Ajinomoto GXT31R2 package substrate Manufacturer
We are a professional Ajinomoto GXT31R2 package substrate Manufacturer, we mainly produce ultra-small bump pitch substrate, ultra-small trace and spacing packaging substrate and PCBs.
The Ajinomoto GXT31R2 package substrate represents a pinnacle of semiconductor packaging innovation. Engineered by Ajinomoto Co., Ltd., a renowned Japanese company known for its excellence in chemical products, this substrate serves as a fundamental component in electronic devices, facilitating seamless integration of semiconductor chips. Boasting exceptional electrical conductivity and superior thermal management properties, the GXT31R2 substrate ensures optimal signal integrity and reliability, even in demanding applications. Its advanced design and customizable features make it versatile for various electronic devices, including integrated circuits and microprocessors. With a commitment to quality and performance, Ajinomoto delivers a substrate solution that meets the rigorous standards of the semiconductor industry, empowering technological advancements and driving innovation forward.
What is Ajinomoto GXT31R2 package substrate?
The Ajinomoto GXT31R2 package substrate is a type of substrate material used in semiconductor packaging. Substrates are the foundation upon which semiconductor devices are built, providing the structural and electrical connections between the chip and the rest of the electronic system. The GXT31R2 substrate is likely manufactured by Ajinomoto Co., Inc., a Japanese company known for producing various chemical products including materials for electronics.
While I don’t have specific details about the GXT31R2 package substrate beyond its name, it’s probable that it offers certain characteristics such as good electrical conductivity, thermal performance, reliability, and compatibility with semiconductor manufacturing processes. These substrates are essential components in the assembly of integrated circuits and other electronic devices.
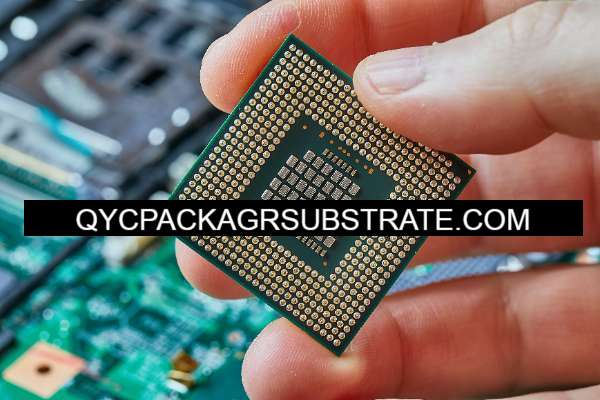
Ajinomoto GXT31R2 package substrate Manufacturer
What are the Ajinomoto GXT31R2 package substrate Design Guidelines?
I don’t have access to specific design guidelines for the Ajinomoto GXT31R2 package substrate, as those would typically be proprietary information provided by Ajinomoto to their customers or partners. However, I can provide some general considerations that might apply to the design of package substrates in semiconductor manufacturing.
- Electrical Performance: Ensure that the substrate material offers low electrical resistance and high signal integrity to facilitate efficient communication between the semiconductor chip and the rest of the electronic system. This involves optimizing trace routing and via placement.
- Thermal Management: Effective heat dissipation is crucial to maintaining the reliability and performance of semiconductor devices. Design the substrate with features such as thermal vias, thermal pads, or heat spreaders to efficiently transfer heat away from the chip.
- Material Compatibility: Consider the compatibility of the substrate material with the semiconductor manufacturing process, including factors such as solderability, adhesion, and chemical resistance. The substrate material should be compatible with the soldering process used to attach the semiconductor chip to the substrate.
- Package Size and Shape: Design the substrate to accommodate the specific size and shape requirements of the semiconductor package. This involves determining the optimal dimensions and layout of the substrate to ensure proper alignment and connection with other components in the electronic system.
- Signal and Power Integrity: Ensure that the substrate design minimizes signal distortion and power delivery issues such as voltage drop and noise. This may involve careful impedance matching, power plane design, and decoupling capacitor placement.
- Reliability:Design the substrate to withstand mechanical stresses, temperature fluctuations, and other environmental factors encountered during the lifespan of the electronic device. This includes considerations such as material strength, solder joint reliability, and mechanical stability.
- Manufacturability: Optimize the substrate design for manufacturability, taking into account factors such as fabrication process complexity, yield, and cost-effectiveness. Design guidelines should aim to streamline the production process while maintaining quality and performance standards.
While these guidelines are general in nature, specific design considerations for the Ajinomoto GXT31R2 package substrate would depend on its unique characteristics and intended application within the semiconductor industry.
What is the Ajinomoto GXT31R2 package substrate Fabrication Process?
How do you manufacture Ajinomoto GXT31R2 package substrate?
The Ajinomoto GXT31R2 package substrate is a specific product, and the manufacturing process for it would likely be proprietary to Ajinomoto Co., Inc., the company that produces it. However, I can give you a general overview of how package substrates are typically manufactured.
