Glass Substrates
Glass Substrates Manufacturing, Advanced production technology, advanced substrate, stable quality, the finished surface is more flat, more high temperature resistance, we produce glass packaging substrate from 2 layers to 20 layers.
Glass substrates serve as the fundamental building blocks for various technological applications, providing a stable and transparent foundation for electronic, optical, and architectural components. Composed of materials such as soda-lime glass, borosilicate glass, or specialty glasses, these substrates exhibit properties crucial for their intended uses. In electronics, they form the base for semiconductor devices like integrated circuits and photovoltaic cells, facilitating the deposition and patterning of thin films. Optically, they enable the creation of lenses, mirrors, and optical filters due to their clarity and refractive index. Architecturally, glass substrates contribute to sleek facades and durable windows, enhancing both aesthetics and functionality. With precise manufacturing processes involving melting, forming, annealing, and finishing, glass substrates are tailored to meet stringent quality standards, ensuring reliability and performance across diverse industries.
What is a Glass Substrate?
A glass substrate refers to a flat piece of glass that serves as a base or foundation for various applications. It’s commonly used in electronics, optics, and other industries where a smooth, durable, and transparent surface is needed.
In electronics, glass substrates are often used for manufacturing semiconductor devices such as integrated circuits (ICs), liquid crystal displays (LCDs), and photovoltaic cells. The glass substrate provides a stable platform for depositing and patterning thin films of conductive, insulating, or semiconducting materials to create electronic components.
In optics, glass substrates are used as the foundation for making lenses, mirrors, and optical filters. The optical properties of the glass, such as its transparency and refractive index, play a crucial role in determining the performance of the final optical device.
Overall, glass substrates are essential components in many technological applications due to their versatility, transparency, and ease of fabrication.
What are Glass Substrate Design Guidelines?
Glass substrate design guidelines refer to recommendations or principles that guide the design process when using glass as a substrate in various applications. These guidelines ensure that the glass substrate meets the requirements of the specific application and functions optimally. Some common glass substrate design guidelines include:
- Material Selection: Choose a type of glass with properties suitable for the intended application, such as thermal expansion coefficient, optical transparency, chemical resistance, and mechanical strength.
- Dimensional Stability: Ensure that the glass substrate maintains dimensional stability over a range of operating conditions, including temperature variations and mechanical stress.
- Surface Quality: Select glass with a high-quality surface finish to minimize defects that could affect the performance of the final product. Surface roughness, flatness, and cleanliness are crucial considerations.
- Thickness Consideration: Determine the appropriate thickness of the glass substrate based on structural requirements, optical properties, and manufacturing constraints.
- Compatibility with Manufacturing Processes: Consider the compatibility of the glass substrate with manufacturing processes such as cutting, grinding, polishing, coating, and bonding. Ensure that the chosen glass can withstand the processing steps involved in producing the final product.
- Environmental Considerations: Assess the glass substrate’s resistance to environmental factors such as humidity, temperature extremes, chemical exposure, and UV radiation, depending on the application’s operating environment.
- Handling and Mounting: Design the glass substrate with features that facilitate handling, mounting, and integration into the final product, such as edge treatments, mounting holes, and alignment marks.
- Optical Performance: If the application involves optics, consider factors such as light transmission, refractive index, dispersion, and birefringence when designing the glass substrate to ensure optimal optical performance.
- Cost Considerations: Balance performance requirements with cost considerations by optimizing the design for efficiency and minimizing material waste.
- Testing and Quality Assurance: Develop testing procedures to ensure the quality and reliability of the glass substrate throughout its lifecycle, including material characterization, dimensional inspection, and performance testing.
By following these glass substrate design guidelines, engineers and designers can effectively utilize glass substrates in various applications while meeting performance, reliability, and cost requirements.
