Flip-Chip Ball Grid Array. FC-BGA Package and FC BGA Substrate Manufacturer. High precision production lines, high speed material, high frequency material. We use advanced Msap and Sap technology, High multilayer interconnection substrates from 2 to 20 layers,
FCBGA, or Flip-Chip Ball Grid Array, is a type of packaging technology used in semiconductor devices. This technology involves “flipping” the semiconductor chip upside down and attaching it directly to the substrate or circuit board using solder bumps. This is in contrast to traditional packaging methods where the chip is mounted upright on the substrate.
Key features of FCBGA substrate:
Flip-Chip Configuration: In FCBGA, the semiconductor chip is flipped upside down, and the active side with the integrated circuits is facing the substrate. This allows for a more direct and shorter connection between the chip and the substrate.
Ball Grid Array (BGA): FCBGA uses a BGA configuration for external connections. BGA is a type of surface-mount packaging in which solder balls are used to connect the chip to the substrate. BGA provides a compact and reliable method of connecting the chip to the circuit board.
Now, let’s address the potential advantages of FCBGA in terms of performance and reliability:
Improved Electrical Performance: The shorter and more direct connections between the chip and the substrate in FCBGA can result in lower inductance and capacitance, reducing signal delays and improving electrical performance. This can lead to faster data transfer and better overall chip performance.
Enhanced Thermal Performance: The flip-chip configuration allows for better thermal management. Since the heat generated by the chip can be more efficiently conducted through the substrate and dissipated, FCBGA can provide better thermal performance compared to traditional packaging methods. This is crucial for high-performance electronic devices, as excessive heat can affect reliability and performance.
Higher Packaging Density: FCBGA allows for higher packaging density because of the compact nature of the ball grid array. This is particularly important in applications where space is a premium, such as in mobile devices and other miniaturized electronics.
Improved Reliability: The direct connections and reduced interconnect lengths in FCBGA can contribute to improved reliability. The shorter signal paths reduce the risk of signal degradation and electromagnetic interference, leading to more reliable operation of electronic devices.
In summary, FCBGA, as part of flip-chip packaging technology with a Ball Grid Array, offers several advantages, including improved electrical and thermal performance, higher packaging density, and enhanced reliability. These features collectively contribute to the potential revolutionization of electronics by enabling more powerful, compact, and reliable electronic devices.
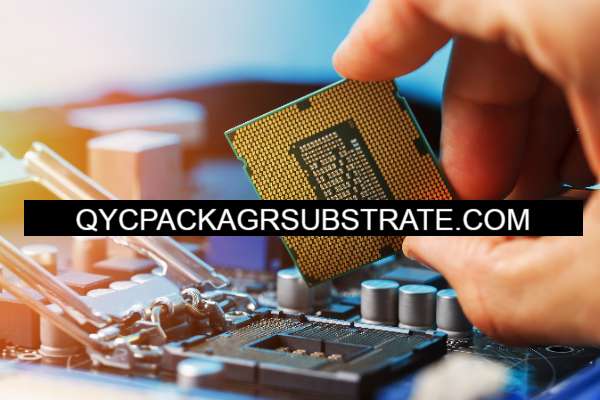
What Functions Does FCBGA Substrate Serve?
The FCBGA (Flip-Chip Ball Grid Array) substrate serves crucial functions in electronic devices, playing a pivotal role in enhancing their performance and efficiency. It serves the following key purposes:
Electrical Connections: The FCBGA substrate facilitates electrical connections between the flip-chip semiconductor device and the circuit board. Through a configuration of solder balls, it enables a reliable and efficient means of connecting the device to the external circuitry, allowing for the transfer of electrical signals between the chip and other components on the board.
Heat Dissipation: The substrate in FCBGA is instrumental in dissipating heat generated by the flip-chip semiconductor device. The flip-chip configuration provides a direct pathway for heat transfer from the chip to the substrate, and the substrate efficiently spreads and dissipates this heat. This feature is particularly crucial in high-performance electronic devices where effective thermal management is essential to prevent overheating and maintain the reliability of the components.
