Microwave Circuit PCB Manufacturer
Microwave Circuit PCB Manufacturer,Microwave Circuit PCBs are specialized printed circuit boards designed to handle high-frequency signals ranging from 1 GHz to 300 GHz. Engineered with materials like PTFE composites or ceramic-filled hydrocarbons, they maintain low dielectric loss and stable electrical properties crucial for high-frequency applications. These PCBs feature controlled impedance traces, precise routing, and advanced grounding techniques to ensure signal integrity and minimize losses. Widely used in radar systems, satellite communications, and wireless networks, Microwave Circuit PCBs play a pivotal role in enabling the performance and reliability of modern high-frequency electronic systems.
What is a Microwave Circuit PCB?
A Microwave Circuit PCB (Printed Circuit Board) is a specialized type of electronic circuit board designed to handle high-frequency signals typically in the microwave range of 1 GHz to 300 GHz. These PCBs are crucial in applications such as radar systems, satellite communications, and wireless networks, where high-frequency performance is essential.
Microwave PCBs differ significantly from standard PCBs in terms of materials and design to accommodate the unique challenges posed by high frequencies. At microwave frequencies, ordinary PCB materials like FR-4 can exhibit excessive signal loss and dispersion, so materials with lower dielectric losses and better high-frequency performance, such as PTFE (Polytetrafluoroethylene) composites, are used.
Design considerations for microwave PCBs include the precise control of the impedance, minimization of signal loss, and management of thermal issues. Features such as embedded passives, careful routing of signal paths, and controlled impedance traces are common. Microwave PCBs may also incorporate advanced techniques such as microstrip, stripline, or coplanar waveguide to manage signal integrity.
Manufacturing microwave PCBs requires high precision to ensure that the dimensions and tolerances necessary to maintain the integrity of high-frequency signals are met. Specialized equipment and expertise are required to fabricate and test these boards, reflecting their complexity and importance in modern high-frequency electronic applications.
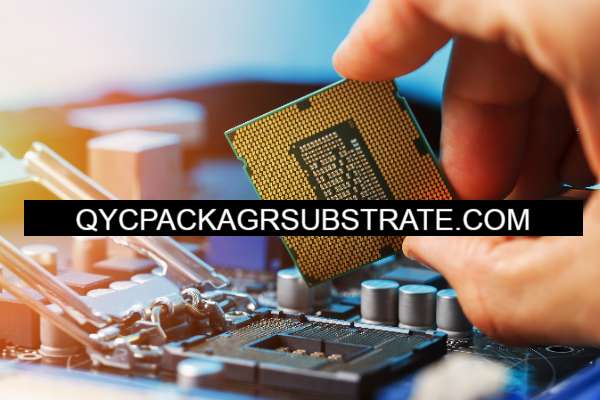
Microwave Circuit PCB Manufacturer
What are the Microwave Circuit PCB Design Guidelines?
Microwave circuit PCB design guidelines are essential principles and practices that engineers follow when designing printed circuit boards for high-frequency applications. These guidelines aim to ensure optimal performance, signal integrity, and reliability of the circuits at microwave frequencies. Here are some key guidelines:
- Material Selection: Choose PCB materials with low dielectric loss and consistent electrical properties across a wide frequency range. Common materials include PTFE (e.g., Rogers RO4000 series), ceramic-filled hydrocarbon (e.g., Nelco N4000), or other specialized substrates.
- Trace Width and Spacing: Maintain appropriate trace widths and spacing to achieve the desired characteristic impedance (typically 50 or 75 ohms). Use impedance calculation tools or formulas to determine trace dimensions accurately.
- Controlled Impedance: Ensure controlled impedance throughout the transmission lines to minimize signal reflections and maintain signal integrity. Design traces with consistent width, thickness, and dielectric properties.
- Grounding: Implement a solid and continuous ground plane to minimize ground loops and provide a stable reference for signal return paths. Ground vias should be strategically placed to maintain low impedance ground connections.
- Signal Routing: Keep signal traces short and direct to minimize signal loss and distortion. Use impedance-matched transmission lines for high-frequency signals and avoid sharp bends or corners.
- Component Placement: Place components carefully to minimize parasitic capacitance and inductance. Position high-frequency components close to each other and use short connections to reduce signal path lengths.
- Thermal Management: Consider thermal issues, especially for high-power applications. Use thermal vias and thermal pads to dissipate heat efficiently and prevent overheating of components.
- EMI/EMC Considerations: Implement shielding techniques such as grounded metal enclosures or shielding cans to reduce electromagnetic interference (EMI) and ensure electromagnetic compatibility (EMC) with other nearby circuits.
