Embedded Components PCB manufacturing
Embedded Components PCB Manufacturing. Embedded Cavity/Slot PCB. or Embedded BGA package substrates. advanced Embedded Cavity production technology. we offer the Embedded cavity PCBs from 4 layer to 30 layers.
Embedded Components PCBs, or Embedded Component Printed Circuit Boards, are innovative electronic assemblies where electronic components are integrated directly into the layers of the PCB substrate, rather than being mounted on the surface. This advanced manufacturing technique offers several advantages, including reduced space requirements, improved electrical performance, enhanced reliability, and better thermal management. By embedding components within the PCB layers, designers can create more compact and lightweight electronic devices without sacrificing functionality or performance. Embedded Components PCBs are commonly used in various applications such as consumer electronics, automotive systems, medical devices, and industrial equipment, where space, weight, and performance are critical factors. As technology continues to evolve, Embedded Components PCBs represent a cutting-edge solution for designing and manufacturing next-generation electronic products with higher functionality and improved efficiency.
What is an Embedded Components PCB?
Embedded Components PCB manufacturing. the Package Substrate will be made with Showa Denko and Ajinomoto High speed materials.or other types high speed materials and high frequency materials.
An Embedded Components PCB (Printed Circuit Board) is a type of PCB where electronic components are directly embedded into the layers of the board itself, rather than being mounted on the surface. This embedding process involves placing the components within the layers of the PCB during the fabrication process, typically between the layers of copper traces and insulating material.
Embedding components into the PCB offers several advantages:
- Space Saving: By embedding components, the overall size of the PCB can be reduced since there’s no need for additional surface-mounted components.
- Improved Electrical Performance: Embedding components can reduce parasitic capacitance and inductance, leading to better electrical performance, such as reduced signal degradation and improved signal integrity.
- Enhanced Reliability: Since the embedded components are protected within the layers of the PCB, they are less susceptible to damage from external factors such as vibration, moisture, or physical impact. This can enhance the overall reliability of the electronic system.
- Thermal Management: Embedding components within the PCB can provide better thermal management since the components are in direct contact with the PCB material, which can act as a heat sink.
- Design Flexibility: Embedding components allows for more flexibility in PCB design, enabling designers to create more compact and innovative electronic products.
However, there are also some challenges associated with embedded components PCBs, including the complexity of fabrication and assembly processes, as well as potential difficulties in reworking or repairing the board if a component fails. Additionally, the cost of manufacturing embedded components PCBs can be higher compared to traditional PCBs due to the specialized processes involved.
What are the Embedded Components PCB Design Guidelines?
Designing a PCB with embedded components requires careful consideration of various factors to ensure optimal performance, reliability, and manufacturability. Here are some embedded components PCB design guidelines:
- Component Selection: Choose components suitable for embedding, considering their size, thermal characteristics, and suitability for embedding within PCB layers. Surface mount components with thin profiles are often preferred.
- PCB Layer Stackup: Design an appropriate layer stackup with consideration for the placement of embedded components. Ensure there are enough layers to accommodate both the embedded components and the necessary routing.
- Component Placement: Strategically place embedded components within the PCB layers to minimize signal interference and thermal issues. Consider the proximity to high-speed signal traces, thermal vias, and other critical components.
- Thermal Management: Incorporate thermal vias and heat sinks as needed to dissipate heat generated by embedded components. Ensure proper thermal conductivity within the PCB material to prevent overheating.
- Electrical Considerations: Optimize signal integrity by minimizing parasitic capacitance and inductance associated with embedded components. Pay attention to impedance matching and signal routing to minimize signal degradation.
- Manufacturability: Work closely with PCB manufacturers to ensure that the chosen embedding process is compatible with the selected components and PCB materials. Consider factors such as component assembly, soldering, and reworkability.
- Testing and Validation: Develop a comprehensive testing plan to validate the functionality and reliability of the embedded components PCB. Consider testing methods such as electrical testing, thermal testing, and reliability testing.