Mechanical Support: FCBGA substrates provide mechanical support for the flip-chip device. Serving as a structural foundation, the substrate securely holds the chip in place, protecting it from mechanical stresses and vibrations. This mechanical support is vital for ensuring the long-term reliability of electronic devices, especially in applications exposed to challenging environmental conditions.
Miniaturization and High Packaging Density: FCBGA substrates contribute to the miniaturization of electronic devices. The flip-chip configuration, combined with the compact nature of the ball grid array, allows for a higher packaging density. This means that more components can be integrated into a smaller space, making electronic devices more compact and efficient. This feature is particularly advantageous in applications where space is limited, such as in mobile devices and portable electronics.
Signal Integrity: The FCBGA substrate helps maintain signal integrity by providing a stable and controlled environment for electrical connections. The short and direct connections between the flip-chip and the substrate reduce the risk of signal degradation, ensuring reliable data transmission and communication within the device.
In summary, the FCBGA substrate serves as a critical component in electronic devices by providing electrical connections, supporting heat dissipation, offering mechanical support, and contributing to the miniaturization and high packaging density of devices. These functions collectively enhance the performance, reliability, and efficiency of electronic devices.
How Many Types of FCBGA Substrate Exist?
There are indeed multiple types of FCBGA (Flip-Chip Ball Grid Array) substrates, and they can vary based on different characteristics, materials, and manufacturing processes. These variations allow for customization to meet specific requirements of diverse applications. Here are some common types of FCBGA substrates:
Organic Substrates: These substrates are typically made of organic materials such as FR-4 (Flame Retardant 4), which is a type of glass-reinforced epoxy laminate. Organic substrates are cost-effective and widely used for applications where moderate performance and reliability are sufficient.
Ceramic Substrates: Ceramic FCBGA substrates are made from materials like alumina or aluminum nitride. Ceramic substrates excel in thermal performance when compared to organic counterparts, making them well-suited for applications where superior heat dissipation and heightened reliability are essential. This is particularly advantageous in scenarios demanding robust performance, such as high-power and high-frequency applications.
High-Frequency Substrates:In applications demanding high-frequency performance, dedicated FCBGA substrates optimized for this purpose are employed. These substrates are engineered to minimize signal loss by utilizing materials with precise dielectric properties that can effectively support high-frequency signals.
Low-Loss Materials: Certain FCBGA substrates incorporate dielectric materials with low loss properties to reduce signal attenuation, thereby enhancing signal integrity. These are important for applications where maintaining the quality of high-speed signals is crucial.
High-Temperature Substrates: In certain applications where devices are subjected to elevated temperatures, high-temperature FCBGA substrates are used. These substrates can withstand and dissipate higher levels of heat without compromising performance.
Flex Substrates: Flexible FCBGA substrates are designed for applications where flexibility is required, such as in bendable or flexible electronics. These substrates are made from flexible materials like polyimide.
The selection of an FCBGA (Flip-Chip Ball Grid Array) substrate is contingent upon the unique demands of the application. It is influenced by considerations such as thermal efficiency, electrical properties, cost factors, and the specific needs of the intended application. The broad array of FCBGA substrates available in the market stems from a variety of manufacturing processes, which include substrate design, material choices, and fabrication techniques.
In conclusion, the availability of diverse FCBGA substrates allows for tailoring solutions to meet the specific requirements of various applications. This includes addressing needs such as high frequency, high density, improved thermal performance, and flexibility.
Is FCBGA Substrate Different from IC Packaging?
FCBGA (Flip-Chip Ball Grid Array) substrate and IC (Integrated Circuit) packaging are related concepts within the realm of chip packaging technology, but they represent different aspects of the overall process. Let’s explore their relationship and how they fit into the broader landscape of integrated circuit technology.
- IC Packaging Overview:
-
- Definition: IC packaging involves enclosing a semiconductor chip within a protective and functional package that provides electrical connections, thermal management, and mechanical support.
- Purpose: IC packaging serves to protect the delicate semiconductor chip from external elements, facilitate electrical connections to external circuitry, dissipate heat, and provide structural support.
