Micro LED Substrate Manufacturer
Micro LED Substrate Manufacturer, Small spacing, small marks, Ultra-thin, flat finished surface, hard base materials. we made this types LED PCBs and BGA/IC substrates with high quality, and fast lead times.
Micro LED substrates serve as the foundational platform for the fabrication of Micro LEDs, miniature light-emitting diodes with dimensions typically less than 100 micrometers. These substrates, crafted from materials like glass, silicon, sapphire, or flexible polymers, provide structural support and electrical connectivity for the tiny LEDs.
The fabrication process involves intricate steps such as surface preparation, patterning, deposition of materials, metalization, and precise etching to define the features required for mounting and connecting the Micro LEDs.
Characterized by qualities like uniformity, thermal conductivity, electrical insulation, and mechanical durability, Micro LED substrates play a pivotal role in ensuring the performance and reliability of Micro LED-based devices.
Their applications span a wide range of industries, from consumer electronics, automotive displays, and wearables to augmented reality (AR), virtual reality (VR), and medical devices. With advancements in technology and manufacturing processes, Micro LED substrates continue to drive innovation in display technology, offering benefits such as high resolution, energy efficiency, and versatility in form factors.
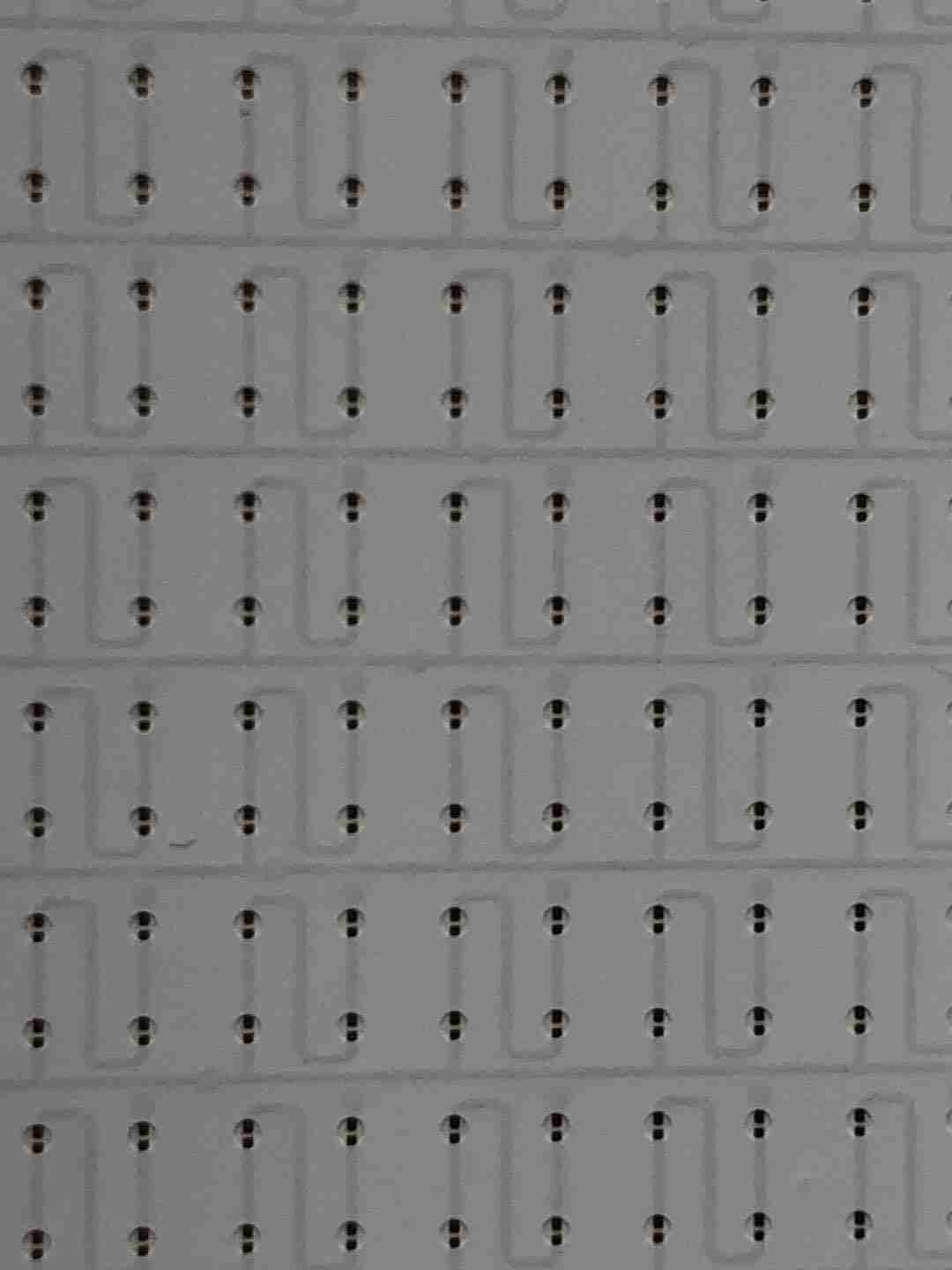
Micro LED Substrate
What is a Micro LED Substrate?
