Ultrathin LED PCB Manufacturer
Ultrathin LED PCB Manufacturer. We offer the Ultrathin 1layer or 2 layer LED PCB thickness from 3mil, 4mil, 5 to 7 mil. for the 4 layer Ultrathin PCBs. we can do the 7mil to 8mil, or maybe 9mil.
Ultrathin LED PCBs are cutting-edge printed circuit boards designed with remarkable thinness, typically ranging from 0.4mm to 1.0mm or even thinner. Engineered specifically for LED lighting applications, these PCBs offer a blend of compactness, flexibility, and efficient heat dissipation. Their slender profile makes them ideal for space-constrained devices like smartphones, tablets, and wearables, where every millimeter matters. Utilizing materials such as aluminum or copper, Ultrathin LED PCBs excel at dispersing heat generated by LEDs, ensuring prolonged lifespan and consistent performance. Their versatility extends to diverse industries, including automotive lighting, signage, display backlighting, and architectural lighting. In manufacturing, specialized processes ensure the thinness and flexibility of the PCB while maintaining optimal thermal management. With their innovative design and superior functionality, Ultrathin LED PCBs illuminate the path towards sleeker, more energy-efficient lighting solutions across various sectors.
What is an Ultrathin LED PCB?
An Ultrathin LED PCB (Printed Circuit Board) refers to a particularly slim circuit board designed specifically for LED (light-emitting diode) applications. The main feature of these PCBs is their minimal thickness, which is typically much less than the standard PCB thickness. Here are some key aspects of ultrathin LED PCBs:
- Thickness: Ultrathin LED PCBs can be as thin as 0.4mm to 1.0mm, compared to standard PCBs which usually have a thickness of around 1.6mm or more. This reduced thickness makes them ideal for use in applications where space is limited or where a low profile is required.
- Material: These PCBs are often made using materials that are good thermal conductors, such as aluminum or copper, to help dissipate heat efficiently. Efficient heat dissipation is critical in LED applications to ensure long life and stable performance of the LEDs.
- Design and Flexibility: The ultrathin design allows these PCBs to be flexible, which is particularly useful in applications requiring the PCB to conform to a particular shape, such as in wearable technology, automotive lighting, or curved displays.
- Applications: Ultrathin LED PCBs are used in a variety of applications, including mobile devices, compact lighting solutions, automotive lighting, backlighting for displays, and other electronic products where space-saving and heat management are priorities.
- Manufacturing: The manufacturing process for ultrathin LED PCBs must be carefully controlled to avoid issues like warping or bending due to their thinness. Special attention is also given to the layout and design to maximize the thermal performance and reliability of the LEDs mounted on them.
In summary, an Ultrathin LED PCB is a specialized, slim form factor circuit board tailored for advanced LED applications, featuring excellent heat dissipation, flexible design possibilities, and suitability for space-constrained uses.
What are the Ultrathin LED PCB Design Guidelines?
Designing ultrathin LED PCBs requires careful consideration of various factors to ensure optimal performance and reliability. Here are some key design guidelines:
- Thermal Management: Efficient heat dissipation is critical for LED performance and longevity. Design the PCB with sufficient thermal vias, thermal pads, or metal-core layers to dissipate heat generated by the LEDs. Ensure that the thermal paths are optimized to transfer heat away from the LEDs to the PCB substrate and, if necessary, to external heat sinks.
- Material Selection: Choose PCB materials with high thermal conductivity, such as aluminum or copper. These materials help in spreading heat away from the LEDs. Consider using metal-core PCBs (MCPCBs) for enhanced thermal performance.
- Component Placement: Place LEDs and other heat-generating components strategically on the PCB to minimize thermal hotspots. Distribute components evenly to ensure uniform heat dissipation across the PCB surface. Keep sensitive components away from areas prone to high temperatures.
- Trace Width and Copper Thickness: Use appropriate trace widths and copper thickness to handle the current requirements of the LEDs without causing excessive voltage drops or overheating. Thicker copper layers and wider traces can reduce resistance and improve thermal conductivity.
- PCB Thickness: While the goal is to keep the PCB as thin as possible, ensure that it provides adequate mechanical stability and heat dissipation. Balance the thinness requirement with structural integrity to prevent bending or warping during operation.
- Flexibility: If the application requires flexibility, consider using flexible PCB materials or designing the PCB with bendable sections. Ensure that the flexibility does not compromise electrical performance or thermal management.
- LED Driver Placement: Place LED drivers or power management components close to the LEDs to minimize trace lengths and reduce voltage drop. This helps maintain consistent power delivery and improves efficiency.
