IPC Class III PCB Manufacturer
IPC Class III PCB Manufacturer. we can produce the best samllest bump pitch with 100um, the best smallest trace are 9um. and the smallest gap are 9um. most of the design are 15um to 30um trace and spacing.
IPC Class III PCBs represent the pinnacle of quality and reliability in the field of printed circuit boards (PCBs). Designed to meet the stringent standards set by the Institute for Interconnecting and Packaging Electronic Circuits (IPC), Class III PCBs are engineered for mission-critical applications where failure is not an option. These PCBs adhere to rigorous specifications, including tighter tolerances, advanced materials, and thorough testing procedures, ensuring maximum durability and performance even in the harshest operating conditions. IPC Class III PCBs are commonly used in industries such as aerospace, military, medical, and automotive, where reliability is paramount. With their superior quality, adherence to strict standards, and ability to withstand extreme environments, IPC Class III PCBs provide the foundation for the most demanding electronic systems, delivering peace of mind to manufacturers and end-users alike.
What is IPC Class III PCB?
IPC Class III PCB (Printed Circuit Board) refers to a set of standards established by the Institute for Interconnecting and Packaging Electronic Circuits (IPC) for the design, manufacture, and assembly of high-reliability electronic assemblies. Class III is the highest level of quality and reliability within the IPC standards hierarchy and is typically used in applications where failure could result in serious consequences, such as in aerospace, military, medical, or automotive industries.
These standards outline stringent requirements for various aspects of the PCB, including material selection, design criteria, fabrication processes, and assembly techniques. IPC Class III PCBs often require tighter tolerances, more rigorous testing procedures, and specialized manufacturing techniques compared to lower classes.
Some key features of IPC Class III PCBs include:
- Enhanced reliability: Class III PCBs must adhere to strict guidelines to ensure the highest level of reliability and durability under harsh operating conditions.
- Tighter tolerances: The tolerances for dimensions, hole sizes, and other critical parameters are more stringent compared to lower classes, ensuring precise and accurate assembly.
- Advanced materials:Class III PCBs often utilize high-performance materials with superior electrical properties and mechanical strength to meet demanding requirements.
- Thorough testing: Extensive testing and inspection procedures are mandated to identify any defects or weaknesses in the PCB assembly, ensuring that it meets the specified performance criteria.
- Robust documentation:Comprehensive documentation, including design files, manufacturing records, and test reports, is required to demonstrate compliance with IPC Class III standards and facilitate traceability throughout the production process.
Overall, IPC Class III PCBs are designed and manufactured to provide maximum reliability and performance in mission-critical electronic applications, making them suitable for use in environments where failure is not an option.
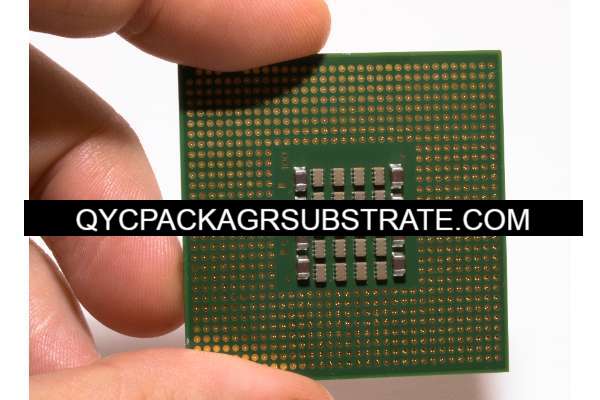
IPC Class III PCB Manufacturer
What are the IPC Class III PCB Design Guidelines?
IPC Class III PCB design guidelines encompass a range of specifications and recommendations aimed at ensuring the highest level of reliability and performance in electronic assemblies. Here are some key aspects covered by these guidelines:
- Material Selection: Class III PCBs often require the use of high-quality, high-reliability materials with specific electrical, thermal, and mechanical properties. Materials should be selected based on their ability to withstand harsh operating conditions and provide long-term reliability.