- Documentation: Provide detailed documentation including assembly instructions, component specifications, layer stackup diagrams, and any special considerations for handling embedded components during manufacturing and assembly.
- Compliance and Standards: Ensure compliance with relevant industry standards and regulations for electronic products, especially regarding safety, EMC (Electromagnetic Compatibility), and thermal management.
- Iterative Design Process: Use simulation tools and prototypes to iteratively refine the PCB design, considering factors such as signal integrity, thermal performance, and manufacturability until the desired performance goals are achieved.
By following these embedded components PCB design guidelines, engineers can create robust and reliable PCBs with embedded components suitable for a wide range of applications.
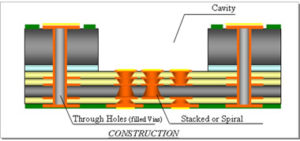
Embedded Components PCB
What is the Embedded Components PCB Fabrication Process?
The fabrication process for embedded components PCBs involves several steps, including design, material selection, component embedding, and assembly. Here’s an overview of the typical embedded components PCB fabrication process:
- Design: The process begins with the design of the PCB layout, including the placement of components and routing of traces. Special attention is given to the arrangement of embedded components within the layers of the PCB.
- Material Selection: Choose suitable materials for the PCB substrate and the embedded components. High-quality materials with good thermal conductivity and dielectric properties are preferred to ensure optimal performance and reliability.
- Layer Stackup Design: Design the layer stackup of the PCB to accommodate the embedded components. Determine the number and arrangement of layers based on factors such as signal integrity, thermal management, and manufacturability.
- Component Embedding: Embed the components within the layers of the PCB during the fabrication process. This can be done using various techniques such as laser drilling, micro-via filling, or lamination. Components are placed between layers of copper traces and insulating material, ensuring proper alignment and adhesion.
- Lamination: Once the components are embedded, the layers of the PCB are laminated together under heat and pressure to form a solid structure. This process ensures proper bonding between the layers and the embedded components.
- Copper Plating and Etching: Copper is plated onto the surface of the PCB and then etched away to create the desired circuit traces. This process is repeated for each layer of the PCB, forming the interconnections between embedded components and external connectors.
- Drilling: Holes are drilled through the PCB to create vias for electrical connections between layers. Special care is taken to avoid damaging the embedded components during the drilling process.
- Surface Finishing: Apply surface finishes such as solder mask and copper plating to protect the PCB from environmental factors and improve solderability.
- Component Assembly: Surface mount components are then soldered onto the PCB surface using conventional assembly techniques. Any additional components that cannot be embedded are mounted at this stage.
- Testing and Inspection: The fabricated PCB undergoes rigorous testing and inspection to ensure functionality, reliability, and adherence to design specifications. This may include electrical testing, thermal testing, and visual inspection.
- Finalization: Once the PCB passes testing and inspection, it is finalized by adding any necessary labeling, marking, or protective coatings before being packaged and shipped to the customer.
Overall, the fabrication process for embedded components PCBs requires careful planning, precise execution, and thorough testing to ensure the final product meets the desired performance and reliability standards. Collaboration between PCB designers, manufacturers, and assembly partners is essential to successfully produce high-quality embedded components PCBs.
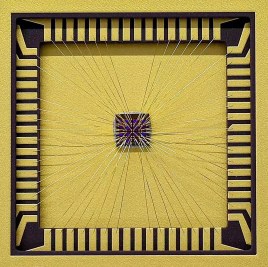
Embedded Components PCB
How do you manufacture an Embedded Components PCB?
Manufacturing an Embedded Components PCB involves several steps, from design to assembly. Here’s a general overview of the manufacturing process:
- Design and Layout: The process begins with the design and layout of the PCB, including the placement of components and routing of traces. Special attention is given to the arrangement of embedded components within the layers of the PCB.