- Signal Integrity: Pay attention to signal integrity to ensure reliable communication between components. Minimize signal trace lengths, use proper ground planes, and implement signal integrity techniques like controlled impedance matching as needed.
- Environmental Considerations: Consider the operating environment of the PCB, such as temperature variations, humidity, and exposure to moisture or chemicals. Select materials and coatings that offer protection against environmental factors to enhance the longevity of the PCB.
- Testing and Validation: Conduct thorough testing and validation of the ultrathin LED PCB design to ensure that it meets performance specifications, thermal requirements, and reliability standards under expected operating conditions.
By following these design guidelines, engineers can develop ultrathin LED PCBs that deliver optimal performance, thermal management, and reliability for various applications.
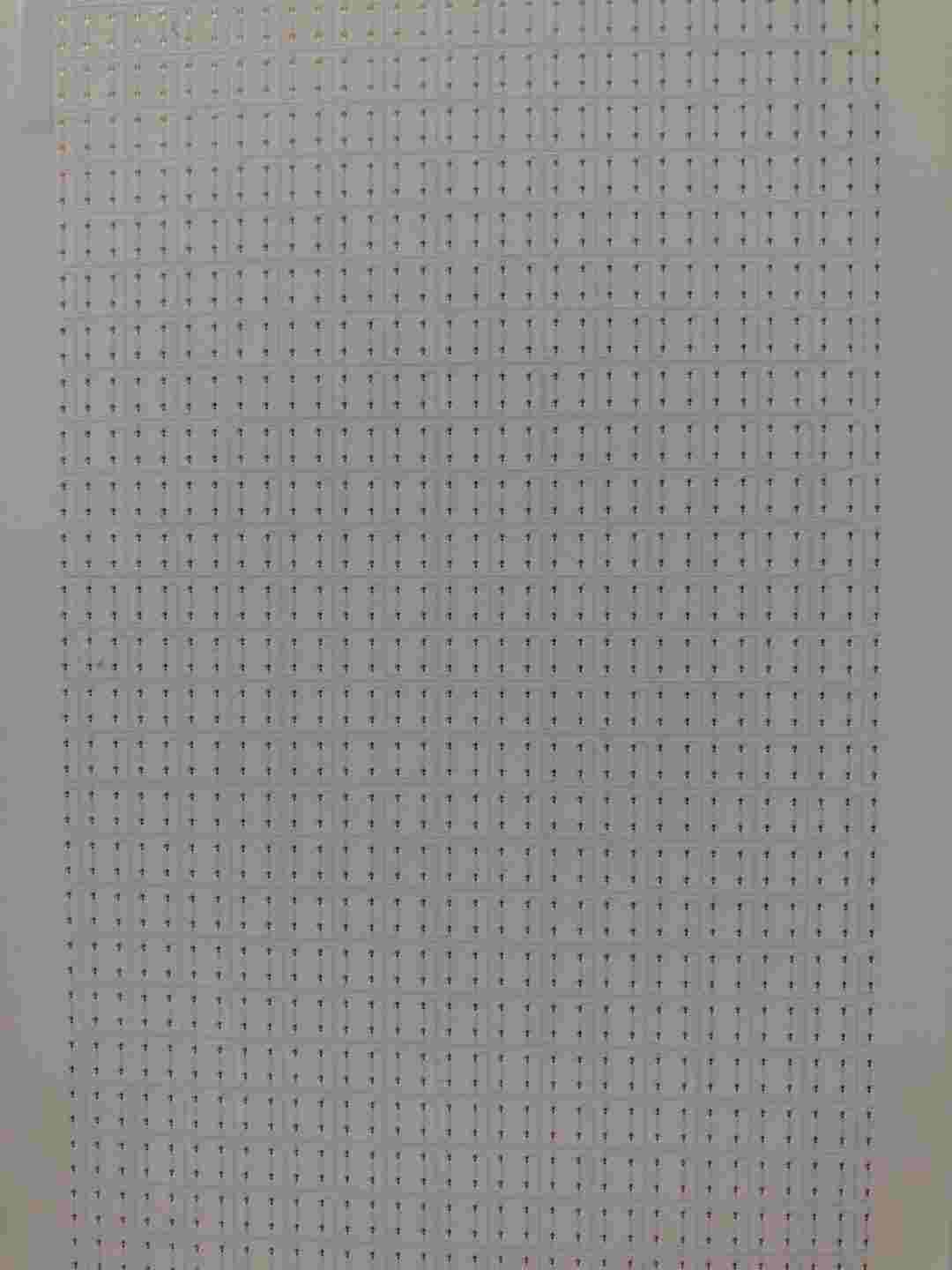
Ultrathin LED PCB
What is the Ultrathin LED PCB Fabrication Process?
