Thin Film Substrates Manufacturer
Thin Film Substrates Manufacturerm,Thin film substrates are foundational materials onto which thin layers of other materials are deposited, crucial in electronics, optics, and coatings. These substrates, like silicon, glass, or metal, undergo precise deposition techniques such as PVD or CVD to modify surface properties like electrical conductivity or optical transparency. Their versatility enables applications in semiconductors, solar cells, sensors, and more, shaping modern technology’s advancement. Tailored to specific needs, thin film substrates optimize device performance, offering solutions to diverse industrial challenges through their engineered structures and materials.
What is a Thin Film Substrate?
A thin film substrate is a base material on which a very thin layer of another material is deposited. This concept is fundamental in fields such as electronics, optics, and materials science. The substrate usually consists of a solid support material that could range from glass, silicon, plastic, or even metal, chosen based on its compatibility with the thin film and the intended application.
The deposition of the thin layer onto the substrate can be achieved through various techniques like physical vapor deposition (PVD), chemical vapor deposition (CVD), or sputtering, among others. The thickness of the film can vary from a few nanometers to several micrometers. This thin film can significantly alter the surface properties of the substrate, including its electrical, optical, and mechanical characteristics.
Thin film substrates are crucial in the manufacture of many modern technologies. For example, in electronics, they are used for creating circuits on semiconductor devices. In optics, thin film coatings on glass substrates enhance reflection, refraction, and filtration properties essential for lenses and mirrors. The choice of substrate and film materials, along with the deposition technique, directly impacts the functionality and efficiency of the final product. Thus, the science of thin film substrates is a key area of research and development, driving advancements in numerous high-tech industries.
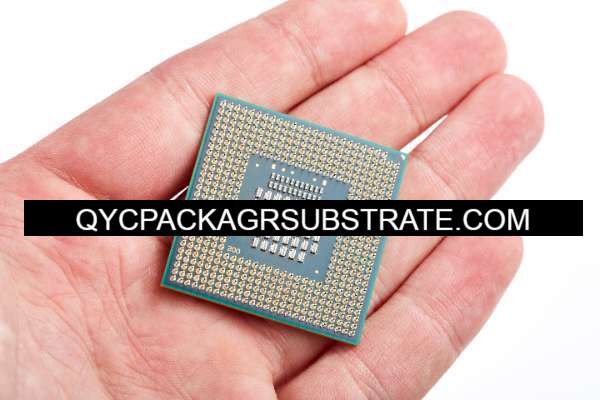
Thin Film Substrates Manufacturer
What are the Thin Film Substrate Design Guidelines?
Designing thin film substrates involves considering various factors to achieve desired performance and functionality. Here are some general guidelines:
- Substrate Selection: Choose a substrate material compatible with the thin film material and the intended application. Consider factors such as thermal expansion coefficient, surface roughness, transparency, and mechanical strength.
- Thin Film Material Selection: Select a thin film material suitable for the desired properties, such as conductivity, optical transparency, or magnetic properties. Consider factors like deposition method compatibility, stability, and cost.
- Thickness Control: Precisely control the thickness of the thin film layer to achieve the desired properties. This can be done through deposition techniques like PVD, CVD, or atomic layer deposition (ALD), and by monitoring deposition parameters such as deposition rate and time.
- Uniformity: Ensure uniformity of the thin film across the substrate surface to avoid variations in performance. Control parameters such as deposition temperature, pressure, and substrate rotation or scanning during deposition.
- Adhesion:Promote strong adhesion between the thin film and the substrate to prevent delamination or peeling. Pre-treat the substrate surface if necessary to improve adhesion, and optimize deposition conditions to promote interfacial bonding.
- Surface Finish: Optimize the surface finish of the substrate to minimize defects and improve thin film quality. Clean the substrate thoroughly to remove contaminants that can affect film adhesion and quality.
- Stress Management: Control internal stress within the thin film to prevent deformation or cracking. Adjust deposition parameters or introduce stress-relieving layers if needed.
- Characterization:Perform thorough characterization of the thin film substrate to validate its properties and performance. Use techniques such as scanning electron microscopy (SEM), X-ray diffraction (XRD), and atomic force microscopy (AFM) to analyze film thickness, morphology, crystal structure, and other relevant properties.
By following these guidelines, designers can create thin film substrates optimized for specific applications, whether in electronics, optics, sensors, or other fields. Each application may have additional considerations, so it’s essential to tailor the design process accordingly.
What is the Thin Film Substrate Fabrication Process?
