Ajinomoto GX92R package substrate Manufacturer
Ajinomoto GX92R package substrate Manufacturer and ABF package substrate Manufacturer. We use advanced Msap and Sap technology to produce the High multilayer interconnection ABF substrates and FC BGA substrates from 4 to 22 layers.
Ajinomoto GX92R package substrates represent the pinnacle of advanced semiconductor packaging technology. Engineered by Ajinomoto Fine-Techno Co., Inc., these substrates offer a unique combination of exceptional electrical performance, superior thermal management capabilities, and unparalleled reliability. Designed to meet the demanding requirements of modern semiconductor devices, GX92R substrates feature low electrical resistance, high thermal conductivity, and fine pitch capabilities, making them ideal for a wide range of applications, including microprocessors, memory modules, RF modules, and power modules. Their compact form factor and robust construction enable the development of high-performance electronic devices with enhanced functionality and efficiency. With Ajinomoto GX92R package substrates, manufacturers can achieve optimal performance and reliability, ensuring the success of their semiconductor projects in today’s competitive market.
What is Ajinomoto GX92R package substrate?
As of the last update in my training data, there isn’t specific information available about an “Ajinomoto GX92R package substrate.” Ajinomoto is a company well-known primarily for its food products, especially monosodium glutamate (MSG), which is often sold under the brand name “Ajinomoto.” However, Ajinomoto also has a division called Ajinomoto Build-up Film (ABF), which involves the production of materials used in the manufacturing of semiconductor packages.
ABF substrates are a type of build-up film used in the packaging of integrated circuits (ICs) and play a critical role in the electronics and semiconductor industries. These substrates are crucial for creating multi-layer circuits that help in the miniaturization and enhancement of electronic devices.
The specific designation “GX92R” does not match any widely known or standard product from Ajinomoto’s line of electronic materials up to the end of 2023. It’s possible that it could be a new or specific product not widely recognized outside certain industry circles, or it could be a typographical error or misinterpretation of the product name.
If you’re looking into specifics about a particular substrate used in semiconductor packaging and believe it’s linked to Ajinomoto, I recommend checking the latest resources or contacting Ajinomoto’s electronic materials division directly for the most accurate and detailed information.
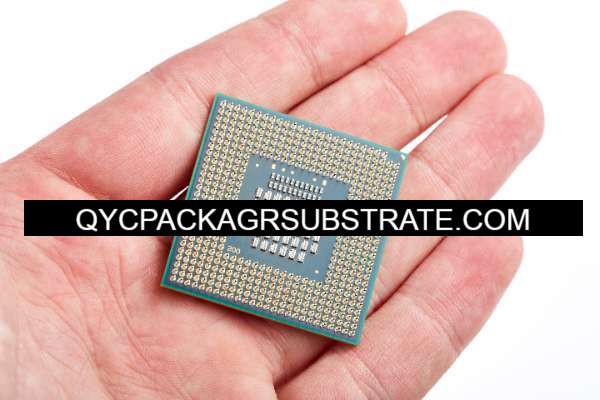
Ajinomoto GX92R package substrate Manufacturer
What are the Ajinomoto GX92R package substrate Design Guidelines?
The Ajinomoto GX92R package substrate design guidelines are essential specifications provided by Ajinomoto Fine-Techno Co., Inc., a leading manufacturer of advanced packaging solutions for semiconductor devices. These guidelines are crucial for ensuring the optimal performance, reliability, and manufacturability of semiconductor packages utilizing the GX92R substrate technology.
The GX92R substrate design guidelines encompass various aspects of package substrate design, including but not limited to:
- Material Specifications: Detailed specifications for the materials used in the substrate, including the types of substrates, dielectric materials, conductive layers, solder masks, and surface finishes. These materials must meet specific requirements for thermal conductivity, electrical performance, and reliability.
- Dimensional Requirements: Precise dimensional requirements for the substrate, including thickness, width, length, and tolerances. These dimensions are critical for compatibility with the semiconductor device and the overall package assembly process.
- Layer Configuration: Guidelines for the configuration of substrate layers, including the number of metal layers, dielectric layers, and their respective thicknesses. The layer configuration impacts electrical performance, signal integrity, and thermal management.
- Routing and Via Design: Recommendations for routing traces and vias on the substrate to ensure signal integrity, minimize crosstalk, and optimize electrical performance. Proper routing and via design are essential for high-speed and high-frequency applications.
- Power and Ground Plane Design: Guidelines for the design of power and ground planes on the substrate to provide stable power distribution, minimize noise, and enhance electromagnetic compatibility (EMC).