The fabrication process for ultrathin LED PCBs follows several steps, similar to the fabrication of standard PCBs, but with additional considerations for the thinness and specific requirements of LED applications. Here’s a general overview of the fabrication process:
- Design and Layout: The process starts with designing the PCB layout using computer-aided design (CAD) software. Engineers determine the placement of components, routing of traces, and optimization of thermal management features based on the application requirements.
- Material Selection: Select the appropriate PCB substrate material based on factors such as thermal conductivity, flexibility, and mechanical strength. Common materials for ultrathin LED PCBs include aluminum, copper, or composite materials with metal cores for enhanced thermal performance.
- Preparation of Substrate:Prepare the chosen substrate material by cleaning and smoothing its surface to ensure proper adhesion of copper foil or other layers during lamination.
- Copper Cladding: Apply a thin layer of copper foil to the substrate material using a lamination process. The copper foil serves as the conductive layer for routing electrical signals and providing thermal conductivity.
- Etching: Use chemical etching or subtractive manufacturing processes to remove unwanted copper from the foil, leaving behind the desired conductive traces and pads according to the PCB layout design.
- Drilling: Drill holes or vias in the PCB for component mounting and electrical connections. Precision drilling is crucial to ensure accurate alignment and dimensioning of the holes.
- Surface Treatment: Apply surface finishes or coatings to protect the copper traces from oxidation and improve solderability. Common surface finishes include HASL (Hot Air Solder Leveling), ENIG (Electroless Nickel Immersion Gold), or OSP (Organic Solderability Preservatives).
- Solder Mask Application: Apply a solder mask layer over the PCB surface, leaving openings for component pads and vias. The solder mask protects the underlying copper traces from environmental factors and prevents solder bridges during assembly.
- Silkscreen Printing: Optionally, add silkscreen printing for labeling component locations, reference designators, and other necessary markings on the PCB surface.
- Component Assembly: Mount LED components, resistors, capacitors, and other electronic components onto the PCB using surface mount technology (SMT) or through-hole assembly techniques, depending on the design requirements.
- Quality Control and Testing:Perform visual inspection, electrical testing, and functional testing to verify the quality, reliability, and performance of the ultrathin LED PCBs. Detect and rectify any defects or discrepancies before finalizing the fabrication process.
- Packaging and Shipping: Package the finished ultrathin LED PCBs according to customer specifications and requirements, ensuring proper protection during transportation and storage.
Throughout the fabrication process, strict quality control measures and adherence to industry standards are essential to ensure the production of high-quality ultrathin LED PCBs that meet performance, reliability, and safety requirements for various applications.
How do you manufacture an Ultrathin LED PCB?
Manufacturing ultrathin LED PCBs involves a specialized process tailored to the unique requirements of these thin and flexible circuit boards. Here’s a step-by-step overview of the manufacturing process:
- Material Selection: Choose a suitable substrate material with high thermal conductivity and flexibility, such as aluminum or copper-clad laminates. The material should be thin yet sturdy enough to support the components and withstand thermal stresses.
- Preparation of Substrate: Clean and prepare the substrate material by removing any contaminants and ensuring a smooth surface. This step is crucial to ensure proper adhesion of subsequent layers and components.
- Copper Foil Lamination: Apply a thin layer of copper foil to the substrate material using a lamination process. This copper foil serves as the conductive layer for routing electrical signals and providing thermal conductivity.
- Etching: Use a chemical etching process to selectively remove unwanted copper from the foil, leaving behind the desired conductive traces and pads according to the PCB layout design. Precision etching is essential to maintain the integrity of the traces and achieve the desired circuit pattern.
- Drilling: Drill holes or vias in the PCB for component mounting and electrical connections. Specialized drilling equipment capable of handling thin and flexible materials is used to ensure accurate hole placement and dimensioning.
- Surface Treatment: Apply surface finishes or coatings to protect the copper traces from oxidation and improve solderability. Common surface finishes include HASL (Hot Air Solder Leveling), ENIG (Electroless Nickel Immersion Gold), or OSP (Organic Solderability Preservatives).
- Solder Mask Application: Apply a solder mask layer over the PCB surface, leaving openings for component pads and vias. The solder mask protects the underlying copper traces from environmental factors and prevents solder bridges during assembly.