The fabrication process of thin film substrates involves several steps to deposit a thin layer of material onto a solid support substrate. Here’s a general overview of the process:
- Substrate Preparation: The first step is to prepare the substrate. This involves cleaning the substrate thoroughly to remove any contaminants that could affect the adhesion or quality of the thin film. Depending on the substrate material and the deposition technique to be used, additional surface treatments such as etching or polishing may be required to achieve the desired surface properties.
- Deposition Technique Selection: Choose an appropriate deposition technique based on factors such as the thin film material, desired film properties, and substrate compatibility. Common deposition techniques include Physical Vapor Deposition (PVD), Chemical Vapor Deposition (CVD), sputtering, and spin coating, among others.
- Deposition Process Setup: Set up the deposition equipment according to the chosen technique. This involves configuring parameters such as deposition temperature, pressure, gas flow rates (for CVD), substrate orientation, and deposition rate. The goal is to create conditions conducive to the desired thin film growth while ensuring uniformity and control over film thickness.
- Thin Film Deposition: Perform the thin film deposition process. Depending on the technique used, this may involve:
– PVD: Evaporate or sputter the thin film material from a solid source onto the substrate surface in a vacuum chamber.
– CVD: React gaseous precursor molecules to deposit the thin film material onto the substrate surface via chemical reactions.
– Sputtering: Bombard a target material with high-energy ions to dislodge atoms or molecules, which then deposit onto the substrate surface.
– Spin Coating: Apply a liquid precursor solution onto the substrate surface and spin the substrate at high speed to achieve a uniform thin film layer through centrifugal force.
- Post-Deposition Treatment (if necessary): Depending on the specific requirements of the thin film substrate, post-deposition treatments such as annealing, doping, or surface modification may be performed to enhance film properties or functionality.
- Characterization: After deposition and any post-treatment steps, characterize the thin film substrate to assess its properties and quality. Use techniques such as scanning electron microscopy (SEM), atomic force microscopy (AFM), X-ray diffraction (XRD), and spectroscopy to analyze film thickness, morphology, crystal structure, and other relevant properties.
- Quality Control:Conduct quality control checks to ensure that the thin film substrate meets the desired specifications and performance criteria. This may involve testing for uniformity, adhesion strength, electrical conductivity, optical transparency, or other relevant parameters.
By following these steps, manufacturers can fabricate thin film substrates tailored to specific applications in fields such as electronics, optics, sensors, and coatings, among others. The precise details of the fabrication process may vary depending on factors such as the thin film material, substrate type, and deposition technique used.
How do you manufacture Thin Film Substrates?
Manufacturing thin film substrates involves a series of steps to deposit a thin layer of material onto a solid support substrate. Here’s a simplified overview of the manufacturing process:
- Substrate Preparation: The process begins with preparing the substrate. This typically involves cleaning the substrate surface thoroughly to remove any contaminants that could affect the adhesion or quality of the thin film. Substrates can be made of various materials like glass, silicon, plastic, or metal, chosen based on compatibility with the thin film material and the intended application.
- Deposition Technique Selection: Choose a suitable deposition technique based on factors such as the thin film material, desired film properties, and substrate compatibility. Common deposition techniques include Physical Vapor Deposition (PVD), Chemical Vapor Deposition (CVD), sputtering, and spin coating, among others.
- Deposition Process Setup: Set up the deposition equipment according to the chosen technique. This involves configuring parameters such as deposition temperature, pressure, gas flow rates (for CVD), substrate orientation, and deposition rate. The goal is to create conditions conducive to the desired thin film growth while ensuring uniformity and control over film thickness.
- Thin Film Deposition: Perform the thin film deposition process using the selected technique. The specifics of this step depend on the chosen method:
– PVD: Evaporate or sputter the thin film material from a solid source onto the substrate surface in a vacuum chamber.
– CVD: React gaseous precursor molecules to deposit the thin film material onto the substrate surface via chemical reactions.
– Sputtering: Bombard a target material with high-energy ions to dislodge atoms or molecules, which then deposit onto the substrate surface.
– Spin Coating: Apply a liquid precursor solution onto the substrate surface and spin the substrate at high speed to achieve a uniform thin film layer through centrifugal force.
- Post-Deposition Treatment (if necessary): Depending on the specific requirements of the thin film substrate, post-deposition treatments such as annealing, doping, or surface modification may be performed to enhance film properties or functionality.
- Characterization and Quality Control: After deposition and any post-treatment steps, characterize the thin film substrate to assess its properties and quality. Use techniques such as scanning electron microscopy (SEM), atomic force microscopy (AFM), X-ray diffraction (XRD), and spectroscopy to analyze film thickness, morphology, crystal structure, and other relevant properties. Conduct quality control checks to ensure that the thin film substrate meets the desired specifications and performance criteria.
