Ultra Thin Multilayer HDI PCBs Manufacturer
Ultra Thin Multilayer HDI PCBs Manufacturer,Ultra Thin Multilayer HDI PCBs (High-Density Interconnect Printed Circuit Boards) are advanced, high-performance boards designed to meet the demands of modern electronic devices. These PCBs feature multiple layers with extremely fine traces and microvias, enabling high component density and excellent electrical performance. Their ultra-thin profile makes them ideal for applications where space is at a premium, such as smartphones, tablets, and wearable technology. HDI technology improves signal integrity and reduces electromagnetic interference, supporting faster signal transmission and improved device performance. As a result, Ultra Thin Multilayer HDI PCBs are crucial in the development of cutting-edge, compact electronic products.
What is Ultra Thin Multilayer HDI PCBs?
Ultra Thin Multilayer High-Density Interconnect (HDI) Printed Circuit Boards (PCBs) represent an advanced subset of PCB technology characterized by their exceptionally thin profiles and high circuit density. These PCBs are designed to support complex electronics with minimal space, making them ideal for applications where size and weight are critical constraints, such as in smartphones, tablets, wearables, medical devices, and aerospace equipment.
The “Ultra Thin” aspect refers to the reduced thickness of these PCBs, which can be as slim as 50 microns. This is achieved by utilizing advanced materials and manufacturing techniques, including laser drilling for microvias, finer trace and space widths, and advanced lamination processes. The thinness allows for more compact and lightweight designs, which is essential for modern electronic devices that demand high performance in a smaller form factor.
“Multilayer” indicates that these PCBs consist of multiple layers of conductive copper and insulating material, which are stacked and laminated together. This multilayer structure increases the board’s complexity and capability, allowing for more circuitry and components to be integrated within the same footprint. Each layer can be designed to perform different functions, enabling more sophisticated and efficient electronic designs.
“High-Density Interconnect” (HDI) refers to the advanced design and manufacturing techniques used to achieve higher wiring densities per unit area compared to traditional PCBs. HDI technology employs microvias, blind and buried vias, and fine line circuitry, enabling more interconnections in a smaller area. This results in enhanced electrical performance, reduced signal loss, and improved overall reliability.
Combining these attributes, Ultra Thin Multilayer HDI PCBs are pivotal in the evolution of modern electronics, supporting the trend towards miniaturization and high performance. They enable designers to create smaller, lighter, and more powerful devices, pushing the boundaries of what is technologically possible in consumer electronics, medical devices, and beyond.
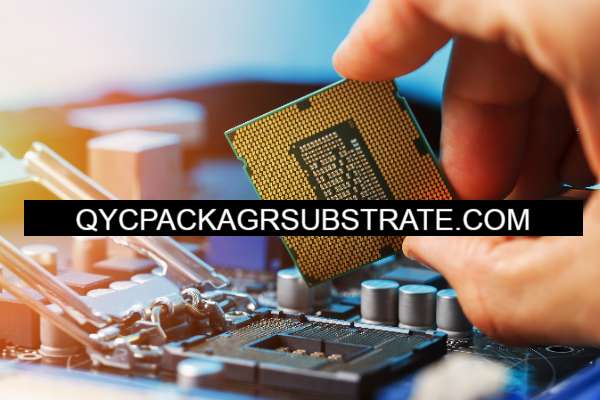
Ultra Thin Multilayer HDI PCBs Manufacturer
What are the Ultra Thin Multilayer HDI PCBs Design Guidelines?
Ultra Thin Multilayer High-Density Interconnect (HDI) Printed Circuit Boards (PCBs) require meticulous design considerations to maximize their performance and reliability. Here are the key design guidelines for Ultra Thin Multilayer HDI PCBs:
- Material Selection: Choose high-quality, thin dielectric materials and copper foils to ensure the overall thinness of the PCB. Materials should have low dielectric constants and low loss tangents to support high-frequency signal transmission.
- Layer Stackup: Plan the layer stackup carefully, considering the number of signal, power, and ground layers. Ensure proper layer sequencing to minimize crosstalk and electromagnetic interference (EMI). Use symmetrical stackups to prevent warping during manufacturing.
- Microvias: Utilize microvias, which are small-diameter vias that connect layers in HDI PCBs. These can be blind or buried vias, reducing the need for through-holes that take up more space. Ensure accurate placement and size of microvias to maintain structural integrity.
- Trace Width and Spacing: Design with finer trace widths and spacing to increase wiring density. Use advanced PCB design software to achieve precision. Ensure traces are capable of handling the required current without excessive heating.