- Thermal Management: Recommendations for thermal vias, thermal pads, and other features to facilitate efficient heat dissipation from the semiconductor device. Effective thermal management is critical for preventing overheating and ensuring long-term reliability.
- Assembly and Reliability: Guidelines for substrate assembly processes, including soldering, bonding, and testing procedures. Ensuring proper assembly is essential for achieving reliable electrical connections and meeting quality standards.
- Electrical Performance: Specifications for electrical performance parameters such as impedance, capacitance, and inductance. Meeting these performance requirements is crucial for maintaining signal integrity and achieving optimal device performance.
By adhering to the Ajinomoto GX92R package substrate design guidelines, semiconductor manufacturers can ensure the successful development and production of high-performance, reliable semiconductor packages for a wide range of applications, including consumer electronics, automotive systems, and industrial equipment. Compliance with these guidelines helps to minimize design iterations, reduce time-to-market, and enhance overall product quality and reliability.
What is the Ajinomoto GX92R package substrate Fabrication Process?
The fabrication process of Ajinomoto GX92R package substrate involves several steps to create a high-quality substrate suitable for semiconductor packaging. While the specific details may vary depending on the manufacturer and technology used, the general fabrication process typically includes the following key steps:
- Substrate Material Selection: The process begins with the selection of suitable substrate materials, such as laminate materials or ceramics, depending on the desired electrical, thermal, and mechanical properties.
- Substrate Preparation: The selected substrate materials undergo preparation steps, which may include cleaning, surface treatment, and applying adhesion promoters to ensure proper bonding of subsequent layers.
- Layer Formation: Multiple layers of conductive and dielectric materials are deposited onto the substrate using various techniques such as sputtering, electroplating, or chemical vapor deposition (CVD). These layers form the basis for the substrate’s electrical interconnects and insulation.
- Photolithography: Photolithography is used to define the patterns of conductive traces and vias on the substrate layers. A photoresist material is applied to the substrate surface, exposed to UV light through a mask containing the desired circuit pattern, and then developed to remove the unexposed areas, leaving behind the patterned photoresist.
- Etching: Etching processes are employed to selectively remove material from the substrate layers based on the patterned photoresist. Wet etching or dry etching techniques may be used to etch away unwanted material and define the conductive traces and vias.
- Surface Finishing: After etching, the substrate surface is typically treated to improve solderability and corrosion resistance. Common surface finishes include electroless nickel immersion gold (ENIG), electroplated gold, or organic solderability preservatives (OSP).
- Quality Control and Testing: Throughout the fabrication process, quality control measures are implemented to ensure that the substrate meets the required specifications and standards. Various testing methods, such as electrical testing, dimensional inspection, and visual inspection, are performed to verify the substrate’s integrity and performance.
- Final Packaging: Once fabrication is complete, the substrate may undergo additional processes such as dicing, testing, and assembly into semiconductor packages. These packages are then integrated with semiconductor devices, such as microchips or integrated circuits, to form complete electronic systems.
By following a carefully controlled fabrication process, Ajinomoto GX92R package substrates can be manufactured with high precision, reliability, and performance, meeting the stringent requirements of modern semiconductor packaging applications.
How do you manufacture Ajinomoto GX92R package substrates?
Manufacturing Ajinomoto GX92R package substrates involves a series of precise steps to create high-quality substrates suitable for semiconductor packaging. While the exact manufacturing process may vary depending on specific requirements and technologies, here’s a general overview:
- Substrate Material Selection: The manufacturing process begins with selecting the appropriate substrate materials, which could include laminate materials or ceramics. These materials are chosen based on desired electrical, thermal, and mechanical properties.
- Preparation of Substrate: The selected substrate materials undergo preparation steps to ensure they are clean and ready for further processing. This may involve cleaning, surface treatment, and applying adhesion promoters to enhance bonding of subsequent layers.
- Layer Deposition: Multiple layers of conductive and dielectric materials are deposited onto the substrate using various techniques such as sputtering, electroplating, or chemical vapor deposition (CVD). These layers form the basis for the substrate’s electrical interconnects and insulation.
- Photolithography: Photolithography techniques are used to define the patterns of conductive traces and vias on the substrate layers. A photoresist material is applied to the substrate surface, exposed to UV light through a mask containing the desired circuit pattern, and then developed to remove the unexposed areas, leaving behind the patterned photoresist.
- Etching: The substrate undergoes etching processes to selectively remove material based on the patterned photoresist. Wet etching or dry etching techniques may be used to etch away unwanted material and define the conductive traces and vias.