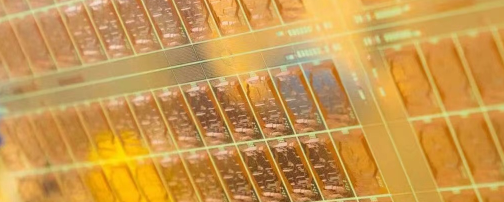
Advanced Glass Substrates
What is the Glass Substrate Fabrication Process?
The fabrication process of glass substrates involves several steps to transform raw materials into finished glass sheets with specific properties suitable for various applications. Here’s a general overview of the glass substrate fabrication process:
- Batch Preparation: The process begins with the preparation of raw materials, which typically include silica sand, soda ash, limestone, and other additives. These materials are carefully mixed in precise proportions to form a glass batch.
- Melting: The glass batch is then fed into a furnace and melted at high temperatures, typically exceeding 1,500 degrees Celsius (2,732 degrees Fahrenheit). The intense heat causes the raw materials to fuse together into a molten liquid.
- Refining: During the melting process, refining agents may be added to remove impurities and bubbles from the molten glass. This step helps improve the optical clarity and mechanical properties of the glass.
- Forming: Once the molten glass reaches the desired composition and consistency, it is shaped into a flat sheet using one of several forming methods:
– Float Glass Process: The molten glass is poured onto a bath of molten tin, where it spreads out to form a continuous ribbon. As it cools and solidifies, it becomes a flat sheet with uniform thickness.
– Drawn Sheet Process: The molten glass is drawn vertically upward through a series of rollers or draw plates, forming a continuous sheet of glass.
– Roll-to-Roll Process: Molten glass is poured onto a conveyor belt and passed through rollers to flatten and shape it into a continuous sheet.
- Annealing: The newly formed glass sheet undergoes an annealing process to relieve internal stresses and improve its mechanical strength. This involves slowly cooling the glass at a controlled rate in a temperature-controlled annealing lehr.
- Cutting and Finishing: Once the glass has been annealed, it is cut into individual sheets of the desired size using diamond or carbide-tipped tools. The edges of the glass may be ground, polished, or chamfered to achieve the desired finish and dimensions.
- Surface Treatment: Depending on the application, the surface of the glass substrate may undergo additional treatment processes such as coating, etching, or printing to enhance its optical, electrical, or mechanical properties.
- Quality Control:Throughout the fabrication process, quality control measures are implemented to ensure that the glass substrates meet specified standards for thickness, flatness, optical clarity, and other properties.
By following these steps, manufacturers can produce high-quality glass substrates tailored to the requirements of diverse applications, including electronics, optics, architecture, and automotive industries.
How do you manufacture Glass Substrates?
Manufacturing glass substrates involves a series of steps to produce flat sheets of glass with specific properties suitable for various applications. Here’s an overview of the typical process:
- Batch Preparation: Raw materials such as silica sand, soda ash, limestone, and other additives are carefully measured and mixed to form a precise glass batch. The proportions of these materials are critical to achieving the desired properties of the glass.
- Melting: The glass batch is fed into a furnace where it is heated to high temperatures, typically exceeding 1,500 degrees Celsius (2,732 degrees Fahrenheit). The intense heat melts the raw materials, forming a molten glass.
- Refining:During the melting process, refining agents may be added to remove impurities and bubbles from the molten glass. This step helps improve the optical clarity and mechanical properties of the glass.
- Forming:
– Float Glass Process: In this widely used method, the molten glass is poured onto a bath of molten tin. Because glass is less dense than tin when molten, it floats on the surface and spreads out to form a continuous ribbon. As it cools and solidifies, it becomes a flat sheet with uniform thickness.
– Drawn Sheet Process: Alternatively, the molten glass can be drawn vertically upward through a series of rollers or draw plates, forming a continuous sheet of glass.
– Roll-to-Roll Process: Molten glass is poured onto a conveyor belt and passed through rollers to flatten and shape it into a continuous sheet.
- Annealing: The newly formed glass sheet undergoes an annealing process to relieve internal stresses and improve its mechanical strength. This involves slowly cooling the glass at a controlled rate in a temperature-controlled annealing lehr.
