Ultrathin Rogers PCB Manufacturer
Ultrathin Rogers PCB Manufacturer,Ultrathin Rogers PCBs represent the pinnacle of high-frequency circuitry, crafted with precision using Rogers Corporation’s advanced ultrathin laminate materials. These PCBs boast an exceptionally slim profile, offering unparalleled performance in compact electronic devices. Renowned for their low dielectric loss and stable operation at high frequencies, Ultrathin Rogers PCBs are the go-to choice for RF and microwave applications where space and performance are paramount. From telecommunications to aerospace, these boards excel, delivering reliable connectivity and signal integrity while pushing the boundaries of miniaturization in modern electronics.
What is an Ultrathin Rogers PCB?
An Ultrathin Rogers PCB refers to a printed circuit board (PCB) manufactured using Rogers Corporation’s ultrathin laminate materials. Rogers is a leading supplier of high-frequency laminates widely used in applications requiring excellent electrical performance, such as in the telecommunications, aerospace, and automotive industries.
These PCBs are characterized by their extremely thin profile, which offers advantages such as reduced weight and space-saving in compact electronic devices. The use of Rogers’ materials ensures superior electrical properties, including low dielectric loss and stable performance at high frequencies, making them ideal for RF (Radio Frequency) and microwave applications.
Designing and manufacturing Ultrathin Rogers PCBs require specialized expertise due to the challenges associated with handling and processing thin laminates. Techniques like controlled impedance routing and precise layer alignment are crucial to maintain signal integrity and reliability.
In summary, Ultrathin Rogers PCBs offer a combination of thinness, lightweight, and high-frequency performance, making them suitable for demanding applications where space and electrical performance are critical factors.
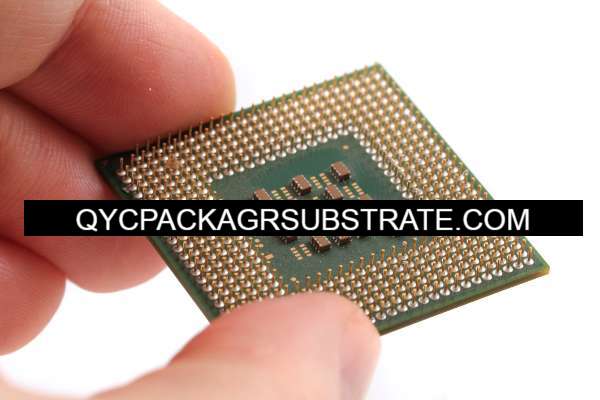
Ultrathin Rogers PCB Manufacturer
What are the Ultrathin Rogers PCB Design Guidelines?
Designing Ultrathin Rogers PCBs requires adherence to specific guidelines to ensure optimal performance and reliability. Here are some key design considerations:
- Material Selection: Choose the appropriate Rogers ultrathin laminate material based on your application requirements, considering factors like dielectric constant, loss tangent, and operating frequency.
- Layer Stackup: Design a well-defined layer stackup considering signal integrity, impedance control, and manufacturability. Typically, Ultrathin Rogers PCBs have fewer layers due to their thin profile.
- Trace Width and Spacing: Maintain appropriate trace widths and spacing to meet impedance requirements and minimize signal loss. Use controlled impedance design techniques to achieve consistent electrical performance.
- Via Design: Optimize via structures to minimize impedance disruptions and signal reflections. Use blind and buried vias where necessary to conserve space and improve signal routing.
- Component Placement: Place components strategically to minimize signal path lengths, reduce electromagnetic interference (EMI), and ensure adequate heat dissipation.
- Thermal Management: Implement effective thermal management techniques, such as thermal vias, copper pours, and heat sinks, to dissipate heat generated by high-power components.
- Grounding: Establish a solid ground plane to minimize ground loops and ensure low impedance return paths for signals. Separate analog and digital ground planes if necessary to prevent interference.
- Signal Integrity Analysis: Perform signal integrity analysis, including simulations and measurements, to validate design performance and identify potential issues such as reflections, crosstalk, and impedance mismatches.
- Design for Manufacturability (DFM): Consider manufacturability constraints such as minimum feature sizes, tolerances, and material handling requirements during the design phase to facilitate smooth production.
- Testing and Validation: Conduct thorough testing and validation of the prototype PCB to verify electrical performance, reliability, and compliance with specifications before mass production.
By following these guidelines, designers can create Ultrathin Rogers PCBs that meet the stringent requirements of high-frequency applications while ensuring robustness and manufacturability. Collaboration with experienced PCB manufacturers and adherence to industry standards further enhance the success of the design process.