By following these steps, manufacturers can produce thin film substrates tailored to specific applications in various industries such as electronics, optics, sensors, and coatings. The precise details of the manufacturing process may vary depending on factors such as the thin film material, substrate type, and deposition technique used.
How much should a Thin Film Substrate cost?
The cost of a thin film substrate can vary widely depending on several factors, including:
- Material: The cost of the substrate material itself can significantly impact the overall cost. Substrates made of materials like glass, silicon, or plastic may have different price points depending on factors such as purity, size, and processing requirements.
- Thin Film Material: The cost of the thin film material being deposited onto the substrate also plays a significant role. Some materials may be more expensive due to their rarity, complexity of synthesis, or purity requirements.
- Deposition Technique: The choice of deposition technique can influence costs. Techniques like Physical Vapor Deposition (PVD) and Chemical Vapor Deposition (CVD) may require specialized equipment and consumables, which can contribute to higher production costs compared to simpler methods like spin coating.
- Equipment and Labor Costs: The cost of equipment for deposition, characterization, and quality control, as well as the labor required to operate and maintain the equipment, are also factors to consider.
- Customization and Volume: Customization of thin film substrates for specific applications may incur additional costs. Similarly, economies of scale apply, with larger production volumes generally leading to lower per-unit costs due to efficiencies in materials and processes.
- Quality Requirements: Thin film substrates for high-performance or critical applications may require stringent quality control measures, which can increase production costs.
- Additional Treatments: Post-deposition treatments such as annealing, doping, or surface modification may add to the overall cost.
Given the variability in these factors, it’s challenging to provide a specific cost for thin film substrates without knowing the exact specifications and requirements of the application. However, thin film substrates can range from relatively inexpensive for simple, small-scale productions to significantly higher costs for specialized, high-performance substrates produced in larger volumes or requiring complex deposition techniques.
What is Thin Film Substrate base material?
The base material of a thin film substrate serves as the foundation onto which a thin layer of another material is deposited. The choice of base material depends on various factors such as the application requirements, compatibility with the thin film material, mechanical properties, thermal stability, and cost considerations. Common base materials for thin film substrates include:
- Silicon (Si): Silicon substrates are widely used in semiconductor and microelectronics industries due to their excellent mechanical properties, thermal conductivity, and compatibility with integrated circuit fabrication processes.
- Glass: Glass substrates are often chosen for their optical transparency and smooth surface finish. They are commonly used in applications such as display technologies, photovoltaics, and optical coatings.
- Quartz: Quartz substrates offer high thermal stability, low thermal expansion coefficient, and excellent optical transparency in the UV range. They find applications in optics, spectroscopy, and semiconductor manufacturing.
- Plastic: Plastic substrates, such as polymethyl methacrylate (PMMA) or polyethylene terephthalate (PET), are lightweight and flexible, making them suitable for applications where weight and flexibility are critical, such as flexible electronics and displays.
- Metal: Metal substrates like aluminum or stainless steel are chosen for their mechanical strength, electrical conductivity, and compatibility with certain deposition techniques. They are used in applications such as thin film sensors, electronic circuits, and decorative coatings.
- Ceramics: Ceramic substrates offer high mechanical strength, thermal stability, and chemical resistance. They are used in harsh environment applications, such as aerospace and automotive sensors, as well as in electronics packaging.
- Semiconductor Wafers: Single-crystal semiconductor wafers, such as silicon wafers, gallium arsenide (GaAs), or sapphire, are used as substrates in the fabrication of semiconductor devices, photonic devices, and optoelectronic components.
The selection of the base material is crucial as it directly influences the properties and performance of the thin film substrate. Compatibility between the base material and the thin film material is essential to ensure strong adhesion, uniformity, and desired functional properties of the thin film. Additionally, factors such as surface roughness, thermal expansion coefficient, and optical properties of the base material should be considered during the substrate design process.
Which company makes Thin Film Substrates?
Some well-known companies that manufacture thin film substrates include Corning, Schott, and Heraeus. These companies have extensive experience and expertise in thin film technology, and their thin film substrates are widely used in electronics, optics, medical, and other industries. They are committed to continuously improving product quality, developing new materials and processes, and collaborating with customers to meet evolving market demands.
Our company also manufactures thin film substrates. We have advanced production equipment and a skilled technical team capable of designing, manufacturing, and testing thin film substrates. Our production processes adhere strictly to quality standards to ensure product stability and reliability. Our strengths include:
- Customization Capability:We can customize thin film substrates according to specific customer requirements, including selecting appropriate substrate materials, optimizing thin film thickness and structure, and providing various surface treatments and coatings options.
- Technological Innovation: We continuously invest in research and technological innovation to explore new materials and processes to meet changing market demands. Our technical team has extensive experience and expertise in the field of thin film technology.
