufacturing complexity. Consider using blind vias or buried vias to maximize routing density while maintaining a thin profile.
- Thermal Management: Implement effective thermal management techniques to dissipate heat generated by components in the limited space available. Consider the use of heat sinks, thermal vias, and other thermal management solutions.
- Flexibility vs. Rigidity: Balance the need for flexibility with the requirement for rigidity. Ultra-thin PCBs may exhibit some flexibility due to their thin profile, but ensure that they maintain sufficient rigidity to withstand mechanical stress and handling.
- Manufacturability: Design the PCB with manufacturability in mind, considering the capabilities and limitations of the chosen fabrication processes. Consult with your PCB manufacturer early in the design process to address any manufacturability concerns.
- Testing and Quality Control: Develop a comprehensive testing and quality control plan to verify the performance and reliability of the ultra-thin PCBs. Consider performing mechanical testing, electrical testing, and reliability testing to ensure compliance with specifications.
By following these design guidelines, you can create ultra-thin hard PCBs that meet the stringent requirements of modern electronic devices while maintaining reliability and performance.
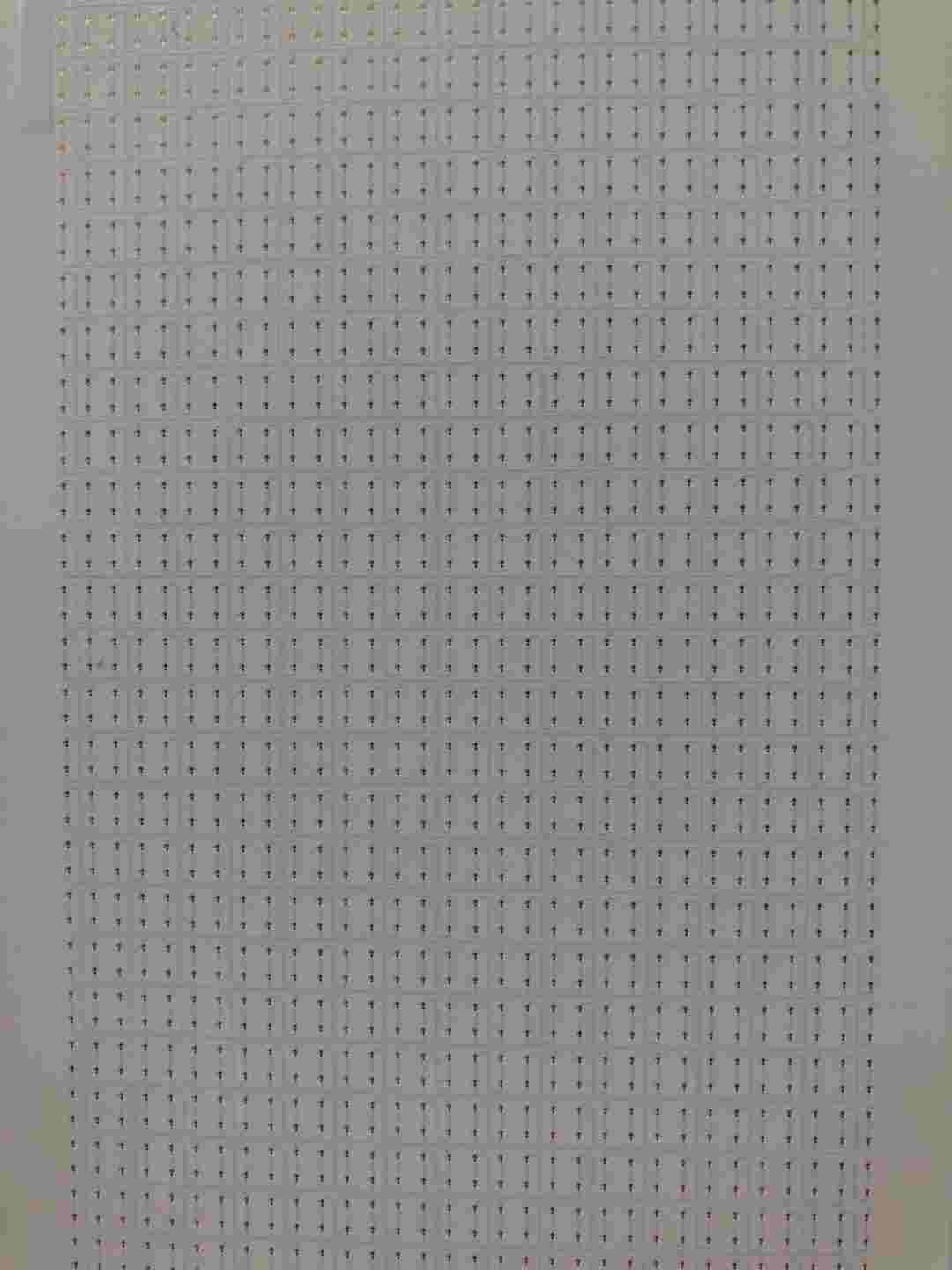
Ultra-thin hard PCB
What is the Ultra-thin hard PCB Fabrication Process?