- Silkscreen Printing: Optionally, add silkscreen printing for labeling component locations, reference designators, and other necessary markings on the PCB surface.
- Component Assembly: Mount LED components, resistors, capacitors, and other electronic components onto the PCB using surface mount technology (SMT) or through-hole assembly techniques, depending on the design requirements. Special attention should be given to component placement and soldering techniques to avoid damaging the thin and flexible PCB.
- Testing and Inspection: Conduct visual inspection, electrical testing, and functional testing to verify the quality, reliability, and performance of the ultrathin LED PCBs. Detect and rectify any defects or discrepancies before finalizing the manufacturing process.
- Packaging and Shipping: Package the finished ultrathin LED PCBs according to customer specifications and requirements, ensuring proper protection during transportation and storage.
Throughout the manufacturing process, strict quality control measures and adherence to industry standards are essential to ensure the production of high-quality ultrathin LED PCBs that meet performance, reliability, and safety requirements for various applications. Additionally, specialized equipment and techniques may be required to handle the thin and flexible nature of these PCBs effectively.
How much should an Ultrathin LED PCB cost?
The cost of an ultrathin LED PCB can vary significantly depending on several factors, including the complexity of the design, the size of the PCB, the quantity ordered, the materials used, and the manufacturer’s pricing structure. However, I can provide a rough estimate based on typical factors:
- Complexity of Design: PCBs with intricate designs, high component density, and advanced features such as multiple layers, fine pitch traces, or impedance control may cost more to manufacture due to increased fabrication and assembly complexity.
- Size of PCB: Larger PCBs generally require more material and production time, which can contribute to higher costs compared to smaller PCBs.
- Quantity Ordered: Economies of scale typically apply in PCB manufacturing, meaning that larger order quantities can lead to lower per-unit costs. Ordering in bulk often results in volume discounts from manufacturers.
- Materials Used: The choice of materials, such as substrate type, copper thickness, and surface finish, can impact the overall cost of the PCB. High-quality materials with specialized features may incur higher costs.
- Manufacturing Process: Specialized processes or additional services such as fast turnaround times, expedited shipping, or testing and inspection services may add to the total cost of manufacturing.
- Manufacturer Pricing:Different PCB manufacturers have varying pricing structures and cost models based on their capabilities, overhead costs, geographical location, and other factors. It’s essential to obtain quotes from multiple manufacturers to compare prices and services.
As a rough estimate, the cost of an ultrathin LED PCB could range from a few dollars to tens of dollars or more per unit, depending on the factors mentioned above. For a more accurate cost assessment, it’s advisable to consult with PCB manufacturers and provide detailed specifications for your specific project requirements.
What is Ultrathin LED PCB base material?
The base material used for ultrathin LED PCBs typically needs to meet specific requirements for thermal conductivity, flexibility, and mechanical strength. Two common types of base materials used for ultrathin LED PCBs are:
- Aluminum-Based PCBs: Aluminum-based PCBs, also known as metal-core PCBs (MCPCBs), feature a thin layer of aluminum as the base material. Aluminum offers excellent thermal conductivity, which helps dissipate heat generated by the LEDs efficiently. MCPCBs are often used in high-power LED applications where thermal management is critical. The aluminum base also provides some degree of flexibility, making it suitable for certain ultrathin LED PCB designs.
- Copper-Based PCBs: Copper-based PCBs utilize a thin layer of copper as the base material. Copper is another excellent thermal conductor and is commonly used in ultrathin LED PCBs to facilitate heat dissipation. Copper-based PCBs can provide good flexibility depending on the thickness and construction of the copper layer. Additionally, copper-clad laminates with flexible substrates can be used to achieve both thermal performance and flexibility in ultrathin LED PCB designs.
Both aluminum-based and copper-based PCBs offer advantages for ultrathin LED applications, and the choice between them depends on factors such as thermal requirements, mechanical flexibility, and cost considerations. Ultimately, the base material selected should provide the necessary thermal management capabilities while meeting the specific needs of the LED lighting application.
Which company makes Ultrathin LED PCBs?
There are many companies that produce Ultrathin LED PCBs (Printed Circuit Boards), including some well-known ones such as International Electronic Company, Osram, Philips, Foxconn, etc. These companies have rich experience and advanced manufacturing technologies in the LED lighting field, enabling them to provide high-quality Ultrathin LED PCB products.
As for our company, as a dedicated electronic manufacturing company, we also have the capability to produce Ultrathin LED PCBs. We have advanced manufacturing equipment and a skilled technical team to meet various requirements for Ultrathin LED PCBs.