A Micro LED substrate refers to the base material upon which Micro LEDs are fabricated. Micro LEDs are tiny light-emitting diodes that are typically smaller than 100 micrometers. The substrate plays a crucial role in supporting these tiny LEDs and providing a stable platform for their operation.
In Micro LED technology, the substrate needs to meet several requirements:
- Uniformity: The substrate must have a uniform surface to ensure consistent LED performance across the display.
- Thermal Conductivity: Efficient heat dissipation is crucial for Micro LED operation to prevent overheating and maintain longevity. The substrate material should have high thermal conductivity to dissipate heat effectively.
- Electrical Insulation: Since Micro LEDs are semiconductor devices, the substrate should provide electrical insulation to prevent short circuits and ensure proper functioning.
- Transparency or Reflectivity: Depending on the application, the substrate may need to be transparent or reflective to allow light to pass through or reflect off effectively.
- Mechanical Durability: The substrate should be mechanically robust to withstand handling during fabrication and assembly processes.
Common materials used for Micro LED substrates include glass, silicon, sapphire, and flexible polymers like polyimide. Each material has its advantages and disadvantages in terms of thermal conductivity, transparency, flexibility, and cost.
Overall, the choice of substrate significantly impacts the performance, durability, and cost of Micro LED displays and other applications. Advances in substrate technology are essential for the continued development and commercialization of Micro LED-based products.
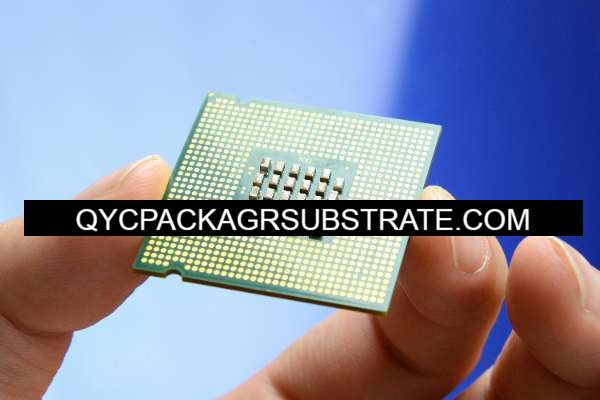
Micro LED Substrate Manufacturer
What are the Micro LED Substrate Design Guidelines?
Micro LED substrate design guidelines are a set of principles and recommendations to ensure the optimal performance and reliability of Micro LED-based devices. These guidelines typically cover various aspects of substrate design, including material selection, surface properties, electrical characteristics, and thermal management. Here are some key considerations typically included in Micro LED substrate design guidelines:
- Material Selection: Choose a substrate material with high thermal conductivity to efficiently dissipate heat generated by Micro LEDs. Common materials include glass, silicon, sapphire, and flexible polymers.
- Surface Uniformity: Ensure the substrate surface is uniform to prevent variations in LED performance across the display. Any irregularities or defects can affect light emission and display quality.
- Electrical Insulation: The substrate should provide electrical insulation to prevent short circuits and ensure proper functioning of the Micro LEDs.
- Thermal Management: Incorporate features such as heat sinks, thermal vias, or other structures to enhance heat dissipation and maintain optimal operating temperatures for the Micro LEDs.
- Transparency or Reflectivity: Depending on the application, the substrate may need to be transparent to allow light to pass through or reflective to enhance light emission efficiency.
- Mechanical Durability: Ensure the substrate is mechanically robust to withstand handling during fabrication, assembly, and use of Micro LED devices.
- Compatibility with Fabrication Processes: The substrate design should be compatible with fabrication processes such as photolithography, deposition, and etching used to manufacture Micro LED arrays.
- Size and Thickness: Optimize the substrate size and thickness to meet the requirements of the specific Micro LED application, considering factors such as display resolution, form factor, and mechanical constraints.