The fabrication process for ultra-thin hard PCBs is similar to that of standard PCBs but with some additional considerations due to their thinness and specific material properties. Here’s a general overview of the fabrication process for ultra-thin hard PCBs:
- Design: The process begins with the PCB design, where the layout, component placement, trace routing, and layer stack-up are defined according to the requirements of the application. Design software such as Altium Designer, Cadence Allegro, or Eagle CAD is typically used for this purpose.
- Material Selection: Choose appropriate substrate materials that provide the necessary rigidity and durability while maintaining a thin profile. Common materials for ultra-thin PCBs include FR-4, polyimide (PI), and liquid crystal polymer (LCP).
- Preparation of Substrate: The chosen substrate material is prepared by cutting it to the required dimensions and cleaning it to remove any contaminants that could affect adhesion or solderability.
- Layer Stack-up: If the PCB design requires multiple layers, the individual layers of substrate material are laminated together using heat and pressure to form a single composite structure.
- Copper Cladding: Copper foil is laminated onto the substrate surfaces using heat and pressure. The copper foil thickness is typically specified according to the design requirements for trace width, current carrying capacity, and impedance control.
- Photoresist Application: A layer of photoresist is applied to the surface of the copper-clad substrate. The photoresist serves as a mask for the subsequent etching process.
- Exposure and Development: The PCB design is transferred onto the photoresist layer using a photomask and exposure to ultraviolet light. The exposed photoresist is then developed to remove the unexposed areas, leaving behind the pattern of traces and pads.
- Etching: The exposed copper is etched away using an etchant solution, leaving behind the desired copper traces and pads on the substrate surface.
- Plating: Through-holes, vias, and other features requiring plated connections are created using electroplating processes. This involves depositing a thin layer of metal (typically copper) onto the exposed surfaces of the PCB to create conductive pathways.
- Surface Finish: The PCB surface is coated with a surface finish to protect the copper traces from oxidation and improve solderability. Common surface finishes for ultra-thin PCBs include electroless nickel immersion gold (ENIG) and immersion tin.
- Final Inspection and Testing: The finished ultra-thin PCBs undergo a series of inspections and tests to ensure they meet the required specifications for dimensional accuracy, electrical continuity, and reliability.
- Assembly: Once the PCBs pass inspection, they are ready for component assembly. Surface mount components (SMD) and through-hole components are soldered onto the PCB using automated assembly equipment.
- Quality Control: After assembly, the PCBs undergo final testing and quality control checks to verify functionality and reliability before they are integrated into the final product.
Throughout the fabrication process, it’s essential to carefully monitor and control parameters such as temperature, pressure, and chemical concentrations to ensure consistent quality and reliability of the ultra-thin hard PCBs. Collaboration with experienced PCB manufacturers familiar with ultra-thin substrate materials and fabrication techniques can help ensure successful production.
How do you manufacture an Ultra-thin hard PCB?
Manufacturing ultra-thin hard PCBs involves several specialized processes to achieve the desired thickness and mechanical properties while maintaining reliability and performance. Here’s a step-by-step overview of the manufacturing process:
- Material Selection: Choose substrate materials that provide the necessary rigidity and durability while maintaining a thin profile. Common materials for ultra-thin hard PCBs include FR-4, polyimide (PI), and liquid crystal polymer (LCP).
- Preparation of Substrate:The chosen substrate material is prepared by cutting it to the required dimensions and cleaning it to remove any contaminants that could affect adhesion or solderability.
- Layer Stack-up: If the PCB design requires multiple layers, the individual layers of substrate material are laminated together using heat and pressure to form a single composite structure.
- Copper Cladding: Copper foil is laminated onto the substrate surfaces using heat and pressure. The thickness of the copper foil is typically specified according to the design requirements for trace width, current carrying capacity, and impedance control.
- Photoresist Application: A layer of photoresist is applied to the surface of the copper-clad substrate. The photoresist serves as a mask for the subsequent etching process.
- Exposure and Development: The PCB design is transferred onto the photoresist layer using a photomask and exposure to ultraviolet light. The exposed photoresist is then developed to remove the unexposed areas, leaving behind the pattern of traces and pads.
- Etching: The exposed copper is etched away using an etchant solution, leaving behind the desired copper traces and pads on the substrate surface.
- Plating: Through-holes, vias, and other features requiring plated connections are created using electroplating processes. This involves depositing a thin layer of metal (typically copper) onto the exposed surfaces of the PCB to create conductive pathways.
