Buried Cavity PCBs Manufacturer
Buried Cavity PCBs Manufacturer. we can produce the best samllest bump pitch with 100um, the best smallest trace are 9um. and the smallest gap are 9um. most of the design are 15um to 30um trace and spacing.
Buried Cavity PCBs represent a cutting-edge solution in electronic design, featuring recessed areas within the board itself to embed components or features. These specialized PCBs offer a host of advantages, including space optimization, improved thermal management, enhanced signal integrity, and reduced electromagnetic interference. By integrating components within the board’s layers, Buried Cavity PCBs enable the creation of sleeker, more compact devices without compromising functionality. They find applications in a diverse range of industries, from consumer electronics like smartphones and wearables to high-performance computing, automotive electronics, medical devices, and IoT technologies. However, their manufacturing process requires precision and expertise, involving intricate cavity milling, insulation application, and component integration. Despite the challenges, the benefits of Buried Cavity PCBs make them an increasingly popular choice for engineers seeking to push the boundaries of electronic design and innovation.
What is a Buried Cavity PCB?
A Buried Cavity PCB (Printed Circuit Board) is a specialized type of PCB design that incorporates one or more recessed areas within the board itself. These recessed areas, or cavities, are created by removing portions of the substrate material between layers of the PCB. The result is a PCB with embedded spaces or voids that can be used for various purposes.
The main advantage of a Buried Cavity PCB is its ability to integrate additional components or features into a compact space without increasing the overall size of the board. This can lead to more efficient use of space, reduced weight, and improved performance in applications where size and weight are critical factors.
Buried Cavity PCBs are commonly used in electronic devices where space is limited, such as smartphones, tablets, wearables, and other portable electronics. They can be used to house components such as sensors, batteries, antennas, or even entire subsystems, allowing for greater functionality in a smaller form factor.
In addition to space savings, Buried Cavity PCBs can also offer benefits such as improved signal integrity, reduced electromagnetic interference (EMI), and enhanced thermal management. By isolating sensitive components or high-frequency circuits within the cavities, designers can minimize signal losses and optimize performance.
Overall, Buried Cavity PCBs represent a versatile and efficient solution for compact electronic designs, offering a balance of functionality, performance, and miniaturization.
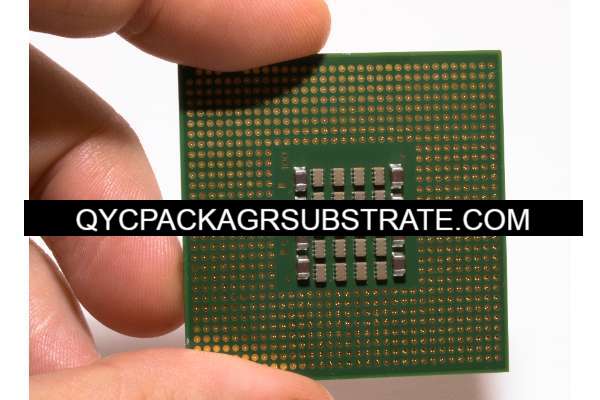
Buried Cavity PCBs Manufacturer
What are the Buried Cavity PCB Design Guidelines?
Designing a Buried Cavity PCB requires careful consideration of several factors to ensure proper functionality, manufacturability, and reliability. Here are some guidelines to follow:
- Define cavity dimensions: Determine the size, shape, and depth of the cavities based on the components or features you plan to embed within the PCB. Consider the clearance requirements for the components and any thermal considerations.
- Layer stackup design:Plan the layer stackup carefully to accommodate the cavities. Ensure that the layers surrounding the cavities provide adequate support and structural integrity to the board.
- Material selection: Choose PCB materials that offer good dimensional stability and are suitable for cavity fabrication. Discuss material options with your PCB manufacturer to ensure compatibility with the chosen fabrication process.
- Cavity placement: Position the cavities strategically within the PCB to optimize space utilization and minimize signal interference. Avoid placing cavities near high-speed signal traces or areas prone to mechanical stress.
- Cavity isolation: Electrically isolate the cavities from adjacent conductive layers to prevent short circuits. Use appropriate insulation materials or coatings to insulate the cavity walls and ensure electrical integrity.
- Signal routing: Plan signal routing around the cavities carefully to maintain signal integrity and minimize signal losses. Avoid routing high-speed or sensitive signals directly over or near the cavities to reduce the risk of electromagnetic interference.
- Thermal management:Consider the impact of cavities on thermal management and heat dissipation. Ensure sufficient airflow or thermal vias to dissipate heat from components housed within the cavities.