What is the Ultrathin Rogers PCB Fabrication Process?
The fabrication process for Ultrathin Rogers PCBs follows a series of steps similar to standard PCB manufacturing, with some modifications to accommodate the unique properties of Rogers’ ultrathin laminates. Here’s an overview of the fabrication process:
- Material Preparation: Start by selecting the appropriate Rogers ultrathin laminate material based on the specific requirements of the PCB design. These laminates are available in various thicknesses and dielectric constants. Ensure proper storage and handling of the laminate to prevent damage.
- Layer Preparation: Prepare the copper foil and laminate materials for lamination. Clean the copper foil surfaces to remove any contaminants and oxide layers that could affect adhesion. Cut the laminate sheets to the desired size according to the PCB design specifications.
- Layer Stackup: Assemble the layers of the PCB stackup, including the ultrathin Rogers laminate layers and copper foil layers. Apply heat and pressure in a lamination press to bond the layers together into a solid panel. Ensure precise alignment of the layers to maintain signal integrity and impedance control.
- Drilling: Use precision drilling equipment to create holes for vias, through-hole components, and mounting holes. Special care must be taken to prevent delamination or damage to the thin laminate during the drilling process.
- Through-hole Plating: Plate the drilled holes with conductive material, typically copper, to establish electrical connections between the different layers of the PCB. This process may involve several steps, including electroless copper deposition and electrolytic copper plating.
- Circuit Patterning: Apply a layer of photosensitive resist material to the copper surfaces and expose it to UV light through a photomask to define the circuit traces and pads. Develop and etch away the unexposed resist to reveal the underlying copper traces.
- Surface Finishing: Apply a surface finish to protect the exposed copper traces from oxidation and facilitate soldering during assembly. Common surface finishes for Ultrathin Rogers PCBs include immersion gold, immersion silver, and OSP (Organic Solderability Preservatives).
- Legend Printing: Optionally, print component designators, logos, and other markings on the PCB surface using a legend printing process. This step enhances the PCB’s identification and assembly process.
- Testing and Inspection: Perform electrical testing, such as continuity testing and impedance measurements, to ensure the integrity of the circuit traces and vias. Inspect the PCB for any defects or irregularities that may affect performance or reliability.
- Routing and Singulation: Use routing equipment to separate individual PCBs from the panel, following the outline of the design. Optionally, perform additional routing to create complex board shapes or cutouts.
- Final Inspection and Packaging: Conduct a final inspection of the finished PCBs to verify compliance with specifications and quality standards. Package the PCBs appropriately for shipment to customers or assembly facilities.
Throughout the Ultrathin Rogers PCB fabrication process, attention to detail, precise control of parameters, and adherence to industry best practices are essential to ensure the quality and reliability of the final product. Collaboration with experienced PCB manufacturers familiar with working with ultrathin laminates can further streamline the fabrication process and optimize results.
How do you manufacture an Ultrathin Rogers PCB?
Manufacturing an Ultrathin Rogers PCB involves several specialized steps to ensure the quality, reliability, and performance of the final product. Here’s a detailed overview of the manufacturing process:
- Material Selection: Choose the appropriate Rogers ultrathin laminate material based on the specific requirements of the PCB design, considering factors such as dielectric constant, loss tangent, and operating frequency.
- Preparation of Laminate: Cut the Rogers ultrathin laminate material into the desired panel size. Ensure proper storage and handling to prevent damage to the thin laminate sheets.
- Cleaning and Surface Preparation: Clean the copper foil surfaces to remove any contaminants and oxide layers that could affect adhesion. Surface preparation is crucial for ensuring good bonding between the copper foil and the laminate material.
- Layer Stackup Assembly: Assemble the layers of the PCB stackup, including the ultrathin Rogers laminate layers and copper foil layers. Apply heat and pressure in a lamination press to bond the layers together into a solid panel. Ensure precise alignment of the layers to maintain signal integrity and impedance control.
- Drilling: Use precision drilling equipment to create holes for vias, through-hole components, and mounting holes. Special care must be taken to prevent delamination or damage to the thin laminate during the drilling process.
- Through-hole Plating: Plate the drilled holes with conductive material, typically copper, to establish electrical connections between the different layers of the PCB. This process may involve several steps, including electroless copper deposition and electrolytic copper plating.
- Circuit Patterning: Apply a layer of photosensitive resist material to the copper surfaces and expose it to UV light through a photomask to define the circuit traces and pads. Develop and etch away the unexposed resist to reveal the underlying copper traces.
