Chip Substrates Manufacturer
Chip Substrates Manufacturer, We are FC BGA package substrates, IC/BGA substrates, and other types package substrates Vendor, we offer high quality substrates with microtrace 9um, spacing 9um, the substrates from 2 layer to 22 layers. we can use the BT materials, ABF materials, and other High speed and high frequency materials.
Chip substrates are the foundational building blocks of integrated circuits (ICs), providing structural support and electrical connectivity for semiconductor devices. These substrates, typically made of materials like silicon, ceramic, or specialized compounds, serve as the platform upon which various components of the IC are mounted or fabricated. They play a crucial role in ensuring the functionality, performance, and reliability of electronic devices, including microprocessors, memory chips, sensors, and optoelectronic components. Chip substrates are designed with careful consideration of factors such as electrical performance, thermal management, signal integrity, and manufacturability. Through processes like layer deposition, photolithography, etching, and planarization, chip substrates are manufactured to meet the demanding requirements of modern semiconductor technology. As integral components of electronic systems, chip substrates contribute to the advancement of technology and enable the development of innovative devices that shape our interconnected world.
What is a Chip Substrate?
A chip substrate is a foundational component in the manufacturing of integrated circuits (ICs), such as microprocessors, memory chips, and other semiconductor devices. It serves as a base or platform upon which various components of the integrated circuit are built or mounted.
The substrate typically consists of a thin, flat material, often made of silicon, ceramic, or a specialized compound such as gallium arsenide. This material provides mechanical support for the components of the integrated circuit and serves as an electrical conductor, allowing signals to pass between different parts of the chip.
In addition to providing mechanical and electrical support, the substrate may also include features such as conductive traces, vias (vertical interconnect access), and bonding pads. These features help to connect the various components of the integrated circuit together and provide pathways for electrical signals to travel.
Overall, the chip substrate plays a crucial role in the functionality and performance of integrated circuits, providing the structural and electrical framework upon which the semiconductor devices are built.
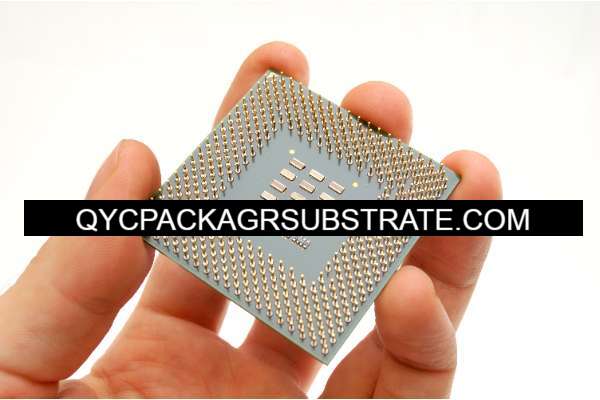
Chip Substrates Manufacturer
What are Chip Substrate Design Guidelines?
Chip substrate design guidelines refer to a set of principles and recommendations that engineers follow when designing the substrate for integrated circuits. These guidelines ensure that the substrate meets the electrical, thermal, and mechanical requirements of the semiconductor device, while also optimizing its performance, reliability, and manufacturability. Some common chip substrate design guidelines include:
- Electrical Performance:The substrate design should minimize parasitic resistance, capacitance, and inductance to ensure optimal electrical performance of the integrated circuit. This involves careful placement of signal traces, vias, and bonding pads to minimize signal interference and loss.
- Thermal Management:Effective thermal management is crucial to prevent overheating and ensure the reliability of the integrated circuit. The substrate design should incorporate features such as thermal vias, heat spreaders, and thermal pads to facilitate heat dissipation from the chip to the surrounding environment.
- Signal Integrity:The substrate design should maintain signal integrity by minimizing signal distortion, reflection, and crosstalk. This involves controlling impedance mismatches, optimizing signal routing, and minimizing the length of high-speed signal traces.
- Mechanical Stability:The substrate must provide sufficient mechanical support to withstand mechanical stresses during handling, assembly, and operation. This requires careful consideration of the substrate material, thickness, and layout to prevent warping, cracking, or delamination.