- Cutting and Finishing: Once annealed, the glass is cut into individual sheets of the desired size using diamond or carbide-tipped tools. The edges may be ground, polished, or chamfered to achieve the desired finish and dimensions.
- Surface Treatment: Depending on the application, the surface of the glass substrate may undergo additional treatment processes such as coating, etching, or printing to enhance its optical, electrical, or mechanical properties.
- Quality Control: Throughout the manufacturing process, quality control measures are implemented to ensure that the glass substrates meet specified standards for thickness, flatness, optical clarity, and other properties.
By following these steps, manufacturers can produce high-quality glass substrates tailored to the requirements of diverse applications, including electronics, optics, architecture, and automotive industries.
How much should Glass Substrates cost?
The cost of glass substrates can vary widely depending on several factors such as the type of glass, its dimensions, thickness, surface finish, quality, quantity ordered, and market conditions. Here are some factors that influence the cost of glass substrates:
- Type of Glass: Different types of glass have different properties and manufacturing processes, which can affect their cost. For example, specialty glasses with specific optical, thermal, or chemical properties may be more expensive than standard soda-lime glass.
- Dimensions and Thickness: Larger or thicker glass substrates typically cost more due to the increased material and manufacturing expenses required to produce them.
- Surface Finish: Glass substrates with higher quality surface finishes, such as polished or coated surfaces, may command a higher price due to additional processing steps and materials involved.
- Quantity Ordered: Bulk orders of glass substrates may be eligible for volume discounts, reducing the cost per unit compared to smaller orders.
- Customization: Customized glass substrates with unique specifications or features may incur additional costs for design, tooling, and production setup.
- Quality and Specifications: Glass substrates manufactured to tighter tolerances or higher quality standards may come at a premium compared to standard-grade glass.
- Market Conditions: Supply and demand dynamics, as well as fluctuations in raw material prices and manufacturing costs, can impact the overall pricing of glass substrates.
It’s essential to consider these factors when estimating the cost of glass substrates for a specific application. Additionally, obtaining quotes from multiple suppliers and comparing prices can help identify the most cost-effective option while ensuring the required quality and performance standards are met.
What is Glass Substrate Base Material?
The term “glass substrate base material” typically refers to the primary type of glass used as the foundation or base for various applications. In the context of electronics, optics, and other industries, glass substrates serve as the platform upon which thin films or functional layers are deposited to create electronic components, optical devices, or other products.
The choice of glass substrate base material depends on the specific requirements of the application, including optical transparency, thermal expansion coefficient, mechanical strength, chemical resistance, and cost considerations. Some common types of glass substrate base materials include:
- Soda-Lime Glass: This is the most common type of glass substrate, known for its low cost and good optical clarity. It is often used in applications where high optical quality is not critical, such as flat panel displays, windows, and simple optical components.
- Borosilicate Glass: Borosilicate glass has excellent thermal shock resistance and low thermal expansion, making it suitable for applications requiring thermal stability, such as laboratory glassware, cookware, and certain electronic components.
- Fused Silica (Quartz): Fused silica offers exceptional optical clarity, high temperature resistance, and low thermal expansion, making it ideal for precision optical components, semiconductor manufacturing, and high-power laser applications.
- Specialty Glasses: Specialty glasses, such as lead-free glasses, aluminosilicate glasses, or specialty coatings, are tailored to specific applications that demand unique optical, mechanical, or chemical properties.
- Float Glass: Float glass is a high-quality, flat glass substrate produced by the float glass process. It offers excellent surface quality, optical clarity, and uniform thickness, making it suitable for applications such as architectural glass, automotive glass, and display panels.
- Quartz Glass: Quartz glass, also known as fused quartz or silica glass, is a high-purity material with exceptional optical and thermal properties. It is commonly used in semiconductor manufacturing, optics, and high-temperature applications.
The selection of the glass substrate base material is crucial to the performance and reliability of the final product. Engineers and designers carefully consider the properties of different types of glass substrates to ensure they meet the requirements of the intended application.
