Radar Substrate Manufacturer
Radar Substrate Manufacturer,Radar substrates are critical components in radar systems, designed to support the transmission and reception of radio waves with minimal loss and interference. These substrates typically utilize materials with excellent dielectric properties and high thermal conductivity to ensure efficient signal propagation and heat dissipation. They are engineered with precise impedance control, optimized layer stack-ups, and often incorporate radar-specific features like low loss tangent and controlled thermal expansion. Radar substrates play a crucial role in enhancing radar system performance, enabling accurate detection, tracking, and imaging capabilities in applications ranging from military defense to automotive radar systems for collision avoidance and autonomous driving technologies.
What is a Radar Substrate?
A radar substrate refers to the material used as a base or foundation for radar systems, particularly for the construction of radar antennas. It plays a crucial role in the performance and efficiency of radar systems by supporting the antenna structure and ensuring proper electromagnetic wave propagation.
The substrate material is chosen based on several factors such as its dielectric constant, thermal stability, mechanical strength, and ability to withstand environmental conditions. Common materials used for radar substrates include various types of ceramics, composites, and specialized polymers. These materials are selected to minimize signal losses, maintain structural integrity, and enhance radar sensitivity and resolution.
In addition to the material itself, the substrate’s shape, dimensions, and surface properties are also critical for optimizing radar performance. Engineers design radar substrates to be lightweight yet durable, capable of supporting the antenna elements while maintaining precise alignment and stability over time.
Overall, the radar substrate is a fundamental component in radar technology, providing the necessary physical and electromagnetic foundation for the efficient operation of radar systems across different applications, from military and aerospace to weather monitoring and automotive radar systems.
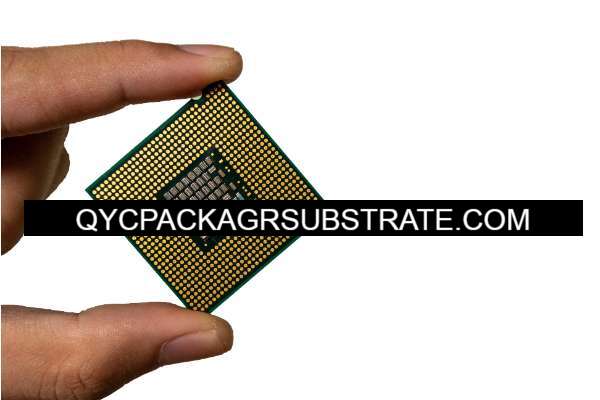
Radar Substrate Manufacturer
What are Radar Substrate Design Guidelines?
Designing radar substrates involves following specific guidelines to ensure optimal performance of radar systems. Here are some key design guidelines:
- Material Selection: Choose a substrate material with a stable dielectric constant over a wide range of frequencies. Common materials include ceramics (such as alumina or aluminum nitride), composites, and specialized polymers (such as PTFE). The material should have low loss tangent to minimize signal attenuation.
- Dielectric Constant: The dielectric constant of the substrate material affects the wavelength and impedance of the signals propagating through the substrate. It should be chosen to match the operating frequency of the radar system for efficient wave propagation and minimal impedance mismatch.
- 3. Dimensional Stability: Ensure the substrate material has low thermal expansion coefficient and excellent dimensional stability over a wide temperature range. This helps maintain the mechanical integrity and alignment of radar components under varying environmental conditions.
- Mechanical Strength: Radar substrates should possess sufficient mechanical strength to support the antenna structure and withstand external mechanical stresses, such as vibrations or impacts. This is crucial for maintaining antenna performance and reliability.
- Surface Finish and Coating: The substrate surface should be smooth and free from imperfections to minimize scattering losses and ensure accurate signal propagation. Surface coatings or treatments may be applied to enhance electrical properties or protect against environmental factors like moisture or corrosion.
- Manufacturability: Consider the ease of manufacturing the radar substrate in terms of machining, forming, and assembly processes. Complex shapes or precision machining may be required to meet design specifications and performance requirements.
- Environmental Durability: Ensure the substrate material is resistant to environmental factors such as humidity, temperature extremes, UV radiation, and chemicals, depending on the operational environment of the radar system.
- Integration with Radar Components: Design the substrate to integrate seamlessly with other radar components, such as feed networks, phase shifters, and reflectors. This includes ensuring proper alignment, electrical connectivity, and thermal management.