- Pad Size and Placement: Use smaller pad sizes to accommodate the high-density component placement. Ensure proper pad placement to avoid overlapping and ensure reliable solder joints.
- Signal Integrity: Maintain signal integrity by minimizing signal paths and using impedance-controlled traces. Implement differential pairs for high-speed signals and ensure proper termination to reduce signal reflection.
- Thermal Management: Incorporate thermal vias and heat sinks to manage heat dissipation. Use materials with high thermal conductivity to prevent overheating, especially in high-power applications.
- Component Placement: Optimize component placement for minimal signal path lengths and reduced parasitic effects. Place decoupling capacitors close to power pins and ensure even distribution of components to avoid imbalance.
- Design for Manufacturability (DFM): Ensure the design is manufacturable by considering the capabilities of the PCB manufacturer. Adhere to their design rules regarding minimum trace width, spacing, via size, and aspect ratios.
- Testing and Inspection: Include test points and design for testability (DFT) to facilitate electrical testing and inspection. Use automated optical inspection (AOI) and X-ray inspection to ensure quality and reliability.
- Flexibility and Rigidity Balance: Balance the flexibility and rigidity of the PCB, especially if the design includes flexible sections. Use appropriate materials and layer configurations to maintain mechanical strength without compromising flexibility.
- Environmental Considerations: Ensure the PCB design can withstand environmental factors such as temperature variations, humidity, and mechanical stress. Use conformal coatings or encapsulation if necessary for additional protection.
Following these design guidelines will help achieve optimal performance, reliability, and manufacturability for Ultra Thin Multilayer HDI PCBs, supporting the advanced requirements of modern electronic devices.
What is the Ultra Thin Multilayer HDI PCBs Fabrication Process?
The fabrication process for Ultra Thin Multilayer High-Density Interconnect (HDI) Printed Circuit Boards (PCBs) involves several intricate steps to achieve the desired thin profile and high circuit density. Here is an overview of the key stages in the fabrication process:
- Material Preparation: Select and prepare the base materials, which typically include thin dielectric substrates and copper foils. These materials are chosen for their electrical performance, thermal properties, and ability to maintain thin profiles.
- Lamination:Begin by laminating the thin dielectric layers with copper foils to create the initial layers of the PCB. This process involves stacking the layers and applying heat and pressure to bond them together. The lamination process must be controlled carefully to avoid warping and ensure uniform thickness.
- Inner Layer Patterning: Apply a photoresist layer to the inner copper layers. Use photolithography to expose the photoresist to light through a mask, which defines the circuit pattern. Develop the photoresist to reveal the copper areas that will form the circuit traces. Etch away the unwanted copper to create the circuit patterns on the inner layers.
- Drilling: Drill microvias and vias into the laminated stack to create pathways for inter-layer connections. In HDI PCBs, microvias are often used, which are smaller in diameter than traditional vias. These vias can be blind or buried, connecting specific layers without penetrating through the entire board.
- Plating: Plate the vias and the etched copper traces with a thin layer of metal, typically copper, to ensure electrical connectivity between layers. This process, known as electroplating, involves depositing metal onto the walls of the vias and the surfaces of the etched copper patterns.
- Outer Layer Patterning: Apply a photoresist layer to the outer copper layers of the PCB. Similar to the inner layer patterning, use photolithography to define the circuit patterns, develop the photoresist, and etch away the unwanted copper.
- Layer Stacking and Lamination: Stack the processed inner layers with additional dielectric layers and copper foils, then laminate them together using heat and pressure. This process bonds all the layers into a single multilayer PCB structure.
- Surface Finishing: Apply surface finish treatments to the exposed copper pads and traces to protect them from oxidation and to enhance solderability. Common finishes include electroless nickel immersion gold (ENIG), immersion silver, or HASL (Hot Air Solder Leveling).
- Drilling and Plating of Outer Vias: If the design includes through-hole vias or additional vias connecting outer layers, drill these vias and plate them as needed. Ensure that the drilling process does not damage the thin PCB structure.
- Inspection and Testing: Perform detailed inspections and tests, including Automated Optical Inspection (AOI), X-ray inspection, and electrical testing, to ensure the PCB meets design specifications and quality standards. This step is crucial for identifying defects or issues that could affect performance.
- Cutting and Routing: Cut and route the PCBs to their final shape and size. This process involves separating the individual PCBs from the panel and cutting out any specific shapes or slots required by the design.
- Final Assembly: Prepare the PCBs for assembly by applying solder mask and silkscreen layers. The solder mask protects the copper traces from accidental soldering and corrosion, while the silkscreen layer provides labeling and markings.
