Thin Film Ceramic Substrates Manufacturer
Thin Film Ceramic Substrates Manufacturer,Thin Film Ceramic Substrates are specialized materials used in electronics for their excellent thermal conductivity, mechanical strength, and electrical insulation properties. These substrates provide a stable foundation for depositing thin layers of metals and oxides through advanced deposition techniques like sputtering and CVD. They are crucial components in applications requiring high-performance integrated circuits, sensors, and semiconductor devices, where precision and reliability are paramount. Thin film ceramic substrates enable efficient heat dissipation, precise electrical performance, and durability in demanding environments, making them essential in modern electronic manufacturing.
What is a Thin Film Ceramic Substrate?
A thin film ceramic substrate is a type of substrate made from ceramic materials, typically with a thickness ranging from a few micrometers to several millimeters. These substrates are engineered to support the deposition of thin films, which are layers of material ranging from nanometers to micrometers in thickness, on their surface. The key characteristics of thin film ceramic substrates include their high thermal stability, excellent electrical insulating properties, and mechanical strength, making them ideal for various high-performance applications.
Ceramic substrates are often made from materials such as alumina (Al₂O₃), zirconia (ZrO₂), or silicon carbide (SiC), each offering unique properties suited to different applications. Alumina, for instance, is widely used due to its good thermal conductivity, high dielectric strength, and chemical stability. Zirconia substrates are chosen for their exceptional toughness and thermal expansion properties, making them suitable for applications that require durability under thermal stress.
In electronic applications, thin film ceramic substrates are essential in the fabrication of semiconductor devices, sensors, and integrated circuits. They provide a stable base that supports the precise deposition of thin layers of metals, oxides, or other materials, essential for the functionality of the device. Additionally, these substrates are used in the production of multilayer ceramic capacitors (MLCCs), high-frequency filters, and power electronics, where their insulating properties and thermal performance are crucial.
The manufacturing process of thin film ceramic substrates involves advanced techniques such as tape casting, screen printing, and thin film deposition processes like sputtering or chemical vapor deposition (CVD). These methods ensure that the substrates meet stringent quality standards required for high-tech applications.
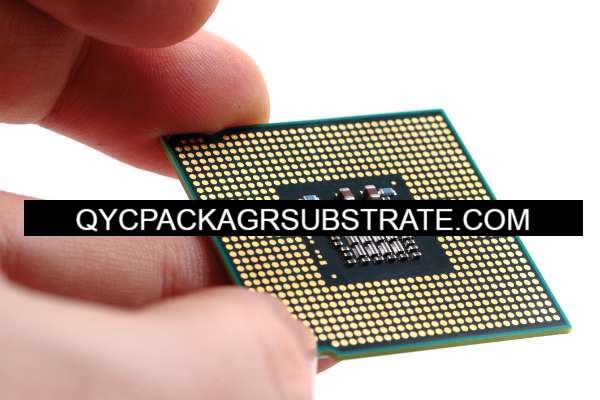
Thin Film Ceramic Substrates Manufacturer
What are Thin Film Ceramic Substrate Design Guidelines?
Designing thin film ceramic substrates involves several key guidelines to ensure optimal performance and reliability in various applications. Here are some important design guidelines:
- Material Selection: Choose the ceramic material based on the specific requirements of the application. Consider factors such as thermal conductivity, dielectric constant, mechanical strength, thermal expansion coefficient, and chemical stability. Common materials include alumina (Al₂O₃), zirconia (ZrO₂), and silicon carbide (SiC), each offering different properties suited to different environments and operating conditions.
- Thickness and Size: Determine the appropriate thickness and size of the substrate based on the mechanical and thermal requirements of the application. Thinner substrates are beneficial for heat dissipation and thermal management, while larger substrates may be necessary for accommodating multiple components or larger-scale devices.
- Surface Finish and Flatness: Ensure the substrate has a smooth and flat surface to facilitate the deposition of thin films and to ensure proper electrical and thermal contact with other components. Surface roughness can affect film quality and adhesion.
- Electrical Design: Design the substrate layout to minimize parasitic capacitances and resistances. This involves optimizing the placement and routing of conductive traces and vias to reduce signal loss and interference.