- Material Selection: Choose suitable materials for the PCB substrate and the embedded components. High-quality materials with good thermal conductivity and dielectric properties are preferred to ensure optimal performance and reliability.
- Layer Stackup Design: Design the layer stackup of the PCB to accommodate the embedded components. Determine the number and arrangement of layers based on factors such as signal integrity, thermal management, and manufacturability.
- Component Embedding: Embed the components within the layers of the PCB during the manufacturing process. This can be done using various techniques such as laser drilling, micro-via filling, or lamination. Components are placed between layers of copper traces and insulating material, ensuring proper alignment and adhesion.
- Lamination: Once the components are embedded, the layers of the PCB are laminated together under heat and pressure to form a solid structure. This process ensures proper bonding between the layers and the embedded components.
- Copper Plating and Etching: Copper is plated onto the surface of the PCB and then etched away to create the desired circuit traces. This process is repeated for each layer of the PCB, forming the interconnections between embedded components and external connectors.
- Drilling: Holes are drilled through the PCB to create vias for electrical connections between layers. Special care is taken to avoid damaging the embedded components during the drilling process.
- Surface Finishing: Apply surface finishes such as solder mask and copper plating to protect the PCB from environmental factors and improve solderability.
- Component Assembly: Surface mount components are then soldered onto the PCB surface using conventional assembly techniques. Any additional components that cannot be embedded are mounted at this stage.
- Testing and Inspection: The manufactured PCB undergoes rigorous testing and inspection to ensure functionality, reliability, and adherence to design specifications. This may include electrical testing, thermal testing, and visual inspection.
- Finalization: Once the PCB passes testing and inspection, it is finalized by adding any necessary labeling, marking, or protective coatings before being packaged and shipped to the customer.
Overall, manufacturing an Embedded Components PCB requires careful planning, precise execution, and thorough testing to ensure the final product meets the desired performance and reliability standards. Collaboration between PCB designers, manufacturers, and assembly partners is essential to successfully produce high-quality embedded components PCBs.
How much should an Embedded Components PCB cost?
The cost of manufacturing an Embedded Components PCB (Printed Circuit Board) can vary significantly depending on various factors such as the complexity of the design, the size of the board, the number and type of embedded components, the choice of materials, the fabrication process, and the volume of production. Here are some factors that can influence the cost:
- Design Complexity: More complex designs with dense component placement and intricate routing patterns will generally incur higher manufacturing costs due to increased production time and specialized fabrication processes.
- Materials: The choice of materials for the PCB substrate, copper thickness, surface finish, and embedded components will affect the overall cost. High-quality materials with specific properties may come at a premium price.
- Embedded Component Technology: The type of embedded components used, such as integrated circuits (ICs), passive components, or sensors, can impact the cost. Some components may require specialized embedding techniques or materials, which could increase manufacturing costs.
- Manufacturing Process: The fabrication process for embedded components PCBs may involve additional steps such as laser drilling, micro-via filling, or lamination, which can add to the production cost compared to conventional PCB manufacturing processes.
- Volume of Production: Economies of scale typically apply in PCB manufacturing, meaning that larger production volumes generally lead to lower per-unit costs. However, setting up production for small volumes or prototypes may incur higher setup costs per unit.
- Testing and Quality Assurance: Rigorous testing and quality assurance procedures contribute to the overall manufacturing cost but are essential for ensuring the reliability and functionality of the PCB.
- Additional Services: Additional services such as design validation, prototype assembly, conformal coating, and packaging may incur extra costs.
Given the variability in these factors, it’s challenging to provide a precise estimate of the cost without specific details about the embedded components PCB design and requirements. Typically, manufacturers provide customized quotes based on the design specifications and volume of production requested.
For a rough estimate, you might consider obtaining quotes from multiple PCB manufacturers based on your specific design requirements and production volume. Additionally, you can use online PCB cost calculators offered by some manufacturers to get an initial idea of the cost.
