Cavity substrate manufacturing
Cavity PCB and Cavity Substrate Manufacturing. Embedded cavity PCB made with FR4, High frequency and high speed materials, or other kinds of materials. and one units PCB boards can open one cavity or multiple Cavity.
Low CET PCB is a type of Printed Circuit Board (PCB) with a low Coefficient of Thermal Expansion (CET). It exhibits excellent thermal stability and dimensional stability, making it suitable for applications in high-temperature environments and thermal cycling conditions. Low CET PCBs use special materials and processes to reduce the PCB’s expansion rate during temperature changes, minimizing stress and mismatch issues caused by thermal expansion. This makes it widely used in fields requiring high performance and reliability, such as aerospace, automotive electronics, and industrial control.
What is a Cavity Substrate?
Cavity substrate manufacturing.High speed and high frequency material packaging substrate manufacturing. Advanced packaging substrate production process and technology.
A cavity substrate typically refers to a component used in microelectronics or photonics applications, particularly in the construction of lasers, optical modulators, or other devices where precise control of light propagation is important.
In these applications, a cavity substrate is a material structure designed to support and confine electromagnetic waves within a defined volume or cavity. This confinement is typically achieved by creating a structure with specific optical properties, such as a high refractive index contrast between different layers or regions within the substrate.
Cavity substrates can be made from various materials, including semiconductors, dielectrics, or optical crystals, depending on the requirements of the application. They are often engineered with precise dimensions and properties to enable the desired performance of the device in which they are used.
What are Cavity Substrate Design Guidelines?
Cavity substrate design guidelines provide recommendations and principles for designing structures that support and confine electromagnetic waves within a defined cavity or volume. These guidelines are crucial in various fields such as microelectronics, photonics, and optics, where precise control of light propagation is essential. Some common cavity substrate design guidelines include:
- Material Selection: Choose materials with appropriate optical properties such as refractive index, absorption coefficient, and dispersion characteristics. The material should also have good mechanical and thermal stability.
- Refractive Index Contrast: Utilize materials with a high refractive index contrast between different layers or regions within the substrate to enable efficient light confinement and waveguiding.
- Geometry and Dimensions: Design the cavity substrate with precise dimensions and geometry to achieve desired optical modes and resonant frequencies. This includes the thickness and shape of layers, as well as the size and shape of the cavity.
- Losses Reduction: Minimize optical losses within the substrate by optimizing material selection, surface roughness, and interface quality between different layers.
- Mode Matching: Ensure proper mode matching between the cavity substrate and other components in the device to maximize coupling efficiency and performance.
- Thermal Management: Incorporate features for effective thermal management to dissipate heat generated within the cavity substrate, thereby maintaining device reliability and performance.
- Manufacturability: Design the cavity substrate considering manufacturability factors such as scalability, reproducibility, and compatibility with fabrication processes.
- Simulation and Modeling: Utilize advanced simulation and modeling techniques to predict and optimize the performance of the cavity substrate before fabrication.
- Environmental Considerations: Account for environmental factors such as temperature variations, humidity, and mechanical stresses to ensure the stability and reliability of the cavity substrate under different operating conditions.
- Testing and Characterization: Develop comprehensive testing and characterization protocols to evaluate the optical performance and validate the design of the cavity substrate.
By adhering to these cavity substrate design guidelines, engineers and researchers can effectively design and optimize structures for various optical and photonics applications, leading to enhanced device performance and functionality.
What is the Cavity Substrate Fabrication Process?
The fabrication process for cavity substrates typically involves several steps tailored to the specific requirements of the application and the materials involved. Below is a generalized overview of the typical fabrication process:
- Material Selection: Choose appropriate substrate materials based on the desired optical properties, mechanical strength, thermal conductivity, and compatibility with the fabrication process. Common substrate materials include semiconductors, dielectrics, and optical crystals.
- Cleaning and Preparation: Clean the substrate surface thoroughly to remove contaminants and ensure proper adhesion of subsequent layers. This step often involves cleaning with solvents, followed by treatments such as plasma cleaning or chemical etching to improve surface quality.
