Cavity PCB/Substrate Manufacturer and package substrate manufacturer. We use advanced Msap and Sap technology, High multilayer interconnection substrates from 4 to 20 layers,
Enter the realm of Cavity PCBs (Printed Circuit Boards) or Substrates – a sophisticated circuit board that artfully incorporates recessed areas within its architecture. These deliberately crafted recesses serve as bespoke spaces for seamlessly embedding electronic components, ushering in a paradigm shift in electronic device solutions.
Unveiling the distinctive traits of Cavity PCBs:
Harmonious Component Integration: Cavity PCBs provide a canvas for the direct integration of a diverse spectrum of electronic components, doing away with the need for superfluous spatial accommodations.
Elegant Design and Weight Optimization: Through the strategic incorporation of recessed areas, Cavity PCBs attain a design finesse, proving particularly advantageous in applications where strict size and weight considerations take center stage.
Fine-Tuned Thermal Dynamics: Meticulously positioned recesses in Cavity PCBs contribute to an elevated thermal performance, orchestrating the efficient dissipation of heat.
Pertinence in RF/Microwave Designs: Cavity PCBs carve a niche in designs entailing radio frequency (RF) and microwave technologies, demanding a meticulous dance of control over signal paths and components.
Trailblazing Packaging Solutions: Embraced in avant-garde packaging solutions for electronic devices, Cavity PCBs play a pivotal role in sectors ranging from aerospace to telecommunications and high-performance computing.
It’s imperative to acknowledge that the bespoke design and application of Cavity PCBs align seamlessly with the idiosyncratic demands of the electronic systems they aim to empower.
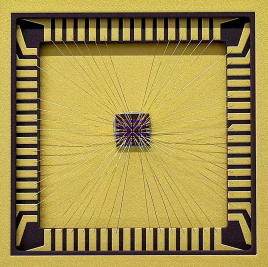
What Functions Does Cavity PCB/Substrate Serve?
Within the realm of electronic systems, Cavity PCBs or Substrates serve as multifaceted contributors, elevating the efficiency and functionality of the overall design. Here’s an exploration of the pivotal functions performed by Cavity PCBs:
Seamless Component Fusion: Cavity PCBs excel in the seamless integration of electronic components, intricately nestled within purposefully designed recessed areas, streamlining the architectural cohesiveness of the system.
Space Optimization Mastery: By skillfully incorporating recessed regions, Cavity PCBs demonstrate prowess in optimizing spatial utilization, a boon for applications where spatial constraints demand ingenuity.
Weight Elegance: The refined design philosophy inherent in Cavity PCBs translates to an elegant reduction in overall weight, presenting a compelling choice for applications where weight considerations hold sway.
Thermal Symphony: The strategic inclusion of recessed zones orchestrates a symphony of superior thermal management, providing additional canvases for the graceful dissipation of heat—an imperative in systems where heat is a performance factor.
Signal Choreography: Especially in the intricate dance of RF and microwave applications, Cavity PCBs take the lead in offering meticulous control over signal paths and components, ensuring a flawless choreography of signal integrity and minimal interference.
Frontiers of Packaging Innovation: Cavity PCBs emerge as pioneers in the avant-garde landscape of packaging solutions for electronic devices, carving a niche in industries spanning aerospace, telecommunications, and high-performance computing.
Bespoke Customization Canvas: The inherent design flexibility of Cavity PCBs transforms them into a canvas for bespoke customization, aligning seamlessly with the unique demands of diverse electronic systems.
Mastering Electromagnetic Harmony: Cavity PCBs contribute to the orchestration of electromagnetic harmony, mitigating interference and shielding electronic components from the whims of external electromagnetic fields.
Guardians of Components: The recessed havens within Cavity PCBs serve as protective guardians, shielding embedded components from the elements and potential physical perils.
Performance Sonata: Collectively, the nuanced functionalities of Cavity PCBs compose a sonata of enhanced performance in electronic systems, addressing challenges with finesse, from spatial optimization to heat dissipation and signal integrity.
In essence, Cavity PCBs stand as virtuosos, offering a harmonious blend of compact design, weight finesse, and orchestrated functionality across diverse electronic landscapes.
What are the Different Types of Cavity PCB/Substrate?
Diverse applications demand various types of Cavity PCBs or substrates, each tailored to meet specific needs and complexities. Here’s an exploration of the different variants:
Solo Symphony – Single-Layer Cavity PCBs: Simplifying the landscape, these boards feature a single layer with thoughtfully placed cavities, making them ideal for straightforward electronic designs.