What is the Embedded Components PCB base material?
The base material for an Embedded Components PCB (Printed Circuit Board) typically consists of layers of substrate material that provide structural support and insulation between conductive layers. Common base materials used in PCB manufacturing include:
- FR-4 (Flame Retardant 4): FR-4 is the most widely used PCB substrate material. It is a composite material made of woven fiberglass cloth impregnated with an epoxy resin binder. FR-4 offers good mechanical strength, electrical insulation properties, and thermal stability, making it suitable for a wide range of applications.
- High-Temperature FR-4: High-temperature FR-4 variants are available for applications that require enhanced thermal resistance. These materials can withstand higher operating temperatures without losing their mechanical or electrical properties.
- Polyimide (PI): Polyimide is a high-performance polymer material known for its excellent thermal stability, chemical resistance, and flexibility. It is often used in applications that require a flexible or rigid-flex PCB design, or in high-temperature environments where traditional substrates may not be suitable.
- Rogers High-Frequency Laminates: Rogers Corporation manufactures high-frequency laminates specifically designed for applications requiring high-speed signal transmission and low signal loss. These laminates offer low dielectric constant and loss tangent, making them suitable for RF/microwave applications.
- Metal Core PCB (MCPCB): Metal Core PCBs use a metal substrate, typically aluminum or copper, as the base material instead of fiberglass. MCPCBs offer excellent thermal conductivity, making them suitable for applications requiring efficient heat dissipation, such as LED lighting and power electronics.
The choice of base material depends on various factors including the application requirements, operating environment, thermal management considerations, and cost constraints. When designing an Embedded Components PCB, it’s essential to select a base material that provides the required mechanical, electrical, and thermal properties to ensure the reliability and performance of the final product.
Which company makes Embedded Components PCB?
There are several companies that manufacture Embedded Components PCBs, including well-known PCB manufacturers and electronics assembly service providers. These companies have expertise in advanced PCB fabrication techniques and can produce Embedded Components PCBs according to custom specifications. Some of the prominent companies in this field include:
- TTM Technologies: TTM Technologies is a leading global PCB manufacturer with expertise in producing complex and advanced PCBs, including those with embedded components. They offer a wide range of PCB fabrication services and have experience in embedding various types of components into PCBs.
- Sanmina: Sanmina is a multinational electronics manufacturing services provider that offers PCB fabrication and assembly services. They have capabilities for embedding components into PCBs and can produce high-quality Embedded Components PCBs for various industries.
- Benchmark Electronics: Benchmark Electronics is a contract manufacturer that offers PCB fabrication and assembly services. They have experience in producing Embedded Components PCBs for applications in aerospace, medical devices, telecommunications, and other industries.
- Rogers Corporation: Rogers Corporation manufactures high-performance materials used in PCB fabrication, including high-frequency laminates suitable for Embedded Components PCBs. While they do not directly manufacture PCBs, they provide materials that enable PCB manufacturers to produce Embedded Components PCBs with superior electrical performance.
As for our company, we have the expertise and capabilities to manufacture Embedded Components PCBs. With a dedicated team of experienced engineers and technicians, state-of-the-art facilities, and advanced manufacturing processes, we can produce high-quality PCBs with embedded components to meet the specific requirements of our customers. Our company employs advanced embedding techniques such as laser drilling, micro-via filling, and lamination to integrate components directly into the PCB layers, ensuring optimal performance, reliability, and manufacturability. We have experience working with a wide range of industries, including automotive, consumer electronics, industrial automation, and telecommunications, and can provide tailored solutions to meet the unique needs of each project. With a commitment to quality, innovation, and customer satisfaction, our company is well-positioned to deliver reliable and cost-effective Embedded Components PCBs for various applications.