- Manufacturability: Work closely with your PCB manufacturer to ensure that the design can be fabricated using their capabilities and processes. Consider factors such as cavity milling, layer alignment, and material handling during fabrication.
- Testing and validation: Implement test points or access points to facilitate testing and debugging of components within the cavities. Perform thorough testing and validation to ensure the reliability and functionality of the PCB design.
- Documentation: Document the design guidelines, cavity dimensions, material specifications, and other relevant details to facilitate communication with stakeholders and ensure consistency in manufacturing.
By following these guidelines, you can create a Buried Cavity PCB design that meets your specific requirements while ensuring reliability and manufacturability. Working closely with your PCB manufacturer and considering all aspects of the design will help you achieve optimal results.
What is the Buried Cavity PCB Fabrication Process?
The fabrication process for a Buried Cavity PCB involves several specialized steps to create the recessed areas within the board and integrate components or features into these cavities. Here’s an overview of the typical fabrication process:
- Design: The process begins with the design of the PCB layout, including the placement and dimensions of the cavities. Design software is used to create the layout according to the desired specifications and requirements.
- Material selection: Choose suitable PCB materials that provide good dimensional stability and are compatible with the fabrication process. Consider factors such as substrate material, copper thickness, and insulation properties.
- Layer stackup: Plan the layer stackup to accommodate the cavities within the PCB. Determine the number of layers and the arrangement of conductive and insulating layers to provide structural support and electrical isolation for the cavities.
- Cavity milling: The cavities are created by milling or routing away portions of the substrate material between the layers of the PCB. CNC (Computer Numerical Control) machines or specialized milling equipment are used to accurately remove the material according to the design specifications.
- Insulation: After milling the cavities, insulating materials may be applied to the cavity walls to provide electrical isolation between the cavities and adjacent conductive layers. Insulation materials such as epoxies or resins are commonly used for this purpose.
- Component integration: Components or features are then integrated into the cavities according to the design requirements. This may involve placing components directly into the cavities or mounting them onto substrate material within the cavities.
- Layer bonding: Once the components are in place, the layers of the PCB are bonded together using adhesives or lamination processes. This helps to secure the components and ensure structural integrity for the finished PCB.
- Routing and etching: After bonding the layers, the PCB undergoes routing and etching processes to define the circuit traces and connections between components. Copper traces are formed on the outer layers of the PCB using chemical etching or other methods.
- Surface finishing: Surface finishes such as solder mask and surface plating are applied to the PCB to protect the circuitry and provide solderability for component attachment. This helps to ensure the reliability and functionality of the finished PCB.
- Testing and inspection: The fabricated PCB undergoes testing and inspection to verify functionality, electrical continuity, and adherence to design specifications. This may involve electrical testing, visual inspection, and other quality assurance measures.
By following these steps, manufacturers can fabricate Buried Cavity PCBs that meet the required specifications and functionality while ensuring reliability and performance. Close collaboration between designers and manufacturers is essential throughout the fabrication process to ensure successful outcomes.
How Do You Manufacture a Buried Cavity PCB?
Manufacturing a Buried Cavity PCB involves several specialized processes to create the recessed areas within the board and integrate components or features into these cavities. Here’s a detailed overview of the typical manufacturing process:
- Design Preparation: The process begins with the design of the PCB layout, including the placement, dimensions, and specifications of the cavities. Design software is used to create the layout according to the desired requirements.
- Material Selection: Choose suitable PCB materials that provide good dimensional stability and are compatible with the manufacturing process. Consider factors such as substrate material, copper thickness, and insulation properties.
- Layer Stackup Design: Plan the layer stackup to accommodate the cavities within the PCB. Determine the number of layers and the arrangement of conductive and insulating layers to provide structural support and electrical isolation for the cavities.
- Cavity Formation: The cavities are created by milling or routing away portions of the substrate material between the layers of the PCB. CNC (Computer Numerical Control) machines or specialized milling equipment are used to accurately remove the material according to the design specifications.
- Insulation Application:After milling the cavities, insulating materials may be applied to the cavity walls to provide electrical isolation between the cavities and adjacent conductive layers. Insulation materials such as epoxies or resins are commonly used for this purpose.
- Component Integration: Components or features are then integrated into the cavities according to the design requirements. This may involve placing components directly into the cavities or mounting them onto substrate material within the cavities.
- Layer Bonding: Once the components are in place, the layers of the PCB are bonded together using adhesives or lamination processes. This helps to secure the components and ensure structural integrity for the finished PCB.
- Routing and Etching: After bonding the layers, the PCB undergoes routing and etching processes to define the circuit traces and connections between components. Copper traces are formed on the outer layers of the PCB using chemical etching or other methods.