- Component Placement: Components should be placed on the PCB layout in a manner that minimizes signal interference, thermal issues, and assembly difficulties. Proper component placement can help optimize signal integrity and thermal management while facilitating efficient assembly processes.
- Trace Routing: PCB traces should be routed to minimize signal distortion, electromagnetic interference (EMI), and crosstalk. High-speed signals, in particular, require careful attention to impedance control, signal integrity, and proper routing techniques such as differential pairs and controlled impedance routing.
- Grounding and Power Distribution:Proper grounding and power distribution are critical for maintaining signal integrity, minimizing noise, and ensuring stable operation of the electronic assembly. Ground and power planes should be carefully designed to provide low impedance paths and reduce voltage drops.
- Thermal Management: Effective thermal management is essential for preventing overheating and ensuring the reliability of electronic components. Considerations such as thermal vias, thermal pads, and heatsinks should be incorporated into the design to dissipate heat efficiently.
- Design for Manufacturability (DFM): Class III PCB designs should be optimized for manufacturability to minimize assembly defects and ensure consistent quality. DFM considerations include component placement, solderability, panelization, and testability.
- Design for Test (DFT):Testability features should be integrated into the PCB design to facilitate efficient testing and inspection processes. This may include test points, access for automated test equipment (ATE), and built-in self-test (BIST) capabilities.
- Environmental Considerations: Class III PCBs may be subjected to extreme environmental conditions, so the design should take into account factors such as temperature, humidity, vibration, and shock resistance to ensure reliable operation in challenging environments.
- Documentation: Comprehensive documentation is essential for Class III PCBs, including detailed design files, manufacturing specifications, assembly instructions, and test reports. This documentation helps ensure traceability and facilitates quality control throughout the production process.
By adhering to these IPC Class III PCB design guidelines, designers can create electronic assemblies that meet the stringent requirements for reliability, performance, and quality demanded by industries such as aerospace, military, medical, and automotive.
What is the IPC Class III PCB Fabrication Process?
The fabrication process for IPC Class III PCBs involves several stages, each crucial for ensuring the highest level of quality, reliability, and performance. Here’s an overview of the typical steps involved in the fabrication of Class III PCBs:
- Design Verification: Before fabrication begins, the PCB design undergoes thorough verification to ensure compliance with IPC Class III standards. This includes checks for design rule violations, signal integrity issues, and manufacturability concerns.
- Material Selection: High-quality materials that meet the requirements for IPC Class III PCBs are selected, including substrates, copper foils, solder masks, and surface finishes. Material properties such as electrical conductivity, thermal conductivity, and mechanical strength are carefully considered.
- Preparation of Substrate: The substrate material, typically a laminate composed of layers of fiberglass reinforced with epoxy resin (FR-4), is prepared by cutting it to size and cleaning it to remove any contaminants that could affect adhesion and solderability.
- Copper Cladding: Copper foils are laminated onto the substrate to create the conductive layers of the PCB. The copper foil is etched to remove excess copper and define the circuit traces according to the PCB design.
- Drilling: Holes are drilled into the PCB to accommodate through-hole components and vias. Precision drilling is essential to ensure accurate hole placement and size control.
- Plating: After drilling, the walls of the plated through-holes are electroplated with copper to provide conductivity and mechanical strength. This process also involves the deposition of surface finishes such as gold, silver, or tin to protect the exposed copper surfaces from oxidation and facilitate soldering.
- Etching and Stripping:The excess copper is etched away from the non-conductive areas of the PCB using chemical etchants. After etching, the remaining photoresist is stripped away, leaving behind the desired circuit traces.
- Solder Mask Application: A solder mask is applied to the PCB to protect the circuitry from environmental factors and prevent solder bridges during assembly. Openings are created in the solder mask to expose the pads for component soldering.
- Silkscreen Printing: Component designators, polarity markings, logos, and other identifying information are printed onto the PCB surface using a silkscreen printing process. This helps assembly technicians identify and place components accurately.
- Final Inspection and Testing: The fabricated PCBs undergo rigorous inspection and testing to ensure they meet the requirements of IPC Class III standards. This may include visual inspection, electrical testing, and dimensional measurements to verify compliance with design specifications.
