Multilayer Substrate Manufacturer
Multilayer Substrate Manufacturer,Multilayer substrates are sophisticated materials crucial in modern electronics. Comprising multiple layers of diverse materials, such as fiberglass-reinforced epoxy resin (FR4) and conductive copper foils, these substrates facilitate the intricate interconnection of electronic components. Their layered structure enables compact designs, optimal signal integrity, and efficient thermal management in printed circuit boards (PCBs) and electronic devices. Multilayer substrates play a pivotal role in advancing technology, offering enhanced functionality, reliability, and performance in various applications, from consumer electronics to aerospace systems.
What is a Multilayer Substrate?
A multilayer substrate refers to a type of material used in electronics, particularly in the manufacturing of printed circuit boards (PCBs). It consists of multiple layers of different materials laminated together to form a single structure. Each layer serves a specific purpose, such as providing electrical conductivity, insulation, or mechanical support.
The construction of a multilayer substrate typically involves alternating layers of conductive copper foil and insulating substrate material, such as fiberglass-reinforced epoxy resin (FR4). These layers are bonded together using heat and pressure to create a solid, rigid board.
Multilayer substrates offer several advantages over single-layer PCBs, including increased routing density, improved signal integrity, and better thermal management. They also allow for the integration of complex electronic components and circuits into a smaller footprint, making them ideal for compact and high-performance electronic devices.
In addition to their use in PCBs, multilayer substrates are also employed in other electronic applications, such as integrated circuits (ICs), microwave circuits, and radio frequency (RF) modules. The design and fabrication of multilayer substrates require specialized knowledge and manufacturing processes to ensure optimal performance and reliability.
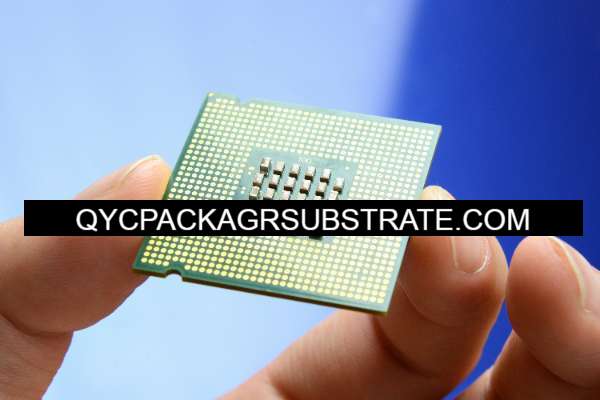
Multilayer Substrate Manufacturer
What are the Multilayer Substrate Design Guidelines?
Designing with multilayer substrates requires careful consideration to ensure optimal performance and reliability. Here are some key design guidelines:
- Layer Stackup Design: Plan the arrangement of layers carefully, considering signal integrity, power distribution, and thermal management. Typically, high-speed signal layers are placed between power and ground planes to minimize electromagnetic interference (EMI) and signal losses.
- Ground and Power Plane Placement: Dedicate internal layers for ground and power planes to provide low-impedance paths for return currents and stable power distribution. Avoid splitting ground planes to minimize ground loops and EMI.
- Signal Routing: Route high-speed signals on inner layers close to reference planes to minimize signal distortions and impedance mismatches. Use controlled impedance routing for critical signals to maintain signal integrity.
- Via Design: Use vias strategically to connect traces between different layers. Place vias close to signal pads to minimize stub length and impedance disruptions. For high-speed signals, consider using blind or buried vias to reduce signal path length.
- Decoupling Capacitors: Place decoupling capacitors near the power pins of ICs to suppress noise and provide clean power. Distribute decoupling capacitors evenly across the PCB to minimize inductance.
- Thermal Management: Ensure proper thermal dissipation by incorporating thermal vias and spreading heat-generating components across multiple layers. Place sensitive components away from heat sources and provide adequate airflow or heatsinking.
- Signal Integrity Analysis: Perform signal integrity simulations and analysis to verify signal quality, impedance matching, and noise margins. Use tools like signal integrity simulators and electromagnetic field solvers to optimize the design.
- EMI/EMC Considerations: Design the PCB to minimize electromagnetic interference (EMI) emissions and ensure compliance with electromagnetic compatibility (EMC) standards. This includes proper grounding, shielding, and layout techniques to reduce noise coupling.