- Varieties: IC packaging comes in various forms, including but not limited to Dual In-Line Packages (DIP), Quad Flat Packages (QFP), Ball Grid Arrays (BGA), and more.
- FCBGA Substrate as Part of IC Packaging:
-
- FCBGA as a Packaging Technology: FCBGA is a specific type of IC packaging technology.
- Flip-Chip Configuration: FCBGA involves a flip-chip configuration where the semiconductor chip is inverted and attached to the substrate using solder bumps.
- Ball Grid Array: FCBGA utilizes a Ball Grid Array (BGA) for external connections, where solder balls connect the chip to the substrate.
- Substrate Role: The FCBGA substrate is a critical component within the IC package, serving as the platform for the flip-chip connection and providing support for electrical, thermal, and mechanical functions.
- Relationship and Position in the IC Ecosystem:
- IC Packaging Classifications: IC packaging technologies are classified based on various factors, including the arrangement of pins or balls, form factor, and the method of connecting the chip to the package.
- FCBGA Position: FCBGA is one specific classification within IC packaging, notable for its flip-chip configuration and use of a ball grid array. It is chosen for applications where the advantages of direct chip attachment, improved thermal performance, and high packaging density are critical.
In summary, FCBGA substrate is a specific implementation of IC packaging technology, characterized by a flip-chip configuration and the use of a ball grid array for external connections. It plays a crucial role within the broader landscape of integrated circuit packaging, contributing to the performance, reliability, and miniaturization of electronic devices. Understanding the relationship between FCBGA and IC packaging helps appreciate their respective roles in the integrated circuit ecosystem.
How Does FCBGA Substrate Differ from Conventional PCBs?
FCBGA (Flip-Chip Ball Grid Array) substrates differ from conventional Printed Circuit Boards (PCBs) and other advanced PCB technologies in several aspects. Let’s compare FCBGA substrates with traditional PCBs, Motherboards, Substrate-like PCBs (SLPs), and HDI (High-Density Interconnect) substrates, emphasizing the unique features and advantages of FCBGA substrates in circuit design:
- Traditional PCBs:
-
- Configuration: Traditional PCBs typically have components mounted on the surface of the board.
- Interconnection: Components are connected through through-hole or surface-mount technology.
- Advantages: Simplicity, cost-effectiveness, and ease of manufacturing for less complex electronic circuits.
- Motherboards:
-
- Function: Motherboards are complex PCBs serving as the central hub in a computer system, connecting various components.
- Interconnection: Motherboards use a combination of surface-mount and through-hole technologies.
- Advantages: Versatility and support for diverse components, but may not be optimized for specific high-performance applications.
- Substrate-like PCBs (SLPs):
-
- Design: SLPs are PCBs designed to mimic the functions of a substrate, often used in mobile devices.
- Interconnection: Utilizes advanced materials and manufacturing processes for improved electrical performance.
- Advantages: Slim profile, lightweight, and optimized for miniaturized electronics with a focus on space efficiency.
- HDI Substrates:
-
- Technology: HDI substrates use advanced fabrication techniques to achieve high-density interconnects.
- Interconnection: Utilizes microvias, fine-line traces, and multiple layers for densely packed components.
- Advantages: Improved signal integrity, reduced signal loss, and enhanced miniaturization.
- FCBGA Substrates:
-
- Configuration: FCBGA involves a flip-chip configuration where the semiconductor chip is inverted and connected directly to the substrate.
- Interconnection: Utilizes a Ball Grid Array (BGA) for external connections, providing a compact and direct connection to the board.
- Advantages:
-
- Improved Electrical Performance: Shorter and more direct connections reduce signal delays.
- Enhanced Thermal Performance: Efficient heat dissipation through the substrate.
- High Packaging Density: Compact nature of the BGA allows for more components in a smaller space.
- Reliability: Reduced risk of signal degradation and electromagnetic interference.
In summary, FCBGA substrates offer advantages in terms of electrical and thermal performance, high packaging density, and reliability compared to traditional PCBs, Motherboards, Substrate-like PCBs, and HDI substrates. The unique features of FCBGA make it well-suited for applications where these characteristics are critical, such as in high-performance electronic devices.