- Surface Finish: The PCB surface is coated with a surface finish to protect the copper traces from oxidation and improve solderability. Common surface finishes for ultra-thin hard PCBs include electroless nickel immersion gold (ENIG) and immersion tin.
- Final Inspection and Testing: The finished ultra-thin hard PCBs undergo a series of inspections and tests to ensure they meet the required specifications for dimensional accuracy, electrical continuity, and reliability.
- Assembly: Once the PCBs pass inspection, they are ready for component assembly. Surface mount components (SMD) and through-hole components are soldered onto the PCB using automated assembly equipment.
- Quality Control: After assembly, the PCBs undergo final testing and quality control checks to verify functionality and reliability before they are integrated into the final product.
Throughout the manufacturing process, it’s essential to carefully monitor and control parameters such as temperature, pressure, and chemical concentrations to ensure consistent quality and reliability of the ultra-thin hard PCBs. Collaboration with experienced PCB manufacturers familiar with ultra-thin substrate materials and fabrication techniques can help ensure successful production.
How much should an Ultra-thin hard PCB cost?
The cost of an ultra-thin hard PCB can vary widely depending on several factors, including the size, complexity, material selection, layer count, surface finish, quantity, and turnaround time. However, as a rough estimate, you can expect the cost of an ultra-thin hard PCB to be higher than that of a standard PCB due to the specialized materials and manufacturing processes involved.
Here are some factors that can influence the cost of an ultra-thin hard PCB:
- Material Cost: Ultra-thin PCB materials such as polyimide (PI) or liquid crystal polymer (LCP) tend to be more expensive than standard FR-4 materials.
- Manufacturing Complexity: The complexity of the PCB design, including the number of layers, fine trace width and spacing, and intricate features such as blind vias or buried vias, can increase manufacturing costs.
- Surface Finish: Certain surface finishes, such as electroless nickel immersion gold (ENIG), can add to the cost compared to simpler finishes like HASL (Hot Air Solder Leveling).
- Quantity: Larger quantities of ultra-thin hard PCBs typically result in lower unit costs due to economies of scale. However, smaller production runs may incur higher costs per unit.
- Turnaround Time: Expedited manufacturing or quick-turn services often come with additional fees, so longer lead times may be more cost-effective.
- Additional Services: Optional services such as impedance control testing, electrical testing, and conformal coating can increase the overall cost of the PCB.
As a rough estimate, the cost of an ultra-thin hard PCB can range from a few dollars to several hundred dollars per square inch, depending on the factors mentioned above. It’s essential to obtain quotes from multiple PCB manufacturers to compare pricing and ensure you’re getting the best value for your specific requirements. Additionally, consider factors such as quality, reliability, and supplier reputation when choosing a PCB manufacturer.
What is Ultra-thin hard PCB base material?
Ultra-thin hard PCBs can be constructed using various base materials, each offering specific properties suited to the requirements of the application. Some common base materials used for ultra-thin hard PCBs include:
- FR-4 (Flame Retardant 4): FR-4 is a widely used substrate material for PCBs due to its excellent electrical insulation properties, mechanical strength, and cost-effectiveness. While not inherently ultra-thin, FR-4 can be manufactured into thin substrates suitable for certain applications.
- Polyimide (PI): Polyimide is a high-performance polymer known for its exceptional thermal stability, chemical resistance, and flexibility. It is commonly used in ultra-thin PCBs for applications requiring high-temperature operation or flexibility, such as in aerospace, automotive, and medical devices.
- Liquid Crystal Polymer (LCP): LCP is a thermoplastic material known for its low dielectric constant, excellent dimensional stability, and high-frequency performance. It is well-suited for ultra-thin PCBs used in high-speed digital and RF/microwave applications.
- Rogers RO4000 Series: Rogers Corporation offers a range of high-frequency laminates specifically designed for RF/microwave applications. These materials provide low loss, high reliability, and tight dimensional control, making them suitable for ultra-thin PCBs used in wireless communication systems and radar applications.
- Aramid-Based Materials: Aramid-based materials, such as Arlon AR (Aromatic polyamide) laminates, offer excellent thermal stability and mechanical strength, making them suitable for ultra-thin PCBs used in harsh environments or high-temperature applications.
- Ceramic Substrates: Ceramic substrates, such as aluminum oxide (Al2O3) or aluminum nitride (AlN), offer superior thermal conductivity and electrical insulation properties compared to organic substrates. While less common for ultra-thin PCBs due to their brittleness, ceramic substrates may be used in specialized applications requiring high thermal performance.
The choice of base material for an ultra-thin hard PCB depends on various factors such as operating conditions, electrical performance requirements, mechanical constraints, and cost considerations. Designers should carefully evaluate these factors to select the most suitable base material for their specific application.
Which company makes Ultra-thin hard PCB?
