Microtrace Ceramic Substrates Manufacturer
Microtrace Ceramic Substrates Manufacturer,Microtrace Ceramic Substrates are advanced ceramic materials used in the fabrication of high-performance electronic circuits and components. Featuring precise micro-scale patterning of conductive traces and components, these substrates offer exceptional thermal conductivity, mechanical strength, and electrical insulation properties. They find applications in diverse industries, including telecommunications, automotive, aerospace, and medical devices, enabling the development of compact and reliable electronic systems. With their superior performance and versatility, Microtrace Ceramic Substrates are integral to the advancement of modern electronics technology.
What is a Microtrace Ceramic Substrate?
A Microtrace Ceramic Substrate refers to a type of substrate material used in electronics manufacturing, particularly in the production of integrated circuits (ICs) and microelectronics. These substrates are typically made of ceramic materials such as alumina (Al2O3) or aluminum nitride (AlN).
Ceramic substrates offer several advantages in electronic applications, including excellent thermal conductivity, mechanical strength, and electrical insulation properties. These properties make them well-suited for use in high-power and high-frequency electronic devices where heat dissipation and electrical insulation are critical.
Microtrace refers to the precise patterning of conductive traces and other electronic components on the ceramic substrate at a micro-scale level. This precise patterning allows for the creation of intricate circuitry and miniaturized electronic devices.
Overall, Microtrace Ceramic Substrates play a crucial role in the development of advanced electronic systems, particularly in applications requiring compact size, high performance, and reliability.
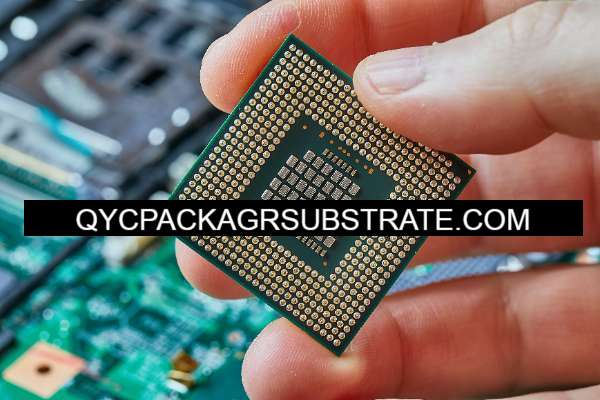
Microtrace Ceramic Substrates Manufacturer
What are the Microtrace Ceramic Substrate Design Guidelines?
Design guidelines for Microtrace Ceramic Substrates typically involve considerations related to material properties, thermal management, electrical performance, and manufacturability. Here are some common guidelines:
- Material Selection: Choose ceramic materials with suitable properties for the specific application, such as thermal conductivity, coefficient of thermal expansion (CTE), dielectric constant, and mechanical strength.
- Trace Layout and Routing: Design the layout of conductive traces and components on the substrate to minimize signal interference, optimize signal integrity, and ensure efficient heat dissipation. Pay attention to trace widths, spacing, and signal routing to minimize signal loss and electromagnetic interference (EMI).
- Thermal Management: Incorporate features such as thermal vias, heat sinks, and thermal pads to facilitate heat dissipation and prevent thermal hotspots. Ensure that the thermal design is adequate to maintain the operating temperature within acceptable limits for all components on the substrate.
- Dielectric Layers: Consider the number and thickness of dielectric layers needed for electrical insulation between conductive traces and components. Optimize dielectric properties to minimize signal distortion and crosstalk.
- Component Placement: Carefully place components on the substrate to optimize signal paths, minimize parasitic capacitance and inductance, and facilitate ease of assembly and testing.
- Signal Integrity: Pay attention to impedance matching, signal termination, and signal integrity considerations to minimize signal reflections, distortion, and noise.
- Manufacturability:Design the substrate with manufacturability in mind, considering factors such as substrate size, material handling, fabrication processes (e.g., laser drilling, screen printing), and compatibility with assembly and packaging techniques.
- Reliability and Environmental Considerations:Design the substrate to withstand environmental stresses such as temperature cycling, mechanical shock, and humidity. Consider reliability features such as conformal coating, hermetic sealing, and ruggedization as needed.
- Electrical Testing:Plan for electrical testing and characterization of the substrate during and after fabrication to ensure that it meets performance specifications and quality standards.
- Documentation and Communication: Clearly document the design specifications, requirements, and constraints, and maintain open communication with manufacturers and stakeholders throughout the design process to address any issues and ensure successful implementation.