- Documentation and Traceability: Comprehensive documentation, including fabrication records, material certifications, and inspection reports, is generated to provide traceability and ensure accountability throughout the fabrication process.
By following these steps and adhering to IPC Class III standards, PCB fabricators can produce high-quality, reliable PCBs suitable for use in demanding applications such as aerospace, military, medical, and automotive electronics.
How do you manufacture IPC Class III PCBs?
Manufacturing IPC Class III PCBs involves adhering to stringent standards and employing advanced processes to ensure the highest level of quality, reliability, and performance. Here’s an overview of the manufacturing process for IPC Class III PCBs:
- Design Verification: Before manufacturing begins, the PCB design undergoes thorough verification to ensure compliance with IPC Class III standards. Design rule checks, signal integrity analysis, and manufacturability assessments are performed to identify and resolve any potential issues.
- Material Selection: High-quality materials that meet the requirements for IPC Class III PCBs are carefully selected, including substrates, copper foils, solder masks, and surface finishes. Material properties such as electrical conductivity, thermal conductivity, and mechanical strength are critical considerations.
- Preparation of Substrate: The substrate material, typically a laminate composed of layers of fiberglass reinforced with epoxy resin (FR-4), is prepared by cutting it to size and cleaning it to remove any contaminants that could affect adhesion and solderability.
- Copper Cladding:Copper foils are laminated onto the substrate to create the conductive layers of the PCB. The copper foil is etched to remove excess copper and define the circuit traces according to the PCB design.
- Drilling: Precision drilling is performed to create holes in the PCB for through-hole components and vias. Advanced drilling equipment and techniques are used to ensure accurate hole placement and size control.
- Plating: The walls of the plated through-holes are electroplated with copper to provide conductivity and mechanical strength. This process also involves the deposition of surface finishes such as gold, silver, or tin to protect the exposed copper surfaces from oxidation and facilitate soldering.
- Etching and Stripping:Excess copper is etched away from the non-conductive areas of the PCB using chemical etchants. After etching, the remaining photoresist is stripped away, leaving behind the desired circuit traces.
- Solder Mask Application: A solder mask is applied to the PCB to protect the circuitry from environmental factors and prevent solder bridges during assembly. Openings are created in the solder mask to expose the pads for component soldering.
- Silkscreen Printing: Component designators, polarity markings, logos, and other identifying information are printed onto the PCB surface using a silkscreen printing process. This helps assembly technicians identify and place components accurately.
- Component Assembly: Surface mount and through-hole components are soldered onto the PCB using automated assembly equipment or manual soldering techniques. Precision placement and soldering processes are critical to ensure proper electrical connections and mechanical stability.
- Final Inspection and Testing: The assembled PCBs undergo rigorous inspection and testing to ensure they meet the requirements of IPC Class III standards. This may include visual inspection, automated optical inspection (AOI), X-ray inspection, and functional testing to verify performance and reliability.
- Documentation and Traceability: Comprehensive documentation, including manufacturing records, material certifications, inspection reports, and test data, is generated to provide traceability and ensure accountability throughout the manufacturing process.
By following these steps and adhering to IPC Class III standards, PCB manufacturers can produce high-quality, reliable PCBs suitable for use in mission-critical applications across various industries.
How much should an IPC Class III PCB cost?
The cost of an IPC Class III PCB can vary significantly depending on various factors such as:
- Complexity of Design: PCBs with intricate designs, high component density, tight tolerances, and advanced features such as fine pitch components or high-speed signals will generally incur higher manufacturing costs.
- Material Selection: High-quality materials required for IPC Class III PCBs, including specialized laminates, copper foils, solder masks, and surface finishes, can contribute to increased manufacturing costs compared to standard materials.
- Manufacturing Processes: The use of advanced manufacturing processes and technologies to meet the stringent requirements of IPC Class III standards may incur additional costs. Processes such as controlled impedance routing, laser drilling, and advanced surface finishes require specialized equipment and expertise.
