Rogers Antenna PCB Manufacturer
We are a professional Rogers Antenna PCB Manufacturer, we mainly produce ultra-small bump pitch substrate, ultra-small trace and spacing packaging substrate and PCBs.
Rogers Antenna PCBs are advanced printed circuit boards specifically engineered for high-frequency antenna applications. Utilizing specialized materials from Rogers Corporation, these PCBs offer exceptional electrical properties optimized for RF and microwave frequencies. With low dielectric loss, excellent signal integrity, and consistent performance across a broad frequency spectrum, Rogers Antenna PCBs ensure high efficiency, reliable signal transmission, and superior gain in demanding environments. Their design allows for precise impedance control, enabling optimal matching and enhanced performance. Ideal for aerospace, telecommunications, automotive radars, satellite systems, and wireless communication devices, Rogers Antenna PCBs deliver unmatched reliability and performance. From compact IoT devices to complex satellite communication systems, these PCBs provide the foundation for robust and efficient antenna solutions, meeting the stringent requirements of modern high-frequency applications.
What is a Rogers Antenna PCB?
A Rogers Antenna PCB refers to a printed circuit board (PCB) designed specifically for antenna applications using high-frequency materials manufactured by Rogers Corporation. Rogers Corporation is known for producing advanced electronic materials, including high-frequency laminates that are particularly suited for RF (radio frequency) and microwave applications. The term “Rogers Antenna PCB” typically emphasizes the use of Rogers’ materials in the construction of the PCB, which are selected for their superior electrical properties, such as low dielectric loss, excellent signal integrity, and consistent performance across a wide range of frequencies.
These characteristics make Rogers materials ideal for antenna applications, especially in demanding fields such as aerospace, telecommunications, automotive radars, and satellite systems. Antennas made with Rogers PCBs can achieve higher efficiency, better gain, and more reliable performance under challenging environmental conditions compared to those made with standard FR-4 materials (a common type of PCB material).
The specific choice of Rogers material (like Rogers RO4003, RO4350, etc.) depends on the particular requirements of the antenna application, including considerations like frequency of operation, thermal management, and mechanical stability. Designing an antenna with a Rogers PCB often involves careful planning and precision to fully leverage the benefits of the material in meeting specific performance criteria.
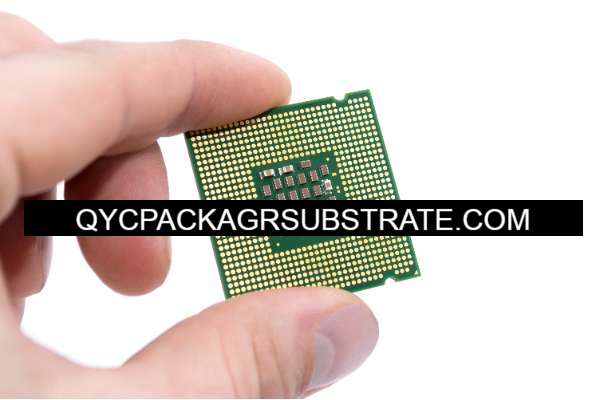
Rogers Antenna PCB Manufacturer
What are the Rogers Antenna PCB Design Guidelines?
Designing antennas using Rogers PCBs requires adherence to specific guidelines to ensure optimal performance. Here are some general guidelines:
- Material Selection: Choose the appropriate Rogers material based on the frequency of operation, dielectric constant, thermal properties, and mechanical stability required for the antenna design. Common materials include RO4003, RO4350, RO3003, etc.
- Substrate Thickness: The substrate thickness affects the antenna’s impedance and radiation characteristics. Follow manufacturer recommendations for the desired substrate thickness based on the antenna design requirements.
- Trace Width and Spacing: Use wider trace widths and larger spacing to reduce losses and ensure consistent impedance matching. These dimensions depend on the chosen Rogers material and the target impedance.
- Ground Plane: Ensure a continuous and uniform ground plane beneath the antenna elements to minimize radiation losses and improve efficiency. The ground plane should extend beyond the antenna structure and provide a low-impedance path for return currents.
- Antenna Element Layout: Place antenna elements and feed lines carefully to minimize coupling, impedance mismatch, and radiation pattern distortion. Avoid placing conductive elements or components that may interfere with the antenna’s operation.
- Via Placement: Strategically place vias to connect different layers of the PCB and provide low-inductance paths for RF signals and ground connections. Vias should be optimized to minimize impedance disruptions and maintain signal integrity.
- Feed Network Design: Design the feed network (e.g., microstrip lines, coplanar waveguides) to efficiently deliver RF power to the antenna elements while minimizing losses and impedance mismatches. Ensure proper impedance matching at the feed point.