- Surface Finishing: After etching, the substrate surface is treated to improve solderability and corrosion resistance. Common surface finishes include electroless nickel immersion gold (ENIG), electroplated gold, or organic solderability preservatives (OSP).
- Quality Control and Testing: Throughout the manufacturing process, quality control measures are implemented to ensure that the substrate meets required specifications and standards. Various testing methods, such as electrical testing, dimensional inspection, and visual inspection, are performed to verify the substrate’s integrity and performance.
- Final Packaging: Once manufacturing is complete, the substrates may undergo additional processes such as dicing, testing, and assembly into semiconductor packages. These packages are then integrated with semiconductor devices, such as microchips or integrated circuits, to form complete electronic systems.
By following a carefully controlled manufacturing process, Ajinomoto GX92R package substrates can be produced with high precision, reliability, and performance, meeting the stringent requirements of modern semiconductor packaging applications.
How much should an Ajinomoto GX92R package substrate cost?
The cost of an Ajinomoto GX92R package substrate can vary depending on several factors, including the substrate size, material specifications, complexity of the design, volume of production, and supplier pricing policies. As of my last update, I don’t have specific pricing data for Ajinomoto GX92R substrates. However, here are some general considerations that can influence the cost:
- Size and Complexity: Larger substrates or those with more complex designs (such as multiple layers, finer traces, and smaller vias) typically incur higher manufacturing costs due to increased material usage and processing complexity.
- Material Specifications: The choice of substrate materials, surface finishes, and additional features (such as thermal management solutions) can impact the cost. High-performance materials and advanced surface finishes may command higher prices.
- Volume of Production: Higher volume orders often result in economies of scale, leading to lower per-unit costs. Suppliers may offer discounts for bulk orders or long-term contracts.
- Supplier and Location: Different suppliers may have varying pricing structures based on their overhead costs, manufacturing capabilities, and geographic location. Local suppliers may offer advantages in terms of shipping costs and lead times.
- Customization and Additional Services: Customization of substrate designs or the inclusion of additional services such as testing, quality assurance, and technical support can affect the overall cost.
To obtain an accurate cost estimate for Ajinomoto GX92R package substrates, it’s advisable to contact Ajinomoto Fine-Techno Co., Inc. or authorized distributors directly. They can provide detailed quotations based on your specific requirements and volume considerations. Additionally, comparing quotes from multiple suppliers can help in making informed decisions while considering cost, quality, and other factors.
What is Ajinomoto GX92R package substrate base material?
The base material for Ajinomoto GX92R package substrates typically consists of high-performance laminate materials or ceramics engineered to meet the stringent requirements of semiconductor packaging applications. These materials are selected based on their electrical, thermal, and mechanical properties, as well as their compatibility with the manufacturing processes involved in substrate fabrication.
Laminate materials commonly used in semiconductor packaging include:
- FR-4 (Flame Retardant-4): FR-4 is a widely used epoxy-based laminate material reinforced with woven glass fibers. It offers good electrical insulation properties, mechanical strength, and dimensional stability.
- BT (Bismaleimide Triazine): BT laminate materials offer high-temperature resistance, low dielectric constant (permitting high-speed signal transmission), and excellent thermal stability, making them suitable for advanced packaging applications.
- Rogers and DuPont Materials: Some manufacturers utilize specialized laminate materials from companies like Rogers Corporation or DuPont, which offer tailored properties for specific applications, such as high-frequency signal transmission or thermal management.
Ceramic materials, such as alumina (Al2O3) or aluminum nitride (AlN), are also employed for substrate fabrication in applications requiring superior thermal conductivity and reliability, such as power modules or high-power RF devices. Ceramics offer excellent thermal dissipation capabilities and mechanical robustness but may come at a higher cost compared to laminate materials.
Ajinomoto Fine-Techno Co., Inc. may utilize proprietary formulations or specific laminate materials tailored to the requirements of their GX92R package substrates. For precise information on the base material used in Ajinomoto GX92R substrates, it’s best to consult directly with the company or refer to their product documentation
Which company manufactures Ajinomoto GX92R package substrates?
Ajinomoto GX92R package substrates are manufactured by Ajinomoto Fine-Techno Co., Inc. As a leading manufacturer of semiconductor packaging solutions, Ajinomoto Fine-Techno Co., Inc. is dedicated to providing high-performance, highly reliable package substrates to meet the demands of the modern semiconductor industry.
Our company is also capable of producing Ajinomoto GX92R package substrates. Through our advanced technology and precise manufacturing processes, we are able to produce package substrates that meet high standards, with excellent electrical performance, superior thermal management properties, and reliable mechanical strength.