- Quantity: Economies of scale typically apply in PCB manufacturing, meaning that larger production quantities may result in lower per-unit costs due to efficiencies in material utilization, setup, and production.
- Lead Time: Expedited production schedules or shorter lead times may incur additional charges from the PCB manufacturer.
- Quality Assurance and Testing: Rigorous quality assurance measures, testing procedures, and compliance with IPC Class III standards may add to the overall cost of manufacturing.
- Supplier Selection: Different PCB manufacturers may offer varying pricing structures, capabilities, and levels of service. Choosing a reputable supplier with experience in manufacturing IPC Class III PCBs may affect the overall cost.
Due to these factors, it’s challenging to provide a specific cost estimate for an IPC Class III PCB without detailed information about the design requirements, materials, manufacturing processes, and quantity needed. It’s advisable to consult with PCB manufacturers and provide detailed specifications to obtain accurate price quotes tailored to your specific project.
What is the IPC Class III PCB base material?
The base material used for IPC Class III PCBs typically consists of high-quality laminates that meet stringent requirements for electrical performance, thermal properties, mechanical strength, and reliability. The most common base material for IPC Class III PCBs is a type of fiberglass-reinforced epoxy resin known as FR-4.
FR-4 is widely used in the PCB industry due to its excellent electrical insulation properties, dimensional stability, and cost-effectiveness. It provides good mechanical strength and can withstand high temperatures encountered during soldering and operation.
However, not all FR-4 laminates are created equal, and for IPC Class III applications, specific grades of FR-4 with enhanced characteristics may be required. These may include:
- High-Temperature FR-4: FR-4 materials designed to withstand elevated temperatures encountered during lead-free soldering processes.
- High-Speed FR-4: FR-4 laminates engineered to minimize signal loss and impedance variations, particularly for high-speed digital or RF applications.
- Halogen-Free FR-4: FR-4 materials that do not contain halogenated flame retardants, which may be required for environmental or regulatory compliance reasons.
- Thermally Conductive FR-4: FR-4 laminates with enhanced thermal conductivity to improve heat dissipation, suitable for applications with high power densities or thermal management requirements.
In addition to FR-4, other base materials such as polyimide (PI), polytetrafluoroethylene (PTFE), or ceramic may be used for specialized IPC Class III PCB applications where specific properties are needed, such as high temperature resistance, low dielectric constant, or exceptional dimensional stability.
Ultimately, the choice of base material for IPC Class III PCBs depends on the specific requirements of the application, including electrical performance, thermal management, environmental considerations, and compliance with industry standards.
Which company makes IPC Class III PCBs?
The production of IPC Class III PCBs is not carried out by a single company, but by multiple specialized PCB manufacturers and assembly factories working together. These companies provide high-quality PCB manufacturing services globally, with some focusing on meeting the requirements of IPC Class III standards. Some well-known PCB manufacturers include Sanmina and TTM Technologies in the United States, Foxconn in China, and Unimicron in Taiwan.
Our company is also capable of producing IPC Class III PCBs. We have advanced production equipment and technology, as well as an experienced engineering team, to meet the demands for high-reliability and high-performance PCBs. Here are our capabilities and advantages in producing IPC Class III PCBs:
- Professional Team: We have experienced engineers and technicians familiar with IPC Class III standards and requirements. They can provide professional design advice and technical support to ensure that PCB design and manufacturing meet customer requirements.
- Advanced Equipment: We are equipped with advanced PCB manufacturing equipment, including high-precision CNC machines, automated drilling machines, chemical etching equipment, automated soldering machines, and more. These machines enable us to achieve high-precision processing and production, ensuring PCB quality and reliability.
- Strict Quality Control: We implement a strict quality management system, conducting rigorous quality control and inspection at every stage from raw material procurement to production. We use advanced testing equipment and methods to ensure that every PCB meets the requirements of IPC Class III standards.
- Customized Services: We can customize PCB design and manufacturing solutions according to customer requirements, including material selection, process flow, and special requirements. We can adapt flexibly to changes in customer needs and provide customized solutions.