- Substrate Material Selection: Package substrates are often made of materials like FR-4 (a type of fiberglass-reinforced epoxy laminate), polyimide, or ceramic, depending on the specific requirements of the application.
- Substrate Preparation: The substrate material is prepared by cutting it into the desired size and shape. This may involve processes such as cutting, drilling, and milling to create the necessary features like holes and channels.
- Copper Deposition: Copper is deposited onto the substrate surface through processes like electroplating or sputtering. This copper layer forms the conductive traces that connect the various components of the electronic device.
- Etching: The excess copper is removed from the substrate surface using a process called etching. This leaves behind the desired copper traces, which form the electrical connections on the substrate.
- Surface Treatment: The substrate surface may undergo various treatments to improve its solderability, adhesion, and resistance to environmental factors such as moisture and corrosion.
- Lamination: In some cases, multiple layers of substrate may be laminated together to create a multilayer package substrate. Each layer may have its own copper traces and vias, which are interconnected through processes like laser drilling.
- Final Inspection and Testing: The finished package substrates undergo thorough inspection and testing to ensure that they meet the required specifications for electrical performance, dimensional accuracy, and reliability.
- Packaging and Shipping: Once the substrates pass inspection, they are packaged according to the customer’s requirements and shipped to their destination.
For specific details on the manufacturing process of the Ajinomoto GXT31R2 package substrate, you would need to contact Ajinomoto Co., Inc. directly or refer to any documentation or technical specifications they provide.
How much should Ajinomoto GXT31R2 package substrate cost?
Determining the exact cost of the Ajinomoto GXT31R2 package substrate would require access to specific pricing information from Ajinomoto or its distributors, as well as consideration of factors such as quantity, customization, and market conditions. However, I can provide some general factors that may influence the cost of package substrates in the semiconductor industry:
- Material Costs:The cost of raw materials used in manufacturing the substrate, including dielectric materials, copper foils, and other additives, will significantly impact the overall cost.
- Manufacturing Complexity: The complexity of the substrate design and fabrication process, including factors such as the number of layers, feature density, and tolerances required, will affect manufacturing costs.
- Production Volume: Economies of scale play a significant role in semiconductor manufacturing. Higher production volumes generally lead to lower per-unit costs due to efficiencies in material usage, equipment utilization, and overhead expenses.
- Technology and Innovation: Substrates utilizing advanced technologies or incorporating innovative features may command higher prices due to their enhanced performance or unique capabilities.
- Customization and Special Requirements: Customization, such as specific layout designs or additional surface treatments, may incur additional costs. Substrates designed to meet stringent performance or reliability standards may also be priced higher.
- Supplier Relationships: Long-term relationships with suppliers and bulk purchasing agreements may result in discounted pricing for customers.
- Market Dynamics: Supply and demand dynamics, as well as competition within the semiconductor industry, can influence substrate pricing. Changes in market conditions, such as fluctuations in raw material costs or shifts in demand, may impact pricing levels.
Without specific pricing information from Ajinomoto or its authorized distributors, it’s challenging to provide an accurate cost estimate for the GXT31R2 package substrate. Pricing for semiconductor components is typically negotiated based on factors such as order volume, contractual agreements, and prevailing market conditions. Customers interested in acquiring the Ajinomoto GXT31R2 substrate should contact Ajinomoto directly or consult with authorized distributors for pricing information.
What is Ajinomoto GXT31R2 package substrate base material?
The base material of the Ajinomoto GXT31R2 package substrate is not publicly disclosed, as it likely involves proprietary formulations and manufacturing processes owned by Ajinomoto Co., Inc. However, I can offer insights into the typical materials used in semiconductor package substrates, which may provide a general understanding of what could be utilized in the GXT31R2.
- Dielectric Material: The substrate’s base often consists of a dielectric material, which serves as the insulating layer between conductive traces and layers. Common dielectric materials include epoxy resin, polyimide, BT (bismaleimide triazine), and FR-4 (flame-retardant fiberglass-reinforced epoxy).
- Conductive Layers: Copper foils are commonly used to create the conductive layers (traces) on the substrate. These copper foils are typically laminated onto the dielectric material during the fabrication process.
- Additional Additives: Depending on the specific requirements of the substrate, additional additives may be incorporated into the base material. For example, fillers or reinforcements such as glass fibers may be added to enhance mechanical strength and thermal stability.
- Surface Finishes: Surface finishes are applied to the substrate to improve solderability and protect against oxidation. Common surface finishes include solder mask, which provides a protective layer over non-conductive areas, and metal finishes such as immersion silver, immersion tin, or electroless nickel immersion gold (ENIG) for solderable surfaces.
- Adhesive Materials: Adhesive materials may be used during the lamination process to bond different layers of the substrate together. These adhesives should provide strong bonding while maintaining compatibility with subsequent manufacturing processes.
The selection of base materials for package substrates depends on various factors such as electrical performance requirements, thermal management needs, mechanical strength, and compatibility with assembly processes. Ajinomoto, as a leading provider of chemical products, likely leverages its expertise to develop proprietary formulations optimized for the GXT31R2 substrate, balancing performance, reliability, and manufacturability.