By following these steps meticulously, manufacturers can produce Ultra Thin Multilayer HDI PCBs that meet the demanding requirements of modern electronic devices, ensuring high performance, reliability, and compact form factors.
How Do You Manufacture Ultra Thin Multilayer HDI PCBs?
Manufacturing Ultra Thin Multilayer High-Density Interconnect (HDI) Printed Circuit Boards (PCBs) involves a series of precise and advanced processes to ensure the high quality and functionality of the final product. Here’s an overview of the manufacturing process:
- Material Preparation: Start with high-quality, thin dielectric materials and copper foils. The dielectric layers must be thin yet durable, and copper foils should be as thin as 9 microns or less. These materials are prepped to ensure they meet the required specifications for thickness and electrical performance.
- Layer Lamination: Stack the dielectric layers and copper foils according to the planned layer stackup. Each layer is carefully aligned and bonded using heat and pressure in a lamination process. This creates a multilayer board with precise alignment between layers.
- Hole Drilling: Use laser drilling to create microvias, which are essential for high-density interconnects. These microvias are small-diameter holes that connect different layers within the PCB. The precision of laser drilling ensures accurate placement and minimal thermal damage to surrounding areas.
- Via Formation: After drilling, the microvias are plated with copper to form conductive paths. This plating process can include both through-hole and blind/buried vias. Ensure that the plating thickness is sufficient to handle the required electrical current and maintain reliability.
- Copper Etching: Apply a photoresist layer to the surface of the PCB, then use photolithography to define the circuit pattern. Expose the photoresist to UV light through a mask to create the desired pattern. Develop the exposed photoresist to reveal the copper areas to be etched away. Etch the copper to remove excess material, leaving behind the circuit traces.
- Chemical Treatment: Clean and treat the PCB surface with chemicals to remove any residues and prepare it for solder mask application. Apply a solder mask to protect the copper traces and prevent solder bridging during assembly.
- Solder Mask and Silkscreen:Apply a solder mask to the PCB to protect the copper traces and define solderable areas. Add a silkscreen layer to print component designators and other markings on the surface.
- Final Lamination and Curing: Perform a final lamination step to bond all layers together, including the solder mask and silkscreen layers. Cure the board in an oven to ensure that all materials are properly set and bonded.
- Inspection and Testing: Conduct thorough inspection using automated optical inspection (AOI) and X-ray to detect any defects, such as misalignments, defects in vias, and etching errors. Perform electrical testing to verify that all connections are correctly made and the board functions as intended.
- Panelization and Cutting: If the PCBs are manufactured as part of a larger panel, cut them into individual boards. Ensure precise cutting to avoid damaging the thin and delicate PCBs.
- Final Assembly and Packaging: Prepare the finished PCBs for assembly, which may include mounting components and soldering. Package the PCBs to protect them during transport and storage, taking care to handle them gently due to their thin and delicate nature.
By carefully managing each of these steps, manufacturers can produce high-quality Ultra Thin Multilayer HDI PCBs that meet the demanding specifications of modern electronic applications.
How Much Should Ultra Thin Multilayer HDI PCBs Cost?
The cost of Ultra Thin Multilayer High-Density Interconnect (HDI) PCBs can vary significantly based on several factors. Here’s a general overview of what influences the cost:
- Complexity and Design: The more complex the design, including the number of layers, density of interconnections, and use of microvias, the higher the cost. Ultra Thin HDI PCBs often involve sophisticated manufacturing techniques, which can increase expenses.
- Material Costs: High-quality dielectric materials, thin copper foils, and other specialized materials used in Ultra Thin HDI PCBs can be expensive. The choice of materials and their thickness can impact the overall cost.
- Layer Count: The number of layers in the PCB affects the cost. More layers mean increased manufacturing complexity and higher costs.
- Quantity: Production volume can significantly influence costs. Higher quantities generally lead to lower per-unit costs due to economies of scale. However, initial setup costs for small runs can be relatively high.
- Manufacturing Processes: Advanced processes such as laser drilling, precise etching, and high-resolution photolithography can drive up costs. The need for specialized equipment and expertise also adds to the expense.
- Testing and Quality Control: Comprehensive testing and quality control measures, including automated optical inspection (AOI) and X-ray inspection, contribute to the overall cost. High standards for quality assurance can increase the price.
- Customization and Prototyping: Custom features or rapid prototyping can add to the cost. Customizations may include unique designs, additional features, or specific requirements that deviate from standard production.
- Lead Time: Faster turnaround times typically come with a higher price tag. If a quick production schedule is required, it can result in increased costs.
- Geographical Location: Costs can vary depending on the manufacturing location. Different regions have varying labor, material, and overhead costs that can affect pricing.
