Ajinomoto Package Substrate Manufacturer
Ajinomoto Package Substrate Manufacturer. the Package Substrate will be made with Showa Denko and Ajinomoto High speed materials.or other types high speed materials and high frequency materials.
Ajinomoto Package Substrate (APS) represents a cutting-edge solution in the realm of semiconductor packaging. Renowned for its unparalleled thermal management capabilities, APS revolutionizes the integration of integrated circuits (ICs) by delivering superior electrical performance and reliability. Engineered with precision and innovation, APS empowers industries ranging from telecommunications to automotive electronics, enabling the creation of compact and efficient electronic devices. Its advanced design not only enhances thermal conductivity but also minimizes signal loss, making it ideal for high-frequency applications such as RF modules and power amplifiers. With a commitment to quality and innovation, APS sets a new standard for semiconductor packaging, driving forward the evolution of technology and meeting the ever-growing demands of the modern electronics industry.
What is Ajinomoto Package Substrate (APS)?
Ajinomoto Package Substrate (APS) is a technology developed by Ajinomoto Fine-Techno Co., Inc., a subsidiary of Ajinomoto Group, a Japanese company known for its food and biotechnology products. APS is a specialized substrate material used in the semiconductor industry for the packaging of integrated circuits (ICs).
APS offers several advantages over traditional substrate materials like ceramic or organic substrates. It provides superior electrical performance, thermal conductivity, and reliability, making it suitable for high-frequency and high-power applications. Additionally, APS enables the integration of multiple functions within a single package, reducing the overall size and weight of electronic devices.
The key features of APS include its excellent thermal management properties, low signal loss, and compatibility with advanced packaging techniques such as flip-chip bonding and through-silicon vias (TSVs). These characteristics make APS particularly well-suited for applications in telecommunications, automotive electronics, and high-performance computing.
Furthermore, APS contributes to the miniaturization and performance improvement of electronic devices by enabling the development of smaller and more efficient packages. Its widespread adoption in the semiconductor industry underscores its importance as a critical enabler of technological innovation and progress.
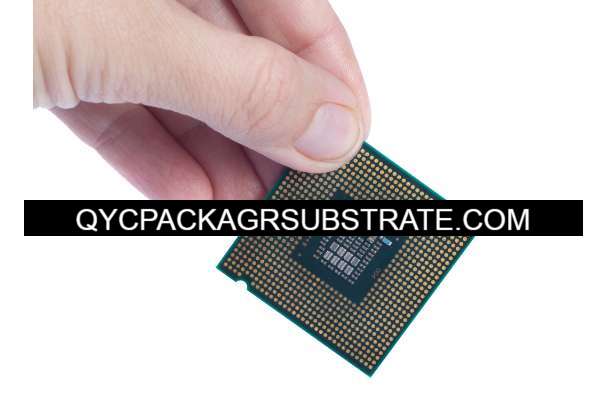
Ajinomoto Package Substrate Manufacturer
What are the Ajinomoto Package Substrate (APS) Design Guidelines?
Ajinomoto Package Substrate (APS) design guidelines provide recommendations and specifications for designing electronic packages using APS technology. While the exact guidelines may vary depending on the specific application and requirements, some common design considerations for APS include:
- Thermal Management: APS is known for its excellent thermal conductivity, so it’s essential to design packages that effectively dissipate heat from the integrated circuits. This may involve incorporating thermal vias, heat sinks, or other thermal management features into the substrate design.
- Signal Integrity: Maintaining signal integrity is crucial for high-frequency applications. Design guidelines may include recommendations for minimizing signal loss, impedance control, and reducing electromagnetic interference (EMI) through careful layout and routing of traces.
- Power Distribution: Efficient power distribution is vital to ensure stable operation of the integrated circuits. Design guidelines may address power plane layout, decoupling capacitor placement, and power delivery network (PDN) design to minimize voltage drops and noise.
- Manufacturability: Designs should be manufacturable within the capabilities of the fabrication process. Guidelines may specify minimum trace widths and clearances, layer stack-up configurations, and other considerations to ensure successful fabrication and assembly of the package.
- Reliability: Packages must meet reliability requirements to ensure long-term operation in harsh environments. Design guidelines may include recommendations for materials selection, solder joint design, and mechanical reinforcement to enhance durability and resistance to thermal and mechanical stresses.
- Package Size and Form Factor: APS technology enables the development of compact and lightweight packages. Design guidelines may provide recommendations for optimizing package size and form factor while meeting performance and reliability requirements.
