Embedded cavity PCB manufacturing
Embedded cavity PCB manufacturing. Open Cavity on the PCB substrates. Open one or Open multi-Cavity on the PCBs. we have made this types cavity PCB from 3 layer to 30 layers. High quality and fast lead time. and We used the base material as you requested.
Embedded Cavity PCBs represent a specialized innovation in printed circuit board technology, featuring meticulously crafted cutouts or cavities within the substrate. These cavities are strategically designed to house sensitive components or entire subsystems, offering numerous advantages in electronic system integration. By embedding components directly into the PCB, these boards enable significant space savings, contributing to more compact and efficient device designs. Moreover, Embedded Cavity PCBs facilitate enhanced thermal management, ensuring optimal operating conditions for components housed within the cavities. This innovative approach also aids in mitigating electromagnetic interference, thereby improving overall system reliability and performance. Commonly utilized in industries such as aerospace, automotive, and medical devices, Embedded Cavity PCBs exemplify the intersection of precision engineering and advanced electronics, providing solutions for applications where space, reliability, and performance are paramount.
What is an Embedded Cavity PCB?
Embedded cavity PCB manufacturing and package substrate manufacturing. We use advanced Msap and Sap technology, High multilayer interconnection substrates from 4 to 18 layers.
An Embedded Cavity PCB (Printed Circuit Board) is a specialized type of PCB design where one or more cavities or cutouts are incorporated directly into the PCB itself. These cavities are typically designed to house components or subsystems within the board, providing a more compact and integrated solution for electronic systems.
The cavities can serve various purposes:
- Component Integration: Some components, especially sensitive ones or those requiring specific environmental conditions, can be housed within the cavities to protect them from external factors such as dust, moisture, or electromagnetic interference.
- Space Optimization: By embedding components or subsystems within the PCB, the overall size of the electronic system can be reduced, making it more compact and suitable for applications where space is limited.
- Heat Dissipation: Cavities can also be used to enhance thermal management by providing space for heat sinks or other cooling solutions to dissipate heat generated by components.
- Electromagnetic Compatibility (EMC): Embedding certain components within the PCB can help in reducing electromagnetic interference, thus improving EMC performance.
- Protection: Cavities can offer physical protection to sensitive components from mechanical shocks or vibrations, enhancing the reliability and durability of the electronic system.
The design and fabrication of Embedded Cavity PCBs require careful consideration of factors such as component placement, routing, thermal management, and manufacturing processes. Specialized techniques and equipment may be required for creating cavities within the PCB, such as controlled-depth milling or laser etching.
Embedded Cavity PCBs are commonly used in various industries, including aerospace, automotive, medical devices, and telecommunications, where compactness, reliability, and performance are critical requirements.
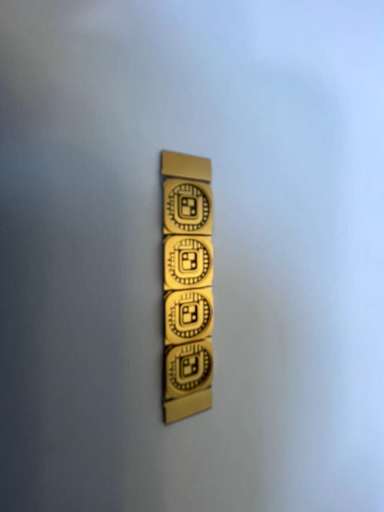
Embedded cavity PCB
What are the Embedded Cavity PCB Design Guidelines?
The Embedded Cavity PCB Design Guidelines refer to a set of principles and rules to be followed when designing embedded cavity PCBs. These guidelines aim to ensure the reliability, performance, and manufacturability of the design. Here are some common Embedded Cavity PCB Design Guidelines:
- Cavity Design: Determine the dimensions, shape, and location of the cavity to accommodate specific components or subsystems. Consideration should be given to component size, heat dissipation requirements, and electromagnetic compatibility in cavity design.
- Component Layout: Arrange components on the PCB to maximize the utilization of cavity space while ensuring good thermal management and circuit routing. Optimizing component layout to minimize electromagnetic interference is crucial.
- Thermal Management: Consider installing heatsinks, heat sinks, or other thermal management solutions within the cavity to ensure components operate within their normal temperature range.
- Electromagnetic Compatibility (EMC): Take measures to reduce electromagnetic interference, such as ground plane separation, differential routing, and good shielding design, to ensure EMC of the system.
- Manufacturability: Consider the manufacturing process of the cavity PCB, including cavity machining and component installation. Ensure the design is compatible with existing manufacturing techniques and equipment for achieving high-quality production.
- Material Selection: Choose appropriate substrate materials and copper thickness to meet design requirements and ensure good signal integrity and reliability.