- Layer Deposition: Deposit thin films or layers of materials onto the substrate using techniques such as physical vapor deposition (PVD), chemical vapor deposition (CVD), sputtering, or spin coating. These layers may include cladding layers, waveguide layers, active materials (such as quantum wells or quantum dots), or electrodes, depending on the device’s design and functionality.
- Patterning: Define the geometry and features of the device structure by patterning the deposited layers. This step typically involves photolithography, electron beam lithography, or other techniques to selectively remove or modify material in specific areas.
- Etching: Etch away unwanted material to create the desired cavity structure and define the waveguides or optical elements within the substrate. Wet chemical etching, dry etching (such as reactive ion etching), or laser ablation may be used depending on the materials and the desired etch profile.
- Integration of Additional Components: Integrate additional components such as mirrors, lenses, or electrical contacts as needed for the device’s functionality. These components may be fabricated separately and then assembled onto the substrate using bonding techniques or integrated directly into the substrate during the fabrication process.
- Annealing and Post-Processing: Perform annealing or other post-processing steps to improve the crystalline structure, reduce defects, and enhance the optical and electrical properties of the fabricated structure.
- Characterization and Testing: Characterize the fabricated cavity substrate using techniques such as optical spectroscopy, microscopy, or electrical measurements to assess its performance and functionality. This step helps validate the fabrication process and identify any defects or areas for improvement.
- Packaging and Integration: Package the fabricated substrate into a suitable housing or encapsulation to protect it from environmental factors and facilitate integration into larger systems or devices.
Throughout the fabrication process, precise control over material deposition, patterning, and etching is essential to ensure the desired optical properties and performance of the cavity substrate. Iterative optimization and refinement may be necessary to achieve the desired device specifications and functionality.
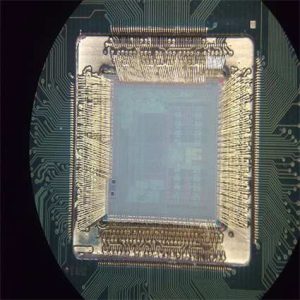
Cavity substrate
How do you manufacture a Cavity Substrate?
The fabrication process for cavity substrates involves several key steps to create structures that support and confine electromagnetic waves within a defined cavity or volume. Here’s a general overview of the cavity substrate fabrication process:
- Substrate Selection: Choose a suitable substrate material based on the desired optical properties, mechanical strength, thermal conductivity, and compatibility with the fabrication process. Common substrate materials include semiconductors, dielectrics, and optical crystals.
- Cleaning and Preparation: Clean the substrate surface thoroughly to remove any contaminants and ensure proper adhesion of subsequent layers. This typically involves cleaning with solvents and may include treatments such as plasma cleaning or chemical etching to improve surface quality.
- Layer Deposition: Deposit thin films or layers of materials onto the substrate using techniques such as physical vapor deposition (PVD), chemical vapor deposition (CVD), sputtering, or spin coating. These layers may include cladding layers, waveguide layers, active materials (such as quantum wells or quantum dots), or electrodes, depending on the device’s design and functionality.
- Patterning: Define the geometry and features of the device structure by patterning the deposited layers. This step typically involves photolithography, electron beam lithography, or other techniques to selectively remove or modify material in specific areas.
- Etching: Etch away unwanted material to create the desired cavity structure and define the waveguides or optical elements within the substrate. This can be accomplished using wet chemical etching, dry etching (such as reactive ion etching), or laser ablation, depending on the materials and desired etch profile.
- Integration of Additional Components: Integrate additional components such as mirrors, lenses, or electrical contacts as needed for the device’s functionality. These components may be fabricated separately and then assembled onto the substrate using bonding techniques or integrated directly into the substrate during the fabrication process.
- Annealing and Post-Processing: Perform annealing or other post-processing steps to improve the crystalline structure, reduce defects, and enhance the optical and electrical properties of the fabricated structure.
- Characterization and Testing: Characterize the fabricated cavity substrate using techniques such as optical spectroscopy, microscopy, or electrical measurements to assess its performance and functionality. This helps validate the fabrication process and identify any defects or areas for improvement.