What Are the Primary Structures and Manufacturing Technologies of FCBGA Substrate?
The primary structures and manufacturing technologies of FCBGA (Flip-Chip Ball Grid Array) substrates involve several key elements, including substrate materials, flip-chip assembly, and ball grid array formation. Here is a comprehensive overview:
Substrate Materials:
Organic or Ceramic: FCBGA substrates can be made from organic materials like FR-4 (Flame Retardant 4) or ceramic materials such as alumina or aluminum nitride. The choice of material depends on factors like thermal conductivity, cost, and application requirements.
Flip-Chip Assembly:
Flip-Chip Configuration: In FCBGA, the semiconductor chip is flipped upside down, and the active side with the integrated circuits faces the substrate.
Solder Bumps: Small solder bumps are placed on the chip’s bonding pads. These bumps will later be used for making electrical connections with the substrate.
Ball Grid Array (BGA) Formation:
Solder Balls: The substrate is equipped with an array of solder balls in a specific grid pattern. These solder balls act as connection points for the external circuitry.
Alignment and Connection: The flip-chipped chip is aligned with the substrate, and the solder bumps on the chip are reflowed to create solder joints with the solder balls on the substrate, establishing electrical connections.
Manufacturing Processes:
High-Density Interconnect (HDI) Technology: FCBGA substrates often incorporate HDI technology, which involves microvia formation, fine-line patterning, and multiple layers of interconnects. HDI allows for high-density routing, reducing signal loss and enhancing signal integrity.
Laser Drilling: In HDI manufacturing, laser drilling is often used for creating microvias, which are small holes that connect different layers of the substrate, enabling more compact designs.
Plating and Etching: Processes like electroplating and etching are utilized to create the circuitry and solder ball pads on the substrate.
Advanced Manufacturing Methods:
Additive Manufacturing: Some FCBGA substrates may benefit from additive manufacturing techniques, such as 3D printing, to create intricate structures or customized designs.
Embedding Components: Advanced FCBGA manufacturing may involve embedding passive components directly into the substrate, reducing the need for additional discrete components on the board.
Structural Characteristics:
Compact Design: FCBGA substrates are known for their compact design, allowing for high packaging density and smaller form factors.
Thermal Management: The structure facilitates efficient heat dissipation due to the direct attachment of the chip to the substrate and the use of materials with good thermal conductivity.
Signal Integrity: High-quality electrical connections and the use of HDI technology contribute to excellent signal integrity.
Application of Improved HDI Manufacturing Technology:
Signal Performance: HDI technology improves signal performance by reducing signal loss and enabling the use of smaller vias and traces.
Miniaturization: HDI allows for finer pitch solder balls, enabling the design of smaller and more densely packed FCBGA substrates.
In summary, FCBGA substrate manufacturing involves a combination of flip-chip assembly, BGA formation, advanced HDI technology, and other manufacturing processes. The resulting structures offer compact designs, excellent thermal management, and high signal integrity, making them suitable for a wide range of high-performance electronic applications. The incorporation of improved HDI manufacturing technology and advanced manufacturing methods further enhances the capabilities of FCBGA substrates in modern packaging technology.
What Are the Frequently Asked Questions (FAQs) About FCB-GA Substrate?
What is FCBGA?
FCBGA stands for Flip-Chip Ball Grid Array. It is an advanced packaging technology used in integrated circuits where the semiconductor chip is flipped and connected directly to the substrate using solder bumps and a ball grid array for external connections.
How does FCBGA differ from traditional packaging?
FCBGA differs by employing a flip-chip configuration, allowing for direct chip attachment to the substrate. This results in improved electrical performance, enhanced thermal management, and higher packaging density compared to traditional packaging methods.
What is the role of the substrate in FCBGA?
The substrate in FCBGA serves as a platform for the flip-chip connection. It provides electrical connections, supports heat dissipation, and offers mechanical support for the semiconductor chip.
What materials are commonly used for FCBGA substrates?