- Manufacturability: Consider manufacturability during the design phase by adhering to PCB fabrication and assembly constraints. Ensure that the design is compatible with the chosen manufacturing processes, such as PCB layer buildup and via types.
- Documentation and Collaboration: Document the design thoroughly with clear schematics, layout guidelines, and design notes. Collaborate with PCB manufacturers and assembly houses to address any design concerns and ensure a smooth manufacturing process.
Following these guidelines can help ensure a successful multilayer substrate design that meets performance requirements and reliability standards.
What is the Multilayer Substrate Fabrication Process?
The fabrication process of multilayer substrates involves several steps to create the layered structure required for printed circuit boards (PCBs) or other electronic devices. Here’s an overview of the typical multilayer substrate fabrication process:
- Layer Stackup Design: The process begins with the design of the layer stackup, which determines the arrangement of conductive and insulating layers in the multilayer substrate. This includes selecting the number of layers, the type of materials used (such as copper foils and substrate laminates), and the order in which they are stacked.
- Preparation of Substrate Materials: The substrate materials, typically fiberglass-reinforced epoxy resin (FR4) or similar laminates, are prepared by cutting them to the required size and cleaning them to remove any contaminants that could affect adhesion during lamination.
- Copper Foil Preparation: Thin copper foils are cleaned and treated to improve adhesion to the substrate material. This may involve processes such as roughening, cleaning, and applying a thin layer of adhesive to promote bonding.
- Circuit Patterning: A photoresist layer is applied to the copper foils, and the desired circuit patterns are transferred onto the foils using photolithography techniques. This involves exposing the photoresist to ultraviolet (UV) light through a photomask, developing the exposed pattern, and etching away the unprotected copper to leave behind the circuit traces.
- Lamination:The prepared substrate materials and copper foils are stacked together in the desired layer sequence, with adhesive layers placed between them. The stack is then laminated under heat and pressure to bond the layers together into a single structure.
- Drilling: Precision holes, known as vias, are drilled through the multilayer substrate to connect traces between different layers. These vias may be through-hole vias that penetrate all layers or blind vias that connect only certain layers.
- Electroplating: After drilling, the vias are plated with copper to provide conductivity between the different layers. This involves depositing a thin layer of copper inside the vias through an electroplating process, which builds up the thickness of the copper to the required level.
- Surface Finishing: The exposed copper surfaces on the outer layers of the multilayer substrate are coated with a surface finish to protect them from oxidation and provide solderability during assembly. Common surface finishes include electroless nickel immersion gold (ENIG), immersion silver, and HASL (hot air solder leveling).
- Final Etching and Inspection: Any excess copper on the outer layers is etched away to define the final circuit patterns. The multilayer substrate is then inspected for defects, such as shorts, opens, or misalignments, using automated optical inspection (AOI) or other inspection methods.
- Routing and Testing: After fabrication, the multilayer substrates are routed into individual PCBs, and electrical testing is performed to ensure that all circuits meet the required specifications. This may include continuity testing, impedance testing, and functionality testing.
By following these steps, manufacturers can fabricate multilayer substrates with the desired layer stackup, circuit patterns, and electrical characteristics for use in various electronic applications.
How do you manufacture a Multilayer Substrate?
Manufacturing a multilayer substrate involves a series of steps to build up the layered structure required for printed circuit boards (PCBs) or other electronic devices. Here’s a detailed overview of the typical manufacturing process:
- Design and Stackup Planning: The process starts with the design of the multilayer substrate, including determining the number of layers, layer materials, thicknesses, and the overall layer stackup. This design phase considers factors such as signal integrity, power distribution, and thermal management.
- Preparation of Substrate Materials: The base substrate materials, often fiberglass-reinforced epoxy resin (FR4) or similar laminates, are prepared by cutting them to size and cleaning them to remove any contaminants that could affect adhesion during lamination.
- Copper Foil Preparation: Thin copper foils are cleaned and treated to improve adhesion to the substrate material. This may involve processes such as roughening, cleaning, and applying a thin layer of adhesive to promote bonding.
- Circuit Patterning: A photoresist layer is applied to the copper foils, and the desired circuit patterns are transferred onto the foils using photolithography techniques. This involves exposing the photoresist to ultraviolet (UV) light through a photomask, developing the exposed pattern, and etching away the unprotected copper to leave behind the circuit traces.
- Lamination: The prepared substrate materials and copper foils are stacked together in the desired layer sequence, with adhesive layers placed between them. The stack is then laminated under heat and pressure to bond the layers together into a single structure. This step may involve multiple lamination cycles to build up the required number of layers.