- Surface Finishing: Surface finishes such as solder mask and surface plating are applied to the PCB to protect the circuitry and provide solderability for component attachment. This helps to ensure the reliability and functionality of the finished PCB.
- Testing and Inspection: The fabricated PCB undergoes testing and inspection to verify functionality, electrical continuity, and adherence to design specifications. This may involve electrical testing, visual inspection, and other quality assurance measures.
By following these steps, manufacturers can successfully produce Buried Cavity PCBs that meet the required specifications and functionality while ensuring reliability and performance. Close collaboration between designers and manufacturers is essential throughout the manufacturing process to ensure successful outcomes.
How Much Should a Buried Cavity PCB Cost?
The cost of manufacturing a Buried Cavity PCB can vary widely depending on several factors:
- Complexity of design: The complexity of the PCB design, including the number and size of cavities, the number of layers, and the placement of components, can significantly impact the cost. More complex designs may require specialized equipment and additional processing steps, increasing manufacturing costs.
- Materials: The choice of materials, including substrate material, copper thickness, and insulation materials, can affect the overall cost of the PCB. High-quality materials may come at a higher price but can contribute to better performance and reliability.
- Manufacturing process: The specific manufacturing processes required to create the cavities, integrate components, and assemble the PCB can influence the cost. Processes such as milling, bonding, routing, and inspection may incur additional expenses.
- Volume: The volume of PCBs being produced can also affect the cost per unit. Larger production volumes typically benefit from economies of scale, leading to lower unit costs. Conversely, smaller production runs may incur higher costs per unit.
- Supplier and location: The choice of PCB manufacturer and their location can impact pricing due to differences in labor costs, overhead expenses, and manufacturing capabilities. Additionally, choosing a reputable supplier with a track record of quality and reliability may result in higher costs but can offer peace of mind and better long-term value.
- Additional services: Additional services such as testing, quality assurance, and certification may add to the overall cost of manufacturing the PCB but can be essential for ensuring reliability and compliance with industry standards.
Overall, it’s challenging to provide a precise cost estimate for a Buried Cavity PCB without specific details about the design, materials, manufacturing processes, and volume requirements. It’s advisable to consult with multiple PCB manufacturers to obtain quotes and evaluate the best options based on your project’s requirements and budget constraints.
What is Buried Cavity PCB Base Material?
The choice of base material for a Buried Cavity PCB depends on various factors including performance requirements, thermal considerations, and manufacturing capabilities. Common base materials used for Buried Cavity PCBs include:
- FR-4 (Flame Retardant 4): FR-4 is a widely used standard material for PCBs due to its affordability, good electrical properties, and availability. It consists of a woven fiberglass cloth impregnated with epoxy resin. FR-4 is suitable for many applications but may have limitations in high-frequency or high-temperature environments.
- High-Tg FR-4: High-Tg (glass transition temperature) FR-4 offers improved thermal stability compared to standard FR-4. It can withstand higher temperatures without losing its mechanical and electrical properties, making it suitable for applications with elevated operating temperatures or thermal cycling.
- Rogers Materials: Rogers Corporation manufactures a range of high-performance laminates specifically designed for demanding applications such as high-frequency circuits, RF/microwave applications, and high-speed digital designs. These materials offer excellent electrical performance, low loss, and stable dielectric properties.
- Polyimide: Polyimide materials, such as Kapton, offer exceptional thermal stability, flexibility, and resistance to harsh environments. They are often used in applications requiring flexibility or resistance to high temperatures, such as aerospace, automotive, and medical devices.
- Teflon (PTFE): Teflon-based materials offer low dielectric loss, high thermal stability, and excellent performance at high frequencies. They are commonly used in RF/microwave applications where signal integrity and low loss are critical.
- Metal Core: Metal core materials, such as aluminum or copper-backed laminates, provide enhanced thermal conductivity compared to standard PCB substrates. They are used in applications requiring efficient heat dissipation, such as LED lighting, power electronics, and automotive applications.
The selection of base material for a Buried Cavity PCB should consider factors such as electrical performance, thermal management, mechanical properties, and cost.
Which Company Makes Buried Cavity PCBs?
Many companies can manufacture Buried Cavity PCBs, especially specialized PCB manufacturers and electronic equipment manufacturers. Some well-known PCB manufacturers include Foxconn, JLCPCB, OFILM, Goertek, and Andalay. These companies have advanced production equipment, rich experience, and professional teams to meet various PCB design needs, including Buried Cavity PCBs.