- Alignment and Registration: Design features to facilitate accurate alignment and registration of Micro LEDs on the substrate during fabrication and assembly processes.
- Cost Considerations: Balance performance requirements with cost considerations to ensure the substrate design is commercially viable for mass production of Micro LED devices.
These guidelines are continually evolving as Micro LED technology advances and new applications emerge. Adhering to these design principles helps ensure the successful development and commercialization of Micro LED-based products with improved performance, reliability, and manufacturability.
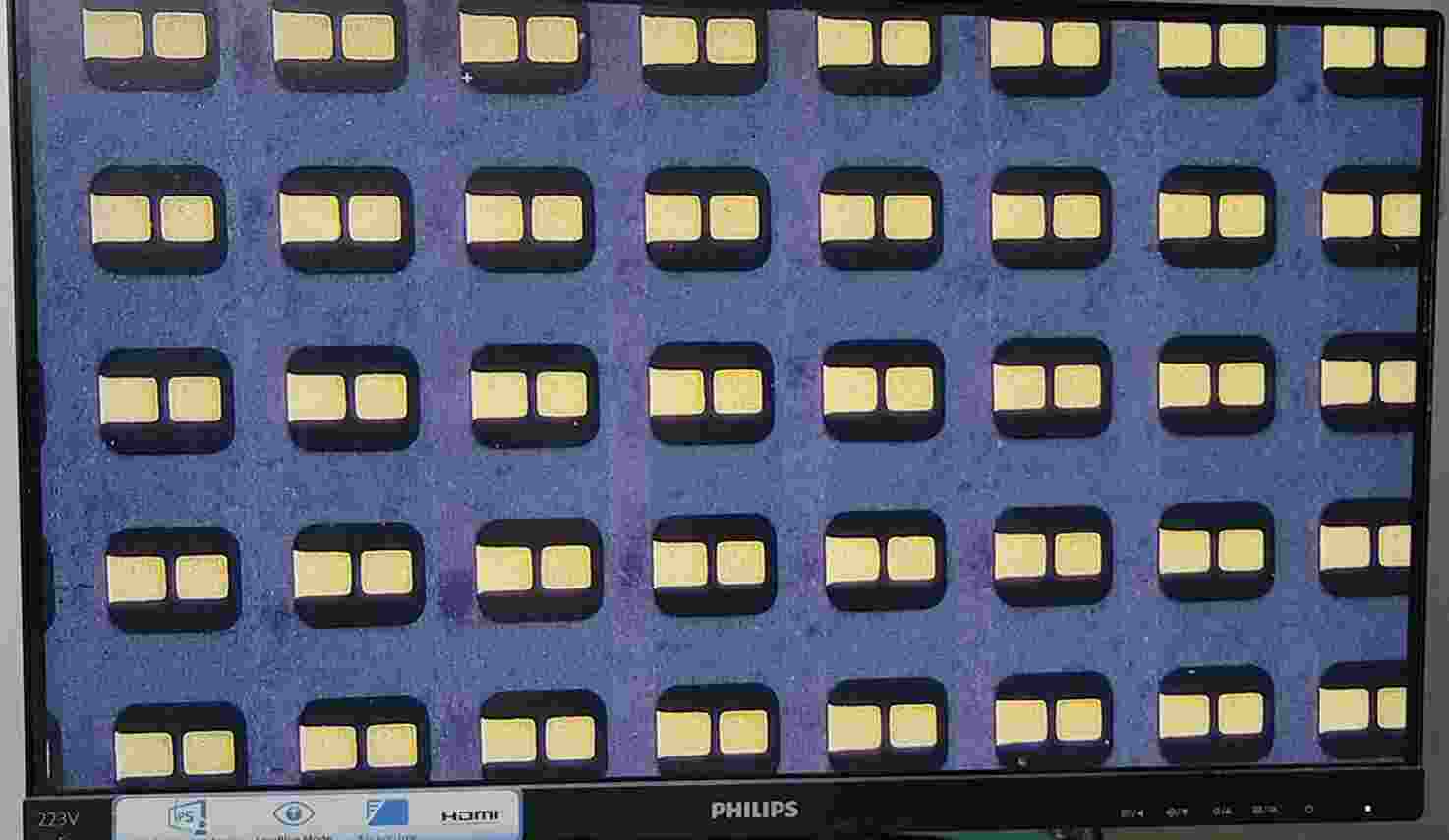
small gap LED Substrate
What is the Micro LED Substrate Fabrication Process?