- Manufacturability:The substrate design should be manufacturable using standard semiconductor manufacturing processes. This involves adhering to design rules and specifications provided by the semiconductor foundry or substrate manufacturer to ensure compatibility with their fabrication capabilities.
- Cost Optimization:The substrate design should balance performance requirements with cost considerations to minimize manufacturing expenses while meeting the desired performance targets. This may involve optimizing material usage, reducing layer count, and simplifying fabrication processes.
By following these chip substrate design guidelines, engineers can ensure that the substrate meets the requirements of the integrated circuit in terms of electrical performance, thermal management, signal integrity, mechanical stability, manufacturability, and cost-effectiveness. This ultimately contributes to the overall functionality, reliability, and performance of the semiconductor device.
What is the Chip Substrate Fabrication Process?
The chip substrate fabrication process involves several steps to create the foundational substrate upon which the integrated circuit components will be built. While the specifics can vary depending on the substrate material and the requirements of the semiconductor device, the general process typically includes the following steps:
- Substrate Material Selection:The first step is to select the appropriate substrate material based on the specific requirements of the integrated circuit. Common substrate materials include silicon, ceramic, and specialized compounds like gallium arsenide.
- Substrate Preparation:The selected substrate material is prepared for further processing by cleaning and polishing to remove any contaminants and imperfections that could affect the performance of the integrated circuit.
- Layer Deposition:Depending on the substrate design, multiple layers of materials may be deposited onto the substrate surface. These layers may include insulating materials, conductive traces, and bonding pads, which are typically deposited using techniques such as physical vapor deposition (PVD), chemical vapor deposition (CVD), or electroplating.
- Photolithography:Photolithography is used to pattern the deposited layers by applying a photoresist material to the substrate surface and then exposing it to ultraviolet (UV) light through a photomask. This process selectively hardens or removes the photoresist, leaving behind the desired patterns on the substrate surface.
- Etching:After patterning, etching processes are used to selectively remove the exposed portions of the deposited layers, leaving behind the desired features such as conductive traces and bonding pads. Wet etching and dry etching techniques are commonly employed for this purpose.
- Via Formation:Vias are small holes or openings that penetrate through the substrate layers to provide vertical interconnect access (VIA) between different layers of the integrated circuit. Via formation typically involves drilling or etching holes in the substrate followed by deposition of conductive material to fill the vias.
- Planarization:Planarization techniques such as chemical mechanical polishing (CMP) are used to smooth out the substrate surface and remove any excess materials, ensuring uniformity and flatness across the substrate.
- Final Inspection and Testing:Once fabrication is complete, the substrate undergoes inspection and testing to ensure that it meets the specified requirements in terms of electrical performance, dimensional accuracy, and reliability.
By following these steps, engineers can fabricate chip substrates that provide the necessary structural support and electrical connectivity for the integrated circuit components, ultimately contributing to the functionality and performance of the semiconductor device.
How do you manufacture a Chip Substrate?
Manufacturing a chip substrate involves a series of intricate processes that begin with selecting the appropriate substrate material and end with quality assurance checks. Here’s a step-by-step overview of the chip substrate manufacturing process:
- Substrate Material Selection:Choose the substrate material based on the specific requirements of the integrated circuit. Common substrate materials include silicon, ceramic, and specialized compounds such as gallium arsenide.
- Substrate Preparation:Clean and polish the substrate material to remove any contaminants and imperfections that could impact the performance of the integrated circuit.
- Layer Deposition:Deposit multiple layers of materials onto the substrate surface using techniques like physical vapor deposition (PVD), chemical vapor deposition (CVD), or electroplating. These layers may include insulating materials, conductive traces, and bonding pads.
- Photolithography:Apply a photoresist material to the substrate surface and expose it to ultraviolet (UV) light through a photomask. This selectively hardens or removes the photoresist, leaving behind the desired patterns on the substrate surface.
- Etching: Use wet or dry etching techniques to selectively remove the exposed portions of the deposited layers, defining features such as conductive traces and bonding pads.
- Via Formation:Create vias, small holes or openings that penetrate through the substrate layers, to provide vertical interconnect access between different layers of the integrated circuit. This typically involves drilling or etching holes followed by deposition of conductive material to fill the vias.