- Radiation Pattern Optimization: Use simulation tools and iterative design techniques to optimize the antenna’s radiation pattern, gain, and bandwidth. Adjust antenna dimensions, feed positions, and ground plane geometry to achieve desired performance metrics.
- Environmental Considerations: Take into account environmental factors such as temperature variations, humidity, and mechanical stress when designing the antenna. Choose Rogers materials with suitable thermal and mechanical properties for the intended application.
- Testing and Validation: Perform extensive testing and validation of the antenna design using RF test equipment and simulations to verify performance characteristics such as return loss, VSWR, radiation efficiency, and far-field patterns.
By following these guidelines and leveraging the unique properties of Rogers PCB materials, designers can create high-performance antennas tailored to specific applications with improved efficiency, reliability, and signal integrity.
What is the Rogers Antenna PCB Fabrication Process?
The fabrication process for Rogers antenna PCBs involves several steps to ensure the precise manufacturing of high-quality printed circuit boards optimized for antenna applications. Here’s an overview of the typical fabrication process:
- Material Selection:Choose the appropriate Rogers laminate material based on the specific requirements of the antenna design, including frequency of operation, dielectric constant, thermal properties, and mechanical stability. Common materials include RO4003, RO4350, RO3003, etc.
- Preparation:Clean the surface of the chosen Rogers laminate material to remove any contaminants that could affect the adhesion of the copper layer.
- Copper Cladding: Apply a thin layer of copper foil to both sides of the Rogers laminate material. The copper layer thickness depends on the desired impedance and conductivity of the PCB.
- Laser Drilling: Use a precision laser drilling process to create vias (plated through-holes) in the PCB substrate. Vias provide electrical connections between different layers of the PCB and facilitate signal transmission and grounding.
- Etching: Use chemical etching or plasma etching to selectively remove unwanted copper from the PCB substrate, leaving behind the desired conductive traces and antenna elements. Etching is typically performed using photolithography techniques to define the layout of the traces and components on the PCB.
- Surface Finish: Apply a surface finish to the exposed copper traces to protect them from oxidation and improve solderability. Common surface finishes include immersion gold, HASL (hot air solder leveling), ENIG (electroless nickel immersion gold), and OSP (organic solderability preservative).
- Solder Mask Application: Apply a solder mask layer over the PCB surface to insulate the conductive traces and protect them from environmental damage and solder bridging during assembly. The solder mask is selectively applied to expose the areas where components will be soldered.
- Silkscreen Printing: Use silkscreen printing to apply component labels, reference designators, and other markings to the PCB surface for assembly and identification purposes.
- Routing and Profiling: Use precision routing equipment to separate individual PCBs from the larger panel. The PCBs are then profiled to their final dimensions using a mechanical or laser cutting process.
- Quality Control: Perform thorough visual inspection and electrical testing to ensure the quality and integrity of the fabricated PCBs. Check for defects such as shorts, opens, impedance variations, and dimensional inaccuracies.
- Packaging and Shipping: Package the finished PCBs according to customer specifications and ship them to the designated location for assembly and integration into the final antenna system.
By following these steps with precision and attention to detail, manufacturers can produce Rogers antenna PCBs that meet the stringent requirements of high-frequency RF applications, ensuring reliable performance and signal integrity.
How do you manufacture a Rogers Antenna PCB?
Manufacturing a Rogers antenna PCB involves a series of steps that require precision, expertise, and specialized equipment. Here’s a detailed overview of the manufacturing process:
- Design Preparation: Begin with the design of the antenna PCB using specialized software like Altium Designer, Eagle, or Cadence Allegro. The design should take into account the specific requirements of the antenna, including frequency of operation, impedance matching, radiation pattern, and mechanical constraints.
- Material Selection: Choose the appropriate Rogers laminate material based on the antenna design requirements. Common materials include RO4003, RO4350, RO3003, etc. Ensure that the material selected meets the desired electrical, thermal, and mechanical properties for the application.
- Panelization: Once the design is finalized, create a panel layout by arranging multiple PCBs on a larger panel. Panelization maximizes manufacturing efficiency by allowing multiple PCBs to be fabricated simultaneously.
- Copper Cladding: Apply a thin layer of copper foil to both sides of the Rogers laminate material using a lamination process. The copper layer thickness is determined based on the desired impedance and conductivity of the PCB.
- Laser Drilling: Use a precision laser drilling system to create vias (plated through-holes) in the PCB substrate. Vias provide electrical connections between different layers of the PCB and facilitate signal transmission and grounding.
- Circuit Patterning: Use photolithography techniques to define the layout of the conductive traces and antenna elements on the PCB. This involves applying a photoresist layer to the copper foil, exposing it to UV light through a photomask, and developing the pattern using chemical etching or plasma etching.