- Surface Finishing: Apply a surface finish to protect the exposed copper traces from oxidation and facilitate soldering during assembly. Common surface finishes for Ultrathin Rogers PCBs include immersion gold, immersion silver, and OSP (Organic Solderability Preservatives).
- Legend Printing: Optionally, print component designators, logos, and other markings on the PCB surface using a legend printing process. This step enhances the PCB’s identification and assembly process.
- Testing and Inspection: Perform electrical testing, such as continuity testing and impedance measurements, to ensure the integrity of the circuit traces and vias. Inspect the PCB for any defects or irregularities that may affect performance or reliability.
- Routing and Singulation: Use routing equipment to separate individual PCBs from the panel, following the outline of the design. Optionally, perform additional routing to create complex board shapes or cutouts.
- Final Inspection and Packaging: Conduct a final inspection of the finished PCBs to verify compliance with specifications and quality standards. Package the PCBs appropriately for shipment to customers or assembly facilities.
Throughout the Ultrathin Rogers PCB manufacturing process, strict quality control measures, precise control of parameters, and adherence to industry standards are essential to ensure the quality and reliability of the final product. Collaboration with experienced PCB manufacturers familiar with working with ultrathin laminates can further optimize the manufacturing process and ensure excellent results.
How much should an Ultrathin Rogers PCB cost?
The cost of an Ultrathin Rogers PCB can vary significantly depending on several factors, including the following:
- Board Size: Larger PCBs typically cost more due to the increased material and manufacturing expenses.
- Number of Layers: The number of layers in the PCB stackup affects manufacturing complexity and cost. Ultrathin Rogers PCBs often have fewer layers compared to standard PCBs due to their thin profile, but additional layers may still increase costs.
- Material Choice: The specific Rogers ultrathin laminate material chosen for the PCB can impact the overall cost, as different materials have varying prices based on their properties and performance characteristics.
- Complexity of Design: PCB designs with intricate layouts, fine traces, tight spacing, and advanced features like blind/buried vias or controlled impedance routing may incur higher manufacturing costs due to increased fabrication complexity.
- Quantity: Economies of scale apply to PCB manufacturing, meaning that larger production quantities typically result in lower per-unit costs. Ordering larger quantities of Ultrathin Rogers PCBs may lead to volume discounts.
- Surface Finish and Other Finishing Options: The choice of surface finish, such as immersion gold or OSP, can affect the cost. Additional finishing options like legend printing or special coatings may also add to the overall expense.
- Lead Time: Expedited manufacturing services often come with additional costs. Longer lead times may allow for more cost-effective production scheduling.
To obtain an accurate cost estimate for an Ultrathin Rogers PCB, it’s essential to consult with PCB manufacturers or suppliers who specialize in producing these types of boards. Providing detailed specifications and design requirements will help in obtaining precise quotations tailored to your project needs.
What is Ultrathin Rogers PCB base material?
The base material for Ultrathin Rogers PCBs consists of specialized laminates produced by Rogers Corporation. Rogers offers a range of high-performance laminates designed specifically for RF/microwave applications, including those requiring ultrathin constructions.
These laminates typically consist of a combination of fiberglass reinforcement and a dielectric material, which is often a ceramic-filled polymer. The choice of dielectric material and its properties, such as dielectric constant (Dk), loss tangent (Df), and thickness, are crucial for achieving the desired electrical performance in high-frequency circuits.
Rogers’ Ultrathin PCB laminates are engineered to provide excellent electrical properties, including low loss, tight dimensional stability, and consistent performance across a wide range of frequencies. They are also designed to be compatible with standard PCB fabrication processes, allowing for efficient manufacturing of complex RF/microwave circuits.
Specific product lines from Rogers that may be used as base materials for Ultrathin PCBs include RO4000® series, RO3000® series, and RO4400™ series, among others. These laminates come in various thicknesses, ranging from very thin (e.g., 2 mils or less) to thicker options, to accommodate different design requirements and applications.
Overall, the Ultrathin Rogers PCB base material is carefully engineered to meet the demanding needs of high-frequency electronics, providing exceptional performance, reliability, and manufacturability for a wide range of applications.
Which company makes Ultrathin Rogers PCBs?
The primary manufacturer of Ultrathin Rogers PCBs is Rogers Corporation. Rogers Corporation is a renowned producer of high-performance materials, specializing in providing advanced material solutions for RF, microwave, and other high-frequency applications. The company has developed a range of high-performance laminates, including those suitable for Ultrathin PCBs.