- Thermal Management: Consider the thermal conductivity of the substrate material and design features such as heat sinks, vias for thermal dissipation, or integration with thermal management structures to efficiently manage heat generated by components on the substrate.
- Mechanical Stability:Ensure the substrate design provides adequate mechanical support and rigidity to withstand mechanical stresses and vibrations encountered during operation and handling.
- Dielectric Properties: Pay attention to the dielectric properties of the ceramic material, especially the dielectric constant and loss tangent, which can affect the performance of high-frequency applications and signal integrity.
- Compatibility with Thin Film Deposition Techniques: Design the substrate to be compatible with thin film deposition techniques such as sputtering, chemical vapor deposition (CVD), or physical vapor deposition (PVD). Consider aspects like substrate temperature stability, surface preparation requirements, and compatibility with deposition materials.
- Reliability and Manufacturing Considerations: Ensure the design takes into account manufacturing constraints and reliability requirements. Factors such as manufacturability, yield, assembly processes, and long-term reliability in the intended operating environment should be considered during the design phase.
- Environmental Considerations: Evaluate the substrate’s performance under environmental conditions such as temperature extremes, humidity, and exposure to chemicals or corrosive substances if applicable to the application.
By adhering to these guidelines, designers can optimize the performance, reliability, and manufacturability of thin film ceramic substrates for various advanced electronic and semiconductor applications. Each guideline plays a crucial role in ensuring that the substrate meets the specific functional and operational requirements of the intended application.
What is the Thin Film Ceramic Substrate Fabrication Process?
The fabrication process of thin film ceramic substrates involves several key steps, each aimed at creating a substrate with precise dimensions, smooth surfaces, and suitable properties for its intended application. Here’s an overview of the typical fabrication process:
- Material Selection: The process begins with selecting the appropriate ceramic material based on the desired properties such as thermal conductivity, dielectric constant, mechanical strength, and chemical stability. Common materials include alumina (Al₂O₃), zirconia (ZrO₂), and silicon carbide (SiC).
- Preparation of Ceramic Powders: The chosen ceramic material is typically in the form of fine powders. These powders are carefully selected and mixed to achieve the desired composition and properties. The mixing process may involve adding binders and solvents to create a homogeneous paste or slurry.
- Substrate Forming: The ceramic paste or slurry is then formed into the desired shape of the substrate. This can be done using various techniques such as tape casting, where the slurry is spread onto a flat surface to form a thin, uniform layer. Alternatively, extrusion or pressing techniques can be used to form the substrate into a specific shape or size.
- Green Machining: After forming, the substrate is typically in a “green” state, meaning it has not yet been fired. Green machining processes such as cutting, drilling, or milling may be performed to achieve the final dimensions and surface features required for the substrate.
- Drying: The green ceramic substrate is then dried to remove excess moisture and solvents. Careful drying is essential to prevent cracking or warping of the substrate.
- Firing (Sintering): The dried substrate undergoes a high-temperature firing process, also known as sintering. During sintering, the ceramic particles are bonded together, resulting in a dense, solid substrate with the desired mechanical, thermal, and electrical properties. The temperature and duration of sintering are carefully controlled to achieve the desired density and microstructure of the ceramic material.
- Surface Finishing: After sintering, the substrate may undergo additional processing steps for surface finishing. This includes polishing or grinding to achieve a smooth surface finish, which is critical for subsequent thin film deposition processes.
- Thin Film Deposition: Once the ceramic substrate is fabricated and finished, thin films of metals, oxides, or other materials may be deposited onto its surface. Thin film deposition techniques such as sputtering, chemical vapor deposition (CVD), or physical vapor deposition (PVD) are used to create thin layers with precise thickness and composition.
- Post-Processing: After thin film deposition, the substrate may undergo further post-processing steps such as annealing, patterning, or etching to define electrical circuits or features on the substrate surface.
- Quality Control and Testing: Throughout the fabrication process, quality control measures are implemented to ensure that the substrates meet specific dimensional, mechanical, electrical, and thermal specifications. Testing may include measurements of surface roughness, dimensional accuracy, electrical insulation properties, and thermal conductivity.
By following these steps, manufacturers can produce thin film ceramic substrates tailored to meet the demanding requirements of various advanced electronic, semiconductor, and sensor applications. Each step in the fabrication process plays a crucial role in achieving substrates with high performance and reliability.