To provide a rough estimate, the cost of Ultra Thin Multilayer HDI PCBs generally ranges from $100 to $300 per square meter. For small production runs or prototypes, the cost can be higher, potentially exceeding $500 per square meter due to setup and tooling costs. For large volume production, the per-unit cost can decrease significantly.
For accurate pricing, it is best to contact PCB manufacturers with specific design requirements and production volumes. They can provide detailed quotes based on the exact specifications and production needs.
What is Ultra Thin Multilayer HDI PCBs Base Material?
The base material for Ultra Thin Multilayer High-Density Interconnect (HDI) Printed Circuit Boards (PCBs) is crucial for ensuring the performance, reliability, and thin profile of the final product. Here’s an overview of the key base materials used:
- Dielectric Materials: The dielectric layer in Ultra Thin Multilayer HDI PCBs is typically composed of high-quality, thin materials that provide electrical insulation between the copper layers. Common dielectric materials include:
– FR-4: A widely used, standard fiberglass epoxy resin material. While it’s not as thin as some specialized materials, it’s versatile and cost-effective.
– Polyimide: Known for its high thermal stability and flexibility, polyimide is often used in flexible and ultra-thin PCBs. It supports high-frequency applications and provides excellent thermal and mechanical properties.
– PTFE (Polytetrafluoroethylene): Used for high-frequency applications due to its low dielectric constant and low loss tangent. PTFE is often used in conjunction with other materials for specialized applications.
- Copper Foil: Thin copper foils are used for the conductive layers of the PCB. For Ultra Thin HDI PCBs, copper foils can be as thin as 9 microns or less. The quality and thickness of the copper foil are critical to achieving high performance and reliability.
- Prepreg: Prepreg is a pre-impregnated composite material, consisting of fibers (such as fiberglass) and resin. It is used to bond the layers of the PCB together. For ultra-thin designs, the prepreg must be carefully chosen to ensure it does not add excessive thickness.
- Core Material: The core material is the central layer of the PCB that may consist of a dielectric material like FR-4 or polyimide with copper clad on both sides. In multilayer HDI PCBs, the core material provides structural integrity and electrical insulation between layers.
- Bonding Materials: Adhesives used in the lamination process must be compatible with the thin materials and capable of forming strong bonds without adding significant thickness. These adhesives are often thermosetting resins that cure under heat and pressure.
- Solder Mask: Although not a core base material, the solder mask applied over the copper traces provides protection and insulation. It is typically a polymer-based coating that must be thin and uniform to maintain the PCB’s slim profile.
- Coverlay: For flexible or semi-flexible designs, a coverlay material (such as polyimide) may be used to protect the PCB and provide mechanical stability. It’s applied to cover exposed copper areas and enhance durability.
In summary, the base materials for Ultra Thin Multilayer HDI PCBs include a combination of advanced dielectric materials, thin copper foils, prepreg, core materials, and bonding agents. Each material is selected based on its performance characteristics and compatibility with the overall design requirements. These materials are chosen to support high-density interconnects while maintaining the required thin profile and high performance of the PCB.
Which Company Makes Ultra Thin Multilayer HDI PCBs?
Several companies around the world specialize in manufacturing Ultra Thin Multilayer High-Density Interconnect (HDI) Printed Circuit Boards (PCBs). Here are some well-known companies with advanced technology and expertise in this field:
- AT&S (Austria Technologie & Systemtechnik AG): As a leading PCB manufacturer in Europe, AT&S offers various high-end PCB solutions, including ultra-thin multilayer HDI PCBs. The company is known for its advanced technology and stringent quality control.
- IPC (Interconnect Products Corporation): IPC is a global leader in PCB manufacturing, focusing on high-density interconnect and ultra-thin PCB production. Their products are widely used in consumer electronics, communications, and medical devices.
- Zhen Ding Technology Holding Limited: This Taiwanese company is one of the largest PCB manufacturers globally, offering multilayer HDI PCB solutions, including ultra-thin designs. They are committed to innovation and high-quality products.
- Unimicron Technology Corporation: Another Taiwanese company, Unimicron excels in ultra-thin HDI PCB technology. Their products are widely used in high-performance electronic devices.
- Nippon Mektron: As a major Japanese PCB manufacturer, Nippon Mektron offers multilayer and high-density interconnect PCB solutions, including ultra-thin HDI PCBs. The company has a strong reputation in the electronics industry.
- Samsung Electro-Mechanics: As a global leader in electronic components, Samsung Electro-Mechanics provides various HDI PCB solutions, focusing on high-end electronic product needs, including ultra-thin multilayer designs.