Duo Dynamics – Double-Layer Cavity PCBs: Elevating the complexity, these boards boast layers on both sides, providing additional space for component integration. They find their niche in applications of moderate intricacy.
Multilayer Marvels – Multilayer Cavity PCBs: Unleashing the potential of depth, these boards come with multiple layers housing cavities, a perfect fit for intricate electronic systems demanding flexibility and superior signal integrity.
Metallic Harmony – Metal Core Cavity PCBs: Fusing substance with style, these boards incorporate a metal core, enhancing thermal conductivity for applications requiring efficient heat dissipation.
Flexible Innovations – Flex Cavity PCBs: Bending the rules, these boards, crafted from flexible materials, provide the flexibility needed for dynamic applications or tight spaces.
Microwave Maestros – RF/Microwave Cavity PCBs: Taking center stage in communication systems, these boards ensure precision in signal paths and minimize interference, catering to the intricate demands of radio frequency and microwave applications.
Hybrid Wonders – Hybrid Cavity PCBs: Merging materials and technologies, these boards are chameleons, adapting to various applications with customized strengths and features.
High-Frequency Virtuosos – High-Frequency Cavity PCBs: Operating in the fast lane, these boards are designed for high-frequency applications, ensuring minimal signal loss and optimal signal integrity.
Bending Boundaries – Rigid-Flex Cavity PCBs: Blending the best of both worlds, these boards seamlessly integrate rigid and flexible portions, offering structural stability with a touch of flexibility.
Hidden Marvels – Buried Cavity PCBs: Concealing complexity beneath the surface, these boards place cavities between inner layers, delivering a clean and compact design solution.
The selection of a Cavity PCB type becomes an art, where intricacies, thermal demands, flexibility, and frequency considerations dance in harmony with the specific needs of the electronic system at hand.
How Does Cavity PCB/Substrate Relate to IC Packaging?
The synergy between Cavity PCBs or substrates and IC (Integrated Circuit) packaging is a pivotal relationship that significantly influences the performance and design of electronic devices. This connection can be explored through the following perspectives:
Seamless IC Integration: Cavity PCBs serve as a seamless canvas for the integration of ICs directly onto the board. The carefully designed cavities offer a purposeful space for ICs, contributing to a more consolidated and streamlined solution.
Architectural Considerations: IC packaging involves encapsulating integrated circuits for protection against environmental elements and mechanical stress. Cavity PCBs play a crucial role in this process by providing designated spaces, ensuring meticulous placement and safeguarding.
Thermal Harmony: Optimal thermal management is paramount for the efficient operation of ICs. Cavity PCBs, featuring recessed areas, facilitate enhanced heat dissipation, thereby enriching the overall thermal performance of the integrated circuits.
Signal Integrity Ballet: The layout and composition of Cavity PCBs are artfully designed to preserve signal integrity. This is particularly significant in IC packaging, where maintaining precise control over signal paths is indispensable to prevent signal degradation or interference.
Cutting-Edge Packaging Solutions: Cavity PCBs often take center stage in avant-garde packaging solutions for ICs, offering a sophisticated and tailored approach to address the specific demands and characteristics of integrated circuits.
Tailored Customization: Cavity PCBs can be intricately customized to align with the unique requirements of different ICs. This customization spans the dimensions and shapes of cavities, the number of layers, and the choice of materials, ensuring a harmonious fit with the characteristics of integrated circuits.
Hybrid Integration Symphony: Cavity PCBs facilitate a symphony of hybrid integration, allowing for the harmonious combination of diverse technologies and components on a single board. This proves particularly relevant in the modern landscape of IC packaging, where multifaceted functionalities converge into a unified package.
Radiant Application in RF/Microwave ICs: Cavity PCBs find a radiant application in the packaging of RF and microwave ICs. Here, the meticulous control over signal paths and thermal considerations becomes a linchpin for the optimal performance of these specialized integrated circuits.
In essence, the interplay between Cavity PCBs and IC packaging unfolds as a dynamic and purposeful collaboration, shaping the landscape of electronic design with an emphasis on consolidation, protection, and performance optimization.
How Does Cavity PCB/Substrate Differ from Traditional PCBs?
Diverging from the conventional path of traditional PCBs, Cavity PCBs or substrates present a distinctive approach in their design and functionality. The differences unfold across various dimensions:
Intricate Recessed Design:
Cavity PCBs: Embrace a design adorned with strategically crafted recessed areas or cavities. These intentional pockets within the board structure serve as purposeful sanctuaries for seamlessly integrating electronic components.