These guidelines may vary depending on the specific application, performance requirements, and manufacturing capabilities, so it’s essential to tailor the design approach accordingly. Working closely with experienced engineers and manufacturers can help ensure that the Microtrace Ceramic Substrate meets the desired performance, reliability, and cost targets.
What is the Microtrace Ceramic Substrate Fabrication Process?
The fabrication process for Microtrace Ceramic Substrates involves several steps to create the ceramic substrate and pattern conductive traces and components on its surface. Here’s a general overview of the process:
- Material Selection: Choose ceramic materials such as alumina (Al2O3) or aluminum nitride (AlN) with suitable properties for the intended application, including thermal conductivity, dielectric constant, mechanical strength, and compatibility with fabrication processes.
- Substrate Preparation:Start with ceramic sheets or panels of the selected material. These substrates are typically prepared by forming, shaping, and sintering ceramic powders into the desired shape and dimensions.
- Surface Preparation: Clean the surface of the ceramic substrate to remove any contaminants or residues that could affect the adhesion of subsequent layers.
- Dielectric Layer Deposition: Apply dielectric materials onto the ceramic substrate surface using techniques such as screen printing, spraying, or chemical vapor deposition (CVD). These dielectric layers provide electrical insulation between conductive traces and components.
- Conductive Trace Patterning: Use photolithography or screen printing techniques to pattern conductive traces onto the surface of the ceramic substrate. Photolithography involves applying a photoresist layer to the substrate, exposing it to UV light through a mask with the desired trace pattern, and developing the photoresist to reveal the pattern. Screen printing involves using a stencil or screen to deposit conductive ink onto the substrate surface.
- Conductive Material Deposition: Deposit conductive materials such as silver, gold, or copper onto the substrate surface to form the conductive traces. This can be done using techniques such as sputtering, evaporation, electroplating, or screen printing, depending on the desired thickness and conductivity requirements.
- Component Attachment:Attach electronic components such as integrated circuits (ICs), resistors, capacitors, and other active or passive devices onto the substrate surface using soldering, bonding, or flip-chip assembly techniques.
- Encapsulation and Packaging: Optionally, encapsulate the substrate and components with protective materials such as epoxy resin or silicone to provide mechanical support, moisture resistance, and environmental protection. Package the substrate into the final form factor required for the application.
- Testing and Quality Control:Perform electrical testing and inspection to ensure that the fabricated Microtrace Ceramic Substrate meets the desired performance specifications and quality standards. This may include continuity testing, impedance measurement, insulation resistance testing, and visual inspection.
- Finishing and Post-Processing: Complete any finishing steps such as trimming excess material, cleaning, labeling, and packaging the finished substrates for shipment or further assembly.
Throughout the fabrication process, strict quality control measures are typically employed to ensure consistency, reliability, and performance of the Microtrace Ceramic Substrates. Additionally, the specific techniques and equipment used may vary depending on factors such as substrate material, design complexity, and manufacturing capabilities. Collaboration with experienced engineers and manufacturers can help optimize the fabrication process for a particular application.
How do you manufacture a Microtrace Ceramic Substrate?
Manufacturing a Microtrace Ceramic Substrate involves several key steps, from material preparation to final inspection. Here’s a detailed overview of the typical manufacturing process:
- Material Selection: Choose ceramic materials with appropriate properties for the application, such as alumina (Al2O3) or aluminum nitride (AlN), based on considerations like thermal conductivity, dielectric constant, and mechanical strength.
- Substrate Formation: Form the ceramic material into sheets or panels of the desired size and thickness through processes like pressing, casting, or tape casting. This step may involve mixing ceramic powders with binders and additives, shaping the mixture, and then drying or firing it to create a solid substrate.
- Surface Preparation: Clean the surface of the ceramic substrate to remove any contaminants or residues that could affect subsequent processing steps.
- Dielectric Layer Deposition:Apply dielectric materials onto the ceramic substrate surface to provide electrical insulation between conductive traces and components. This can be done through methods like screen printing, spraying, or chemical vapor deposition (CVD). Multiple layers may be applied and fired sequentially to achieve the desired dielectric thickness.
- Conductive Trace Patterning: Use photolithography or screen printing techniques to pattern the conductive traces onto the substrate surface. Photolithography involves applying a photoresist layer, exposing it to UV light through a mask with the desired trace pattern, and developing the photoresist to reveal the pattern. Screen printing uses a stencil or screen to deposit conductive ink onto the substrate surface.
- Conductive Material Deposition: Deposit conductive materials such as silver, gold, or copper onto the substrate surface to form the conductive traces. This can be accomplished through methods like sputtering, evaporation, electroplating, or screen printing, depending on the desired thickness and conductivity requirements.