- Planarization:Smooth out the substrate surface and remove excess materials using planarization techniques such as chemical mechanical polishing (CMP), ensuring uniformity and flatness across the substrate.
- Final Inspection and Testing:Inspect and test the finished substrate to ensure it meets specified requirements for electrical performance, dimensional accuracy, and reliability.
Throughout the manufacturing process, strict quality control measures are implemented to monitor each step and ensure consistency and reliability of the substrate. Any defects or deviations from specifications are identified and addressed promptly to maintain the quality of the final product.
By following these steps, manufacturers can produce chip substrates that provide the necessary structural support and electrical connectivity for the integrated circuit components, contributing to the functionality and performance of the semiconductor device.
How much should a Chip Substrate cost?
The cost of a chip substrate can vary widely depending on factors such as the substrate material, size, complexity, manufacturing process, and volume of production. Generally, chip substrates represent a significant portion of the overall cost of semiconductor devices, particularly for advanced integrated circuits used in high-performance applications such as computing, telecommunications, and consumer electronics.
Here are some factors that can influence the cost of a chip substrate:
- Substrate Material:Different substrate materials have varying costs. Silicon substrates are commonly used and may have lower costs compared to specialized materials like gallium arsenide. Ceramic substrates can also be more expensive due to their unique properties.
- Size and Complexity:Larger substrates or those with more complex designs requiring multiple layers, finer features, or advanced technologies may incur higher manufacturing costs.
- Manufacturing Process:The choice of manufacturing processes, such as deposition techniques, lithography, etching, and planarization methods, can impact the cost of production. Advanced fabrication processes may require more expensive equipment and materials.
- Volume of Production:Economies of scale come into play with larger production volumes. Higher volume production typically leads to lower per-unit costs due to spreading fixed costs across a larger number of units.
- Quality and Reliability Requirements:Meeting stringent quality and reliability standards may involve additional testing and inspection procedures, which can add to the overall cost.
- Supplier and Market Dynamics: Market conditions, competition among suppliers, and supply chain factors can also influence substrate costs.
Given these factors, it’s challenging to provide a specific cost figure for a chip substrate without knowing the details of the substrate’s specifications and production requirements. However, chip substrates can range from a few cents for simpler designs used in low-cost consumer electronics to hundreds or even thousands of dollars for advanced substrates used in high-performance computing or specialized applications.
Ultimately, the cost of a chip substrate is a balance between performance requirements, manufacturing capabilities, and budget constraints, and it’s typically one of many factors considered in the overall cost of semiconductor device production.
What is Chip Substrate Base Material?
The chip substrate base material refers to the foundational material upon which the various components of an integrated circuit (IC) are built or mounted. This material forms the structural backbone of the IC and provides the necessary mechanical support and electrical connectivity for the semiconductor device. The choice of substrate base material depends on factors such as the performance requirements, thermal properties, and cost considerations of the IC.
Some common chip substrate base materials include:
- Silicon:Silicon is one of the most widely used substrate materials in semiconductor manufacturing due to its abundance, excellent electrical properties, and compatibility with standard fabrication processes. Silicon substrates are commonly used for ICs such as microprocessors, memory chips, and sensors.
- Ceramic:Ceramic substrates, typically made of materials like alumina (aluminum oxide) or aluminum nitride, offer advantages such as high thermal conductivity, excellent mechanical stability, and good electrical insulation properties. Ceramic substrates are often used in high-power applications and devices requiring superior thermal management.
- Gallium Arsenide (GaAs):Gallium arsenide substrates are employed in specialized applications such as high-frequency devices, microwave circuits, and optoelectronic components. GaAs substrates offer advantages such as high electron mobility, which is advantageous in high-speed and high-frequency applications.
- Glass:Glass substrates are sometimes used in certain applications where optical transparency or specific thermal properties are required. Glass substrates can be made from various compositions to meet specific application requirements.
- Flexible Substrates:In some cases, flexible or bendable substrates made of polymers or other flexible materials are used, particularly in applications like flexible electronics, wearable devices, and displays.