- Surface Treatment: Apply a surface treatment to the exposed copper traces to protect them from oxidation and improve solderability. Common surface finishes include immersion gold, HASL (hot air solder leveling), ENIG (electroless nickel immersion gold), and OSP (organic solderability preservative).
- Solder Mask Application: Apply a solder mask layer over the PCB surface to insulate the conductive traces and protect them from environmental damage and solder bridging during assembly. The solder mask is selectively applied to expose the areas where components will be soldered.
- Silkscreen Printing: Use silkscreen printing to apply component labels, reference designators, and other markings to the PCB surface for assembly and identification purposes.
- Routing and Profiling: Use precision routing equipment to separate individual PCBs from the larger panel. The PCBs are then profiled to their final dimensions using a mechanical or laser cutting process.
- Quality Control: Perform thorough visual inspection and electrical testing to ensure the quality and integrity of the fabricated PCBs. Check for defects such as shorts, opens, impedance variations, and dimensional inaccuracies.
- Packaging and Shipping: Package the finished PCBs according to customer specifications and ship them to the designated location for assembly and integration into the final antenna system.
Throughout the manufacturing process, it’s essential to maintain strict quality control standards to ensure that the Rogers antenna PCBs meet the required specifications and performance criteria for their intended application.
How much should a Rogers Antenna PCB cost?
The cost of a Rogers antenna PCB can vary significantly depending on various factors such as:
- Board Size and Complexity: Larger boards with intricate designs or multiple layers will generally cost more to manufacture due to increased material and production costs.
- Material Type: Different types of Rogers laminates have varying costs based on their electrical properties, thermal performance, and manufacturing processes.
- Thickness: Thicker PCBs may require more material and processing steps, leading to higher costs.
- Copper Weight: The thickness of the copper layers (usually measured in ounces per square foot) affects conductivity and can impact cost.
- Surface Finish:The chosen surface finish (e.g., immersion gold, HASL, ENIG) can influence the overall cost of the PCB.
- Quantities:Ordering larger quantities of PCBs typically reduces the per-unit cost due to economies of scale.
- Turnaround Time: Expedited fabrication and delivery options often incur additional charges.
- Additional Services: Extra services such as assembly, testing, and certifications (e.g., IPC Class 3) may add to the overall cost.
As a rough estimate, the cost of a standard Rogers antenna PCB can range from tens to hundreds of dollars per square foot, with additional costs for setup fees, tooling, and shipping. However, for a precise cost estimation, it’s best to consult with a PCB manufacturer or supplier, providing detailed specifications of your design and requirements. They can offer quotes based on your specific needs and volume expectations.
What is Rogers Antenna PCB base material?
The base material used in Rogers antenna PCBs is typically a high-frequency laminate manufactured by Rogers Corporation. Rogers offers a range of specialized materials designed specifically for RF (radio frequency) and microwave applications, including antennas. Some of the common base materials used for Rogers antenna PCBs include:
- RO4003: A high-performance, thermoset composite material with a low dielectric constant (εr) and low loss tangent (Df). RO4003 is suitable for high-frequency applications up to several gigahertz.
- RO4350: A high-frequency laminate with excellent electrical properties, including a low dielectric constant (εr) and tight control of dielectric constant tolerance. RO4350 is widely used in applications requiring stable electrical performance over a wide frequency range.
- RO3003:Similar to RO4003 but with a slightly higher dielectric constant (εr), RO3003 is well-suited for applications requiring controlled impedance and high-frequency performance.
These Rogers materials are known for their consistent electrical properties, thermal stability, and mechanical strength, making them ideal for antenna PCBs where reliable RF performance is critical. The choice of base material depends on factors such as the frequency of operation, signal integrity requirements, and environmental conditions. Designers select the most suitable Rogers material based on the specific needs of the antenna application.
Which company makes Rogers Antenna PCBs?
Manufacturing Rogers Antenna PCBs is typically undertaken by specialized PCB manufacturers, with Rogers Corporation supplying the high-frequency PCB materials. Some well-known PCB manufacturers and assemblers, such as HDI PCB manufacturers, high-frequency PCB manufacturers, and RF PCB manufacturers, may produce Rogers Antenna PCBs. They possess advanced production equipment, extensive experience, and professional teams capable of manufacturing high-quality Rogers Antenna PCBs according to customer design requirements and specifications.
In our company, we have the capability to produce Rogers Antenna PCBs. As a professional PCB manufacturer, we have advanced production equipment and technology to produce various types of PCBs, including Rogers Antenna PCBs. Our production process strictly follows international standards and quality management systems to ensure that each production step meets the highest quality standards.
Our manufacturing capabilities include the following aspects:
- Advanced Equipment: We have advanced PCB production equipment, including high-precision drilling machines, chemical etching equipment, automated soldering lines, and testing equipment, to meet the manufacturing requirements of various complex PCBs.