The fabrication process for Micro LED substrates involves several steps to prepare the base material and create the necessary features for mounting and electrically connecting the Micro LEDs. Here’s a general overview of the Micro LED substrate fabrication process:
- Substrate Preparation: The process begins with preparing the substrate material, which could be glass, silicon, sapphire, or flexible polymers. The substrate is cleaned thoroughly to remove any contaminants that could affect subsequent processing steps.
- Surface Treatment: Depending on the substrate material and desired properties, surface treatment processes such as chemical etching, oxidation, or deposition of thin films may be performed to modify surface properties like roughness, conductivity, or adhesion.
- Patterning: Patterning involves defining the locations and shapes of features on the substrate where the Micro LEDs will be placed. This step is typically accomplished using photolithography, where a photoresist material is selectively exposed to UV light through a mask, creating a pattern on the substrate surface.
- Deposition: Various materials may be deposited onto the substrate surface to create electrical connections, insulating layers, or reflective coatings. Common deposition techniques include physical vapor deposition (PVD), chemical vapor deposition (CVD), and atomic layer deposition (ALD).
- Metalization: Metalization involves depositing thin layers of metals such as aluminum, copper, or gold onto the substrate to create electrical connections and interconnects for the Micro LEDs. Metal layers may also serve as reflective coatings to enhance light extraction efficiency.
- Etching: Etching processes are used to remove unwanted material from the substrate surface and define the final features for mounting and connecting the Micro LEDs. Wet chemical etching or dry plasma etching techniques may be employed depending on the substrate material and desired etch profile.
- Dicing or Laser Ablation: Once the substrate features are defined, the substrate may be diced into individual pieces or regions using mechanical dicing saws or laser ablation techniques. This step creates separate substrates for each Micro LED array or device.
- Cleaning and Inspection: After fabrication, the substrates undergo thorough cleaning to remove any residues or contaminants introduced during processing. Substrates are then inspected for defects or irregularities that could impact Micro LED performance.
- Micro LED Placement and Bonding: Finally, the fabricated substrates are ready for Micro LED placement and bonding. Micro LEDs are typically transferred onto the substrate using pick-and-place tools or transfer printing techniques. Bonding processes such as flip-chip bonding or wire bonding are then used to electrically connect the Micro LEDs to the substrate.
- Testing and Packaging: Once the Micro LEDs are bonded to the substrate, the devices undergo testing to ensure proper functionality and performance. Substrates may then be packaged into final products such as displays, lighting modules, or wearable devices.
Overall, the Micro LED substrate fabrication process is a complex series of steps that require precise control and coordination to produce high-quality substrates for Micro LED-based applications. Advances in fabrication techniques and materials continue to drive improvements in Micro LED performance, reliability, and manufacturability.
How do you manufacture a Micro LED Substrate?
Manufacturing a Micro LED substrate involves several key steps that require precision and specialized equipment. Here’s a general overview of the manufacturing process:
- Substrate Selection: Choose a suitable substrate material based on the specific requirements of the Micro LED application. Common substrate materials include glass, silicon, sapphire, and flexible polymers.
- Cleaning and Surface Preparation: Thoroughly clean the substrate surface to remove any contaminants that could affect subsequent processing steps. Surface preparation techniques such as chemical treatments or plasma cleaning may be employed to improve adhesion and surface properties.
- Patterning: Use photolithography or other patterning techniques to define the locations and shapes of features on the substrate where the Micro LEDs will be placed. This step involves applying a photoresist material, exposing it to UV light through a mask, and developing to create the desired pattern on the substrate surface.
- Deposition: Deposit thin films of materials onto the substrate surface to create electrical connections, insulating layers, or reflective coatings. Deposition techniques such as physical vapor deposition (PVD), chemical vapor deposition (CVD), or atomic layer deposition (ALD) may be used depending on the desired film properties.
- Etching: Use wet chemical etching or dry plasma etching processes to remove unwanted material from the substrate surface and define the final features for mounting and connecting the Micro LEDs.
- Metalization: Deposit thin layers of metals such as aluminum, copper, or gold onto the substrate to create electrical connections and interconnects for the Micro LEDs. Metal layers may also serve as reflective coatings to enhance light extraction efficiency.
- Dicing or Laser Ablation: Dice the substrate into individual pieces or regions using mechanical dicing saws or laser ablation techniques. This step creates separate substrates for each Micro LED array or device.
- Cleaning and Inspection: Clean the fabricated substrates to remove any residues or contaminants introduced during processing. Inspect the substrates for defects or irregularities that could impact Micro LED performance.