Qualities of Good Customer Service
Good customer service is essential for fostering positive relationships with customers and ensuring their satisfaction. Here are some qualities that characterize good customer service:
- Empathy: Good customer service representatives demonstrate empathy by understanding and acknowledging the customer’s feelings, concerns, and needs. They listen actively and show genuine care and compassion for the customer’s situation.
- Effective Communication: Clear and concise communication is key to providing good customer service. Representatives should be able to convey information in a manner that is easy to understand and be responsive to customer inquiries and feedback.
- Product Knowledge: Customer service representatives should have a deep understanding of the products or services offered by the company. They should be able to provide accurate information, answer questions, and offer helpful recommendations to customers.
- Problem-Solving Skills: Good customer service involves resolving customer issues and addressing their concerns in a timely and efficient manner. Representatives should be proactive in finding solutions and taking ownership of customer problems until they are fully resolved.
- Professionalism: Customer service representatives should maintain a professional demeanor at all times, treating customers with respect and courtesy. They should be patient, courteous, and maintain a positive attitude, even in challenging situations.
- Adaptability: Every customer interaction is unique, and good customer service requires the ability to adapt to different situations and customer personalities. Representatives should be flexible and able to tailor their approach to meet the needs of each individual customer.
- Timeliness: Promptness is important in customer service. Representatives should respond to customer inquiries and resolve issues in a timely manner, keeping customers informed of any delays or updates along the way.
- Follow-Up: Following up with customers after resolving an issue or completing a transaction shows that you value their feedback and care about their experience. Good customer service involves checking in with customers to ensure their satisfaction and address any lingering concerns.
- Consistency: Consistency is key to building trust and loyalty with customers. Good customer service should be consistently delivered across all channels and interactions, whether it’s in person, over the phone, or online.
- Continuous Improvement: Good customer service is a continuous process of improvement. Companies should regularly gather feedback from customers, analyze trends and patterns, and make adjustments to their processes and training to enhance the customer experience over time.
By embodying these qualities, businesses can build strong customer relationships, foster loyalty, and differentiate themselves in a competitive marketplace.
FAQs
What are Embedded Components PCBs?
Embedded Components PCBs are printed circuit boards where electronic components are directly embedded within the layers of the board itself, rather than being mounted on the surface.
What are the advantages of Embedded Components PCBs?
Embedded Components PCBs offer advantages such as space-saving, improved electrical performance, enhanced reliability, better thermal management, and design flexibility.
What types of components can be embedded in PCBs?
Various types of components can be embedded in PCBs, including integrated circuits (ICs), passive components like resistors and capacitors, sensors, and other discrete components.
What materials are used in Embedded Components PCBs?
The base material for Embedded Components PCBs typically includes substrates like FR-4, high-temperature FR-4, polyimide, or metal core PCBs, depending on the application requirements.
How are components embedded in PCBs?
Components can be embedded in PCBs using techniques such as laser drilling, micro-via filling, or lamination. These methods involve placing components between layers of copper traces and insulating material during the PCB fabrication process.
What are the challenges associated with Embedded Components PCBs?
Challenges may include the complexity of fabrication and assembly processes, difficulties in reworking or repairing embedded components, and higher manufacturing costs compared to traditional PCBs.
What industries commonly use Embedded Components PCBs?
Embedded Components PCBs are used in various industries such as aerospace, automotive, consumer electronics, medical devices, telecommunications, and industrial automation, among others.
How do you design an Embedded Components PCB?
Design considerations for Embedded Components PCBs include component selection, PCB layer stackup design, thermal management, electrical considerations, manufacturability, testing, and compliance with industry standards.
What is the cost of manufacturing Embedded Components PCBs?
The cost of manufacturing Embedded Components PCBs depends on factors like design complexity, materials used, fabrication process, volume of production, and additional services required.
Where can I find a manufacturer for Embedded Components PCBs?
Many PCB manufacturers and electronics assembly service providers offer Embedded Components PCB fabrication services. It’s essential to choose a manufacturer with expertise in embedded component technology and a track record of producing high-quality PCBs.