- Component Attachment: Attach electronic components such as integrated circuits (ICs), resistors, capacitors, and other devices onto the substrate surface using techniques like soldering, bonding, or flip-chip assembly. Precision placement and alignment are crucial to ensure proper functionality and reliability.
- Encapsulation and Packaging: Optionally, encapsulate the substrate and components with protective materials such as epoxy resin or silicone to provide mechanical support, moisture resistance, and environmental protection. The substrate may then be packaged into the final form factor required for the application.
- Testing and Quality Control: Perform thorough electrical testing and inspection to verify that the fabricated Microtrace Ceramic Substrate meets the specified performance requirements and quality standards. This may include continuity testing, impedance measurement, insulation resistance testing, and visual inspection.
- Finishing and Post-Processing: Complete any finishing steps such as trimming excess material, cleaning, labeling, and packaging the finished substrates for shipment or further assembly.
Throughout the manufacturing process, strict quality control measures are typically implemented to ensure consistency, reliability, and performance of the Microtrace Ceramic Substrates. Collaboration between engineers, designers, and manufacturing experts is essential to optimize the process for a specific application and ensure the highest possible quality.
How much should a Microtrace Ceramic Substrate cost?
The cost of a Microtrace Ceramic Substrate can vary significantly depending on several factors, including:
- Material: The cost of the ceramic material used in the substrate, such as alumina (Al2O3) or aluminum nitride (AlN), can vary based on factors like purity, particle size, and supplier pricing.
- Manufacturing Complexity: The complexity of the substrate design, including the number of layers, the intricacy of the trace patterns, and the precision required in manufacturing, can impact the cost. More complex designs may require specialized equipment and processes, increasing manufacturing expenses.
- Size and Thickness: The size and thickness of the substrate affect material usage and processing time, which can influence the overall cost.
- Quantity: Economies of scale often apply in manufacturing, meaning that larger production volumes typically lead to lower per-unit costs due to efficiencies in material procurement, processing, and labor.
- Quality and Performance Requirements: Substrates manufactured to meet specific quality standards, performance specifications, and reliability requirements may incur additional costs for testing, inspection, and quality control measures.
- Additional Features: Optional features such as encapsulation, packaging, surface finishing, and customization may add to the overall cost.
- Supplier and Location: The choice of supplier and their geographic location can impact costs due to differences in labor rates, overhead expenses, and shipping logistics.
To get an accurate cost estimate for a Microtrace Ceramic Substrate, it’s essential to consult with manufacturers or suppliers who specialize in ceramic substrate fabrication. They can provide detailed quotations based on your specific design requirements, quantity needs, and desired quality standards. Additionally, considering multiple suppliers and comparing quotes can help identify the most cost-effective option while ensuring the desired level of quality and performance.
What is Microtrace Ceramic Substrate base material?
The base material for a Microtrace Ceramic Substrate is typically a ceramic material chosen for its thermal conductivity, electrical insulation properties, mechanical strength, and compatibility with microelectronic fabrication processes. Two common ceramic materials used as base substrates for microelectronics applications are alumina (Al2O3) and aluminum nitride (AlN).
- Alumina (Al2O3):Alumina ceramic substrates are widely used in microelectronics due to their excellent thermal conductivity, high dielectric strength, and relatively low cost. They are suitable for applications requiring high-power handling capability and good mechanical stability. Alumina substrates are available in various purity grades and can be processed using techniques such as tape casting, pressing, and firing.
- Aluminum Nitride (AlN): Aluminum nitride ceramic substrates offer even higher thermal conductivity than alumina, making them well-suited for applications requiring efficient heat dissipation, such as high-power RF devices and LED packaging. AlN substrates also exhibit good electrical insulation properties, low coefficient of thermal expansion (CTE), and compatibility with semiconductor fabrication processes.
These ceramic materials serve as the foundation upon which conductive traces, components, and other electronic structures are patterned to create the Microtrace Ceramic Substrate. The choice between alumina and aluminum nitride depends on factors such as thermal management requirements, electrical performance specifications, and cost considerations for a particular application.
Which company makes Microtrace Ceramic Substrates?
Microtrace Ceramic Substrates are produced by several companies, including major manufacturers such as Kyocera, Murata, TDK, NGK Insulators, and others. These companies have extensive experience and technical expertise in the microelectronics industry, capable of providing high-quality Microtrace Ceramic Substrates to meet various application requirements.
Representing our company, we are also one of the manufacturers of Microtrace Ceramic Substrates. We have advanced manufacturing equipment and a professional technical team dedicated to providing customers with high-quality products and customized solutions. Our manufacturing process strictly adheres to industry standards and quality management systems to ensure stable and reliable product performance.