Traditional PCBs: Follow a more conventional route with a flat and uniform surface, where components are conventionally mounted on the board’s exterior.
Embedded Component Integration:
Cavity PCBs: Showcase the art of direct component integration within the cavities, forging a path toward a more compact and integrated solution. Components become integral parts of the board’s structure rather than surface adornments.
Traditional PCBs: Adhere to the standard practice of mounting components on the surface, employing soldering or other attachment methods.
Dimensional Elegance:
Cavity PCBs: Redefine dimensions with their recessed design, allowing for a more compact layout. This not only optimizes space but may also contribute to a reduction in overall weight.
Traditional PCBs: Adhere to a flat design paradigm, where the size and weight are influenced by the surface-mounted components.
Thermal Symphony:
Cavity PCBs: Feature a thermal symphony orchestrated by the recessed areas, enhancing heat dissipation through additional surface area. This design proves advantageous in applications where managing heat is a critical concern.
Traditional PCBs: Rely on external cooling methods such as heat sinks or fans to manage heat dissipation.
Application Artistry:
Cavity PCBs: Find their stage in applications where spatial optimization, intricate designs, and direct component integration take center stage. These boards shine in advanced packaging solutions, RF/microwave designs, and high-performance computing scenarios.
Traditional PCBs: Embrace a broader spectrum of applications, serving as the foundation for electronic devices with a standard form factor and where space constraints are less stringent.
Complexity and Tailoring:
Cavity PCBs: Tend to be more bespoke, with designs that may delve into complexity, especially in specialized domains like RF/microwave or high-frequency applications. The emphasis on customization is pronounced.
Traditional PCBs: Showcase versatility and can be standardized for mass production, catering to a wide array of applications with less emphasis on intricate designs.
Versatile Integration Canvas:
Cavity PCBs: Act as a versatile canvas for accommodating diverse electronic components within the recessed areas. This flexibility allows for tailored solutions, aligned with specific requirements.
Traditional PCBs: Offer versatility in their own right, catering to a range of electronic applications with standard component mounting practices.
In essence, the divergence between Cavity PCBs and traditional PCBs lies in their design philosophy, integration methodology, and the nuanced applications they elegantly cater to, each carving its own narrative in the landscape of electronic design
What are the Main Structures and Manufacturing Technologies of Cavity PCB/Substrate?
Navigating the landscape of electronic design, Cavity PCBs or substrates unfold a diverse array of structures and manufacturing technologies, each tailored to carve a niche in the intricate realm of electronic applications. Here’s a glimpse into the various structures and manufacturing techniques associated with these innovative boards:
Solo Sonata – Single-Layer Cavity PCBs:
Structure: Orchestrated with a single layer, featuring artfully designed recessed areas to house electronic components.
Manufacturing Technology: Dances through standard PCB fabrication processes, adorned with additional steps to carve out the elegantly recessed cavities.
Duet Dynamics – Double-Layer Cavity PCBs:
Structure: Engages in a harmonious duet with two layers, inviting cavities on both sides to create an extended space for component placement.
Manufacturing Technology: Involves a layer-by-layer choreography during fabrication, where precision drilling and plating take center stage to craft dual-sided cavities.
Multilayer Symphony – Multilayer Cavity PCBs:
Structure: Conducts a symphony with multiple layers, distributing cavities across the board, offering a versatile canvas for intricate component integration.
Manufacturing Technology: Unfolds a complex layer stacking performance, weaving together different layers with specialized techniques for crafting cavities at various depths.
Metallic Crescendo – Metal Core Cavity PCBs:
Structure: Takes center stage with a metal core, elevating thermal conductivity, and integrating cavities seamlessly into the metallic ensemble.
Manufacturing Technology: Weaves traditional PCB processes with the inclusion of a metal core layer, often choreographed using metal-backed laminates.
Flex Harmony – Flex Cavity PCBs:
Structure: Expresses flexibility through the use of bendable materials, incorporating cavities within the flexible substrate.
Manufacturing Technology: Involves a flexible PCB performance, where laser cutting or routing takes the lead to carve out cavities in the flexible composition.
RF/Microwave Crescendo – RF/Microwave Cavity PCBs:
Structure: Tailored for the grandeur of RF and microwave applications, where precise signal paths and cavities for RF components take the spotlight.
Manufacturing Technology: Showcases specialized processes like controlled impedance routing, precision drilling, and plating to hit the right notes for RF/microwave circuit requirements.
Hybrid Ensemble – Hybrid Cavity PCBs:
Structure: Becomes a versatile ensemble, harmonizing different materials and technologies into a singular board.