- Electrical Properties: Besides dielectric constant, consider other electrical properties such as loss tangent, electrical conductivity, and impedance matching to optimize radar performance and minimize signal loss.
- Testing and Validation: Perform thorough testing and validation of the radar substrate design to ensure it meets performance specifications across all operational conditions and environmental stresses.
By adhering to these radar substrate design guidelines, engineers can develop substrates that enhance radar system performance, reliability, and longevity across a wide range of applications.
What is the Radar Substrate Fabrication Process?
The fabrication process of radar substrates involves several steps to transform chosen materials into functional components that support radar systems. Here is a generalized outline of the radar substrate fabrication process:
- Material Selection: Choose an appropriate substrate material based on the radar system requirements, considering factors such as dielectric constant, mechanical strength, thermal stability, and environmental durability. Common materials include ceramics (e.g., alumina, aluminum nitride), composites, and specialized polymers (e.g., PTFE).
- Material Preparation: Prepare the selected substrate material in accordance with the desired dimensions and specifications. This may involve cutting, shaping, or forming the material into the required size and geometry using techniques such as milling, turning, or laser cutting.
- Surface Treatment: Depending on the application and material type, the substrate surface may undergo treatments such as polishing, coating, or metallization. These treatments can improve surface smoothness, enhance electrical properties, provide corrosion resistance, or facilitate bonding with other radar components.
- Pattern Design and Etching: If the radar substrate requires specific patterns or features (e.g., microstrip lines, antenna elements), design these patterns using CAD (Computer-Aided Design) software. Transfer these designs onto the substrate material through processes like photolithography or screen printing. Etching techniques (e.g., wet chemical etching, dry etching) are then used to define the desired patterns on the substrate surface.
- Metallization and Bonding: Apply metallization layers to the substrate as needed for electrical conductivity or to create interconnections between components. Bonding techniques such as soldering, epoxy bonding, or wire bonding may be used to attach semiconductor devices, connectors, or other components to the substrate.
- Quality Control and Testing: Throughout the fabrication process, conduct quality control checks to ensure dimensional accuracy, surface finish, and adherence to electrical specifications. Testing methods such as impedance measurement, thermal cycling, and environmental testing (e.g., humidity, temperature extremes) may be employed to validate substrate performance.
- Assembly Integration: Integrate the fabricated radar substrate with other radar system components such as antennas, RF (Radio Frequency) circuits, feed networks, and signal processing units. Ensure proper alignment, electrical connectivity, and mechanical stability to optimize overall radar system performance.
- Packaging and Protection: Once integrated, protect the radar substrate and assembled components with suitable packaging materials or enclosures. This helps safeguard against environmental factors, mechanical damage, and ensures long-term reliability of the radar system.
By following these steps, engineers can effectively fabricate radar substrates that meet the stringent requirements of modern radar systems, including those used in military, aerospace, weather monitoring, and automotive applications. Each step is critical to achieving optimal performance, reliability, and longevity of radar systems in diverse operational environments.
How do you manufacture a Radar Substrate?
Manufacturing a radar substrate involves a series of precise steps to create a stable, efficient base for radar system components. Here’s a detailed outline of the radar substrate manufacturing process:
- Material Selection: Choose a substrate material based on dielectric constant, thermal stability, mechanical strength, and environmental resilience. Common materials include ceramics (e.g., alumina, aluminum nitride), composites, and specialized polymers (e.g., PTFE).
- Material Preparation: Cut or form the substrate material into desired dimensions using techniques like milling, turning, or laser cutting. Ensure surfaces are smooth and free from imperfections to minimize signal loss.
- Surface Treatment: Polish or apply coatings to improve surface smoothness, enhance electrical properties, or provide protection against environmental factors like moisture and corrosion.
- Pattern Design and Etching: Design specific patterns (e.g., microstrip lines, antenna elements) using CAD software. Transfer designs onto the substrate using photolithography or screen printing. Etch patterns using wet chemical or dry etching methods.
- Metallization:Apply metallization layers to the substrate surface for electrical conductivity and to create interconnections. Techniques include sputtering, evaporation, or electroplating.
- Bonding: Bond semiconductor devices, connectors, or other components to the substrate using soldering, epoxy bonding, or wire bonding. Ensure strong mechanical and electrical connections.