Firstly, we have state-of-the-art PCB manufacturing equipment that can produce high-precision, high-quality Ultrathin PCBs. We utilize advanced processes and quality control procedures to ensure that the thickness of the PCB meets customer requirements while ensuring stability and reliability.
Secondly, our technical team has extensive experience and expertise in PCB design and manufacturing, giving us a competitive advantage. We can provide customized Ultrathin LED PCB solutions tailored to the customer’s needs, including optimization of PCB design, material selection, and manufacturing processes.
Furthermore, we prioritize communication and collaboration with our customers, striving to understand their needs and provide solutions that meet their requirements. We offer flexible production capabilities and fast turnaround times to meet the timely demands of our customers for Ultrathin LED PCBs.
In summary, as a company with advanced manufacturing technology and rich experience in electronic manufacturing, we have the capability to produce high-quality Ultrathin LED PCBs and provide customized solutions to meet customer needs in the LED lighting field.
What are the 7 qualities of good customer service?
Good customer service is essential for building strong relationships with customers and fostering loyalty. Seven qualities that characterize good customer service include:
- Responsiveness:Being responsive means promptly addressing customer inquiries, concerns, and requests. Responding in a timely manner demonstrates attentiveness and shows customers that their needs are valued.
- Empathy: Empathy involves understanding and empathizing with customers’ perspectives and emotions. It entails actively listening to their concerns, acknowledging their feelings, and demonstrating compassion and understanding.
- Clarity: Providing clear and concise communication is crucial for effective customer service. Clear communication helps avoid misunderstandings and ensures that customers receive accurate information and guidance.
- Professionalism: Professionalism encompasses maintaining a courteous and respectful demeanor at all times, regardless of the situation. It involves being polite, patient, and maintaining a positive attitude, even when faced with challenging circumstances.
- Knowledgeability: Good customer service representatives possess in-depth knowledge about the products or services they are supporting. They can answer questions, provide accurate information, and offer helpful recommendations to assist customers effectively.
- Problem-Solving Skills: Effective problem-solving skills are essential for resolving customer issues and complaints satisfactorily. Customer service representatives should be resourceful, proactive, and capable of finding creative solutions to address customer concerns.
- Consistency: Consistency in customer service ensures that customers receive the same high level of service across all interactions and touchpoints with the company. Consistency builds trust and reliability, reinforcing positive perceptions of the brand.
By embodying these qualities, businesses can deliver exceptional customer service experiences that leave a lasting impression on customers and contribute to long-term success and customer loyalty.
FAQs
What are Ultrathin LED PCBs?
Ultrathin LED PCBs are specialized printed circuit boards that are designed to be exceptionally thin, typically ranging from 0.4mm to 1.0mm or even thinner. They are specifically engineered for LED lighting applications where space constraints and heat dissipation are critical considerations.
What are the advantages of Ultrathin LED PCBs?
Ultrathin LED PCBs offer several advantages, including space-saving design, flexibility for unique form factors, efficient heat dissipation, and suitability for applications where weight and size are significant factors, such as wearable devices and compact electronics.
What materials are used in Ultrathin LED PCBs?
Common materials used in Ultrathin LED PCBs include aluminum and copper, which offer excellent thermal conductivity for effective heat dissipation. Additionally, flexible substrates may be employed for applications requiring bendable or conformal PCBs.
What are the typical applications of Ultrathin LED PCBs?
Ultrathin LED PCBs find applications in various industries, including consumer electronics (such as smartphones, tablets, and laptops), automotive lighting, signage, display backlighting, wearable technology, and architectural lighting.
How are Ultrathin LED PCBs manufactured?
The manufacturing process for Ultrathin LED PCBs involves specialized techniques to ensure the thinness and flexibility of the PCB while maintaining thermal performance. This process includes material selection, copper foil lamination, etching, drilling, surface treatment, component assembly, testing, and quality control.
What considerations should be made when designing Ultrathin LED PCBs?
Designing Ultrathin LED PCBs requires careful consideration of thermal management, material selection, component placement, trace width, flexibility, and environmental factors to ensure optimal performance, reliability, and longevity of the LED lighting system.
Are Ultrathin LED PCBs more expensive than traditional PCBs?
Ultrathin LED PCBs may involve additional manufacturing complexity and specialized materials, which can contribute to slightly higher costs compared to traditional PCBs. However, the benefits they offer in terms of space-saving design and efficient heat dissipation often justify the investment.