At our company, we also produce Buried Cavity PCBs, providing customized solutions for our customers. We have advanced production equipment and technology to achieve precise cavity manufacturing and high-quality PCB production. Our team consists of experienced engineers and technicians who can provide comprehensive technical support and consulting services to help customers achieve their design and performance goals.
Our Buried Cavity PCB manufacturing process includes the following key steps:
- Design Preparation:We work closely with customers to understand their design requirements and specifications, developing suitable PCB design solutions.
- Material Selection: We choose high-quality PCB materials to ensure they meet the performance and reliability requirements of our customers.
- Production Manufacturing: We use advanced production equipment and processes to accurately manufacture cavities and integrate components into the PCB.
- Quality Control: We strictly implement a quality management system to monitor and inspect the production process, ensuring product quality meets customer expectations.
- Testing and Validation: We conduct comprehensive testing and validation to ensure the produced Buried Cavity PCBs meet design specifications and function properly.
Through our professional team and advanced technology, we can provide customers with high-quality, reliable, and high-performance Buried Cavity PCBs to meet their various application needs. We are committed to providing customers with the best solutions and establishing long-term stable partnerships.
What are the 7 Qualities of Good Customer Service?
Good customer service is characterized by several key qualities that contribute to a positive experience for customers. Here are seven qualities of good customer service:
- Responsiveness: Good customer service is responsive to customers’ needs and inquiries in a timely manner. This includes promptly answering phone calls, emails, and messages, as well as addressing customer concerns or issues promptly.
- Empathy: Empathy involves understanding and relating to customers’ feelings, concerns, and perspectives. Good customer service representatives listen attentively, show empathy towards customers’ situations, and strive to understand their needs.
- Clarity: Clear communication is essential for good customer service. Customer service representatives should communicate information clearly and effectively, using simple language and avoiding jargon or technical terms that customers may not understand.
- Professionalism: Professionalism involves maintaining a courteous, respectful, and helpful demeanor when interacting with customers. Good customer service representatives are polite, patient, and maintain a positive attitude, even in challenging situations.
- Problem-solving skills: Good customer service involves effectively resolving customers’ issues, concerns, or complaints. Customer service representatives should possess strong problem-solving skills, be proactive in finding solutions, and take ownership of issues until they are resolved satisfactorily.
- Consistency: Consistency is key to good customer service. Customers expect consistent experiences across all interactions with a company, whether it’s in-store, online, or over the phone. Good customer service ensures that policies, procedures, and service standards are consistently applied to all customers.
- Follow-up: Following up with customers after their interaction is an important aspect of good customer service. This can involve checking in to ensure that the issue was resolved satisfactorily, seeking feedback on the customer’s experience, or providing additional assistance if needed.
By embodying these qualities, companies can provide exceptional customer service that fosters customer satisfaction, loyalty, and positive word-of-mouth recommendations.
FAQs
What is a Buried Cavity PCB?
A Buried Cavity PCB is a type of printed circuit board that features recessed areas within the board itself, often used to embed components or features into the PCB.
What are the benefits of using Buried Cavity PCBs?
Buried Cavity PCBs offer advantages such as space savings, improved thermal management, enhanced signal integrity, reduced electromagnetic interference, and the ability to integrate additional components or features into a compact space.
What types of applications are Buried Cavity PCBs suitable for?
Buried Cavity PCBs are suitable for a wide range of applications where space is limited, such as smartphones, tablets, wearables, medical devices, automotive electronics, and IoT (Internet of Things) devices.
How are Buried Cavity PCBs manufactured?
The manufacturing process for Buried Cavity PCBs involves creating recessed areas within the board, integrating components or features into these cavities, and bonding the layers of the PCB together. Specialized processes such as cavity milling, insulation application, and component integration are used.
What materials are used in Buried Cavity PCBs?
Common materials used in Buried Cavity PCBs include FR-4 (Flame Retardant 4), high-Tg FR-4, Rogers materials, polyimide, Teflon (PTFE), and metal core materials. The choice of material depends on factors such as performance requirements, thermal considerations, and manufacturing capabilities.
What design considerations should be taken into account for Buried Cavity PCBs?
Design considerations for Buried Cavity PCBs include cavity dimensions, layer stackup design, material selection, cavity placement, cavity isolation, signal routing, thermal management, manufacturability, testing, and validation.
Are there any limitations or challenges associated with Buried Cavity PCBs?
While Buried Cavity PCBs offer many benefits, they can also present challenges such as increased manufacturing complexity, higher production costs, and potential reliability issues if not designed and manufactured properly. Additionally, the integration of components into cavities may require careful consideration of clearance and thermal management.