- Quality Assurance: We strictly control the production process and use advanced testing equipment and methods for quality inspection to ensure that products meet customer requirements and standards.
- Quick Response: We can respond quickly to customer needs, providing flexible solutions and timely delivery of products. We prioritize communication and collaboration with customers to ensure that their needs and expectations are met.
In summary, our company has the capability to manufacture thin film substrates and provide customized solutions according to customer requirements. We are committed to providing high-performance and reliable products through continuous technological innovation and quality service.
What are the qualities of good customer service?
Good customer service is characterized by several key qualities that contribute to positive interactions and relationships between businesses and their customers. Some of these qualities include:
- Responsiveness: Good customer service involves promptly addressing customer inquiries, concerns, and requests. Responding in a timely manner demonstrates attentiveness and shows customers that their needs are valued.
- Empathy: Empathy is essential in understanding and relating to customers’ feelings, experiences, and perspectives. Showing empathy helps build rapport and trust, as customers feel understood and supported.
- Professionalism:Professionalism involves maintaining a courteous and respectful demeanor in all interactions with customers. It includes communicating clearly, listening actively, and resolving issues efficiently while upholding company standards and policies.
- Knowledgeability: Good customer service representatives possess in-depth knowledge about the products or services offered by the company. They can provide accurate information, answer questions, and offer helpful recommendations to assist customers in making informed decisions.
- Adaptability: Customer service professionals should be adaptable and flexible in their approach to handling different situations and customer needs. They should be able to tailor their responses and solutions to meet the unique requirements of each customer interaction.
- Problem-solving skills: Effective problem-solving is crucial in addressing customer concerns and resolving issues satisfactorily. Customer service representatives should be resourceful, proactive, and creative in finding solutions that meet customers’ needs and exceed their expectations.
- Consistency: Consistency in service delivery ensures that customers receive the same level of quality and attention across all interactions with the company. Consistent service builds trust and loyalty, as customers know what to expect from the business.
- Follow-up: Following up with customers after resolving an issue or completing a transaction demonstrates care and concern for their satisfaction. It provides an opportunity to gather feedback, address any remaining concerns, and strengthen the relationship with the customer.
- Personalization: Tailoring the customer service experience to each individual customer’s preferences and needs can enhance satisfaction and loyalty. Personalization can involve addressing customers by name, remembering their previous interactions, and offering relevant recommendations or assistance.
- Positive attitude: Maintaining a positive and enthusiastic attitude can help create a pleasant and welcoming customer service experience. A positive attitude is contagious and can leave a lasting impression on customers, encouraging them to return in the future.
Overall, good customer service involves going above and beyond to meet customer needs, create positive experiences, and build long-lasting relationships based on trust and satisfaction.
FAQs
What is a thin film substrate?
A thin film substrate is a base material onto which a thin layer of another material is deposited. These substrates are used in various industries such as electronics, optics, and coatings to enhance the performance of devices and components.
What are thin film substrates used for?
Thin film substrates are used in a wide range of applications, including semiconductor devices, photovoltaic cells, optical coatings, sensors, and medical devices. They can modify surface properties such as electrical conductivity, optical transparency, and mechanical strength.
What materials are used for thin film substrates?
Common materials used for thin film substrates include silicon, glass, quartz, plastic, metal, and semiconductor wafers like silicon and sapphire. The choice of substrate material depends on factors such as compatibility with the thin film material and the desired application.
How are thin film substrates manufactured?
The manufacturing process of thin film substrates involves depositing a thin layer of material onto a solid support substrate. This can be achieved through various deposition techniques such as Physical Vapor Deposition (PVD), Chemical Vapor Deposition (CVD), sputtering, or spin coating, followed by post-deposition treatments if necessary.
What are the advantages of using thin film substrates?
Thin film substrates offer several advantages, including improved surface properties, enhanced performance of devices or components, reduced weight and size, and the ability to tailor material properties to specific applications. They are also compatible with high-throughput manufacturing processes.
How do I choose the right thin film substrate for my application?
Choosing the right thin film substrate involves considering factors such as the intended application, compatibility with the thin film material, mechanical and thermal properties, optical transparency, and cost. Consulting with experts or suppliers in the field can help identify the most suitable substrate for your specific needs.
What are the key considerations for thin film substrate design?
Key considerations for thin film substrate design include substrate material selection, thickness control, uniformity, adhesion between layers, stress management, surface finish, and characterization to ensure desired properties and performance.
Where can I purchase thin film substrates?
Thin film substrates can be purchased from various suppliers, including manufacturers, distributors, and specialized vendors in the field of thin film technology. It’s essential to choose a reputable supplier that offers high-quality products and technical support to meet your specific requirements.