How do you manufacture Thin Film Ceramic Substrates?
Manufacturing thin film ceramic substrates involves a precise and controlled process to achieve substrates with specific mechanical, thermal, and electrical properties suitable for advanced electronic and semiconductor applications. Here’s a detailed overview of the typical manufacturing process:
- Material Selection: The process begins with selecting ceramic materials based on the required properties such as thermal conductivity, dielectric constant, mechanical strength, and chemical stability. Common materials include alumina (Al₂O₃), zirconia (ZrO₂), silicon carbide (SiC), and various other ceramic compositions tailored to specific applications.
- Powder Preparation: Ceramic materials are typically used in powder form. The powders are carefully selected and blended to achieve the desired composition and properties. This mixing process may involve adding binders, dispersants, and solvents to create a homogenous slurry or paste suitable for subsequent forming processes.
- Forming Techniques:
– Tape Casting: A widely used method where the ceramic slurry is spread onto a flat carrier film, forming a thin, uniform layer. The slurry is then dried and peeled off to create a green tape that can be further processed.
– Extrusion: Involves forcing the ceramic paste through a die to produce continuous shapes such as rods or tubes. Extrusion is suitable for forming substrates with complex cross-sections.
– Dry Pressing: In this method, the ceramic powder is compacted into a mold under high pressure to form a green body of the desired shape.
– Injection Molding: Used for forming intricate shapes by injecting ceramic paste into molds under high pressure.
- Green Machining: After forming, the green ceramic substrate may undergo machining processes such as cutting, drilling, or milling to achieve precise dimensions and features. This step is crucial to prepare the substrate for sintering.
- Drying: The formed green ceramic substrate is dried to remove excess moisture and solvents. Proper drying is essential to prevent cracking or distortion during subsequent processing.
- Sintering: The dried green ceramic substrate undergoes sintering, a high-temperature process where the ceramic particles are bonded together to form a dense, solid substrate. Sintering temperatures typically range from 1200°C to 1800°C, depending on the ceramic material and desired properties. The sintering process is critical for achieving the final mechanical, thermal, and electrical properties of the substrate.
- Surface Finishing: After sintering, the ceramic substrate may undergo surface finishing processes such as grinding, polishing, or lapping to achieve a smooth surface finish. Surface finish is crucial for subsequent thin film deposition processes and ensuring proper electrical and thermal performance.
- Thin Film Deposition: Once the substrate is fabricated and finished, thin films of metals, oxides, or other materials may be deposited onto its surface. Thin film deposition techniques such as sputtering, chemical vapor deposition (CVD), or physical vapor deposition (PVD) are used to create layers with precise thickness and composition required for specific electronic or sensor applications.
- Post-Processing: Following thin film deposition, additional post-processing steps may be required. This could include annealing to enhance film properties, patterning or etching to define electrical circuits or features, and applying protective coatings for durability or environmental resistance.
- Quality Control and Testing: Throughout the manufacturing process, stringent quality control measures are implemented to ensure that the thin film ceramic substrates meet specified dimensional tolerances, mechanical strength, electrical insulation properties, thermal conductivity, and overall reliability. Testing may involve various techniques such as surface profilometry, electrical impedance measurements, thermal cycling tests, and visual inspection.
By following these manufacturing steps and maintaining strict quality control, manufacturers can produce thin film ceramic substrates tailored to meet the demanding requirements of modern electronics, semiconductor devices, sensors, and other high-performance applications. Each stage in the process is crucial to achieving substrates with consistent performance and reliability in diverse operating conditions.
How much should Thin Film Ceramic Substrates cost?
The cost of thin film ceramic substrates can vary significantly depending on several factors including:
- Material Type: Different ceramic materials have varying costs. For example, alumina (Al₂O₃) is generally more affordable compared to materials like zirconia (ZrO₂) or silicon carbide (SiC), which are more expensive due to their advanced properties.
- Size and Thickness: Larger and thicker substrates require more material and may involve higher manufacturing costs.
- Complexity of Design: Substrates with intricate shapes, fine features, or specific tolerances may require more precise manufacturing processes, potentially increasing costs.
- Surface Finish Requirements: Achieving a high-quality surface finish for thin film deposition can involve additional processing steps and may impact costs.