As a PCB manufacturer, our company possesses the capability to produce Ultrathin Rogers PCBs. We have advanced manufacturing equipment and a skilled technical team capable of producing high-quality PCB products according to customer requirements and specifications. We are familiar with Rogers’ material properties and processing requirements, ensuring strict adherence to relevant technical specifications and quality standards throughout the manufacturing process.
Our production process includes material preparation, laminate assembly, drilling, plating, circuit formation, surface treatment, printing, and final inspection. We prioritize quality control and implement rigorous testing and inspection measures to ensure that each PCB product meets customer requirements and standards.
Moreover, our team provides customized technical support and solutions to meet the specific needs of our clients’ projects. We are committed to establishing long-term partnerships with our clients, providing them with reliable products and excellent service.
Therefore, our company offers comprehensive solutions for producing Ultrathin Rogers PCBs to meet the high-frequency circuit application needs of our clients, ensuring that product quality and performance meet expectations.
What are the qualities of good customer service?
Good customer service is characterized by several qualities that ensure positive interactions and satisfaction for customers. Here are some key qualities:
- Effective Communication: Good communication skills are essential for understanding customers’ needs, providing clear information, and addressing concerns promptly and courteously.
- Empathy: Showing empathy towards customers by understanding their perspective, acknowledging their feelings, and demonstrating a willingness to help can build trust and rapport.
- Knowledgeability: Customer service representatives should be knowledgeable about the products or services offered, as well as company policies and procedures, to provide accurate information and assistance.
- Responsiveness: Being responsive to customer inquiries, requests, and feedback in a timely manner demonstrates commitment to customer satisfaction and builds confidence in the company’s reliability.
- Problem-solving Skills: The ability to identify and resolve customer issues efficiently and effectively is crucial for delivering excellent customer service and maintaining customer loyalty.
- Professionalism: Maintaining professionalism in interactions with customers, including being courteous, respectful, and maintaining a positive attitude, contributes to a positive customer experience.
- Personalization: Tailoring interactions and solutions to meet individual customer needs and preferences can enhance the customer experience and foster stronger relationships.
- Follow-up: Following up with customers after resolving issues or completing transactions shows appreciation for their business and helps ensure their satisfaction over time.
- Adaptability: Being flexible and adaptable in responding to different customer situations and preferences enables customer service representatives to provide customized support and solutions.
- Consistency:Providing consistently high-quality customer service across all channels and touchpoints helps build trust and loyalty with customers over time.
By embodying these qualities, companies can deliver exceptional customer service that exceeds expectations and fosters long-term customer relationships.
FAQs
What are Ultrathin Rogers PCBs?
Ultrathin Rogers PCBs are printed circuit boards manufactured using Rogers Corporation’s ultrathin laminate materials. These PCBs are characterized by their extremely thin profile, which offers advantages such as reduced weight and space-saving in compact electronic devices.
What are the advantages of Ultrathin Rogers PCBs?
Ultrathin Rogers PCBs offer advantages such as excellent electrical performance at high frequencies, low dielectric loss, and stable performance. They are ideal for RF (Radio Frequency) and microwave applications where space and electrical performance are critical factors.
What applications are Ultrathin Rogers PCBs suitable for?
Ultrathin Rogers PCBs are suitable for a wide range of applications, including telecommunications, aerospace, automotive, medical devices, and consumer electronics. They are commonly used in RF/microwave circuits, antennas, power amplifiers, and other high-frequency applications.
How are Ultrathin Rogers PCBs manufactured?
Manufacturing Ultrathin Rogers PCBs involves specialized processes such as material preparation, layer stackup assembly, drilling, circuit patterning, surface finishing, and testing. These PCBs are produced using Rogers’ ultrathin laminate materials and may require careful handling due to their thin profile.
What design considerations are important for Ultrathin Rogers PCBs?
Designing Ultrathin Rogers PCBs requires considerations such as material selection, layer stackup design, trace width and spacing, via design, thermal management, grounding, signal integrity analysis, and manufacturability. These factors ensure optimal performance and reliability of the PCBs.
Where can I source Ultrathin Rogers PCBs?
Ultrathin Rogers PCBs can be sourced from reputable PCB manufacturers or suppliers that specialize in high-frequency PCBs. It’s essential to choose a manufacturer with experience in working with Rogers’ materials and expertise in producing Ultrathin PCBs to ensure quality and performance.
What are the cost considerations for Ultrathin Rogers PCBs?
The cost of Ultrathin Rogers PCBs depends on factors such as board size, number of layers, material choice, complexity of design, quantity, surface finish, lead time, and additional finishing options. Requesting quotations from PCB manufacturers can provide a better understanding of the cost implications for specific projects.