Our company is also capable of manufacturing Ultra Thin Multilayer HDI PCBs. We have advanced manufacturing equipment and technology to meet the high demands of ultra-thin designs. Our production capabilities include but are not limited to:
- High-Precision Manufacturing: We use the latest laser drilling technology and microvia techniques to ensure the precision of small vias and traces, meeting the design requirements of ultra-thin HDI PCBs.
- Multilayer Lamination Technology: We handle complex multilayer laminations, ensuring precise alignment and bonding of each layer to guarantee overall performance and reliability.
- High-Quality Materials: We use high-quality thin dielectric materials and copper foils to ensure excellent electrical performance and mechanical strength while maintaining ultra-thin design standards.
- Strict Quality Control: We conduct rigorous inspections during the production process, including automated optical inspection (AOI) and X-ray inspection, to ensure that each PCB meets quality and reliability standards.
- Custom Services: We offer tailored services, capable of designing and producing PCBs according to specific customer needs, catering to various application scenarios.
We are committed to providing high-quality ultra-thin multilayer HDI PCB solutions, supporting innovation and development in various high-end electronic devices.
What are the 7 Qualities of Good Customer Service?
Good customer service is crucial for building strong relationships with customers and ensuring their satisfaction. Here are seven key qualities that define excellent customer service:
- Empathy: Understanding and sharing the feelings of customers is essential. Empathetic customer service representatives can connect with customers on a personal level, making them feel valued and heard. This involves actively listening to customer concerns and responding with genuine care and understanding.
- Responsiveness: Timely responses to customer inquiries, issues, or complaints are critical. Quick and efficient handling of customer needs demonstrates respect for their time and urgency. Effective customer service teams prioritize responsiveness to resolve issues promptly and keep customers informed.
- Knowledgeability: Providing accurate and comprehensive information is crucial for resolving customer queries and issues. Customer service representatives should have a deep understanding of the company’s products, services, and policies to offer reliable support and guidance.
- Patience: Dealing with customers who may be frustrated, confused, or upset requires patience. Good customer service involves calmly and professionally addressing customer concerns, allowing them to express their issues without feeling rushed or dismissed.
- Communication Skills: Clear, concise, and effective communication is vital. Representatives should be able to convey information in a way that is easy for customers to understand. Good communication also involves using positive language, avoiding jargon, and ensuring that customers feel comfortable and respected.
- Reliability: Consistency in service is key to building trust. Customers should be able to rely on the company to meet its promises and deliver on its commitments. Reliable customer service involves following through on promises, providing accurate information, and ensuring that issues are resolved as agreed.
- Problem-Solving Skills: Effective customer service involves not just addressing complaints but also finding solutions. Representatives should be skilled at identifying the root cause of issues and developing practical solutions. A proactive approach to problem-solving helps in turning negative experiences into positive outcomes.
These qualities collectively contribute to a positive customer experience, fostering loyalty and encouraging repeat business.
FAQs about Ultra Thin Multilayer HDI PCBs
What is an Ultra Thin Multilayer HDI PCB?
An Ultra Thin Multilayer HDI PCB is a type of printed circuit board that is both very thin and has multiple layers with high-density interconnections. These PCBs are designed for applications requiring compact and lightweight electronic components with high performance.
What are the advantages of Ultra Thin Multilayer HDI PCBs?
The main advantages include reduced size and weight, enhanced signal integrity, improved thermal management, and the ability to support complex circuitry in a compact space. They are ideal for high-performance electronics such as smartphones, tablets, and wearable devices.
What materials are used in Ultra Thin Multilayer HDI PCBs?
Common materials include thin dielectric materials (like polyimide), high-quality copper foils, prepreg, and coverlays. These materials are selected to achieve the desired thinness while maintaining electrical and mechanical performance.
What manufacturing processes are involved?
Manufacturing involves material preparation, layer lamination, microvia drilling, copper etching, chemical treatment, solder mask application, final lamination, and quality inspection. Each step is critical to ensure the precision and reliability of the final PCB.
What are the typical applications for Ultra Thin Multilayer HDI PCBs?
They are used in high-end electronics such as smartphones, tablets, medical devices, and aerospace components, where space and weight are at a premium, and high performance is required.
What are the challenges in designing Ultra Thin Multilayer HDI PCBs?
Challenges include maintaining signal integrity, managing heat dissipation, ensuring precise layer alignment, and handling delicate materials without damage. Design must also account for manufacturability and cost constraints.
How does cost compare to standard PCBs?
Ultra Thin Multilayer HDI PCBs are generally more expensive than standard PCBs due to their advanced materials, manufacturing complexity, and precision requirements. The cost varies based on factors like design complexity, production volume, and material choices.