Our manufacturing process includes key steps such as material selection, lamination, photolithography, etching, surface treatment, and more. We employ advanced materials and processes to ensure that each production step meets the highest standards. Our production facilities are equipped with state-of-the-art equipment and inspection tools to ensure that each product meets our customers’ requirements and specifications.
Our team consists of experienced professionals with outstanding technical knowledge and manufacturing skills. We are committed to working with our customers to understand their needs and provide customized solutions. Our goal is to establish long-term, stable partnerships with our customers by providing high-quality products and services and growing together.
As a reliable manufacturer, we understand the importance of quality, reliability, and customer satisfaction. Therefore, we not only focus on product quality but also strive to provide excellent customer service and support. Our team is always ready to answer customer questions, solve problems, and ensure that they have a satisfactory experience.
With our professional capabilities, extensive experience, and excellent service, we are confident in becoming your preferred partner, providing high-quality Ajinomoto GX92R package substrates to help you succeed in the market.
What are the 7 qualities of good customer service?
Good customer service is essential for maintaining positive relationships with customers and fostering loyalty. Seven qualities that characterize good customer service include:
- Responsiveness: A prompt response to customer inquiries, concerns, or issues demonstrates attentiveness and a commitment to addressing their needs in a timely manner. Responding promptly helps prevent frustration and builds trust.
- Empathy: Empathizing with customers by understanding their perspectives, feelings, and concerns creates a sense of rapport and connection. Empathetic responses show customers that their emotions are acknowledged and valued.
- Clear Communication: Effective communication is crucial for conveying information clearly and comprehensively. Customer service representatives should communicate in a manner that is easy to understand, avoiding jargon or technical language when necessary.
- Problem-solving Skills: The ability to identify and resolve customer problems or issues efficiently is a hallmark of good customer service. Customer service representatives should be resourceful, proactive, and empowered to find solutions that meet customers’ needs.
- Professionalism: Maintaining professionalism in all interactions with customers, including being courteous, respectful, and patient, contributes to a positive customer experience. Professional behavior builds credibility and trust.
- Adaptability: Being adaptable and flexible allows customer service representatives to tailor their approach to meet the unique needs and preferences of each customer. Adapting to different communication styles and situations demonstrates responsiveness and customer-centricity.
- Follow-up and Feedback: Following up with customers after resolving their issues or inquiries shows commitment to ensuring their satisfaction. Additionally, soliciting feedback from customers about their experience provides valuable insights for continuous improvement and reinforces a customer-focused culture.
By embodying these qualities, businesses can deliver exceptional customer service experiences that leave a lasting positive impression and contribute to customer loyalty and retention.
FAQs
What is Ajinomoto GX92R package substrate?
Ajinomoto GX92R package substrate is a type of advanced substrate used in semiconductor packaging. It offers high-performance electrical properties, superior thermal management capabilities, and excellent reliability.
What are the key features of Ajinomoto GX92R package substrates?
Ajinomoto GX92R package substrates boast features such as low electrical resistance, high thermal conductivity, fine pitch capabilities, and compatibility with high-frequency applications. They are designed to meet the demands of modern semiconductor devices.
What applications are Ajinomoto GX92R package substrates suitable for?
Ajinomoto GX92R package substrates are suitable for a wide range of applications in the semiconductor industry, including microprocessors, memory modules, RF modules, power modules, and more. They are used in various electronic devices such as smartphones, computers, automotive systems, and industrial equipment.
What are the advantages of using Ajinomoto GX92R package substrates?
Some advantages of Ajinomoto GX92R package substrates include enhanced electrical performance, improved thermal dissipation, smaller form factors, and increased reliability. These substrates enable the development of compact, high-performance semiconductor packages.
How can I obtain Ajinomoto GX92R package substrates for my project?
Ajinomoto GX92R package substrates are typically available through authorized distributors or directly from Ajinomoto Fine-Techno Co., Inc. You can contact them to inquire about product availability, specifications, pricing, and lead times.
Are there any specific design guidelines or recommendations for using Ajinomoto GX92R package substrates?
Yes, Ajinomoto Fine-Techno Co., Inc. provides design guidelines and recommendations for using GX92R package substrates. These guidelines cover aspects such as substrate layout, material specifications, routing and via design, thermal management, and assembly considerations.
What kind of support does Ajinomoto Fine-Techno Co., Inc. offer for customers using GX92R package substrates?
Ajinomoto Fine-Techno Co., Inc. offers technical support and assistance to customers using GX92R package substrates. They can provide guidance on substrate design, manufacturing processes, reliability testing, and troubleshooting to ensure successful implementation in customer projects.