Manufacturing Technology: Requires a virtuoso performance in combining multiple manufacturing processes, seamlessly blending traditional FR-4 with specialized materials or layering different structures.
High-Frequency Overture – High-Frequency Cavity PCBs:
Structure: Composed for high-frequency applications, ensuring a resonance of minimal signal loss and optimal signal integrity.
Manufacturing Technology: Unveils a score enriched with advanced materials, controlled impedance processes, and precision techniques to maintain high-frequency performance.
Rigid-Flex Ballet – Rigid-Flex Cavity PCBs:
Structure: Unites the elegance of both rigid and flexible portions, offering a balletic fusion of structural stability and flexibility.
Manufacturing Technology: Demands a seamless performance in both rigid and flexible PCB processes, creating a composition that gracefully transitions between the two.
Buried Elegance – Buried Cavity PCBs:
Structure: Features cavities tucked away between inner layers, presenting a concealed elegance for component placement.
Manufacturing Technology: Involves a delicate layer stacking dance, where drilling and plating perform a refined act to create hidden cavities within the inner layers.
In essence, the structures and manufacturing technologies of Cavity PCBs unfold as a rich symphony, each type playing its unique melody in the grand performance of electronic design.
FAQs – Frequently Asked Questions
What Defines a Cavity PCB or Substrate?
Cavity PCBs, or substrates, stand out for incorporating recessed areas within their structure. These cavities are purposefully crafted to host electronic components, allowing for direct integration into the board.
How Do Cavity PCBs Differ from Traditional PCBs?
The distinction lies in design; Cavity PCBs feature recessed areas for component integration, offering a more compact and integrated solution compared to the standard flat surface of traditional PCBs.
In Which Applications Are Cavity PCBs Applicable?
Cavity PCBs find their place in diverse industries, from advanced packaging solutions to RF/microwave designs and high-performance computing. They excel in applications where space optimization and direct component integration are paramount.
What Materials Are Employed in Cavity PCB Manufacturing?
Materials vary based on application requirements. Common choices include FR-4 for standard use, metal core for enhanced thermal conductivity, and flexible materials for applications demanding flexibility.
How Are Cavities Crafted in Cavity PCBs?
Precision techniques like drilling, milling, or routing are employed during the PCB fabrication process to create cavities. The technique chosen depends on the design and material specifications.
Why is Thermal Management Crucial in Cavity PCBs?
Thermal management is vital, especially in metal core Cavity PCBs, as it aids efficient heat dissipation. The recessed areas and thermally conductive materials contribute to maintaining optimal component performance.
Can Cavity PCBs Be Customized?
Absolutely. Cavity PCBs offer customization options, allowing manufacturers to tailor designs to specific needs, including cavity size and shape, layer count, and material choices for bespoke solutions.
How Does Cavity PCB Manufacturing Preserve Signal Integrity?
Signal integrity is safeguarded through meticulous design and manufacturing processes. Controlled impedance routing, precise drilling, and the use of quality materials play pivotal roles in maintaining signal integrity.
Conclusion
In summary, the journey through the realm of Cavity PCBs or substrates reveals a fascinating narrative of innovation in electronic design. These boards, distinguished by their recessed structures, redefine the landscape with a more integrated and space-efficient approach compared to conventional PCBs. The diverse array of Cavity PCB structures, spanning from single-layer simplicity to intricate hybrid configurations, caters to the distinct needs of industries such as advanced packaging, RF/microwave, and high-performance computing.
The manufacturing saga of Cavity PCBs unfolds with precision techniques like drilling, milling, and routing, harmonizing with an array of materials, including the versatile FR-4, thermally conductive metal cores, and flexible substrates. Thermal management emerges as a pivotal act, particularly in metal core Cavity PCBs, enhancing heat dissipation and orchestrating optimal performance.
The narrative embraces customization as a key theme, allowing manufacturers to compose bespoke designs tailored to specific requirements, encompassing cavity dimensions, shapes, and material preferences. Signal integrity becomes the crescendo, with careful design considerations, controlled impedance routing, and the embrace of high-quality materials to safeguard the harmonious flow of electronic signals.
Selecting a Cavity PCB manufacturer becomes a nuanced decision, with a spotlight on expertise, customization capabilities, commitment to quality standards, and the capacity to meet diverse application needs.
In essence, the symphony of Cavity PCBs echoes through the corridors of electronic innovation, each type and manufacturing technique contributing its distinct melody to the evolving composition of technology. As these boards continue to carve their niche, their adaptability and personalized touch position them as indispensable players in the ever-evolving dance of electronic progress.