- Packaging and Integration: Package the fabricated substrate into a suitable housing or encapsulation to protect it from environmental factors and facilitate integration into larger systems or devices.
Throughout the fabrication process, precise control over material deposition, patterning, and etching is essential to ensure the desired optical properties and performance of the cavity substrate. Iterative optimization and refinement may be necessary to achieve the desired device specifications and functionality.
How much should a Cavity Substrate cost?
The cost of a cavity substrate can vary widely depending on various factors such as the materials used, complexity of design, fabrication techniques, and desired specifications. Here are some factors that can influence the cost:
- Material Costs: The choice of substrate material can significantly impact the overall cost. Materials with specific optical properties or unique characteristics may be more expensive than others.
- Fabrication Techniques: Different fabrication techniques, such as photolithography, chemical vapor deposition, or laser ablation, have associated costs. More advanced or specialized techniques may incur higher costs.
- Complexity of Design: The complexity of the cavity substrate design, including the number of layers, features, and dimensions, can affect the fabrication complexity and, consequently, the cost.
- Volume of Production: Economies of scale typically apply in manufacturing. Larger production volumes may lead to lower per-unit costs due to efficiencies in material procurement, equipment utilization, and labor.
- Customization and Special Requirements: If the cavity substrate requires customization or special features tailored to a specific application, it may involve additional development costs.
- Quality and Tolerance Requirements: Tighter tolerances and higher quality standards may necessitate more precise fabrication processes and additional quality control measures, potentially increasing the cost.
- Supplier and Location: The choice of supplier and their location can impact costs due to differences in labor costs, overhead expenses, and shipping fees.
Given these variables, it’s challenging to provide a specific cost without knowing the details of the cavity substrate’s specifications and requirements. It’s recommended to consult with manufacturers or suppliers who specialize in cavity substrate fabrication to obtain accurate cost estimates based on your specific needs.
What is Cavity Substrate Base Material?
The cavity substrate base material refers to the primary material used as the foundation or substrate upon which additional layers and components are deposited or integrated to construct the cavity substrate. This base material serves as the structural support and provides the foundation for the device’s functionality.
The choice of cavity substrate base material depends on several factors including:
- Optical Properties: The base material should have appropriate optical properties such as refractive index, transparency, and dispersion characteristics to enable the desired optical functionality of the device.
- Mechanical Strength: It should possess sufficient mechanical strength to withstand processing steps and environmental conditions without deformation or damage.
- Thermal Conductivity: Good thermal conductivity helps dissipate heat generated within the device, maintaining its performance and reliability.
- Compatibility with Fabrication Processes: The base material should be compatible with the fabrication techniques and processes used to deposit additional layers and components onto it.
Common materials used as cavity substrate base materials include:
Semiconductors: Silicon (Si) and gallium arsenide (GaAs) are commonly used semiconductor materials for cavity substrates in photonics and microelectronics applications.
Dielectrics: Dielectric materials such as silicon dioxide (SiO2) and silicon nitride (Si3N4) are used when insulating properties or optical transparency is required.
Optical Crystals: Materials like lithium niobate (LiNbO3) and potassium titanyl phosphate (KTP) are used in applications requiring specific optical properties or nonlinear optical effects.
The selection of the cavity substrate base material is critical as it influences the device’s performance, manufacturability, and overall functionality.
Which company makes Cavity Substrates?
There are many companies that play an important role in manufacturing cavity substrates. Companies in the semiconductor, optoelectronics, and microelectronics industries around the world may be involved in the manufacture of cavity substrates. For example, major semiconductor manufacturers such as Intel, Samsung, and TSMC typically have advanced process technologies and equipment that can be used to manufacture various types of cavity substrates.
In addition to large semiconductor manufacturers, there are also companies specializing in the manufacture of optoelectronic and optical devices that may produce cavity substrates. These companies may focus more on specific types of cavity substrates, such as those used for lasers, optical modulators, or other optical devices.
Our company is also a player in the manufacturing of cavity substrates. We have advanced manufacturing equipment and an experienced team of engineers capable of providing high-quality customized solutions for cavity substrates to our customers. Our manufacturing process covers key steps such as material selection, layer deposition, pattern formation, etching, and more. We prioritize quality control to ensure that the produced cavity substrates meet our customers’ requirements and specifications.