- Quality Control:Perform rigorous testing to verify dimensional accuracy, surface quality, and electrical characteristics. Tests may include impedance measurements, thermal cycling, and environmental tests (e.g., humidity, temperature extremes).
- Assembly Integration: Integrate the substrate with radar components such as antennas, RF circuits, and signal processing units. Ensure proper alignment and connectivity for optimal performance.
- Packaging: Protect the assembled substrate and components with suitable packaging materials or enclosures to withstand environmental stresses and ensure long-term reliability.
- Testing and Validation: Conduct comprehensive testing of the complete radar system to ensure substrate functionality and overall system performance meet specifications across operational conditions.
By following these steps meticulously, manufacturers can produce radar substrates that meet stringent requirements for performance, reliability, and durability in various radar applications. Each stage contributes to creating a robust foundation essential for the functionality of radar systems in diverse operational environments.
How much should a Radar Substrate cost?
The cost of a radar substrate can vary widely depending on several factors:
- Material: Different substrate materials have varying costs. For example, ceramics such as alumina or aluminum nitride are generally more expensive than polymers like PTFE.
- Size and Complexity: Larger substrates or those with complex geometries may require more material and labor, thus increasing the cost.
- Manufacturing Process: The specific techniques and equipment required for fabrication (e.g., precision machining, photolithography, metallization) influence costs.
- Quality and Tolerance Requirements: Higher precision and tighter tolerances in dimensions and surface finish may increase costs due to more stringent manufacturing processes and quality control measures.
- Volume: Economies of scale apply; larger production runs generally reduce per-unit costs due to efficiencies in material usage and manufacturing processes.
- Customization: Custom-designed substrates tailored to specific radar system requirements may incur higher costs compared to standard or off-the-shelf options.
- Additional Features: Integration of additional features such as specialized coatings, enhanced thermal management capabilities, or advanced electrical properties can add to the cost.
As a rough estimate, radar substrates can range from tens to several hundred dollars per unit in simpler applications. In more complex or specialized radar systems (e.g., military, aerospace), costs can escalate significantly depending on the factors mentioned above.
Ultimately, the cost of a radar substrate should be evaluated in the context of its performance requirements, operational environment, and the overall budget for the radar system. Manufacturers and designers typically balance cost considerations with performance, reliability, and longevity to achieve the best value for their specific application.
What is Radar Substrate base material?
The base material for radar substrates varies depending on the specific requirements of the radar system and its intended application. Several materials are commonly used as radar substrate base materials:
- Ceramics: Ceramics such as alumina (Al2O3) and aluminum nitride (AlN) are popular choices due to their high thermal conductivity, excellent mechanical strength, and stable dielectric properties over a wide range of temperatures and frequencies.
- Polymers:Specialized polymers like polytetrafluoroethylene (PTFE), also known as Teflon, are used for radar substrates requiring low dielectric constant, low loss tangent, and good chemical resistance. PTFE substrates are often used in high-frequency radar applications.
- Composites: Composite materials, which combine different materials to achieve specific properties, are used in radar substrates to optimize mechanical strength, thermal stability, and electrical performance.
- Metals: In some cases, metal substrates or metal-coated substrates are used to provide enhanced thermal conductivity or specific electromagnetic properties required for radar operation.
- Glass: Glass substrates may be used in certain radar applications where transparency to radio waves is necessary, or for specialized purposes such as high-precision radar components.
The choice of substrate base material depends on factors such as the operating frequency range of the radar system, thermal management requirements, mechanical strength needed, environmental conditions (e.g., humidity, temperature extremes), and desired electrical properties (dielectric constant, loss tangent). Each material offers different advantages and trade-offs, and selection is typically based on balancing these factors to achieve optimal radar system performance and reliability.
Which company makes Radar Substrate?
Many companies specialize in manufacturing radar substrates, including electronic materials manufacturers and technology providers worldwide. These companies typically possess advanced material development capabilities and precision manufacturing technologies to produce various substrates that meet the high-performance requirements of radar systems.
For example, well-known international companies such as Rogers Corporation, DuPont, CeramTec from the United States, and Murata Manufacturing, Toshiba Materials, Murata Ceramics from Japan, have extensive experience and technological strength in the field of radar substrates. They not only offer a variety of substrate materials but also provide customized design and production services to meet specific requirements of different radar systems.