- Rich Experience: We have an experienced technical team familiar with the design and manufacturing processes of Rogers Antenna PCBs, capable of providing professional technical support and advice.
- Quality Assurance: We strictly implement a quality management system, controlling every aspect from raw material procurement to production manufacturing and final product inspection to ensure stable and reliable product quality.
- Customer Customization: We can customize various types of Rogers Antenna PCBs according to customer requirements, including different materials, sizes, layers, and special process requirements.
- Fast Delivery: We can provide fast delivery cycles to ensure that customers receive the products they need on time.
As a professional PCB manufacturer, we are committed to providing customers with high-quality, high-performance Rogers Antenna PCBs to meet their various application requirements. Whether it is small-batch production or large-scale orders, we can provide customers with the best solutions and services.
What are the 7 qualities of good customer service?
Good customer service is essential for maintaining customer satisfaction and fostering long-term relationships. Here are seven qualities that contribute to effective customer service:
- Responsiveness: Being responsive means promptly addressing customer inquiries, concerns, and requests. Whether it’s answering phone calls, replying to emails, or engaging with customers on social media, responding in a timely manner shows that you value their time and are committed to assisting them.
- Empathy: Empathy involves understanding and acknowledging the customer’s emotions, concerns, and perspectives. It’s about putting yourself in their shoes and showing genuine care and compassion. Empathetic responses can help defuse tense situations and build trust with customers.
- Professionalism: Professionalism entails maintaining a courteous, respectful, and knowledgeable demeanor when interacting with customers. It involves adhering to company policies and standards while delivering service that is efficient, accurate, and reliable.
- Problem-Solving Skills: Effective customer service representatives possess strong problem-solving skills to address customer issues and resolve conflicts. They listen actively, identify root causes, and propose appropriate solutions or alternatives to meet the customer’s needs.
- Communication Skills: Clear and effective communication is crucial in customer service. This includes not only conveying information accurately but also actively listening to customers to understand their needs and concerns. Good communication builds rapport and ensures that customers feel heard and understood.
- Patience: Patience is vital when dealing with challenging or frustrated customers. It involves remaining calm, composed, and understanding, even in difficult situations. Demonstrating patience can help de-escalate conflicts and turn negative experiences into positive ones.
- Follow-Up and Follow-Through: Good customer service doesn’t end with resolving an immediate issue; it includes following up to ensure customer satisfaction and following through on commitments. Whether it’s checking in after a service interaction or ensuring that a problem has been fully resolved, proactive follow-up demonstrates dedication to customer care.
By embodying these qualities, businesses can deliver exceptional customer service experiences that leave a lasting positive impression and foster loyalty among their customers.
FAQs
What are Rogers Antenna PCBs?
Rogers Antenna PCBs are printed circuit boards (PCBs) specifically designed for antenna applications using high-frequency materials manufactured by Rogers Corporation. These PCBs are optimized to meet the demanding requirements of RF (radio frequency) and microwave antennas in various industries.
What makes Rogers Antenna PCBs different from regular PCBs?
Rogers Antenna PCBs use specialized high-frequency laminates from Rogers Corporation, known for their superior electrical properties and performance at high frequencies. These materials offer low dielectric loss, excellent signal integrity, and consistent performance across a wide range of frequencies, making them ideal for antenna applications.
What are the advantages of using Rogers Antenna PCBs?
The advantages of Rogers Antenna PCBs include high performance at high frequencies, low signal loss, excellent impedance control, thermal stability, and mechanical reliability. These properties result in antennas with improved efficiency, better gain, and reliable performance in demanding applications.
What factors should be considered when designing Rogers Antenna PCBs?
When designing Rogers Antenna PCBs, factors such as substrate material selection, trace width and spacing, ground plane design, antenna element layout, feed network design, via placement, and environmental considerations need to be taken into account to optimize performance and reliability.
Can Rogers Antenna PCBs be used in various applications?
Yes, Rogers Antenna PCBs can be used in a wide range of applications, including aerospace, telecommunications, automotive radars, satellite systems, wireless communication devices, and IoT (Internet of Things) devices. They are suitable for any application requiring high-frequency antenna solutions.
How can I ensure the quality of Rogers Antenna PCBs?
Ensuring the quality of Rogers Antenna PCBs involves selecting a reputable PCB manufacturer with experience in high-frequency applications, adhering to design guidelines, conducting thorough testing and validation, and using high-quality materials and manufacturing processes.
Are Rogers Antenna PCBs more expensive than regular PCBs?
Rogers Antenna PCBs may be more expensive than regular PCBs due to the cost of the specialized high-frequency materials and the precision manufacturing processes involved. However, the performance benefits and reliability they offer often justify the investment, especially in critical applications.