- Thin Film Deposition Requirements: The cost of thin film deposition techniques (e.g., sputtering, CVD, PVD) and the materials used for deposition also contribute to the overall cost.
- Quantity: Economies of scale typically apply – larger production runs can lead to lower per-unit costs due to efficiencies in manufacturing and material usage.
- Quality and Performance Specifications: Meeting stringent quality standards and performance requirements may necessitate additional testing and quality control measures, affecting costs.
Given these factors, it is challenging to provide a precise cost without specific details about the substrate’s size, material, design complexity, and intended application. However, as a rough estimate, thin film ceramic substrates can range from a few dollars per unit for simpler designs and materials to several tens or even hundreds of dollars per unit for larger, more complex substrates with advanced materials and stringent specifications.
For accurate pricing, it’s advisable to consult with manufacturers or suppliers specializing in thin film ceramic substrates. They can provide detailed quotations based on specific design requirements, quantities, and desired performance characteristics.
What is Thin Film Ceramic Substrate base material?
The base material of a thin film ceramic substrate refers to the primary ceramic material that forms the substrate itself. This material serves as the foundational layer onto which thin films of metals, oxides, or other materials are deposited for various electronic, semiconductor, or sensor applications. The choice of base material is crucial as it determines the substrate’s mechanical, thermal, electrical, and chemical properties.
Common base materials for thin film ceramic substrates include:
- Alumina (Al₂O₃): Alumina is one of the most widely used ceramic materials for substrates due to its excellent thermal conductivity, high dielectric strength, good mechanical strength, and chemical stability. It is suitable for a wide range of applications including electronics, sensors, and high-temperature environments.
- Zirconia (ZrO₂): Zirconia offers exceptional mechanical properties, including high strength, toughness, and resistance to wear and corrosion. It is often chosen for applications requiring durability under harsh conditions or where thermal shock resistance is important.
- Aluminum Nitride (AlN):Aluminum nitride exhibits high thermal conductivity, making it ideal for substrates requiring efficient heat dissipation. It is commonly used in high-power electronic devices and components where thermal management is critical.
- Silicon Carbide (SiC): Silicon carbide combines high thermal conductivity with excellent electrical properties and chemical inertness. It is suitable for applications in harsh environments, high-power electronics, and semiconductor devices where high temperature and high-frequency operation are required.
- Beryllium Oxide (BeO): Beryllium oxide offers very high thermal conductivity, second only to diamond among ceramics. It is used in specialized applications where superior thermal management is essential, although its use is limited due to toxicity concerns associated with beryllium.
These materials are chosen based on the specific requirements of the application, such as thermal management, electrical insulation, mechanical strength, and environmental stability. Each material has its advantages and limitations, influencing its suitability for different types of thin film ceramic substrates. The selection process involves balancing these factors to ensure optimal performance and reliability in the final application.
Which company manufactures Thin Film Ceramic Substrates?
There are many companies specialized in manufacturing thin film ceramic substrates worldwide, offering a wide range of products for various applications. Some well-known companies include Panasonic, Murata Manufacturing, Kyocera, Corning, and others. These companies utilize advanced ceramic materials and precise manufacturing processes to provide high-performance substrate products for electronics, semiconductor, sensor, and related industries.
As for our company, to manufacture thin film ceramic substrates, we would need advanced capabilities in ceramic processing and thin film deposition technologies. Firstly, we should be able to select and process high-quality ceramic materials such as alumina, aluminum nitride, zirconia, etc., to meet diverse application requirements from customers. Secondly, proficiency in thin film deposition techniques including sputtering, chemical vapor deposition (CVD), physical vapor deposition (PVD), etc., is crucial to uniformly and accurately deposit metals, oxides, or other thin film materials onto the ceramic substrate surfaces.
Our company would also require advanced processing equipment and rigorous process control capabilities to ensure the produced thin film ceramic substrates meet stringent customer requirements, including dimensional accuracy, surface smoothness, and thin film thickness control. Moreover, emphasis on establishing and implementing a robust quality control system would be essential to ensure the stability and reliability of our products through various testing and inspection methods.
Furthermore, our commitment to technological innovation and research and development investment enables continuous improvement of production processes and product performance to meet the evolving demands of the electronics industry. Through close collaboration with customers and providing customized services, we aim to deliver tailored high-quality thin film ceramic substrates that help customers gain competitive advantages in the market.