- Electromagnetic Compatibility (EMC): To minimize electromagnetic interference (EMI) and ensure compatibility with regulatory standards, design guidelines may include provisions for shielding, grounding, and isolation of sensitive components.
- Cost Optimization: Design guidelines may also address cost considerations by optimizing material usage, minimizing fabrication complexity, and maximizing yield during manufacturing.
Overall, adhering to APS design guidelines ensures that electronic packages meet performance, reliability, and manufacturability requirements while leveraging the unique capabilities of APS technology.
What is the Ajinomoto Package Substrate (APS) Fabrication Process?
The fabrication process for Ajinomoto Package Substrate (APS) involves several steps to create the specialized substrate material used in semiconductor packaging. While specific details may vary depending on the manufacturer and the desired characteristics of the APS, a typical fabrication process may include the following steps:
- Substrate Preparation: The fabrication process begins with the preparation of a base substrate material, typically a high-performance composite material such as silicon, glass, or a ceramic material. This substrate serves as the foundation for the APS.
- Material Deposition: Various layers of materials are deposited onto the substrate using techniques such as physical vapor deposition (PVD), chemical vapor deposition (CVD), or sputtering. These layers may include conductive metals for signal traces and power planes, dielectric materials for insulation, and other specialized materials to enhance thermal conductivity, reliability, and performance.
- Lithography: A patterned mask is used to selectively expose regions of the deposited material layers. This process, known as lithography, defines the desired circuitry layout and features on the APS substrate.
- Etching: Exposed regions of the material layers are then etched away using chemical or physical etching processes, leaving behind the desired patterned features such as conductive traces, vias, and pads.
- Surface Finishing: Surface finishing processes such as chemical mechanical polishing (CMP) or electroplating may be employed to smoothen the substrate surface, remove any remaining material residues, and improve the overall surface quality and planarity.
- Inspection and Testing: The fabricated APS substrate undergoes rigorous inspection and testing to ensure quality and compliance with design specifications. This may include visual inspection, electrical testing, and other quality control measures to identify and rectify any defects or deviations from the desired characteristics.
- Packaging Integration: Once the APS substrate is fabricated and tested, it is integrated into the semiconductor packaging process. This may involve attaching semiconductor chips, wire bonding or flip-chip bonding, encapsulation, and other assembly steps to complete the electronic package.
- Final Testing and Quality Assurance: The assembled electronic packages undergo final testing and quality assurance procedures to verify functionality, performance, and reliability before being shipped to customers.
By following these fabrication steps, manufacturers can produce APS substrates with the desired electrical, thermal, and mechanical properties to meet the demanding requirements of semiconductor packaging applications.
How do you manufacture Ajinomoto Package Substrate (APS)?
The manufacturing process of Ajinomoto Package Substrate (APS) involves several steps to create the specialized material used in semiconductor packaging. Here is an overview of the typical manufacturing process:
- Substrate Preparation: The process begins with the preparation of the substrate material, which is often fiberglass-reinforced epoxy resin (FR-4) or polyimide. The substrate material is cut into sheets of appropriate size and thickness to serve as the base for the APS.
- Surface Treatment: The substrate material undergoes surface treatment to enhance adhesion and promote bonding with the subsequent layers. This may involve processes such as cleaning, roughening, or applying a thin layer of adhesive primer.
- Lamination: In the lamination process, multiple layers of thin films are laminated onto the prepared substrate material. These thin films typically consist of copper foil, dielectric materials, and adhesive layers. The lamination process may involve heat and pressure to bond the layers together and form a composite structure.
- Circuit Patterning: After lamination, the composite material undergoes circuit patterning to define the conductive traces and features required for interconnecting electronic components. This is typically done using photolithography techniques, where a photoresist layer is applied to the surface, exposed to UV light through a mask, and developed to transfer the desired circuit pattern onto the substrate material.
- Etching: The exposed areas of the substrate material are then etched away using chemical processes, leaving behind the desired conductive traces and features. This step removes the copper foil from the substrate surface, creating the circuit pattern defined during the patterning process.
- Surface Finishing: Following etching, the substrate material may undergo surface finishing processes to improve solderability and protect against oxidation. Common surface finishes include electroless nickel immersion gold (ENIG), immersion silver, and organic surface protectants.
- Quality Control: Throughout the manufacturing process, quality control measures are implemented to ensure the consistency, reliability, and performance of the APS material. This may include inspections, testing, and validation of key parameters such as thickness, conductivity, adhesion, and surface finish.