FCBGA substrates can be made from organic materials like FR-4 or ceramic materials such as alumina or aluminum nitride. Material selection depends on factors like thermal conductivity and application requirements.
How does FCBGA contribute to thermal management?
FCBGA facilitates efficient heat dissipation due to the direct attachment of the chip to the substrate. This configuration allows for effective transfer of heat away from the chip.
What is the significance of the ball grid array (BGA) in FCBGA?
The BGA is a crucial element in FCBGA for external connections. Solder balls on the substrate create a reliable and efficient connection between the chip and the external circuitry.
What advantages does FCBGA offer in terms of signal integrity?
FCBGA provides improved signal integrity due to the direct and short electrical connections between the chip and the substrate. This reduces signal delays and the risk of signal degradation.
How does FCBGA support high-density packaging?
FCBGA supports high-density packaging through the compact nature of the ball grid array, allowing for a higher concentration of solder balls in a smaller space.
What role does HDI technology play in FCBGA manufacturing?
High-Density Interconnect (HDI) technology in FCBGA involves advanced fabrication techniques like microvias, fine-line patterning, and multiple layers. HDI enhances packaging density and contributes to improved signal performance.
In which applications is FCBGA commonly used?
FCBGA is commonly used in high-performance electronic devices such as CPUs, GPUs, and other integrated circuits where advanced packaging technology is required for optimal performance, reliability, and miniaturization.
Is FC-BGA Substrate Paving the Way for the Future?
As of my last knowledge update in January 2022, FCBGA (Flip-Chip Ball Grid Array) substrate technology has been a significant and evolving aspect of advanced packaging in the electronics industry. While I can’t provide real-time updates, I can discuss potential development trends based on the information available until my last update:
- Increased Adoption in High-Performance Devices:
-
- FCBGA has been widely adopted in high-performance electronic devices, including CPUs and GPUs. We can anticipate continued growth in its usage, especially as electronic devices demand higher processing power and efficiency.
- Advancements in Material Science:
-
- Ongoing advancements in material science may lead to the development of new substrate materials with enhanced thermal conductivity, electrical properties, and mechanical strength. This could further improve the overall performance and reliability of FCBGA-based devices.
- Integration with Emerging Technologies:
-
- FCBGA may play a key role in the integration of emerging technologies, such as those related to artificial intelligence, 5G, and the Internet of Things (IoT). The compact design and high packaging density of FCBGA make it suitable for applications requiring advanced functionality in a limited space.
- Enhancements in Thermal Management:
-
- Future developments in FCBGA may focus on even more effective thermal management solutions. As electronic devices continue to become more powerful, efficient heat dissipation will remain a critical consideration for reliability and performance.
- Miniaturization and Wearable Electronics:
-
- The compact nature of FCBGA substrates makes them well-suited for miniaturized electronics and wearable devices. Future trends may see FCBGA technology contributing to the development of smaller, more lightweight, and energy-efficient wearables.
- Advanced Manufacturing Techniques:
-
- Continued advancements in manufacturing techniques, including 3D printing and other additive manufacturing methods, may influence the design and production of FCBGA substrates. These techniques could provide new possibilities for customization and innovation.
- Integration with System-in-Package (SiP) Solutions:
-
- FCBGA substrates may increasingly be integrated into System-in-Package (SiP) solutions, where multiple functional components are combined into a single package. This can contribute to overall system efficiency and performance.
- Focus on Signal Integrity and High-Frequency Applications:
- With the growing demand for high-speed data transmission, FCBGA technology may see advancements in signal integrity and high-frequency applications.This is essential for applications such as data centers, telecommunications, and high-performance computing.
In conclusion, it is highly probable that FCBGA substrate technology will maintain its crucial role in shaping the future of the electronics industry.Anticipated trends include increased adoption in high-performance devices, advancements in material science, integration with emerging technologies, enhancements in thermal management, contributions to miniaturization and wearable electronics, the evolution of manufacturing techniques, integration with SiP solutions, and a focus on signal integrity for high-frequency applications. These trends collectively showcase the technology’s adaptability and relevance in shaping the future of electronic design and packaging.