- Simulation and Testing: Use electromagnetic simulation software to analyze and optimize the design before fabrication. Perform thorough testing and validation of the fabricated PCB to verify performance against specifications.
- Documentation: Maintain detailed documentation of the design, including schematic diagrams, layout files, and manufacturing notes, to facilitate troubleshooting, future revisions, and reproduction of the PCB.
By following these guidelines, engineers can design microwave circuit PCBs that meet the stringent requirements of high-frequency applications, ensuring reliable performance and signal integrity.
What is the Microwave Circuit PCB Fabrication Process?
The fabrication process for microwave circuit PCBs involves several steps, each crucial for ensuring the performance and reliability of the final product. Here’s an overview of the typical fabrication process:
- Design: The process begins with the design of the PCB layout using specialized software. Engineers lay out the circuit components, traces, and other features according to the design requirements, considering factors like signal integrity, impedance control, and thermal management.
- Material Selection: Select appropriate PCB substrate materials with low dielectric loss and consistent electrical properties at microwave frequencies. Common materials include PTFE (Polytetrafluoroethylene) composites like Rogers RO4000 series or high-frequency laminates such as Nelco N4000.
- Preparation of Substrate: The chosen substrate material is prepared by cutting it to the required size and cleaning its surface to remove any contaminants that could affect the adhesion of the copper layers.
- Copper Cladding: Copper foil is laminated onto one or both sides of the substrate material using heat and pressure. The thickness of the copper foil is chosen based on the current-carrying capacity and impedance requirements of the PCB.
- Circuit Patterning: A photosensitive resist material is applied over the copper foil, and the PCB layout design is transferred onto it using a photomask and UV light exposure. After exposure, the resist is developed, leaving behind a patterned layer of resist that protects the areas of copper to be retained.
- Etching: The PCB is submerged in an etchant solution, typically an acid, which selectively removes the exposed copper not protected by the resist. This etching process defines the traces and features of the PCB layout.
- Resist Stripping: The remaining resist material is removed from the PCB surface, leaving behind the desired copper traces and features.
- Surface Finish: Depending on the application, surface finish may be applied to the exposed copper surfaces to enhance solderability, prevent oxidation, and improve electrical performance. Common surface finishes for microwave PCBs include immersion gold, immersion silver, or electroless nickel immersion gold (ENIG).
- Drilling: Precision CNC drilling machines are used to drill holes for component mounting and vias. These holes are plated to provide electrical continuity between the different layers of the PCB.
- Plating and Layer Build-Up: Additional copper layers may be added to the PCB through a process called electroplating. Each layer is patterned and etched as required to create the desired circuitry. The process may be repeated to build up multiple layers.
- Final Inspection: The fabricated PCB undergoes rigorous inspection to verify dimensional accuracy, trace continuity, and quality of surface finish. Any defects or irregularities are identified and corrected before proceeding.
- Testing: The finished PCB is subjected to electrical testing to ensure that it meets the specified performance criteria, including impedance matching, signal integrity, and functionality.
Once the fabrication process is complete and the PCB passes all quality assurance tests, it is ready for assembly, where components are mounted onto the board to create the final electronic device or system.
How do you manufacture a Microwave Circuit PCB?
Manufacturing a microwave circuit PCB involves several specialized steps tailored to the requirements of high-frequency applications. Here’s a detailed overview of the manufacturing process:
- Design and Layout:Engineers create the PCB layout using software specifically designed for high-frequency circuit design. They consider factors such as trace impedance, signal integrity, and thermal management during the layout process.
- Material Selection: Choose PCB substrate materials with low dielectric loss and consistent electrical properties at microwave frequencies. Common materials include PTFE (Polytetrafluoroethylene) composites like Rogers RO4000 series or high-frequency laminates such as Nelco N4000.
- Preparation of Substrate: Cut the substrate material to the required size and clean its surface to remove any contaminants that could affect adhesion.
- Copper Cladding: Laminate copper foil onto one or both sides of the substrate using heat and pressure. The thickness of the copper foil is chosen based on the current-carrying capacity and impedance requirements.
- Circuit Patterning: Apply a photosensitive resist material over the copper foil and transfer the PCB layout design onto it using a photomask and UV light exposure. Develop the resist to leave behind a patterned layer protecting the areas of copper to be retained.
- Etching: Submerge the PCB in an etchant solution, typically an acid, to selectively remove the exposed copper not protected by the resist. This defines the traces and features of the PCB layout.
- Resist Stripping: Remove the remaining resist material from the PCB surface, leaving behind the desired copper traces and features.