There are many companies that offer manufacturing services for ultra-thin hard PCBs, including Advanced Circuits, Rogers Corporation, Mektec, Nippon Mektron, and Zhen Ding Technology. These companies have advanced technology and equipment to meet various manufacturing needs for ultra-thin hard PCBs, including high-density routing, fine tracing, and complex layering.
Our company is also capable of producing ultra-thin hard PCBs. As a PCB manufacturer with many years of experience, we have the following advantages:
- Advanced Technology and Equipment: We have advanced production equipment and a skilled technical team capable of meeting the high-precision processing requirements of ultra-thin hard PCBs.
- Rich Experience: We have extensive experience in the field of PCB manufacturing and deep understanding of various types of PCB production.
- Customized Services:We provide customized PCB manufacturing services, tailored to the specific requirements of our customers, including material selection, layering, surface treatment, etc.
- Strict Quality Control: We have a rigorous quality control system in place to ensure that every piece of ultra-thin hard PCB meets the requirements and standards of our customers.
- Timely Delivery: We are able to deliver orders to our customers on time, ensuring that their production schedules are not affected.
Whether in consumer electronics, medical devices, aerospace, or other fields, we are able to provide customers with high-quality ultra-thin hard PCB manufacturing services to meet their various needs and requirements.
What are the 7 qualities of good customer service?
Good customer service is characterized by several key qualities that contribute to positive interactions and relationships between businesses and their customers. Here are seven essential qualities:
- Responsiveness: Good customer service involves promptly addressing customer inquiries, concerns, and requests. Being responsive demonstrates that the business values the customer’s time and is committed to providing timely assistance.
- Empathy: Empathy involves understanding and acknowledging the customer’s feelings, concerns, and perspectives. Customer service representatives who demonstrate empathy can build rapport with customers and create a supportive environment for resolving issues.
- Clarity: Effective communication is essential for providing good customer service. Clear and concise communication ensures that customers understand the information provided and the steps needed to resolve their concerns.
- Professionalism: Good customer service is delivered with professionalism, which includes being courteous, respectful, and maintaining a positive attitude even in challenging situations. Professionalism builds trust and confidence in the business and its representatives.
- Problem-solving Skills: Customer service representatives should possess strong problem-solving skills to effectively address customer issues and find appropriate solutions. This may involve actively listening to the customer, analyzing the situation, and offering creative or practical solutions.
- Consistency: Consistency in customer service is crucial for building trust and loyalty. Customers expect consistent experiences across different interactions and touchpoints with the business, including in-person, online, and over the phone.
- Follow-up: Good customer service extends beyond the initial interaction. Following up with customers to ensure their needs have been met and to gather feedback demonstrates a commitment to customer satisfaction and continuous improvement.
By embodying these qualities, businesses can deliver exceptional customer service experiences that foster customer loyalty, positive word-of-mouth, and long-term success.
FAQs
What is an ultra-thin hard PCB?
An ultra-thin hard PCB is a type of printed circuit board that is exceptionally thin while still maintaining rigidity and durability. These PCBs are typically used in applications where space is limited or weight needs to be minimized.
What are the benefits of using ultra-thin hard PCBs?
Ultra-thin hard PCBs offer benefits such as space-saving design, reduced weight, and improved thermal management. They are also suitable for applications requiring high-density routing and flexibility.
What materials are used in ultra-thin hard PCBs?
Common materials used in ultra-thin hard PCBs include FR-4, polyimide (PI), liquid crystal polymer (LCP), and aramid-based materials. These materials provide the necessary rigidity and durability while maintaining a thin profile.
What are the typical applications of ultra-thin hard PCBs?
Ultra-thin hard PCBs are used in various applications, including mobile devices, wearables, medical devices, aerospace, automotive electronics, and IoT (Internet of Things) devices.
What design considerations are important for ultra-thin hard PCBs?
Design considerations for ultra-thin hard PCBs include thickness constraints, material selection, layer count, component placement, trace width and spacing, thermal management, and manufacturability.
Can ultra-thin hard PCBs be manufactured with high reliability?
Yes, ultra-thin hard PCBs can be manufactured with high reliability by following best practices in design, material selection, and manufacturing processes. Working with experienced PCB manufacturers is essential to ensure reliable production.
Are there any limitations or challenges in using ultra-thin hard PCBs?
Some limitations and challenges in using ultra-thin hard PCBs include handling and assembly difficulties due to their thinness, potential for mechanical fragility, and limited options for surface finishes and solder masks.
What factors affect the cost of ultra-thin hard PCBs?
The cost of ultra-thin hard PCBs depends on factors such as material selection, complexity of the design, layer count, surface finish, quantity, and turnaround time. Generally, ultra-thin hard PCBs may cost more than standard PCBs due to specialized materials and manufacturing processes.