- Testing and Validation: Conduct system-level testing and validation after the design is complete to ensure the embedded cavity PCB meets specifications and meets performance and reliability requirements.
These guidelines can be customized according to the specific requirements of the application and project to ensure optimal design outcomes and manufacturing success.
What is the Embedded Cavity PCB Fabrication Process?
The fabrication process for Embedded Cavity PCBs involves several steps to create the PCB with embedded cavities. Here’s an overview of the typical process:
- Design: The process begins with the design of the PCB layout, including the placement of components and the definition of cavity locations, dimensions, and shapes. Specialized PCB design software is often used for this purpose.
- Material Selection: Choose appropriate substrate materials based on factors such as thermal conductivity, dielectric properties, and mechanical strength. Copper foils with suitable thickness are selected for the conductive layers.
- Cavity Generation: Cavities are created within the PCB substrate using precision machining techniques such as milling, drilling, or laser ablation. The cavities are carefully designed and machined to the required dimensions and shapes to accommodate specific components or subsystems.
- Copper Deposition: Copper layers are deposited onto the substrate using techniques such as electroplating or chemical vapor deposition (CVD). This forms the conductive traces and layers on the surface and within the cavities as needed for the circuitry.
- Circuit Patterning: The circuitry is patterned onto the PCB using photolithography or other etching techniques. This involves applying a layer of photoresist material, exposing it to UV light through a photomask, and then developing it to remove the unwanted copper, leaving behind the desired traces and conductive paths.
- Component Mounting: Electronic components are mounted onto the PCB using surface-mount technology (SMT) or through-hole mounting techniques, depending on the design requirements. Care must be taken to ensure proper alignment and connection of components within the cavities.
- Soldering: Solder paste is applied to the component pads, and the PCB is subjected to a reflow soldering process to attach the components securely to the board.
- Testing and Inspection: The fabricated PCB undergoes electrical testing and visual inspection to ensure the integrity of the circuitry, component placement, and solder joints. Any defects or discrepancies are identified and addressed as needed.
- Finishing: The final steps may include applying surface finishes such as solder mask and silkscreen legend, as well as routing and edge trimming to finalize the PCB.
- Quality Assurance: Throughout the fabrication process, quality assurance measures are implemented to maintain consistency, reliability, and compliance with design specifications and industry standards.
By following these steps, manufacturers can produce Embedded Cavity PCBs that meet the required specifications and performance criteria for various applications.
How do you manufacture an Embedded Cavity PCB?
Manufacturing an Embedded Cavity PCB involves specialized processes to create printed circuit boards with embedded cavities. Here’s a detailed overview of the typical manufacturing process:
- Design Preparation: The process starts with the design of the PCB layout, including the placement of components and the definition of cavity locations, sizes, and shapes. This design phase is crucial to ensure that the final product meets the requirements of the intended application.
- Material Selection: Choose appropriate substrate materials based on factors such as thermal conductivity, dielectric properties, and mechanical strength. Copper foils with suitable thickness are also selected for the conductive layers.
- Cavity Generation: Cavities are created within the PCB substrate using precision machining techniques such as milling, drilling, or laser ablation. The cavities are carefully designed and machined to the required dimensions and shapes to accommodate specific components or subsystems.
- Layer Preparation: Depending on the design requirements, multiple layers of substrate and conductive materials may be prepared and stacked together. Each layer may undergo surface treatment processes such as cleaning, etching, or coating to ensure proper adhesion and conductivity.
- Lamination: The prepared layers are laminated together under heat and pressure to form a single composite structure. This lamination process ensures proper bonding between the layers and helps to maintain the integrity of the embedded cavities.
- Circuit Patterning: The conductive layers are patterned with the desired circuitry using photolithography or other etching techniques. This involves applying a layer of photoresist material, exposing it to UV light through a photomask, and then developing it to remove the unwanted copper, leaving behind the desired traces and conductive paths.
- Component Integration: Electronic components are mounted onto the PCB using surface-mount technology (SMT) or through-hole mounting techniques. Care must be taken to ensure proper alignment and connection of components within the cavities.
- Soldering: Solder paste is applied to the component pads, and the PCB is subjected to a reflow soldering process to attach the components securely to the board. This soldering process ensures reliable electrical connections between the components and the conductive traces.
- Testing and Inspection: The fabricated PCB undergoes electrical testing and visual inspection to ensure the integrity of the circuitry, component placement, and solder joints. Any defects or discrepancies are identified and addressed as needed.
- Finishing: The final steps may include applying surface finishes such as solder mask and silkscreen legend, as well as routing and edge trimming to finalize the PCB. These finishing processes enhance the durability, aesthetics, and functionality of the embedded cavity PCB.
- Quality Assurance: Throughout the manufacturing process, rigorous quality assurance measures are implemented to maintain consistency, reliability, and compliance with design specifications and industry standards.