In our company, we also have the capability to manufacture radar substrates. We have advanced material selection and processing technologies that allow us to produce substrates from ceramics, polymers, and composite materials. Our manufacturing processes adhere strictly to international standards and customer technical specifications to ensure stable and reliable product quality.
Our strengths include:
- Material Expertise: We can select the most suitable substrate materials according to the application requirements, such as ceramics with high thermal conductivity or polymers with low dielectric constant, ensuring excellent performance of radar systems.
- Manufacturing Technology: With advanced processing equipment and a skilled technical team, we achieve high-precision machining and manufacturing, ensuring precise dimensions and surface quality of substrates.
- Customization Capability: We offer customized design and production services to meet specific customer needs, including specific circuit patterns, special surface treatments, and integration of additional functionalities.
- Quality Assurance: We implement a rigorous quality management system from raw material procurement to final product delivery, conducting strict controls and testing at every stage to ensure products meet design requirements and performance specifications.
- Customer Service: We emphasize close cooperation with customers throughout the entire process, from project initiation to production delivery, maintaining communication and collaboration to meet customer needs and expectations.
In summary, as a company with extensive experience and professional capabilities, we are confident in providing high-quality radar substrate products and offering customized design and production according to your specific requirements. Whether in civilian or military radar applications, we aim to be your trusted partner.
What are the 7 qualities of good customer service?
Good customer service is characterized by several key qualities that contribute to a positive experience for customers. Here are seven qualities of good customer service:
- Responsiveness: Good customer service involves promptly addressing customer inquiries, concerns, and requests. This includes acknowledging customer communications promptly and providing timely and helpful responses.
- Empathy: Customer service representatives should demonstrate empathy by understanding and acknowledging the customer’s feelings, concerns, and perspectives. Empathetic responses help build rapport and show that the customer’s experience is valued.
- Clear Communication: Effective communication is crucial in customer service. Representatives should communicate clearly and concisely, ensuring that information is easily understood by the customer. This includes using plain language, avoiding jargon, and providing accurate information.
- Knowledgeability: Customer service agents should have a good understanding of the products or services they support. They should be knowledgeable enough to answer questions accurately, provide relevant information, and offer solutions or recommendations that meet customer needs.
- Professionalism: Professionalism in customer service involves maintaining a courteous and respectful demeanor at all times. This includes being patient, maintaining composure, and treating customers with politeness and professionalism, even in challenging situations.
- Problem-solving Skills: Effective customer service requires the ability to identify and resolve customer issues efficiently. This involves listening actively to understand the problem, proposing appropriate solutions, and following through to ensure the customer’s concern is fully addressed.
- Personalization: Providing personalized service involves recognizing and responding to individual customer preferences, history, and specific needs. Personalization can enhance the customer experience by making interactions more relevant and meaningful.
By embodying these qualities, organizations can deliver exceptional customer service that fosters customer satisfaction, loyalty, and positive word-of-mouth. Good customer service goes beyond transactional interactions—it builds relationships and enhances the overall reputation of the company.
FAQs
What are radar substrates made of?
Radar substrates can be made from various materials such as ceramics (e.g., alumina, aluminum nitride), polymers (e.g., PTFE), composites, and sometimes metals. The choice depends on factors like dielectric constant, thermal stability, and mechanical strength required for radar system performance.
What are the key properties of radar substrates?
Important properties include high thermal conductivity, low dielectric loss, mechanical stability, dimensional accuracy, and the ability to withstand environmental factors like humidity and temperature variations.
How are radar substrates manufactured?
The manufacturing process involves selecting the appropriate material, shaping or forming it to required dimensions, applying surface treatments, etching patterns as needed, metallizing for electrical conductivity, and ensuring quality control through rigorous testing.
What are the applications of radar substrates?
Radar substrates are essential in radar systems used across various applications including military and defense (radar systems for surveillance, target detection), aerospace (weather monitoring, air traffic control), automotive (collision avoidance systems), and telecommunications (satellite communication).
What factors should be considered when choosing a radar substrate?
Factors include the operating frequency of the radar system, thermal management requirements, mechanical strength, environmental durability, electrical properties (dielectric constant, loss tangent), and manufacturability.
Why is radar substrate design important?
Optimal substrate design ensures efficient performance of radar systems by minimizing signal losses, supporting antenna elements effectively, and maintaining stability under varying operational conditions.