We have strong production capabilities and a flexible production process, enabling us to meet the needs of different customers, from small batch to large-scale production. We are committed to working with our customers, understanding their needs, and providing customized solutions to ensure the success of their projects.
As a professional cavity substrate manufacturer, we are willing to establish long-term partnerships with our customers to drive innovation and progress in the optoelectronics and microelectronics industries, contributing to the advancement of the industry.
What are the 7 qualities of good customer service?
Good customer service is characterized by several key qualities that contribute to positive interactions and experiences for customers. Here are seven essential qualities of good customer service
- Responsiveness: Good customer service involves promptly addressing customer inquiries, concerns, and requests. Whether it’s answering phone calls, responding to emails, or engaging with customers on social media, being responsive demonstrates attentiveness and a commitment to customer satisfaction.
- Empathy: Empathy is the ability to understand and share the feelings of others. Good customer service representatives empathize with customers’ situations, acknowledge their concerns, and show genuine care and understanding. This helps build rapport and trust with customers.
- Clear Communication: Effective communication is crucial in customer service interactions. Good customer service involves using clear and concise language to convey information, instructions, or solutions to customers. Communication should be tailored to the customer’s level of understanding and delivered in a friendly and professional manner.
- Problem-Solving Skills: Good customer service representatives possess strong problem-solving skills to address customer issues and resolve conflicts effectively. They listen attentively to customers, identify root causes of problems, and offer appropriate solutions or alternatives to ensure customer satisfaction.
- Product Knowledge: Having comprehensive knowledge about products or services is essential for providing good customer service. Customer service representatives should be well-informed about the features, benefits, and uses of the products or services they support. This enables them to answer customer questions accurately and provide valuable assistance and recommendations.
- Consistency: Consistency is key to delivering good customer service experiences. Customers expect consistent levels of service across all interactions and touchpoints with a company, whether it’s in-store, online, or over the phone. Consistency builds trust and fosters loyalty among customers.
- Positive Attitude: A positive attitude is contagious and can significantly influence customer perceptions of service quality. Good customer service representatives approach interactions with optimism, enthusiasm, and a willingness to help. They maintain a friendly and professional demeanor, even in challenging situations, which enhances the overall customer experience.
By embodying these qualities, businesses can create a customer-centric culture and deliver exceptional service that exceeds customer expectations, fosters loyalty, and drives long-term success.
FAQs
What is a cavity substrate?
A cavity substrate is a material structure designed to support and confine electromagnetic waves within a defined volume or cavity. It is commonly used in the construction of lasers, optical modulators, and other devices where precise control of light propagation is necessary.
What materials are used in cavity substrates?
Cavity substrates can be made from various materials, including semiconductors (e.g., silicon, gallium arsenide), dielectrics (e.g., silicon dioxide, silicon nitride), and optical crystals (e.g., lithium niobate, potassium titanyl phosphate), depending on the specific application requirements.
What are the key properties of cavity substrates?
Key properties of cavity substrates include optical transparency, refractive index, thermal conductivity, mechanical strength, and compatibility with fabrication processes. These properties determine the substrate’s performance and suitability for different applications.
What are the applications of cavity substrates?
Cavity substrates find applications in various fields, including photonics, telecommunications, optical sensing, and laser technology. They are used in devices such as lasers, optical switches, modulators, photodetectors, and optical filters.
How are cavity substrates fabricated?
The fabrication process for cavity substrates typically involves steps such as material deposition, patterning, etching, and post-processing. Techniques such as physical vapor deposition, photolithography, and dry etching are commonly used to create the desired structure and features on the substrate.
What factors influence the cost of cavity substrates?
The cost of cavity substrates depends on factors such as the choice of materials, complexity of design, fabrication techniques, volume of production, and quality requirements. Customization and special features may also affect the overall cost.
Where can I find suppliers of cavity substrates?
Suppliers of cavity substrates can be found through online directories, industry trade shows, and professional networks. It’s essential to choose a reputable supplier with expertise in cavity substrate manufacturing and a track record of delivering high-quality products.