- Micro LED Placement and Bonding: Transfer Micro LEDs onto the substrate using pick-and-place tools or transfer printing techniques. Bond the Micro LEDs to the substrate using flip-chip bonding or wire bonding to establish electrical connections.
- Testing and Packaging: Test the assembled Micro LED substrates to ensure proper functionality and performance. Package the substrates into final products such as displays, lighting modules, or wearable devices.
Throughout the manufacturing process, strict quality control measures are implemented to ensure the consistency and reliability of the Micro LED substrates. Advancements in manufacturing technology and materials continue to drive improvements in Micro LED production efficiency and yield.
How much should a Micro LED Substrate cost?
The cost of a Micro LED substrate can vary widely depending on several factors, including the substrate material, size, complexity, manufacturing processes involved, and the volume of production. As of my last update in January 2022, it’s challenging to provide an exact cost without specific details about the substrate’s specifications and the manufacturer’s pricing structure.
However, here are some general considerations that can influence the cost of a Micro LED substrate:
- Substrate Material: Different substrate materials have varying costs. For example, glass substrates may be less expensive compared to sapphire substrates, which are known for their high cost but excellent optical and mechanical properties.
- Size and Thickness: Larger substrates typically cost more due to the increased material usage and processing complexity. Additionally, thicker substrates may require more material and processing steps, affecting the overall cost.
- Complexity of Features: The complexity of the substrate design, including the number and intricacy of patterns, layers, and features, can impact manufacturing costs. More complex designs may require additional processing steps, which can increase costs.
- Manufacturing Processes: The choice of manufacturing processes, such as deposition techniques, lithography methods, and etching processes, can affect costs. Some processes may require expensive equipment or consumables, contributing to higher production costs.
- Volume of Production: Economies of scale play a significant role in determining the cost of Micro LED substrates. Higher production volumes typically lead to lower per-unit costs due to efficiencies in manufacturing and purchasing.
- Quality and Yield: Quality control measures and yield rates also influence costs. Higher-quality substrates with lower defect rates may command a premium price, while lower yields can increase production costs.
Given these factors, the cost of a Micro LED substrate can range from a few dollars to tens or even hundreds of dollars per substrate, depending on the specific requirements and market dynamics. Additionally, as Micro LED technology continues to advance and adoption increases, economies of scale and technological improvements may drive down costs over time.
What is Micro LED Substrate base material?
The base material for Micro LED substrates can vary depending on the specific requirements of the application and the manufacturer’s preferences. Several materials are commonly used as substrates for Micro LED fabrication:
- Glass: Glass substrates are widely used due to their excellent optical properties, flatness, and compatibility with high-resolution displays. They are relatively inexpensive compared to some other materials and offer good thermal stability. However, glass substrates can be brittle and may require additional processing steps for certain applications.
- Silicon: Silicon substrates are commonly used in Micro LED fabrication, especially for applications where flexibility or integration with silicon-based electronics is desired. Silicon substrates offer excellent thermal conductivity and mechanical properties. They can also be fabricated with precise features using semiconductor manufacturing techniques.
- Sapphire: Sapphire substrates are known for their high optical transparency, mechanical hardness, and chemical resistance. They are often used in high-performance Micro LED displays where optical quality and durability are crucial. However, sapphire substrates can be more expensive compared to other materials.
- Flexible Polymers: Flexible polymer substrates such as polyimide or polymethyl methacrylate (PMMA) are used in applications requiring bendable or conformable displays, such as wearable devices or curved displays. Flexible substrates offer versatility in design and form factor but may have lower thermal conductivity compared to rigid substrates.
- Metal Foils: Metal foils such as copper or aluminum can also be used as substrates for Micro LED fabrication, especially in applications where thermal management is critical. Metal substrates offer excellent thermal conductivity and mechanical stability but may require additional processing steps to ensure electrical insulation and compatibility with Micro LED fabrication processes.
The choice of substrate material depends on factors such as cost, performance requirements, form factor, and manufacturing considerations. Each material has its advantages and limitations, and manufacturers may select the most suitable substrate based on the specific needs of their Micro LED applications.
Which company manufactures Micro LED Substrates?
Currently, many companies are manufacturing Micro LED Substrates, including major manufacturers such as Samsung, LG, AU Optronics, Infineon, and Acer. These companies have extensive experience and technological capabilities in the field of Micro LED technology, and they are committed to developing high-quality, high-performance Micro LED substrates to meet various application requirements.