Each substrate base material has its own unique properties and characteristics, which make it suitable for specific types of ICs and applications. The selection of the substrate base material is an important consideration in the design and manufacturing of integrated circuits, as it can significantly impact the performance, reliability, and cost of the semiconductor device.
Which company makes Chip Substrates?
Many companies specialize in the production of chip substrates. Some major companies include Shin-Etsu Chemical, Toray Industries, JSR, Panasonic, Nippon Steel & Sumikin Materials in Japan, Tela Innovations, Lam Research, Texas Instruments in the United States, and others. These companies have rich experience and advanced technology in chip substrate manufacturing.
As for our company, we can manufacture high-quality chip substrates to meet customer demands. Equipped with advanced manufacturing equipment and a skilled technical team, we offer chip substrates made from various materials, including silicon, ceramics, glass, and more. We emphasize quality control and technological innovation to ensure the production of high-quality products that meet customer requirements. Our manufacturing process strictly follows industry standards and quality management systems, with rigorous inspections and testing from raw material procurement to final product delivery. Additionally, we can customize chip substrates according to specific customer requirements, providing personalized solutions.
Our team is professional, efficient, and capable of closely collaborating with customers to understand and fulfill their needs. We prioritize communication and cooperation with customers, maintaining flexibility and responsiveness to ensure customer satisfaction and trust. Through continuous technological innovation and quality improvement, we are committed to becoming a leading supplier in the chip substrate field, offering customers high-quality products and services.
What are the 7 qualities of good customer service?
Good customer service is essential for building strong relationships with customers and fostering loyalty. Seven qualities of good customer service include:
- Responsiveness:Promptly addressing customer inquiries, concerns, and requests demonstrates attentiveness and a commitment to customer satisfaction.
- Empathy:Showing understanding and compassion towards customers’ needs and concerns helps to build rapport and trust. Empathetic responses can turn negative experiences into positive ones.
- Clear Communication:Providing clear and concise information, instructions, and explanations helps to avoid misunderstandings and confusion. Effective communication ensures that customers feel informed and valued.
- Professionalism:Maintaining professionalism in interactions with customers conveys credibility, reliability, and competence. Professional behavior instills confidence in the company and its products or services.
- Problem-solving Skills:Demonstrating effective problem-solving skills enables agents to address customer issues and resolve conflicts efficiently. Proactive problem-solving fosters customer satisfaction and loyalty.
- Flexibility:Being flexible and adaptable in accommodating customer needs and preferences shows a willingness to go above and beyond to meet their expectations. Flexibility can help tailor solutions to individual customers’ circumstances.
- Consistency:Providing consistent service across all touchpoints and interactions ensures a cohesive and reliable customer experience. Consistency builds trust and reinforces the company’s brand reputation.
By embodying these qualities, businesses can deliver exceptional customer service that enhances customer satisfaction, fosters loyalty, and drives long-term success.
FAQs
What is a chip substrate?
A chip substrate is a foundational component in the manufacturing of integrated circuits (ICs). It serves as a base or platform upon which various components of the IC are built or mounted, providing mechanical support and electrical connectivity.
What materials are used for chip substrates?
Common materials used for chip substrates include silicon, ceramic, gallium arsenide, and glass. The choice of material depends on factors such as performance requirements, thermal properties, and cost considerations.
What is the role of a chip substrate in an integrated circuit?
The chip substrate provides mechanical support for the components of the integrated circuit and serves as an electrical conductor, allowing signals to pass between different parts of the chip. It also helps dissipate heat generated by the IC.
What are the key considerations in chip substrate design?
Key considerations in chip substrate design include electrical performance, thermal management, signal integrity, mechanical stability, manufacturability, and cost optimization.
How are chip substrates manufactured?
Chip substrates are manufactured through processes such as layer deposition, photolithography, etching, via formation, planarization, and final inspection/testing. These processes may vary depending on the substrate material and design requirements.
What factors affect the cost of chip substrates?
The cost of chip substrates can vary depending on factors such as substrate material, size, complexity, manufacturing process, and volume of production. Economies of scale, quality requirements, and market dynamics also influence substrate costs.
Where can chip substrates be used?
Chip substrates are used in various electronic devices and applications, including microprocessors, memory chips, sensors, optoelectronic components, and high-frequency devices.