Which company manufactures Glass Substrates?
Glass substrates are manufactured by several companies, including major manufacturers such as Corning, Asahi Glass, Sharp, LG Display, BOE, and Samsung Display. These companies have extensive experience and expertise in glass manufacturing, enabling them to produce various types and specifications of glass substrates for electronic, optical, architectural, and other applications.
At our company, we also have the capability to produce high-quality glass substrates. We have advanced glass manufacturing equipment and a skilled technical team capable of meeting customers’ diverse requirements for glass substrates. Our production processes adhere to international standards to ensure consistent and reliable product quality. Additionally, we offer customization of glass substrates according to specific customer needs, including dimensions, thickness, and surface treatments.
Our glass substrates find wide-ranging applications across various industries, including electronics (such as flat panel displays, smartphones), optical devices (such as lenses, mirrors), and architectural materials (such as glass facades). Whether for mass production or custom manufacturing, we strive to deliver high-quality products and professional services to meet our customers’ demands.
Through continuous technological innovation and quality management, our company aims to become one of the leading manufacturers in the glass substrate industry, providing customers with superior products and satisfactory services.
What are the 7 qualities of good customer service?
Good customer service is essential for building strong relationships with customers and fostering loyalty. Here are seven qualities that contribute to excellent customer service:
- Responsiveness: Being responsive means promptly addressing customer inquiries, concerns, and requests. This includes answering phone calls and emails promptly, acknowledging messages, and providing timely assistance to resolve issues.
- Empathy: Empathy involves understanding and showing compassion for customers’ feelings, concerns, and situations. Empathetic customer service representatives listen attentively, validate customers’ emotions, and demonstrate understanding and support.
- Professionalism: Professionalism encompasses maintaining a courteous, respectful, and knowledgeable demeanor at all times. Customer service representatives should communicate clearly, remain calm under pressure, and adhere to company policies and standards.
- Effective Communication: Effective communication involves conveying information clearly, accurately, and in a manner that is easy for customers to understand. This includes active listening, asking relevant questions, and providing helpful explanations or instructions.
- Problem-Solving Skills:Good customer service requires the ability to effectively identify, analyze, and resolve customer problems and issues. Customer service representatives should be resourceful, creative, and proactive in finding solutions to meet customers’ needs.
- Reliability: Reliability involves delivering on promises and commitments made to customers. This includes following through on resolutions, providing accurate information, and consistently meeting or exceeding customer expectations.
- Personalization: Personalization entails tailoring interactions and solutions to each customer’s unique needs, preferences, and circumstances. By showing genuine interest and understanding, customer service representatives can create personalized experiences that leave a positive impression on customers.
By embodying these qualities, businesses can cultivate a reputation for exceptional customer service and build long-lasting relationships with their customers.
FAQs (Frequently Asked Questions)
What is a glass substrate?
A glass substrate is a flat piece of glass used as a base or foundation for various applications, including electronics, optics, and architecture.
What are glass substrates used for?
Glass substrates are used in a wide range of applications, such as manufacturing semiconductor devices (e.g., integrated circuits), optical components (e.g., lenses, mirrors), flat panel displays, solar panels, and architectural glass.
What are the different types of glass substrates?
Common types of glass substrates include soda-lime glass, borosilicate glass, fused silica (quartz), specialty glasses (e.g., lead-free glass, aluminosilicate glass), and float glass.
What are the key properties of glass substrates?
Key properties of glass substrates include optical transparency, thermal expansion coefficient, mechanical strength, chemical resistance, surface finish, and dimensional stability.
How are glass substrates manufactured?
The manufacturing process of glass substrates typically involves batch preparation, melting, forming (e.g., float glass process, drawn sheet process), annealing, cutting, finishing, surface treatment, and quality control.
What factors should be considered when selecting a glass substrate?
Factors to consider when selecting a glass substrate include the application requirements (e.g., optical, mechanical, thermal properties), environmental conditions, cost, and manufacturing capabilities.