- Final Inspection and Packaging: Once the manufacturing process is complete, the APS material undergoes final inspection to verify compliance with specifications and quality standards. The material is then packaged and prepared for distribution to semiconductor packaging facilities, where it will be used in the assembly of electronic devices
How much should an Ajinomoto Package Substrate (APS) cost?
Determining the exact cost of an Ajinomoto Package Substrate (APS) can be complex and depends on various factors including the size, complexity, materials used, manufacturing process, volume discounts, and market conditions. However, I can provide some insights into the factors that influence the cost of APS substrates:
- Material Costs: The cost of raw materials used in the fabrication of APS substrates, including base substrates, conductive metals, dielectric materials, and other specialized components, significantly impacts the overall cost. Prices for these materials can vary based on factors such as purity, availability, and market demand.
- Manufacturing Process:The fabrication process for APS substrates involves several steps including layer deposition, photolithography, etching, surface finishing, and testing. The complexity and sophistication of these manufacturing processes can affect production costs. Advanced techniques or specialized equipment may incur higher operational expenses, contributing to the overall cost of APS substrates.
- Research and Development: Costs associated with research and development (R&D) efforts to develop and optimize APS technology, improve manufacturing processes, and enhance product performance also factor into the overall cost. These expenses are typically amortized across the production volume of APS substrates.
- Quality Control and Testing: Rigorous quality control and testing procedures are essential to ensure the reliability and performance of APS substrates. The investment in quality assurance measures, including inspection, testing, and compliance with industry standards, adds to the manufacturing costs.
- Volume Discounts and Economies of Scale: Larger production volumes often enable manufacturers to negotiate favorable pricing for raw materials, equipment, and production facilities. Economies of scale can drive down the unit cost of APS substrates, making them more cost-effective for high-volume applications.
- Market Dynamics: Market conditions, including supply and demand dynamics, competition, and pricing strategies of manufacturers, influence the overall cost of APS substrates. Fluctuations in material prices, currency exchange rates, and geopolitical factors can also impact pricing.
- Value-added Services: Additional services such as customization, packaging, logistics, and technical support may incur extra costs but provide added value to customers. The inclusion of value-added services can affect the final price of APS substrates.
- Profit Margin: Manufacturers factor in profit margins to cover operating expenses, R&D investments, and generate returns for shareholders. Profit margin considerations influence the pricing strategy for APS substrates.
In summary, the cost of an Ajinomoto Package Substrate (APS) can vary widely depending on factors such as material costs, manufacturing processes, quality control measures, volume discounts, market dynamics, and value-added services. Pricing is typically determined based on a combination of these factors to ensure competitiveness while maintaining profitability for the manufacturer.
What is Ajinomoto Package Substrate (APS) base material?
The Ajinomoto Package Substrate (APS) base material is a specialized material used in the manufacturing of semiconductor packages. APS is a type of organic substrate material that serves as the foundation for mounting and interconnecting electronic components within semiconductor packages. It is a crucial component in the assembly of integrated circuits (ICs) and other electronic devices.
APS base material is engineered to meet stringent requirements for electrical performance, thermal management, and reliability in semiconductor packaging applications. It typically consists of multiple layers of thin films deposited onto a substrate material, such as fiberglass-reinforced epoxy resin (FR-4) or polyimide.
One of the key characteristics of APS base material is its high thermal conductivity, which helps dissipate heat generated by the electronic components during operation. This is essential for maintaining the performance and reliability of semiconductor devices, particularly in high-power and high-frequency applications.
Additionally, APS base material offers excellent electrical properties, including low dielectric constant and low loss tangent, which minimize signal distortion and ensure reliable signal transmission within the package. This is critical for maintaining signal integrity and achieving high-speed data transfer in modern electronic devices.
Furthermore, APS base material provides mechanical stability and robustness to semiconductor packages, ensuring that they can withstand the stresses of assembly, handling, and operation. This helps prevent damage to the electronic components and extends the service life of the devices.
Overall, the Ajinomoto Package Substrate (APS) base material plays a vital role in the development of advanced semiconductor packages, enabling the creation of compact, efficient, and reliable electronic devices for a wide range of applications, including smartphones, tablets, computers, automotive electronics, and industrial equipment.
Which company manufactures Ajinomoto Package Substrate (APS)?
Ajinomoto Package Substrate (APS) is manufactured by Ajinomoto Fine-Techno Co., Inc., a subsidiary of Japan’s Ajinomoto Group. Our company has the capability to produce similar advanced packaging substrates and can customize them according to customers’ specific needs. We have advanced technology and equipment, a professional R&D team and rich experience to meet the needs of various application fields.