By following these steps, manufacturers can produce high-quality Embedded Cavity PCBs that meet the requirements of various applications.
How much should an Embedded Cavity PCB cost?
The cost of an Embedded Cavity PCB can vary significantly depending on various factors such as:
- Design Complexity: The complexity of the PCB design, including the number of layers, size, and intricacy of the embedded cavities, will affect the manufacturing cost. More complex designs may require specialized equipment and processes, which can increase production costs.
- Materials: The choice of materials for the PCB substrate, conductive layers, and surface finishes will impact the overall cost. High-performance materials with specific properties, such as thermal conductivity or dielectric strength, may be more expensive than standard materials.
- Manufacturing Process: The manufacturing process involved in creating the embedded cavities, such as milling, drilling, or laser ablation, will influence the cost. Additionally, factors such as lamination, circuit patterning, component mounting, and soldering will contribute to the overall production cost.
- Quantity: The quantity of Embedded Cavity PCBs being produced will affect the unit cost. Typically, higher quantities can lead to economies of scale and lower per-unit costs due to efficiencies in manufacturing and bulk material purchases.
- Lead Time: Expedited production schedules or shorter lead times may incur additional costs for rush orders or priority manufacturing services.
- Supplier and Location: The choice of PCB manufacturer and their location can impact costs due to differences in labor rates, overhead expenses, and shipping costs.
- Additional Services: Additional services such as testing, inspection, quality assurance, and documentation may also add to the overall cost of the Embedded Cavity PCB.
It’s essential to work closely with a reputable PCB manufacturer to obtain a detailed quote tailored to the specific requirements of the project. Factors such as design complexity, materials, quantity, and additional services should all be considered when determining the cost of an Embedded Cavity PCB.
What is the Embedded Cavity PCB base material?
The choice of base material for Embedded Cavity PCBs depends on the specific requirements of the application, but commonly used materials include:
- FR-4: FR-4 (Flame Retardant 4) is a widely used substrate material for PCBs due to its excellent electrical insulation properties, mechanical strength, and affordability. It consists of woven fiberglass cloth impregnated with an epoxy resin binder.
- High-Temperature FR-4: For applications where elevated temperatures are a concern, high-temperature FR-4 variants with enhanced thermal properties may be used. These materials offer improved heat resistance while retaining the electrical and mechanical characteristics of standard FR-4.
- Polyimide (PI): Polyimide substrates, such as Kapton, are known for their exceptional thermal stability, flexibility, and resistance to chemicals and radiation. They are suitable for high-temperature and harsh environment applications where flexibility or thin form factors are required.
- Rogers Materials: Rogers Corporation produces a range of high-performance substrates optimized for RF/microwave applications. These materials offer low dielectric constant and loss tangent, making them suitable for high-frequency circuit designs.
- Metal Core PCBs: In applications requiring superior thermal management, metal core PCBs may be used. These PCBs feature a metal core (usually aluminum or copper) that provides excellent heat dissipation, making them ideal for power electronics and LED lighting applications.
- Ceramic: Ceramic substrates offer excellent thermal conductivity, mechanical stability, and electrical insulation properties. They are commonly used in high-power, high-frequency, and harsh environment applications where superior thermal performance is required.
The choice of base material depends on factors such as operating temperature, mechanical strength, electrical properties, and cost considerations. It’s essential to select a material that best meets the specific requirements of the Embedded Cavity PCB design and application. Additionally, the base material should be compatible with the manufacturing processes involved in creating the embedded cavities and assembling the PCB.
Which company manufactures Embedded Cavity PCBs?
Embedded Cavity PCBs are manufactured by various companies specializing in PCB fabrication and assembly. These companies typically have expertise in advanced PCB design, precision machining, and assembly techniques required for creating PCBs with embedded cavities. Some well-known PCB manufacturers and assembly service providers offer Embedded Cavity PCBs as part of their product offerings.
As for our company, we have the capability to produce Embedded Cavity PCBs to meet the diverse needs of our customers. With our state-of-the-art facilities and experienced team of engineers and technicians, we can handle the entire manufacturing process, from design optimization to final assembly.
Our company utilizes advanced CAD/CAM software and precision machining equipment to create custom-designed cavities within the PCB substrate. We carefully select high-quality materials, including specialized substrates and conductive layers, to ensure optimal performance and reliability.
Our manufacturing process follows strict quality control measures at every stage to guarantee the integrity and functionality of the Embedded Cavity PCBs. We conduct thorough testing and inspection to identify any defects or discrepancies and ensure compliance with industry standards and customer specifications.
Additionally, our company offers flexibility in terms of design customization, production volume, and lead times to accommodate the unique requirements of each project. Whether it’s for aerospace, automotive, medical, or telecommunications applications, we are committed to delivering Embedded Cavity PCBs of the highest quality and precision.