- Drilling: Precision holes, known as vias, are drilled through the multilayer substrate to connect traces between different layers. These vias may be through-hole vias that penetrate all layers or blind vias that connect only certain layers.
- Electroplating: After drilling, the vias are plated with copper to provide conductivity between the different layers. This involves depositing a thin layer of copper inside the vias through an electroplating process, which builds up the thickness of the copper to the required level.
- Surface Finishing: The exposed copper surfaces on the outer layers of the multilayer substrate are coated with a surface finish to protect them from oxidation and provide solderability during assembly. Common surface finishes include electroless nickel immersion gold (ENIG), immersion silver, and HASL (hot air solder leveling).
- Final Etching and Inspection: Any excess copper on the outer layers is etched away to define the final circuit patterns. The multilayer substrate is then inspected for defects, such as shorts, opens, or misalignments, using automated optical inspection (AOI) or other inspection methods.
- Routing and Testing: After fabrication, the multilayer substrates are routed into individual PCBs, and electrical testing is performed to ensure that all circuits meet the required specifications. This may include continuity testing, impedance testing, and functionality testing.
By following these steps, manufacturers can produce multilayer substrates with the desired layer stackup, circuit patterns, and electrical characteristics for use in various electronic applications.
How much should a Multilayer Substrate cost?
The cost of a multilayer substrate can vary widely depending on several factors, including the complexity of the design, the number of layers, the materials used, the size of the substrate, and the manufacturing processes involved. Here are some key factors that can influence the cost:
- Number of Layers: Generally, the more layers a multilayer substrate has, the higher the cost. This is because each additional layer requires more materials, processing steps, and precision during fabrication.
- Materials: The choice of substrate materials, such as FR4, high-frequency laminates, or exotic materials like Rogers or Duroid, can impact the cost. Exotic materials tend to be more expensive than standard FR4, but they may offer superior performance for specific applications.
- Copper Weight: Thicker copper foils and higher copper weights can increase the cost of a multilayer substrate due to the increased material costs and the need for more precise manufacturing processes.
- Surface Finish: The type of surface finish used on the substrate, such as ENIG, immersion silver, or HASL, can affect the cost. Some surface finishes are more expensive than others due to the materials and processes involved.
- Complexity of Design: Complex designs with tight tolerances, fine pitch components, high-speed signals, and special features like blind vias or buried vias may require additional processing steps and specialized equipment, which can increase the cost.
- Manufacturing Volume: The volume of multilayer substrates being produced can also impact the cost. Larger production volumes typically result in economies of scale, leading to lower unit costs.
- Lead Time: Shorter lead times often come with higher costs, as rush orders may require expedited processing and additional resources to meet tight deadlines.
To get an accurate cost estimate for a specific multilayer substrate project, it’s best to consult with PCB manufacturers or suppliers. They can provide quotes based on your design specifications and production requirements. Additionally, online PCB cost calculators or quotation tools offered by PCB manufacturers can give you a rough estimate based on input parameters such as board size, layer count, and material choices.
What is Multilayer Substrate base material?
The base material used in multilayer substrates typically consists of layers of fiberglass-reinforced epoxy resin, commonly referred to as FR4. FR4 is a type of composite material composed of woven fiberglass cloth impregnated with epoxy resin.
FR4 is chosen for its excellent electrical insulating properties, mechanical strength, dimensional stability, and cost-effectiveness. It provides a stable substrate for mounting electronic components and routing electrical connections. The fiberglass reinforcement adds strength and rigidity to the material, while the epoxy resin provides insulation and adhesion properties.
In addition to FR4, other materials may be used for specific applications or performance requirements. For example, high-frequency applications may require specialized substrates with low dielectric constants and controlled impedance characteristics. Materials such as Rogers or Duroid are commonly used for these high-frequency applications due to their superior electrical properties.
Overall, the choice of base material for multilayer substrates depends on factors such as the desired electrical performance, mechanical requirements, cost considerations, and compatibility with manufacturing processes.
Which company manufactures Multilayer Substrates?
Several companies manufacture multilayer substrates, including well-known manufacturers such as Foxconn, JLCPCB, Eurocircuits, and Futaihua. These companies have extensive experience and expertise in the electronics manufacturing industry, capable of providing various types and specifications of multilayer substrates to meet different customer needs.