- Surface Finish: Apply surface finish to the exposed copper surfaces to enhance solderability, prevent oxidation, and improve electrical performance. Common surface finishes include immersion gold, immersion silver, or electroless nickel immersion gold (ENIG).
- Drilling:Use precision CNC drilling machines to drill holes for component mounting and vias. These holes are plated to provide electrical continuity between the different layers of the PCB.
- Plating and Layer Build-Up: Add additional copper layers to the PCB through electroplating. Each layer is patterned and etched as required to create the desired circuitry. Repeat this process to build up multiple layers.
- Final Inspection: Conduct rigorous inspection to verify dimensional accuracy, trace continuity, and quality of surface finish. Correct any defects or irregularities before proceeding.
- Testing: Subject the finished PCB to electrical testing to ensure it meets specified performance criteria, including impedance matching, signal integrity, and functionality.
Once the PCB passes all quality assurance tests, it is ready for assembly, where components are mounted onto the board to create the final electronic device or system.
How much should a Microwave Circuit PCB cost?
The cost of a microwave circuit PCB can vary significantly depending on several factors, including the complexity of the design, the choice of materials, the number of layers, the size of the board, and the quantity ordered. Here are some considerations that can affect the cost:
- Design Complexity: PCBs with complex designs, such as high-density interconnects (HDIs) or intricate RF/microwave circuitry, may require more advanced manufacturing processes, leading to higher costs.
- Material Selection: High-frequency PCB materials like PTFE composites or specialized laminates tend to be more expensive than standard FR-4. The choice of material can significantly impact the overall cost.
- Number of Layers: Multi-layer PCBs with more layers require additional processing steps and materials, leading to higher costs compared to single-layer or double-layer boards.
- Size and Thickness: Larger PCBs or boards with greater thickness may require more material and processing time, resulting in higher costs.
- Surface Finish and Features: The type of surface finish (e.g., immersion gold, HASL, ENIG) and additional features like impedance control, blind vias, or buried vias can contribute to the overall cost.
- Quantity: Economies of scale typically apply, meaning that larger production quantities can result in lower per-unit costs due to efficiencies in manufacturing and material utilization.
- Lead Time: Expedited manufacturing or shorter lead times may incur additional costs compared to standard turnaround times.
As a rough estimate, the cost of a microwave circuit PCB can range from a few dollars for simple single-layer boards to hundreds or even thousands of dollars for complex multi-layer boards with advanced features. For a more accurate cost estimate, it’s recommended to consult with PCB manufacturers and provide detailed specifications of your design requirements.
What is Microwave Circuit PCB base material?
The base material for microwave circuit PCBs is crucial for achieving high-performance at microwave frequencies. Several materials are commonly used due to their excellent electrical properties, low dielectric loss, and stability over a wide range of frequencies. Some of the most popular base materials for microwave circuit PCBs include:
- PTFE (Polytetrafluoroethylene) Composite: PTFE-based materials, such as those in the Rogers RO4000 series (e.g., RO4350B, RO4003C), are widely used in microwave PCBs. PTFE has very low dielectric loss and maintains stable electrical properties at high frequencies.
- Ceramic-filled Hydrocarbon: Materials like Nelco N4000-13EP or Taconic TLX series are examples of ceramic-filled hydrocarbon substrates. These materials offer excellent electrical performance and thermal stability, making them suitable for high-frequency applications.
- Rogers RT/Duroid: Rogers RT/duroid materials, such as RT/duroid 5880, are high-performance laminates known for their low dielectric constant and low loss tangent. They provide consistent electrical properties across a wide frequency range.
- Isola FR408: Isola FR408 is a high-performance epoxy laminate with woven glass reinforcement. It offers excellent electrical properties and is suitable for applications requiring tight impedance control and signal integrity.
- Arlon AD series: Arlon AD series materials are based on PTFE and ceramic fillers, offering low loss tangent and stable dielectric constant over temperature and frequency.
These base materials are engineered to have specific electrical properties, such as dielectric constant (εr), dissipation factor (Df), and thermal conductivity, that are critical for maintaining signal integrity and minimizing losses in microwave circuits. The choice of base material depends on factors such as frequency of operation, power handling requirements, environmental conditions, and cost considerations.
Which company makes Microwave Circuit PCBs?
Many companies specialize in manufacturing microwave circuit PCBs. Some well-known companies include Rogers Corporation, Taconic Advanced Dielectric Division, Isola Group, Arlon Electronic Materials, and Panasonic Electronic Materials. These companies have extensive experience and expertise in the microwave and RF fields, producing PCB materials with excellent electrical performance and stability to meet the demands of high-frequency, high-performance applications.