With our dedication to innovation, quality, and customer satisfaction, we strive to be a trusted partner for companies seeking reliable Embedded Cavity PCB solutions.
What are the 7 qualities of good customer service?
Good customer service is characterized by several key qualities that contribute to a positive customer experience. Here are seven qualities of good customer service:
- Responsiveness: Good customer service involves promptly addressing customer inquiries, concerns, and requests. Whether through phone calls, emails, or live chat support, customers expect timely responses to their queries. Being responsive shows that the company values its customers’ time and is committed to assisting them promptly.
- Empathy: Empathy involves understanding and acknowledging the customer’s feelings, needs, and perspectives. Customer service representatives who demonstrate empathy show genuine concern for the customer’s situation and strive to provide personalized assistance. By empathizing with customers, companies can build rapport, foster trust, and enhance the overall customer experience.
- Clarity: Clear communication is essential for effective customer service. Customer service representatives should communicate information, instructions, and solutions in a clear and concise manner, avoiding jargon or technical language that may confuse customers. Providing clear and easy-to-understand explanations helps customers feel informed and empowered to make decisions.
- Professionalism: Professionalism encompasses various aspects of customer service, including courtesy, respect, and integrity. Customer service representatives should maintain a professional demeanor at all times, regardless of the nature of the interaction or the customer’s behavior. Demonstrating professionalism builds credibility and trust, enhancing the company’s reputation and fostering positive customer relationships.
- Problem-Solving Skills: Good customer service involves effectively resolving customer issues and concerns. Customer service representatives should possess strong problem-solving skills, enabling them to identify root causes, explore solutions, and implement appropriate remedies. By proactively addressing customer problems, companies can prevent escalations and ensure customer satisfaction.
- Adaptability: In today’s dynamic business environment, adaptability is crucial for delivering good customer service. Customer service representatives should be flexible and adaptable, able to quickly adjust their approach to meet the evolving needs and preferences of customers. Whether facing technical issues, policy changes, or unexpected challenges, adaptability enables customer service teams to maintain high service standards and overcome obstacles effectively.
- Consistency: Consistency is key to building trust and loyalty with customers. Good customer service involves delivering consistent experiences across all touchpoints and interactions, regardless of the channel or representative involved. Consistency in service delivery, response times, and quality standards reassures customers and reinforces their confidence in the company.
By embodying these qualities, businesses can provide exceptional customer service that exceeds expectations, strengthens customer relationships, and contributes to long-term success.
FAQs
What is an Embedded Cavity PCB?
An Embedded Cavity PCB is a specialized type of printed circuit board that features cavities or cutouts within the substrate. These cavities are designed to house components or subsystems, allowing for a more compact and integrated electronic system.
What are the benefits of Embedded Cavity PCBs?
Embedded Cavity PCBs offer several advantages, including space optimization, improved thermal management, enhanced electromagnetic compatibility (EMC), physical protection for components, and the ability to integrate sensitive or specialized components within the board.
What types of components can be housed in the cavities of Embedded Cavity PCBs?
Various components can be housed in the cavities, including integrated circuits (ICs), sensors, connectors, passive components (resistors, capacitors), and even entire subsystems such as RF modules or power supplies.
How are the cavities created in Embedded Cavity PCBs?
The cavities are typically created using precision machining techniques such as milling, drilling, or laser ablation. These techniques allow for precise shaping and sizing of the cavities within the PCB substrate.
What materials are commonly used in the fabrication of Embedded Cavity PCBs?
Common materials used in Embedded Cavity PCBs include FR-4 (Flame Retardant 4), high-temperature FR-4 variants, polyimide (PI), metal core substrates, and ceramic materials. The choice of material depends on factors such as thermal conductivity, mechanical strength, and electrical properties.
Are there any limitations or considerations when designing Embedded Cavity PCBs?
Designing Embedded Cavity PCBs requires careful consideration of factors such as component placement, routing, thermal management, EMC, and manufacturing processes. Special attention should be paid to ensuring adequate clearance and spacing between components and cavities to avoid interference and maintain reliability.
What industries commonly use Embedded Cavity PCBs?
Embedded Cavity PCBs find applications in various industries, including aerospace, automotive, medical devices, telecommunications, industrial automation, and consumer electronics. They are particularly useful in applications where space constraints, thermal management, or EMC are critical considerations.
Can Embedded Cavity PCBs be customized to specific requirements?
Yes, Embedded Cavity PCBs can be customized to meet the specific requirements of different applications. Design customization options include cavity dimensions, shapes, placement, and integration of specific components or subsystems. Additionally, material selection, surface finishes, and assembly processes can be tailored to suit the application needs.