As for our company, we are also a professional electronic manufacturing enterprise with advanced manufacturing equipment and a skilled technical team. We are committed to providing high-quality and reliable multilayer substrates to meet customers’ personalized requirements.
Our multilayer substrate production process strictly follows industry standards and quality management systems, ensuring stable and reliable product quality. We have advanced production equipment, including automated PCB manufacturing lines and precision testing equipment, enabling efficient production of multilayer substrates of various specifications and complexities.
Our technical team has rich experience and professional knowledge, capable of providing customers with comprehensive technical support and solutions. Whether it’s design optimization, process improvement, or quality control, we can provide professional advice and support to ensure products achieve optimal performance and reliability.
In addition to standard FR4 multilayer substrates, we can also provide other types of multilayer substrates according to specific customer requirements, such as high-frequency materials, high-temperature materials, etc. We are committed to establishing long-term and stable cooperation with customers, providing customized solutions, and jointly promoting the development of the electronics industry.
Overall, as a professional electronic manufacturing enterprise, our company has rich experience and professional capabilities, capable of producing various specifications and types of multilayer substrates to provide customers with high-quality products and services. We look forward to cooperating with you to achieve mutual benefits.
What are the 7 qualities of good customer service?
Good customer service is characterized by several key qualities that contribute to positive interactions and customer satisfaction. Here are seven qualities of good customer service:
- Responsiveness: Good customer service involves promptly addressing customer inquiries, concerns, and requests. Responding in a timely manner demonstrates attentiveness to customer needs and shows that their satisfaction is a priority.
- Empathy: Empathy involves understanding and acknowledging the customer’s perspective, feelings, and needs. Empathetic customer service representatives listen actively, express understanding, and demonstrate compassion to build rapport and trust with customers.
- Clarity and Communication: Effective communication is essential for providing good customer service. Customer service representatives should communicate clearly, using simple language and avoiding jargon or technical terms. They should also provide accurate information and instructions to assist customers effectively.
- Problem-Solving Skills: Good customer service requires strong problem-solving skills to resolve customer issues and address challenges effectively. Customer service representatives should be resourceful, analytical, and proactive in finding solutions that meet the customer’s needs and expectations.
- Professionalism:Professionalism involves maintaining a courteous and respectful demeanor when interacting with customers. Customer service representatives should conduct themselves professionally, remaining calm, patient, and composed, even in challenging situations.
- Consistency: Consistency in service delivery is important for building trust and credibility with customers. Good customer service should be consistent across all channels and interactions, ensuring that customers receive the same level of quality and attention every time they engage with the company.
- Follow-Up and Follow-Through: Following up with customers after resolving an issue or completing a transaction demonstrates commitment and care. Good customer service includes following through on promises, commitments, and actions to ensure customer satisfaction and loyalty.
By embodying these qualities, businesses can deliver exceptional customer service experiences that foster positive relationships, loyalty, and repeat business.
FAQs
What are the advantages of multilayer substrates over single-layer PCBs?
Multilayer substrates offer several advantages, including increased routing density, improved signal integrity, better thermal management, and the ability to integrate complex electronic components into a smaller footprint.
How are multilayer substrates manufactured?
The manufacturing process of multilayer substrates involves several steps, including layer stackup design, preparation of substrate materials, copper foil preparation, circuit patterning, lamination, drilling, electroplating, surface finishing, final etching and inspection, and routing and testing.
What materials are used in multilayer substrates?
The base material used in multilayer substrates is typically fiberglass-reinforced epoxy resin, commonly referred to as FR4. Other materials may be used for specific applications or performance requirements, such as high-frequency laminates like Rogers or Duroid.
What are the design guidelines for multilayer substrates?
Design guidelines for multilayer substrates include considerations such as layer stackup design, ground and power plane placement, signal routing, via design, decoupling capacitors, thermal management, signal integrity analysis, EMI/EMC considerations, manufacturability, documentation, and collaboration.
What factors influence the cost of multilayer substrates?
The cost of multilayer substrates can vary depending on factors such as the number of layers, materials used, surface finish, complexity of design, manufacturing volume, and lead time.
Which companies manufacture multilayer substrates?
Several companies manufacture multilayer substrates, including well-known manufacturers such as Foxconn, JLCPCB, Eurocircuits, and Futaihua. Additionally, there are many other PCB manufacturers and suppliers worldwide that offer multilayer substrate fabrication services.