For detailed information on the specific base material used in the Ajinomoto GXT31R2 package substrate, it would be necessary to consult Ajinomoto’s technical documentation or reach out to the company directly for proprietary details.
Which company makes Ajinomoto GXT31R2 package substrate?
The Ajinomoto GXT31R2 package substrate is manufactured by Ajinomoto Co., Ltd. in Japan. However, our company also has the capability to produce similar package substrates. As a technologically advanced and experienced semiconductor packaging material manufacturer, we possess advanced process technology and a research and development team capable of designing and manufacturing high-performance package substrates according to customer requirements.
Our company has been focusing on the research and production of semiconductor packaging materials for many years, with advanced production equipment and a strict quality control system in place. Our manufacturing process covers various steps required for package substrates, including material preparation, lamination, circuit fabrication, metallization treatment, surface coating, and more. We can provide customized solutions tailored to specific characteristics and performance requirements based on customer needs.
We are committed to providing high-quality and reliable products to meet customer demands. With our experienced team, we offer technical support and solutions to ensure the smooth progress of customer projects. Our production capabilities and flexibility allow us to serve customers of different scales and requirements, delivering high-quality package substrate products and services.
In summary, although the Ajinomoto GXT31R2 package substrate is manufactured by Ajinomoto Co., Ltd., our company also possesses the capability to produce similar products. With our rich experience and expertise, we can provide customized package substrate solutions according to customer requirements, ensuring product quality and performance meet industry standards.
What are the 7 qualities of good customer service?
Good customer service is essential for building strong relationships with customers and fostering loyalty. Here are seven qualities that characterize excellent customer service:
- Responsiveness: Responding promptly to customer inquiries, concerns, and requests demonstrates attentiveness and shows customers that their needs are being taken seriously. Timely responses help to resolve issues quickly and prevent further dissatisfaction.
- Empathy: Empathy involves understanding and acknowledging the customer’s perspective, feelings, and concerns. By empathizing with customers, service representatives can show genuine care and compassion, which helps to build trust and rapport.
- Clear Communication: Effective communication is key to delivering excellent customer service. Service representatives should be able to convey information clearly, listen actively to customers’ needs, and provide concise and accurate answers to their questions.
- Problem-Solving Skills: Good customer service involves the ability to address and resolve customer issues effectively. Service representatives should be resourceful, proactive, and capable of finding solutions to problems in a timely manner.
- Professionalism: Maintaining professionalism in all interactions with customers is crucial for building credibility and trust. Service representatives should be courteous, respectful, and maintain a positive attitude, even in challenging situations.
- Product Knowledge: Having a thorough understanding of the products or services offered allows service representatives to provide accurate information and assist customers more effectively. Customers appreciate dealing with knowledgeable representatives who can offer expert guidance and advice.
- Follow-Up: Following up with customers after resolving an issue or completing a transaction demonstrates commitment to their satisfaction. Service representatives can check in to ensure that the customer’s needs have been met and offer additional assistance if necessary, fostering long-term relationships.
By embodying these qualities, businesses can deliver exceptional customer service experiences that leave a positive impression and encourage repeat business and referrals.
FAQs
What is the Ajinomoto GXT31R2 package substrate?
The Ajinomoto GXT31R2 package substrate is a type of substrate material used in semiconductor packaging. It serves as the foundation for mounting semiconductor chips and providing electrical connections within electronic devices.
What are the key features of the Ajinomoto GXT31R2 package substrate?
While specific details may vary, key features may include high electrical conductivity, excellent thermal performance, reliability, compatibility with semiconductor manufacturing processes, and possibly unique proprietary characteristics developed by Ajinomoto.
What are the applications of the Ajinomoto GXT31R2 package substrate?
The substrate may be used in various electronic devices, including integrated circuits, microprocessors, memory modules, and other semiconductor-based products where high-performance packaging is required.
What advantages does the Ajinomoto GXT31R2 package substrate offer?
Advantages may include improved signal integrity, enhanced thermal management, increased reliability, and potentially cost-effective manufacturing solutions.
Is the Ajinomoto GXT31R2 package substrate customizable?
Depending on Ajinomoto’s offerings and customer requirements, the substrate may be customizable to some extent in terms of size, layout, material composition, and other parameters.
How can I obtain the Ajinomoto GXT31R2 package substrate for my project?
Interested parties can inquire about the substrate through Ajinomoto’s official channels, such as their website or authorized distributors. They can provide information on availability, pricing, and customization options.
What technical support is available for the Ajinomoto GXT31R2 package substrate?
Ajinomoto may offer technical support, including documentation, design guidelines, and assistance with integration into specific applications. Customers can reach out to Ajinomoto for further information and support.
What quality assurance measures are in place for the Ajinomoto GXT31R2 package substrate?
Ajinomoto likely implements stringent quality control processes to ensure that the substrate meets industry standards and customer expectations. This may involve testing for electrical performance, thermal characteristics, reliability, and other criteria.