In summary, as a specialized manufacturer of thin film ceramic substrates, our company possesses extensive industry experience and technical capabilities, dedicated to offering innovative and reliable products and solutions for our customers.
What are the qualities of good customer service?
Good customer service encompasses several key qualities that contribute to a positive experience for customers. Here are some important qualities:
- Responsiveness: Good customer service involves being prompt and timely in addressing customer inquiries, requests, and issues. Responding quickly shows respect for the customer’s time and demonstrates a commitment to their satisfaction.
- Empathy: Empathy means understanding and acknowledging the customer’s feelings, concerns, and perspectives. It involves listening actively, showing compassion, and putting yourself in the customer’s shoes to better address their needs.
- Clarity and Communication: Effective communication is essential in customer service. It includes clear and concise explanations, active listening to understand customer inquiries fully, and providing information in a way that is easy to understand.
- Problem-solving Skills: Good customer service representatives are skilled at identifying and resolving issues or complaints effectively. They are proactive in finding solutions and are empowered to make decisions that benefit the customer.
- Professionalism: Maintaining a professional demeanor and attitude is crucial in customer service. This includes being polite, courteous, and respectful in all interactions with customers, regardless of the situation.
- Knowledgeability: Having a good understanding of the products or services offered allows customer service representatives to provide accurate information and assistance. They should be well-trained and informed about company policies, procedures, and offerings.
- Commitment to Customer Satisfaction: Good customer service involves a genuine commitment to ensuring that customers are satisfied with their experience. This may involve going above and beyond to meet customer expectations and build long-term relationships.
- Adaptability: Customers have varying needs and preferences, so adaptability is important. Being flexible and willing to adjust your approach based on individual customer situations helps in delivering personalized service.
- Positive Attitude: Maintaining a positive and optimistic attitude can influence the customer’s perception of their interaction. It helps create a welcoming and supportive environment, even during challenging situations.
- Follow-up and Feedback: Following up with customers after resolving issues or completing transactions shows care and concern. Seeking feedback also allows businesses to continuously improve their customer service based on customer input.
Overall, good customer service involves a combination of interpersonal skills, knowledge, responsiveness, and a genuine desire to help customers. It focuses on creating a positive customer experience that builds trust, loyalty, and satisfaction.
FAQs
What are thin film ceramic substrates?
Thin film ceramic substrates are specialized materials used in electronics and semiconductor industries as a base for depositing thin layers (films) of metals, oxides, or other materials. They provide a stable platform for electronic components and circuits.
What are the advantages of thin film ceramic substrates?
Thin film ceramic substrates offer advantages such as high thermal conductivity, excellent electrical insulation properties, mechanical strength, chemical stability, and compatibility with high-temperature environments. They are crucial for applications requiring precise control over thermal management and electrical performance.
What materials are commonly used for thin film ceramic substrates?
Common materials include alumina (Al₂O₃), aluminum nitride (AlN), zirconia (ZrO₂), and silicon carbide (SiC). These materials are chosen based on their specific properties suited to different application requirements.
What are thin film deposition techniques used on ceramic substrates?
Thin film deposition techniques include sputtering, chemical vapor deposition (CVD), physical vapor deposition (PVD), and others. These techniques are used to deposit thin layers of metals (e.g., gold, silver), oxides (e.g., silicon dioxide), or other materials onto the ceramic substrate surface.
What are the typical applications of thin film ceramic substrates?
Thin film ceramic substrates are used in a wide range of applications such as integrated circuits (ICs), sensors, microwave devices, high-frequency filters, LED packaging, and power electronics. They are essential where high performance, reliability, and durability are required.
How are thin film ceramic substrates manufactured?
The manufacturing process involves steps such as material selection, preparation of ceramic powders, substrate forming (e.g., tape casting, extrusion), drying, sintering (high-temperature firing), surface finishing, thin film deposition, and quality control testing. It requires specialized equipment and expertise in ceramic processing and thin film deposition technologies.
What are the key considerations when choosing thin film ceramic substrates?
Factors to consider include thermal conductivity, dielectric properties, mechanical strength, compatibility with thin film deposition techniques, dimensional stability, surface smoothness, and environmental durability. The choice depends on the specific requirements of the application.