Our company has the following advantages in manufacturing Microtrace Ceramic Substrates:
- Advanced Process Technology: We have advanced manufacturing equipment and process technology to achieve high-precision production of Microtrace Ceramic Substrates, meeting the specific requirements of customers.
- Professional Team: We have an experienced and skilled team capable of providing comprehensive technical support and services from design to production, ensuring the best quality and performance of products.
- Customized Solutions: We can provide customized solutions according to customer requirements, including design optimization, process adjustment, and product improvement to meet the needs of different application scenarios.
- Strict Quality Control: We strictly implement quality management systems to comprehensively test and control raw materials, production processes, and finished products to ensure stable and reliable product quality.
Through our efforts and professional expertise, we believe that we can provide customers with high-quality Microtrace Ceramic Substrates, supporting their product performance and competitiveness.
What are the 7 qualities of good customer service?
Good customer service is characterized by several key qualities that contribute to positive interactions and experiences for customers. Here are seven qualities:
- Responsiveness: A good customer service team responds promptly to customer inquiries, concerns, and requests. They acknowledge messages quickly and provide timely assistance to address customer needs.
- Empathy: Empathy involves understanding and acknowledging the customer’s feelings, perspectives, and situations. Good customer service representatives listen actively, show genuine concern for the customer’s issues, and strive to empathize with their experiences.
- Clear Communication: Effective communication is essential in customer service interactions. Customer service representatives should communicate clearly and concisely, using language that is easy to understand. They should provide relevant information, answer questions accurately, and avoid jargon or technical language when necessary.
- Problem-Solving Skills: Good customer service involves the ability to identify and resolve customer problems and issues effectively. Customer service representatives should be resourceful, knowledgeable about products or services, and empowered to find solutions that meet the customer’s needs.
- Professionalism:Professionalism encompasses various aspects of behavior and conduct, including politeness, courtesy, and respectfulness. Good customer service representatives maintain a professional demeanor, even in challenging situations, and treat customers with dignity and respect.
- Reliability: Reliable customer service involves consistency and dependability in meeting customer expectations. Customers should trust that the company will deliver on its promises, follow through with commitments, and provide consistent service quality over time.
- Proactive Engagement: Good customer service goes beyond reactive responses to customer inquiries or issues. It involves proactive engagement, such as reaching out to customers with relevant information, anticipating their needs, and offering assistance before problems arise.
By embodying these qualities, businesses can cultivate positive relationships with their customers, enhance satisfaction and loyalty, and differentiate themselves in the competitive marketplace.
FAQs
What are Microtrace Ceramic Substrates?
Microtrace Ceramic Substrates are ceramic materials used as the base for electronic circuits and components. They feature precise patterning of conductive traces and components at a micro-scale level, making them suitable for advanced electronics applications.
What are the benefits of using Microtrace Ceramic Substrates?
Microtrace Ceramic Substrates offer several advantages, including excellent thermal conductivity, mechanical strength, and electrical insulation properties. They enable the creation of compact and high-performance electronic devices with efficient heat dissipation and reliable operation.
What materials are commonly used in Microtrace Ceramic Substrates?
Common materials used in Microtrace Ceramic Substrates include alumina (Al2O3) and aluminum nitride (AlN). These ceramic materials offer desirable properties such as thermal conductivity, dielectric strength, and compatibility with microelectronics fabrication processes.
What applications are Microtrace Ceramic Substrates used for?
Microtrace Ceramic Substrates find applications in various industries, including telecommunications, aerospace, automotive, medical devices, and consumer electronics. They are used in products such as RF/microwave components, power modules, LED packages, sensors, and MEMS devices.
How are Microtrace Ceramic Substrates manufactured?
The manufacturing process for Microtrace Ceramic Substrates involves several steps, including material preparation, substrate formation, surface preparation, conductive trace patterning, conductive material deposition, component attachment, encapsulation, testing, and finishing.
What factors should be considered when designing Microtrace Ceramic Substrates?
Design considerations for Microtrace Ceramic Substrates include material selection, thermal management, trace layout and routing, dielectric layers, component placement, signal integrity, manufacturability, reliability, and environmental considerations.
Where can I purchase Microtrace Ceramic Substrates?
Microtrace Ceramic Substrates can be purchased from specialized manufacturers, suppliers, or distributors that specialize in electronic components and materials. It’s essential to choose a reputable supplier with expertise in ceramic substrate fabrication and a track record of delivering high-quality products.