As for our company, we are also capable of producing Micro LED substrates, with the following advantages and capabilities:
- Advanced Technology and Equipment: We have advanced manufacturing technology and equipment, including the latest lithography, thin film deposition, and plasma etching equipment, to achieve high-precision, high-efficiency production of Micro LED substrates.
- Diverse Material Selection: We can choose different types of substrate materials according to customer requirements, such as glass, silicon, sapphire, flexible polymers, etc., to meet the requirements of different application scenarios.
- Flexible Customization Ability: We can customize Micro LED substrates according to specific customer needs, including size, shape, surface treatment, and design of special functions, to provide personalized solutions for customers.
- Strict Quality Control: We implement a strict quality management system to ensure that each Micro LED substrate meets customer requirements and standards, thereby ensuring product stability and reliability.
- Continuous Technological Innovation: We continue to invest in research and development, track the latest advances in Micro LED technology, continuously optimize production processes and product performance, to meet the changing market demands and customer needs.
In summary, our company has the capability to produce Micro LED substrates, and through advanced technology, diverse material selection, flexible customization ability, strict quality control, and continuous technological innovation, we can provide customers with high-quality, high-performance Micro LED substrate products.
What are the 7 qualities of good customer service?
Good customer service is essential for building positive relationships with customers and fostering loyalty. Here are seven qualities that characterize good customer service:
- Responsiveness:A good customer service team responds promptly to customer inquiries, concerns, and requests. This includes answering phone calls, replying to emails, and addressing issues in a timely manner. Customers appreciate quick responses and feel valued when their needs are addressed promptly.
- Empathy: Empathy involves understanding and relating to the customer’s emotions, concerns, and perspectives. Good customer service representatives listen attentively to customers, show genuine concern for their problems, and strive to understand their unique situations. Demonstrating empathy helps build trust and rapport with customers.
- Professionalism: Professionalism encompasses courteous behavior, clear communication, and a respectful attitude towards customers. Customer service representatives should maintain a professional demeanor at all times, even when dealing with challenging situations. Professionalism instills confidence in customers and reflects positively on the company’s image.
- Knowledgeability: Good customer service requires having in-depth knowledge about the company’s products, services, policies, and procedures. Customer service representatives should be well-trained and equipped to answer questions, provide accurate information, and offer relevant solutions to customer issues. Knowledgeable representatives inspire confidence and credibility in the company.
- Problem-Solving Skills: Effective problem-solving skills are essential for resolving customer issues and complaints satisfactorily. Customer service representatives should be proactive in identifying and addressing customer problems, using critical thinking and creativity to find solutions. Being resourceful and adaptable enables representatives to handle various situations effectively.
- Consistency: Consistency in customer service means delivering a consistently high level of service across all interactions and touchpoints. Whether it’s in-person interactions, phone calls, emails, or online chats, customers expect a consistent experience. Consistency builds trust and reliability, leading to enhanced customer satisfaction and loyalty.
- Follow-Up and Follow-Through: Good customer service doesn’t end after resolving an issue; it includes following up with customers to ensure their satisfaction and following through on any commitments made. Following up demonstrates care and concern for the customer’s experience, while following through builds credibility and reinforces trust.
By embodying these qualities, companies can deliver exceptional customer service experiences that leave a lasting positive impression on customers and contribute to long-term success.
FAQs
What is a Micro LED substrate?
A Micro LED substrate refers to the base material upon which Micro LEDs are fabricated. It provides support for the tiny LEDs and facilitates their electrical connections.
What materials are commonly used for Micro LED substrates?
Common substrate materials include glass, silicon, sapphire, and flexible polymers like polyimide. Each material offers different properties suited for various applications.
What are the key considerations in Micro LED substrate design?
Important factors in substrate design include material selection, surface uniformity, thermal management, electrical insulation, transparency or reflectivity, mechanical durability, and compatibility with fabrication processes.
How are Micro LED substrates fabricated?
The fabrication process typically involves steps such as substrate preparation, surface treatment, patterning, deposition of materials, metalization, etching, dicing or laser ablation, cleaning, inspection, Micro LED placement, bonding, testing, and packaging.
What companies manufacture Micro LED substrates?
Major manufacturers of Micro LED substrates include companies like Samsung, LG, AU Optronics, and others with expertise in semiconductor manufacturing and display technology.
What are the cost factors associated with Micro LED substrates?
The cost of Micro LED substrates depends on factors such as substrate material, size, complexity, manufacturing processes, volume of production, quality, and yield rates.