Of course, our company can also produce microwave circuit PCBs. We have advanced manufacturing equipment and a skilled technical team capable of customizing various types of PCBs, including microwave circuit PCBs, according to customer requirements. We use high-quality base materials such as the PTFE series, Rogers RO4000 series, Isola FR408, and others, which exhibit excellent electrical properties and stability suitable for high-performance applications within the microwave frequency range.
Throughout the manufacturing process, we maintain strict control over every aspect to ensure that the PCBs meet the quality and performance standards required by our customers. With a comprehensive quality management system, including rigorous inspection and testing procedures, we ensure that each PCB can reliably operate under high-frequency conditions. Additionally, we offer flexible customization services to tailor the PCBs to the specific design requirements of our customers, catering to various application scenarios.
As your partner, we are committed to providing you with high-quality, high-performance microwave circuit PCBs to help you achieve project success. Our team is dedicated to serving you and collaborating to drive industry development and progress.
What are the 7 qualities of good customer service?
Good customer service is essential for building strong relationships with customers and fostering loyalty. Here are seven qualities that characterize excellent customer service:
- Responsiveness:A good customer service team is prompt in addressing customer inquiries, concerns, and requests. They respond quickly to emails, phone calls, and messages, demonstrating that they value the customer’s time and are eager to assist.
- Empathy: Empathy is the ability to understand and share the feelings of others. A customer service representative who empathizes with customers demonstrates genuine concern for their needs and is better equipped to provide personalized solutions.
- Clear Communication:Effective communication is key to providing good customer service. Customer service representatives should communicate clearly and concisely, ensuring that customers understand the information provided and the steps to resolve their issues.
- Knowledgeability: Customers expect to receive accurate information and expert advice from customer service representatives. A good customer service team is well-trained and knowledgeable about the company’s products, services, policies, and procedures.
- Problem-Solving Skills: Good customer service involves identifying and resolving customer issues efficiently and effectively. Customer service representatives should be proactive in finding solutions to problems and demonstrating resourcefulness in challenging situations.
- Professionalism: Professionalism encompasses various attributes such as courtesy, respect, and integrity. Customer service representatives should conduct themselves professionally at all times, maintaining a positive attitude and upholding the company’s values and standards.
- Follow-Up: Following up with customers after resolving their issues demonstrates a commitment to customer satisfaction and reinforces the relationship. Good customer service includes checking in with customers to ensure that their needs have been met and addressing any additional concerns they may have.
By embodying these qualities, businesses can provide exceptional customer service that exceeds expectations, builds trust, and fosters long-term customer loyalty.
FAQs
What is a Microwave Circuit PCB?
A Microwave Circuit PCB is a specialized type of printed circuit board designed to handle high-frequency signals typically in the microwave range of 1 GHz to 300 GHz. These PCBs are essential for applications such as radar systems, satellite communications, and wireless networks.
What are the key features of Microwave Circuit PCBs?
Microwave Circuit PCBs require materials with low dielectric loss and consistent electrical properties across a wide frequency range. They often incorporate controlled impedance traces, precision routing, and grounding techniques to maintain signal integrity and minimize losses.
What materials are used in Microwave Circuit PCBs?
Common materials used in Microwave Circuit PCBs include PTFE (Polytetrafluoroethylene) composites, ceramic-filled hydrocarbons, and high-frequency laminates like Rogers RO4000 series. These materials offer low dielectric loss and stable electrical properties at microwave frequencies.
How are Microwave Circuit PCBs fabricated?
Fabricating Microwave Circuit PCBs involves specialized processes such as precision etching, controlled impedance routing, and surface finish application. These processes are tailored to the requirements of high-frequency applications and often require advanced manufacturing equipment and expertise.
What are the design considerations for Microwave Circuit PCBs?
Designing Microwave Circuit PCBs requires careful attention to factors such as impedance control, signal routing, grounding, and thermal management. Engineers must optimize the layout and materials to minimize signal loss, maintain signal integrity, and manage thermal issues.
What are some common applications of Microwave Circuit PCBs?
Microwave Circuit PCBs are used in a wide range of applications, including radar systems, satellite communications, wireless networks, microwave radios, and aerospace and defense electronics. They are critical components in high-frequency electronic systems where performance and reliability are paramount.
How can I ensure the quality of Microwave Circuit PCBs?
Ensuring the quality of Microwave Circuit PCBs involves working with reputable PCB manufacturers who have experience and expertise in high-frequency PCB fabrication. It’s essential to specify the required electrical properties, material characteristics, and performance criteria to meet the demands of the application.