As a company that manufactures APS products, we are committed to providing high-performance, high-reliability packaging substrates to provide critical support for customers’ electronic devices. Our production process strictly follows quality control standards to ensure that each product meets the highest standards. We continuously optimize our production processes to improve efficiency and reduce costs to provide customers with competitive prices.
In addition to producing APS products, we also provide various value-added services related to packaging substrates, including customized design, technical support, after-sales service, etc. We work closely with our customers, listen to their needs, and provide them with a full range of solutions and support to help them achieve product innovation and market competitiveness.
In short, our company has the ability to produce similar products and is committed to providing customers with satisfactory solutions through advanced technology, high-quality products and services.
What are the 7 qualities of good customer service?
Effective customer service is characterized by several key qualities that contribute to positive interactions and customer satisfaction. Here are seven qualities of good customer service:
- Empathy: Good customer service involves understanding and empathizing with the customer’s needs, concerns, and emotions. Empathetic interactions demonstrate that the service provider cares about the customer’s experience and is committed to finding solutions that address their specific situation.
- Communication Skills: Clear and effective communication is essential for conveying information, listening to customer inquiries or complaints, and providing assistance. Service representatives should communicate in a professional, courteous, and easily understandable manner, whether through verbal or written communication channels.
- Responsiveness: Customers appreciate prompt responses and timely assistance when they reach out for support or assistance. Good customer service involves being proactive and responsive to customer inquiries, requests, and feedback, ensuring that issues are addressed promptly and efficiently.
- Product Knowledge: Service representatives should have a deep understanding of the products or services offered by the company. This includes knowledge of product features, specifications, benefits, and troubleshooting procedures. A thorough understanding of the offerings enables service providers to offer accurate information and effective solutions to customers.
- Problem-Solving Skills: Effective problem-solving skills are essential for resolving customer issues and addressing challenges that may arise. Service representatives should be resourceful, analytical, and creative in finding solutions to customer problems, whether it involves troubleshooting technical issues, resolving billing disputes, or accommodating special requests.
- Professionalism: Good customer service is characterized by professionalism in all interactions with customers. Service representatives should maintain a positive attitude, remain calm and composed, and adhere to company policies and standards of conduct. Professionalism builds trust and confidence in the service provider and reflects positively on the company’s reputation.
- Follow-Up and Feedback: Following up with customers after resolving an issue or completing a service request demonstrates commitment to customer satisfaction and ensures that the customer’s needs have been fully addressed. Additionally, soliciting feedback from customers about their experience provides valuable insights for improving service quality and identifying areas for enhancement.
By embodying these qualities, companies can deliver exceptional customer service experiences that foster customer loyalty, retention, and advocacy.
FAQs
What is Ajinomoto Package Substrate (APS)?
Ajinomoto Package Substrate (APS) is a specialized substrate material used in the semiconductor industry for the packaging of integrated circuits (ICs). It offers superior electrical performance, thermal conductivity, and reliability compared to traditional substrate materials.
What are the key features of APS?
APS is known for its excellent thermal management properties, low signal loss, and compatibility with advanced packaging techniques such as flip-chip bonding and through-silicon vias (TSVs). It enables the integration of multiple functions within a single package, leading to smaller and more efficient electronic devices.
What are the advantages of using APS?
The advantages of using APS include improved thermal performance, enhanced electrical connectivity, miniaturization of electronic devices, and increased reliability. APS technology enables the development of high-performance and compact semiconductor packages suitable for a wide range of applications.
What applications is APS suitable for?
APS is suitable for various applications in industries such as telecommunications, automotive electronics, high-performance computing, consumer electronics, and industrial automation. It is used in the packaging of ICs for power amplifiers, RF modules, microprocessors, and other high-frequency and high-power devices.
How is APS manufactured?
The manufacturing process for APS involves several steps, including substrate preparation, material deposition, lithography, etching, surface finishing, and testing. Specific details of the manufacturing process may vary depending on the manufacturer and desired substrate properties.
What are the design guidelines for APS?
APS design guidelines provide recommendations and specifications for designing electronic packages using APS technology. Key considerations include thermal management, signal integrity, power distribution, manufacturability, reliability, package size, and electromagnetic compatibility (EMC).
Where can APS substrates be sourced?
APS substrates can be sourced directly from manufacturers such as Ajinomoto Fine-Techno Co., Inc. or through authorized distributors and suppliers specializing in semiconductor packaging materials. Customers can inquire about product availability, specifications, and pricing from these sources.