- Timely Delivery: We are committed to providing timely delivery services to ensure that customer projects are completed on time. With our efficient production capacity and supply chain management system, we can meet customers’ demands for fast delivery of PCBs.
Through our professional team, advanced equipment, strict quality control, and customized services, we can provide customers with high-quality IPC Class III PCBs that meet their requirements for high-reliability and high-performance electronic products.
What are the 7 qualities of good customer service?
Good customer service is essential for building strong relationships with customers and fostering loyalty. Here are seven qualities that characterize excellent customer service:
- Attentiveness: Attentive customer service representatives listen actively to customers, showing genuine interest in their needs and concerns. They pay close attention to details and strive to understand the customer’s perspective fully.
- Empathy: Empathetic customer service involves understanding and acknowledging the customer’s emotions and experiences. Representatives show empathy by putting themselves in the customer’s shoes, demonstrating understanding, and expressing concern for their feelings.
- Patience: Patience is crucial in customer service, especially when dealing with challenging or frustrated customers. Representatives remain calm and composed, taking the time to address the customer’s issues and provide assistance without rushing or becoming agitated.
- Clear Communication: Effective communication is key to providing good customer service. Representatives should communicate clearly and concisely, using language that the customer can understand. They should be able to explain complex concepts or solutions in simple terms and provide accurate information.
- Product Knowledge: Good customer service requires a deep understanding of the company’s products or services. Representatives should be knowledgeable about the features, benefits, and use cases of the offerings, allowing them to provide informed recommendations and solutions to customers.
- Problem-Solving Skills: Customer service representatives should possess strong problem-solving skills to address customer issues effectively. They should be able to identify problems, analyze situations, and propose solutions that meet the customer’s needs and expectations.
- Professionalism: Professionalism in customer service involves maintaining a courteous and respectful demeanor at all times. Representatives should conduct themselves professionally, demonstrating integrity, reliability, and trustworthiness in their interactions with customers.
By embodying these qualities, organizations can deliver exceptional customer service experiences that leave a positive impression on customers and contribute to long-term satisfaction and loyalty.
FAQs
What is IPC Class III?
IPC Class III refers to the highest level of quality and reliability standards set by the Institute for Interconnecting and Packaging Electronic Circuits (IPC) for printed circuit boards (PCBs). It is commonly used in industries where failure could result in severe consequences, such as aerospace, military, medical, and automotive.
What are the key characteristics of IPC Class III PCBs?
IPC Class III PCBs are characterized by stringent requirements for reliability, durability, and performance. They often feature tighter tolerances, advanced materials, thorough testing procedures, and robust documentation compared to lower IPC classes.
What applications are IPC Class III PCBs used for?
IPC Class III PCBs are used in mission-critical electronic applications where failure is not an option. Common applications include aerospace and defense systems, medical devices, automotive electronics, and industrial equipment operating in harsh environments.
What are the main differences between IPC Class II and Class III PCBs?
IPC Class III PCBs have more stringent requirements compared to Class II PCBs in terms of reliability, durability, and performance. Class III PCBs typically require tighter tolerances, more rigorous testing procedures, and specialized manufacturing techniques to meet the demands of high-reliability applications.
What materials are commonly used in IPC Class III PCBs?
IPC Class III PCBs often use high-quality materials such as advanced laminates, high-performance copper foils, specialized solder masks, and surface finishes. These materials are selected for their superior electrical properties, thermal conductivity, mechanical strength, and reliability.
How can I ensure compliance with IPC Class III standards for my PCB design?
To ensure compliance with IPC Class III standards, it’s essential to work with experienced PCB designers and manufacturers who are familiar with the requirements and specifications. Following industry best practices, using certified materials, and conducting thorough testing are also crucial steps.
Are IPC Class III PCBs more expensive than lower-class PCBs?
Yes, IPC Class III PCBs tend to be more expensive than lower-class PCBs due to the additional requirements for reliability and performance. The use of high-quality materials, advanced manufacturing processes, and thorough testing procedures contribute to higher production costs.